Texas Instruments 的 DS90UR241Q/124Q 规格书
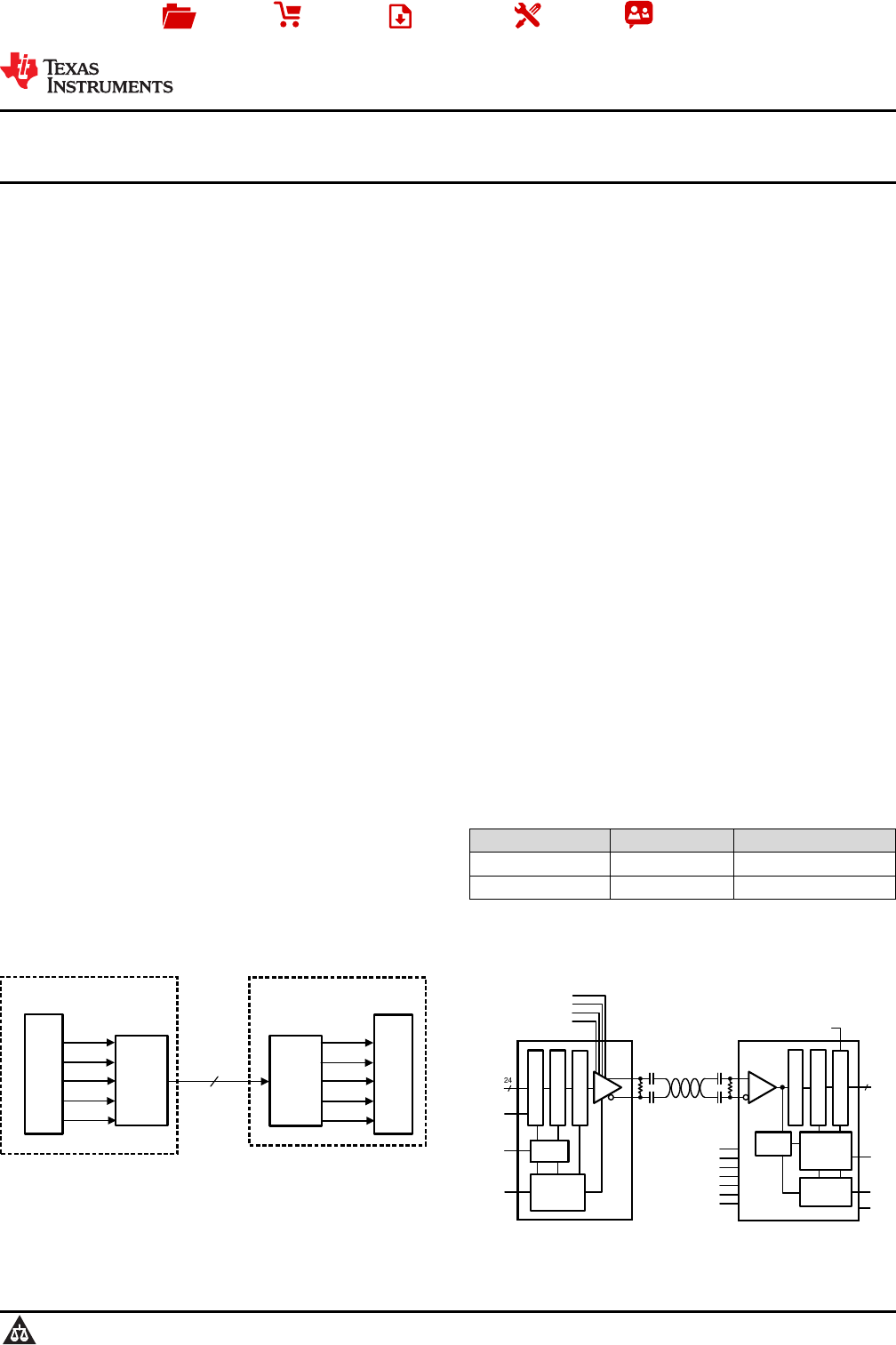
DEN
RAOFF
DIN
TRFB
24
REN
RAOFF
TCLK
TPWDNB
SERIALIZER ± DS90UR241
PLL
Timing
and
Control
DOUT-
RT = 100:
RT = 100:
RIN-
DESERIALIZER ± DS90UR124
DOUT+ RIN+
PLL Timing
and
Control
24 ROUT
LOCK
RCLK
Clock
Recovery
Output Latch
Serial to Parallel
DC Balance Decoder
Input Latch
Parallel to Serial
DC Balance Encoder
PRE
PASS
RRFB
RPWDNB
BISTEN
BISTM
SLEW
PTOSEL
VODSEL
Video
Source DS90UR241
Serializer
RGB Data
DE
Clock
HSYNC
VSYNC
Host
(Graphics/Video Processor, ECU)
LCD
DS90UR124
Deserializer
RGB Data
DE
Clock
HSYNC
VSYNC
Display
(Infotainment, Instrument Cluster, CID)
1 Pair
FPD-Link II
(LVDS)
(LVCMOS) (LVCMOS)
Product
Folder
Sample &
Buy
Technical
Documents
Tools &
Software
Support &
Community
DS90UR124-Q1
,
DS90UR241-Q1
SNLS231O –SEPTEMBER 2006–REVISED APRIL 2015
DS90URxxx-Q1 5-MHz to 43-MHz DC-Balanced 24-Bit FPD-Link II Serializer and
Deserializer Chipset
1 Features 2 Applications
1• Supports Displays With 18-Bit Color Depth • Automotive Central Information Displays
• 5-MHz to 43-MHz Pixel Clock • Automotive Instrument Cluster Displays
• Automotive-Grade Product AEC-Q100 Grade 2 • Automotive Heads-Up Displays
Qualified • Remote Camera-Based Driver Assistance
• 24:1 Interface Compression Systems
• Embedded Clock With DC Balancing Supports 3 Description
AC-Coupled Data Transmission The DS90URxxx-Q1 chipset translates a 24-bit
• Capable to Drive up to 10 Meters Shielded parallel bus into a fully transparent data/control FPD-
Twisted-Pair Cable Link II LVDS serial stream with embedded clock
• No Reference Clock Required (Deserializer) information. This chipset is ideally suited for driving
• Meets ISO 10605 ESD – Greater than 8 kV HBM graphical data to displays requiring 18-bit color depth:
RGB666 + HS, VS, DE + three additional general-
ESD Structure purpose data channels. This single serial stream
• Hot Plug Support simplifies transferring a 24-bit bus over PCB traces
• EMI Reduction – Serializer Accepts Spread and cable by eliminating the skew problems between
Spectrum Input; Data Randomization and parallel data and clock paths. The device saves
Shuffling on Serial Link; Deserializer Provides system cost by narrowing data paths that in turn
Adjustable PTO (Progressive Turnon) LVCMOS reduce PCB layers, cable width, and connector size
and pins.
Outputs
• @Speed BIST (Built-In Self-Test) to Validate The DS90URxxx-Q1 incorporates FPD-Link II LVDS
LVDS Transmission Path signaling on the high-speed I/O. FPD-Link II LVDS
provides a low-power and low-noise environment for
• Individual Power-Down Controls for Both reliably transferring data over a serial transmission
Transmitter and Receiver path. By optimizing the Serializer output edge rate for
• Power Supply Range 3.3 V ±10% the operating frequency range, EMI is further
• 48-Pin TQFP Package for Transmitter and 64-Pin reduced.
TQFP Package for Receiver Device Information(1)
• Temperature Range: –40°C to 105°C PART NUMBER PACKAGE BODY SIZE (NOM)
• Backward-Compatible Mode With DS90UR124-Q1 TQFP (64) 10.00 mm × 10.00 mm
DS90C241/DS90C124 DS90UR241-Q1 TQFP (48) 7.00 mm × 7.00 mm
(1) For all available packages, see the orderable addendum at
the end of the data sheet.
Applications Diagram Block Diagram
1
An IMPORTANT NOTICE at the end of this data sheet addresses availability, warranty, changes, use in safety-critical applications,
intellectual property matters and other important disclaimers. PRODUCTION DATA.
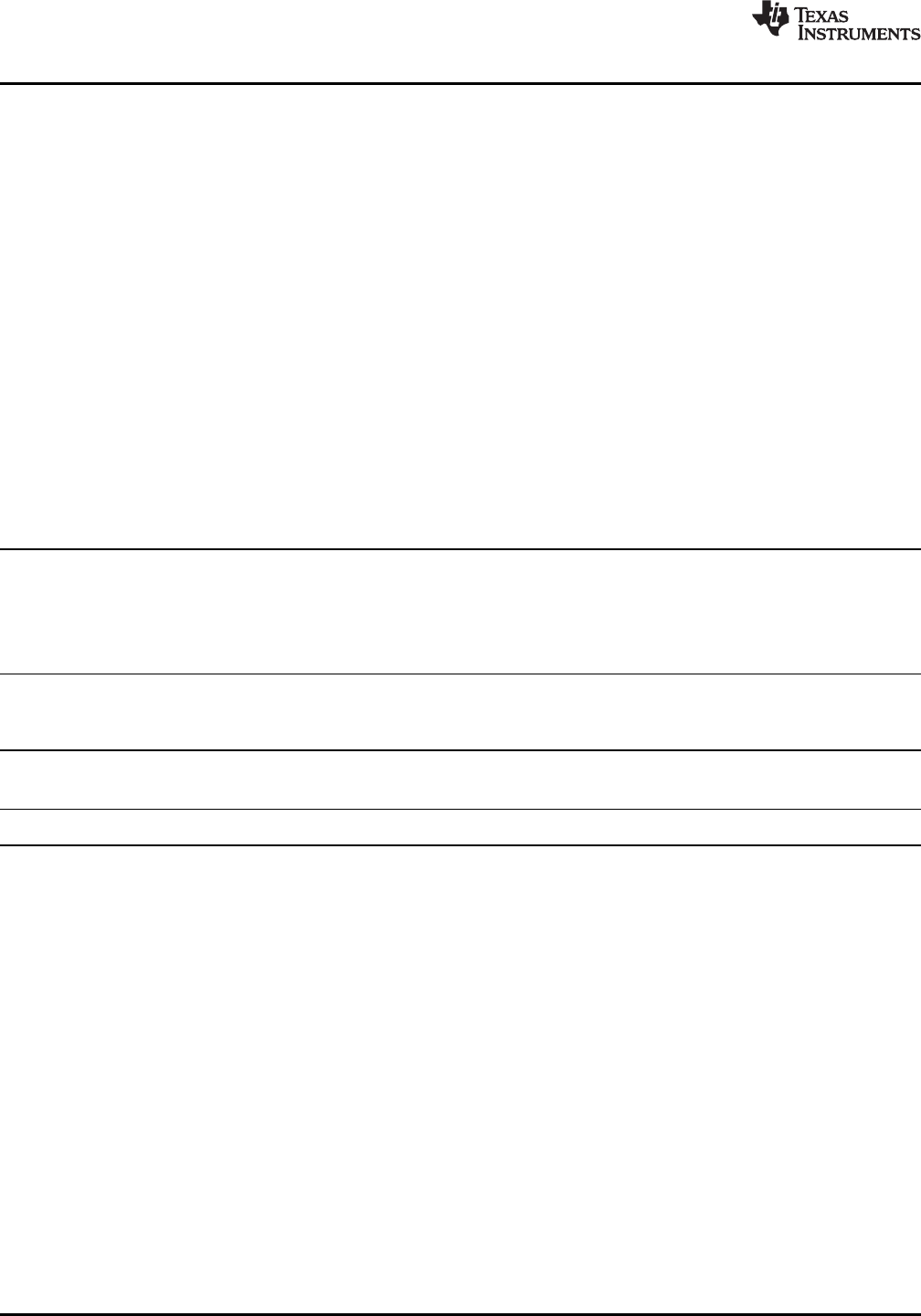
DS90UR124-Q1
,
DS90UR241-Q1
SNLS231O –SEPTEMBER 2006–REVISED APRIL 2015
www.ti.com
Table of Contents
8.2 Functional Block Diagram....................................... 18
1 Features.................................................................. 18.3 Feature Description................................................. 18
2 Applications ........................................................... 18.4 Device Functional Modes........................................ 23
3 Description ............................................................. 19 Application and Implementation ........................ 24
4 Revision History..................................................... 29.1 Application Information............................................ 24
5 Description (continued)......................................... 39.2 Typical Applications ................................................ 25
6 Pin Configuration and Functions......................... 310 Power Supply Recommendations ..................... 29
7 Specifications......................................................... 711 Layout................................................................... 30
7.1 Absolute Maximum Ratings ...................................... 711.1 Layout Guidelines ................................................. 30
7.2 ESD Ratings.............................................................. 711.2 Layout Examples................................................... 32
7.3 Recommended Operating Conditions....................... 712 Device and Documentation Support ................. 34
7.4 Thermal Information.................................................. 812.1 Device Support...................................................... 34
7.5 Electrical Characteristics........................................... 812.2 Documentation Support ........................................ 34
7.6 Serializer Input Timing Requirements for TCLK ..... 10 12.3 Related Links ........................................................ 34
7.7 Serializer Switching Characteristics........................ 10 12.4 Trademarks........................................................... 34
7.8 Deserializer Switching Characteristics.................... 10 12.5 Electrostatic Discharge Caution............................ 34
7.9 Typical Characteristics............................................ 17 12.6 Glossary................................................................ 34
8 Detailed Description............................................ 18 13 Mechanical, Packaging, and Orderable
8.1 Overview ................................................................. 18 Information ........................................................... 34
4 Revision History
NOTE: Page numbers for previous revisions may differ from page numbers in the current version.
Changes from Revision N (March 2013) to Revision O Page
• Added ESD Ratings table, Feature Description section, Device Functional Modes,Application and Implementation
section, Power Supply Recommendations section, Layout section, Device and Documentation Support section, and
Mechanical, Packaging, and Orderable Information section.................................................................................................. 1
Changes from Revision M (March 2013) to Revision N Page
• Changed layout of National Data Sheet to TI format ........................................................................................................... 23
2Submit Documentation Feedback Copyright © 2006–2015, Texas Instruments Incorporated
Product Folder Links: DS90UR124-Q1 DS90UR241-Q1
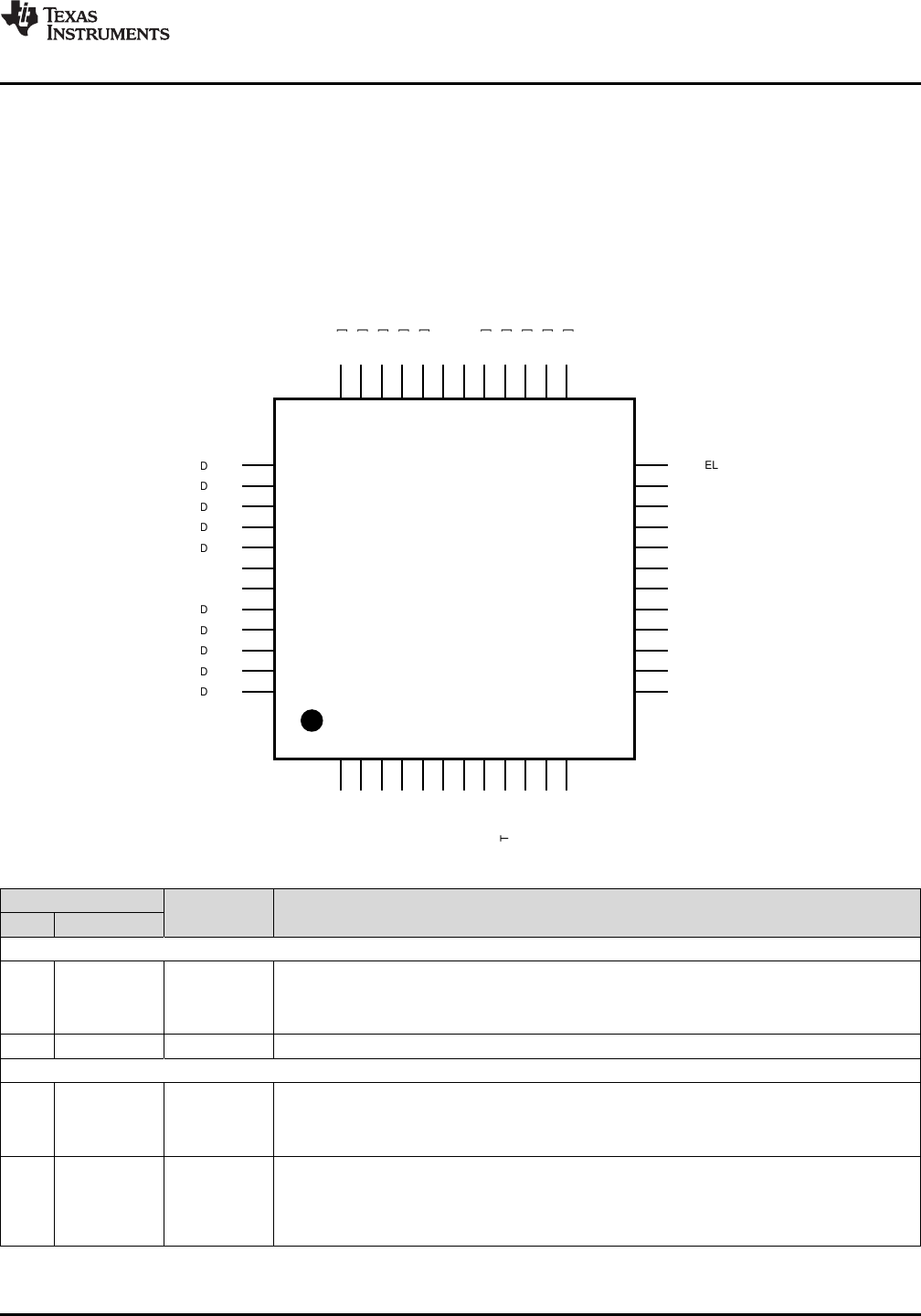
48
DIN[19]
47
DIN[18]
46
DIN[17]
45
DIN[16]
44
DIN[15]
43
VSS
42
VDD
41
DIN[14]
40
DIN[13]
39
DIN[12]
38
DIN[11]
37
DIN[10]
13
14
15
16
17
18
19
20
21
22
23
24
RES0
VDD
VSS
VDD
VSS
DEN
DOUT-
DOUT+
VSS
VDD
PRE
VODSEL
12RAOFF
11TRFB
10TCLK
9TPWDNB
8RES0
7
VDD
6
VSS
5RES0
4
DIN[23]
3
DIN[22]
2
DIN[21]
1
DIN[20]
25
26
27
28
29
30
31
32
33
34
35
36
DIN[0]
DIN[1]
DIN[2]
DIN[3]
DIN[4]
VDD
VSS
DIN[5]
DIN[6]
DIN[7]
DIN[8]
DIN[9]
DS90UR241
DS90UR124-Q1
,
DS90UR241-Q1
www.ti.com
SNLS231O –SEPTEMBER 2006–REVISED APRIL 2015
5 Description (continued)
In addition, the device features pre-emphasis to boost signals over longer distances using lossy cables. Internal
DC-balanced encoding and decoding is used to support AC-coupled interconnects. Using TI’s proprietary random
lock, the parallel data of the Serializer are randomized to the Deserializer without the need of REFCLK.
6 Pin Configuration and Functions
PFB Package
48-Pin TQFP
Top View
Pin Functions: PFB Package
PIN I/O DESCRIPTION
NO. NAME
LVCMOS PARALLEL INTERFACE PINS
4-1,
48-44, DIN[23:0] LVCMOS_I Transmitter Parallel Interface Data Input Pins. Tie LOW if unused; do not float.
41-32,
29-25
10 TCLK LVCMOS_I Transmitter Parallel Interface Clock Input Pin. Strobe edge set by TRFB configuration pin.
CONTROL AND CONFIGURATION PINS
Transmitter Data Enable
DEN = H; LVDS Driver Outputs are Enabled (ON).
18 DEN LVCMOS_I DEN = L; LVDS Driver Outputs are Disabled (OFF), Transmitter LVDS Driver DOUT (+/-) Outputs
are in Tri-state, PLL still operational and locked to TCLK.
Pre-emphasis Level Select
PRE = NC (No Connect); Pre-emphasis is Disabled (OFF).
23 PRE LVCMOS_I Pre-emphasis is active when input is tied to VSS through external resistor RPRE. Resistor value
determines pre-emphasis level. Recommended value RPRE ≥6 kΩ; Imax = [48 / RPRE], RPREmin =
6 kΩ
Copyright © 2006–2015, Texas Instruments Incorporated Submit Documentation Feedback 3
Product Folder Links: DS90UR124-Q1 DS90UR241-Q1
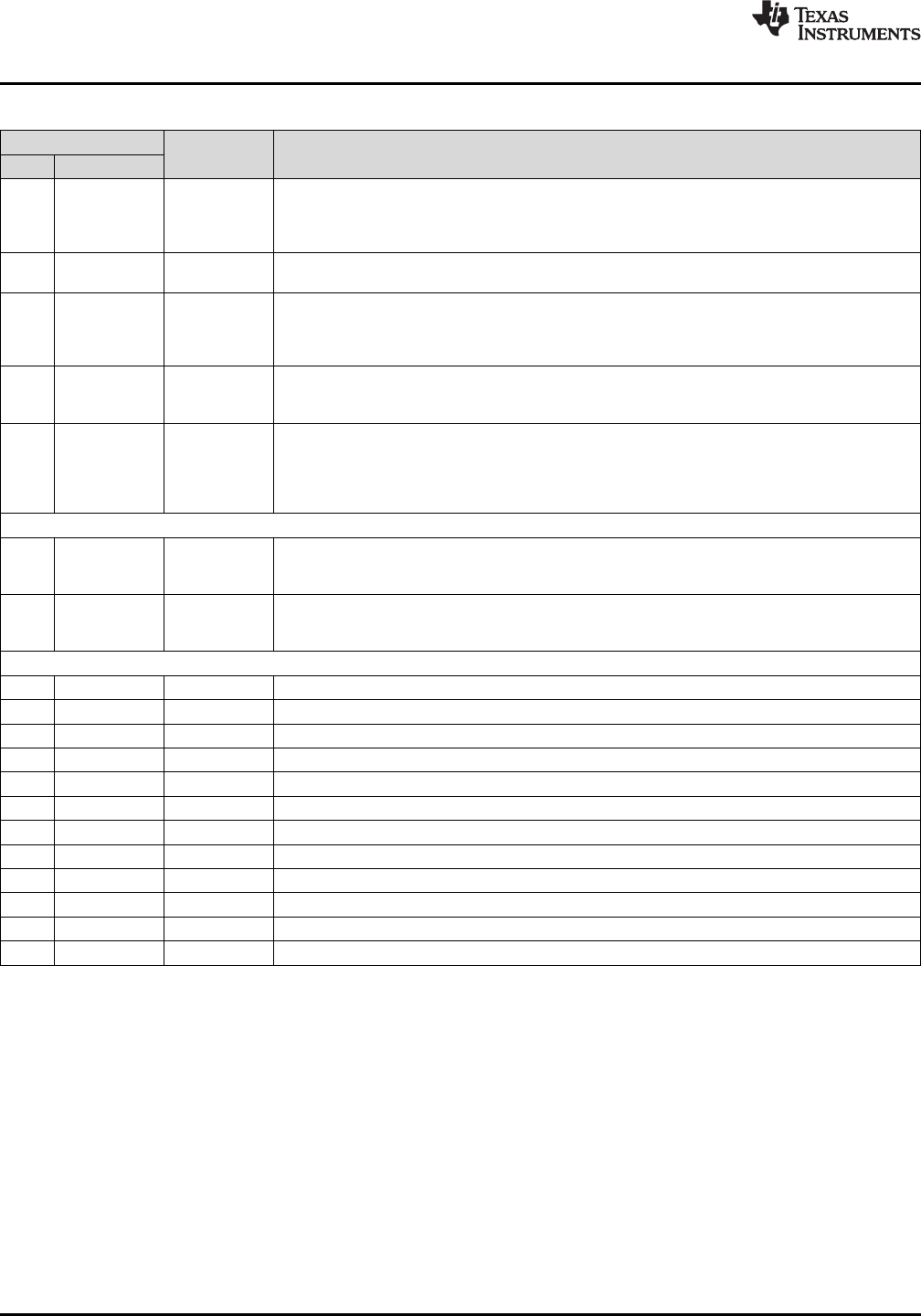
DS90UR124-Q1
,
DS90UR241-Q1
SNLS231O –SEPTEMBER 2006–REVISED APRIL 2015
www.ti.com
Pin Functions: PFB Package (continued)
PIN I/O DESCRIPTION
NO. NAME
Randomizer Control Input Pin
RAOFF = H, Backwards compatible mode for use with DS90C124 Deserializer.
12 RAOFF LVCMOS_I RAOFF = L; Additional randomization ON (Default), Selects 2E7 LSFR setting.
See Table 1 for more details.
5, 8, RES0 LVCMOS_I Reserved. This pin must be tied LOW.
13
Transmitter Power Down Bar
TPWDNB = H; Transmitter is Enabled and ON
9 TPWDNB LVCMOS_I TPWDNB = L; Transmitter is in power down mode (Sleep), LVDS Driver DOUT (+/-) Outputs are in
Tri-state stand-by mode, PLL is shutdown to minimize power consumption.
Transmitter Clock Edge Select Pin
11 TRFB LVCMOS_I TRFB = H; Parallel Interface Data is strobed on the Rising Clock Edge.
TRFB = L; Parallel Interface Data is strobed on the Falling Clock Edge
VOD Level Select
VODSEL = L; LVDS Driver Output is ±500 mV (RL= 100 Ω)
24 VODSEL LVCMOS_I VODSEL = H; LVDS Driver Output is ±900 mV (RL= 100 Ω)
For normal applications, set this pin LOW. For long cable applications where a larger VOD is
required, set this pin HIGH.
LVDS SERIAL INTERFACE PINS
Transmitter LVDS True (+) Output.
20 DOUT+ LVDS_O This output is intended to be loaded with a 100-Ωload to the DOUT+ pin. The interconnect should
be AC coupled to this pin with a 100-nF capacitor.
Transmitter LVDS Inverted (-) Output
19 DOUT−LVDS_O This output is intended to be loaded with a 100-Ωload to the DOUT- pin. The interconnect should
be AC coupled to this pin with a 100-nF capacitor.
POWER / GROUND PINS
22 VDD VDD Analog Voltage Supply, LVDS Output POWER
16 VDD VDD Analog Voltage Supply, VCO POWER
14 VDD VDD Analog Voltage Supply, PLL POWER
30 VDD VDD Digital Voltage Supply, Serializer POWER
7 VDD VDD Digital Voltage Supply, Serializer Logic POWER
42 VDD VDD Digital Voltage Supply, Serializer INPUT POWER
21 VSS GND Analog Ground, LVDS Output GROUND
17 VSS GND Analog Ground, VCO GROUND
15 VSS GND Analog Ground, PLL GROUND
31 VSS GND Digital Ground, Serializer GROUND
6 VSS GND Digital Ground, Serializer Logic GROUND
43 VSS GND Digital Ground, Serializer Input GROUND
4Submit Documentation Feedback Copyright © 2006–2015, Texas Instruments Incorporated
Product Folder Links: DS90UR124-Q1 DS90UR241-Q1

64
REN
63
VDD
62
VSS
61
VDD
60
VSS
59
RRFB
58
RIN-
57
RIN+
56
55
54
53
17
18
19
20
21
22
23
24
25
26
27
28
ROUT[15]
ROUT[14]
ROUT[13]
ROUT[12]
LOCK
RCLK
VSS
VDD
ROUT[11]
ROUT[10]
ROUT[9]
ROUT[8]
12
ROUT[16]
11
ROUT[17]
10
ROUT[18]
9
ROUT[19]
8
VSS
7
VDD
6
ROUT[20]
5
ROUT[21]
4
ROUT[22]
3
ROUT[23]
2RES0
1
37
38
39
40
41
42
43
44
45
46
47
48
ROUT[7]
ROUT[6]
ROUT[5]
ROUT[4]
VSS
VDD
ROUT[3]
ROUT[2]
ROUT[1]
ROUT[0]
VSS
VDD
PTO GROUP 3
PTO GROUP 1
PTO GROUP 2
16
15
14
13
33
34
35
36
RES0
52
51
50
49
29
30
31
32
DS90UR124
RES0
RES0
RES0
RES0
RES0
RES0
RES0
VSS
VDD
RES0
PASS
RPWDNB
BISTEN
BISTM
RAOFF
SLEW
VSS
VDD
RES0
PTOSEL
DS90UR124-Q1
,
DS90UR241-Q1
www.ti.com
SNLS231O –SEPTEMBER 2006–REVISED APRIL 2015
PAG Package
64-Pin TQFP
Top View
Pin Functions: PAG Package
PIN I/O DESCRIPTION
NO. NAME
LVCMOS PARALLEL INTERFACE PINS
24 RCLK LVCMOS_O Parallel Interface Clock Output Pin. Strobe edge set by RRFB configuration pin.
35-38, ROUT[7:0] LVCMOS_O Receiver Parallel Interface Data Outputs – Group 1
41-44
19-22, ROUT[15:8] LVCMOS_O Receiver Parallel Interface Data Outputs – Group 2
27-30
7-10, ROUT[23:16] LVCMOS_O Receiver Parallel Interface Data Outputs – Group 3
13-16
CONTROL AND CONFIGURATION PINS
LOCK indicates the status of the receiver PLL
23 LOCK LVCMOS_O LOCK = H; receiver PLL is locked
LOCK = L; receiver PLL is unlocked, ROUT[23-0] and RCLK are at Tri-state.
Progressive Turn On Operation Selection
PTO = H; ROUT[23:0] are grouped into three groups of eight, with each group switching about ±1
49 PTOSEL LVCMOS_I UI to ±2 UI apart relative to RCLK. (Figure 17)
PTO = L; PTO Spread Mode, ROUT[23:0] outputs are spread ±1 UI to ±2 UI and RCLK spread ±1
UI. (Figure 18)See Applications Informations section for more details.
Randomizer Control Input Pin (See Table 2 for more details.)
63 RAOFF LVCMOS_I RAOFF = H, Backwards compatible mode for use with DS90C241 Serializer.
RAOFF = L; Additional randomization ON (Default), Selects 2E7 LSFR setting.
Receiver Data Enable
REN = H; ROUT[23-0] and RCLK are Enabled (ON).
60 REN LVCMOS_I REN = L; ROUT[23-0] and RCLK are Disabled (OFF), Receiver ROUT[23-0] and RCLK Outputs are
in Tri-state, PLL still operational and locked to TCLK.
Copyright © 2006–2015, Texas Instruments Incorporated Submit Documentation Feedback 5
Product Folder Links: DS90UR124-Q1 DS90UR241-Q1

DS90UR124-Q1
,
DS90UR241-Q1
SNLS231O –SEPTEMBER 2006–REVISED APRIL 2015
www.ti.com
Pin Functions: PAG Package (continued)
PIN I/O DESCRIPTION
NO. NAME
50 RES0 LVCMOS_I Reserved. This pin MUST be tied LOW.
1-6,
17, No Connection. Pins are not physically connected to the die. Recommendation is to leave pin
RES0 NC
18, open or tie it to LOW.
33, 34
Receiver Power Down Bar
RPWDNB = H; Receiver is Enabled and ON
48 RPWDNB LVCMOS_I RPWDNB = L; Receiver is in power down mode (Sleep), ROUT[23-0], RCLK, and LOCK are in Tri-
state standby mode, PLL is shutdown to minimize power consumption.
Receiver Clock Edge Select Pin
55 RRFB LVCMOS_I RRFB = H; ROUT LVCMOS Outputs strobed on the Rising Clock Edge.
RRFB = L; ROUT LVCMOS Outputs strobed on the Falling Clock Edge.
LVCMOS Output Slew Rate Control
64 SLEW LVCMOS_I SLEW = L; Low drive output at 2 mA (default)
SLEW = H; High drive output at 4 mA
BIST MODE PINS (See Application and Implementation for more details.)
Control Pin for BIST Mode Enable
BISTEN = L; Default at Low, Normal Mode.
61 BISTEN LVCMOS_I BISTEN = H; BIST mode active. When BISTEN = H and DS90UR241 DIN[23:0] = Low or
Floating; device will go to BIST mode accordingly. Check PASS output pin for test status.
BIST Mode selection. Control pin for which Deserializer is set for BIST reporting mode.
62 BISTM LVCMOS_I BISTM = L; Default at Low, Status of all ROUT with respective bit error on cycle-by-cycle basis
BISTM = H; Total accumulated bit error count provided on ROUT[7:0] (binary counter up to 255)
Pass flag output for @Speed BIST Test operation.
45 PASS LVCMOS_O PASS = L; BIST failure
PASS = H; LOCK = H before BIST can be enabled, then 1x10-9 error rate achieved across link.
LVDS SERIAL INTERFACE PINS
Receiver LVDS True (+) Input — This input is intended to be terminated with a 100Ωload to the
53 RIN+ LVDS_I RIN+ pin. The interconnect should be AC Coupled to this pin with a 100 nF capacitor.
Receiver LVDS Inverted (−)Input — This input is intended to be terminated with a 100Ωload to
54 RIN−LVDS_I the RIN- pin. The interconnect should be AC Coupled to this pin with a 100 nF capacitor.
POWER / GROUND PINS
51 VDD VDD Analog LVDS Voltage Supply, POWER
59 VDD VDD Analog Voltage Supply, PLL POWER
57 VDD VDD Analog Voltage supply, PLL VCO POWER
32 VDD VDD Digital Voltage Supply, LOGIC POWER
46 VDD VDD Digital Voltage Supply, LOGIC POWER
40 VDD VDD Digital Voltage Supply, LVCMOS Output POWER
26 VDD VDD Digital Voltage Supply, LVCMOS Output POWER
11 VDD VDD Digital Voltage Supply, LVCMOS Output POWER
52 VSS GND Analog LVDS GROUND
58 VSS GND Analog Ground, PLL GROUND
56 VSS GND Analog Ground, PLL VCO GROUND
31 VSS GND Digital Ground, Logic GROUND
47 VSS GND Digital Ground, LOGIC GROUND
39 VSS GND Digital Ground, LVCMOS Output GROUND
25 VSS GND Digital Ground, LVCMOS Output GROUND
12 VSS GND Digital Ground, LVCMOS Output GROUND
6Submit Documentation Feedback Copyright © 2006–2015, Texas Instruments Incorporated
Product Folder Links: DS90UR124-Q1 DS90UR241-Q1
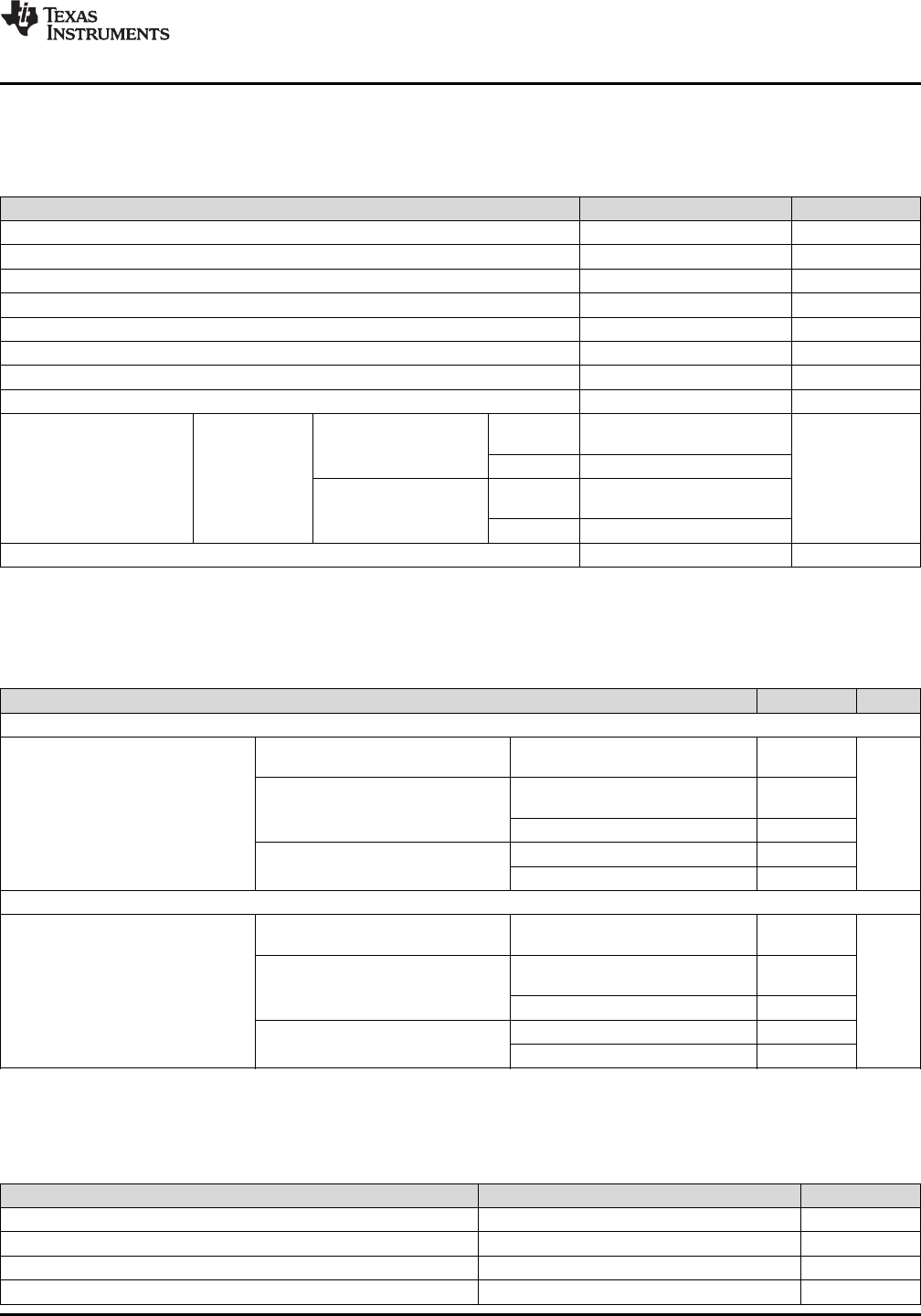
DS90UR124-Q1
,
DS90UR241-Q1
www.ti.com
SNLS231O –SEPTEMBER 2006–REVISED APRIL 2015
7 Specifications
7.1 Absolute Maximum Ratings
over operating free-air temperature range (unless otherwise noted) (1)
MIN MAX UNIT
Supply Voltage (VDD) –0.3 4 V
LVCMOS Input Voltage –0.3 VDD +0.3 V
LVCMOS Output Voltage –0.3 VDD +0.3 V
LVDS Receiver Input Voltage –0.3 +3.9 V
LVDS Driver Output Voltage –0.3 +3.9 V
LVDS Output Short Circuit Duration 10 ms
Junction Temperature 150 °C
Lead Temperature (Soldering, 4 seconds) 260 °C
45.8 (4L);
RθJA
DS90UR241 −48L 75.4 (2L)
TQFP RθJC 21.0
Maximum Package Power Package °C/W
Dissipation Capacity(2) Derating: 42.8 (4L);
RθJA
DS90UR124 −64L 67.2 (2L)
TQFP RθJC 14.6
Storage temperature, Tstg –65 150 °C
(1) Stresses beyond those listed under Absolute Maximum Ratings may cause permanent damage to the device. These are stress ratings
only, which do not imply functional operation of the device at these or any other conditions beyond those indicated under Recommended
Operating Conditions. Exposure to absolute-maximum-rated conditions for extended periods may affect device reliability.
(2) 1/RθJA °C/W above +25°C
7.2 ESD Ratings
VALUE UNIT
DS90UR241-Q1 IN PFB PACKAGE
Human body model (HBM), per AEC ≥±8000
All pins
Q100-002(1)
Corner pins (1, 12, 13, 24, 25, 36, ±12500
Charged device model (CDM), per 37, and 48)
V(ESD) Electrostatic discharge V
AEC Q100-011 Other pins ±12500
Contact Discharge (20, 19) ±10000
(ISO10605)(2) Air Discharge (20, 19) ±30000
DS90UR124-Q1 IN PAG PACKAGE
Human body model (HBM), per AEC All pins ≥±8000
Q100-002(1)
Corner pins (1, 16, 17, 32, 33, 48, ±12500
Charged device model (CDM), per 49, and 64)
V(ESD) Electrostatic discharge V
AEC Q100-011 Other pins ±12500
Contact Discharge (RIN+, RIN−) ±10000
(ISO10605)(2) Air Discharge (RIN+, RIN−) ±30000
(1) AEC Q100-002 indicates HBM stressing is done in accordance with the ANSI/ESDA/JEDEC JS-001 specification.
(2) RD= 2 kΩ, CS= 330 pF
7.3 Recommended Operating Conditions
over operating free-air temperature range (unless otherwise noted)
MIN NOM MAX UNIT
Supply Voltage (VDD) 3.0 3.3 3.6 V
Operating Free Air Temperature (TA) –40 25 105 °C
Clock Rate 5 43 MHz
Supply Noise ±100 mVP-P
Copyright © 2006–2015, Texas Instruments Incorporated Submit Documentation Feedback 7
Product Folder Links: DS90UR124-Q1 DS90UR241-Q1
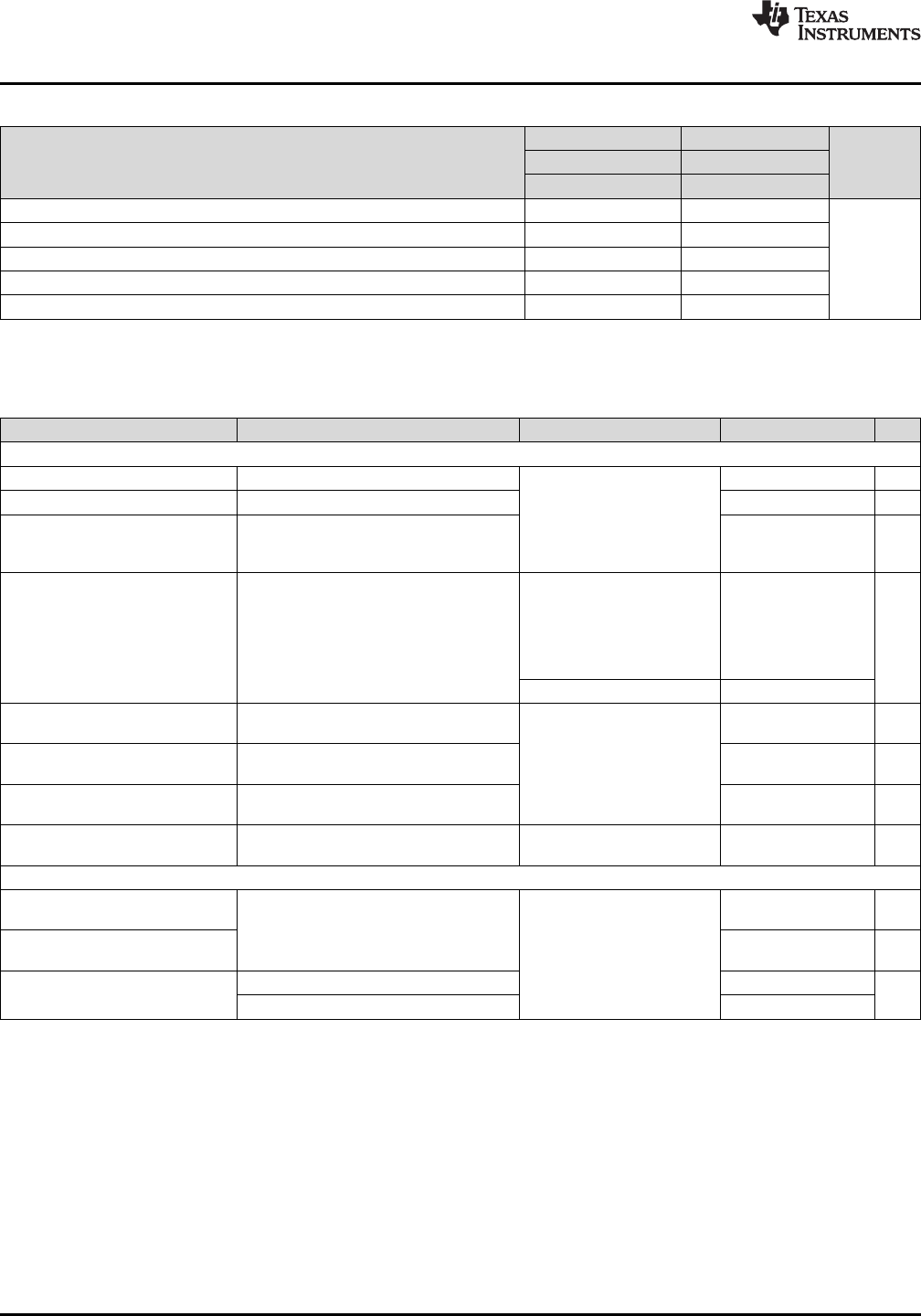
DS90UR124-Q1
,
DS90UR241-Q1
SNLS231O –SEPTEMBER 2006–REVISED APRIL 2015
www.ti.com
7.4 Thermal Information
DS90UR124-Q1 DS90UR241-Q1
THERMAL METRIC(1) PAG [TQFP] PFB [TQFP] UNIT
64 PINS 48 PINS
RθJA Junction-to-ambient thermal resistance 58.1 64.3
RθJC(top) Junction-to-case (top) thermal resistance 13.0 14.1
RθJB Junction-to-board thermal resistance 30.4 30.2 °C/W
ψJT Junction-to-top characterization parameter 0.3 0.4
ψJB Junction-to-board characterization parameter 30.0 29.8
(1) For more information about traditional and new thermal metrics, see the IC Package Thermal Metrics application report, SPRA953.
7.5 Electrical Characteristics
over recommended operating supply and temperature ranges unless otherwise specified
PARAMETER TEST CONDITIONS PIN/FREQ. MIN TYP MAX UNIT
LVCMOS DC SPECIFICATIONS
VIH High-Level Input Voltage Tx: DIN[0:23], TCLK, 2 VDD V
TPWDNB, DEN, TRFB,
VIL Low-Level Input Voltage GND 0.8 V
RAOFF, VODSEL, RES0.
Rx: RPWDNB, RRFB, REN,
VCL Input Clamp Voltage ICL =−18 mA –0.8 –1.5 V
PTOSEL, BISTEN, BISTM,
SLEW, RES0.
Tx: DIN[0:23], TCLK,
TPWDNB, DEN, TRFB,
RAOFF, RES0. –10 ±2 10
Rx: RRFB, REN, PTOSEL,
IIN Input Current VIN = 0 V or 3.6 V µA
BISTEN, BISTM, SLEW,
RES0.
Rx: RPWDNB –20 ±5 20
High-Level Output IOH =−2 mA, SLEW = L
VOH 2.3 3 VDD V
Voltage IOH =−4 mA, SLEW = H
Low-Level Output IOL = 2 mA, SLEW = L Rx: ROUT[0:23], RCLK,
VOL GND 0.33 0.5 V
Voltage IOL = 4 mA, SLEW = H LOCK, PASS.
Output Short Circuit
IOS VOUT = 0 V –40 –70 –110 mA
Current
RPWDNB, REN = 0 V, Rx: ROUT[0:23], RCLK,
IOZ Tri-state Output Current –30 ±0.4 30 µA
VOUT = 0 V or VDD LOCK, PASS.
LVDS DC SPECIFICATIONS
Differential Threshold
VTH 50 mV
High Voltage VCM = 1.8 V
Differential Threshold
VTL –50 mV
Rx: RIN+, RIN−
Low Voltage
VIN = 2.4 V, VDD = 3.6 V ±100 ±250
IIN Input Current µA
VIN = 0 V, VDD = 3.6 V ±100 ±250
8Submit Documentation Feedback Copyright © 2006–2015, Texas Instruments Incorporated
Product Folder Links: DS90UR124-Q1 DS90UR241-Q1
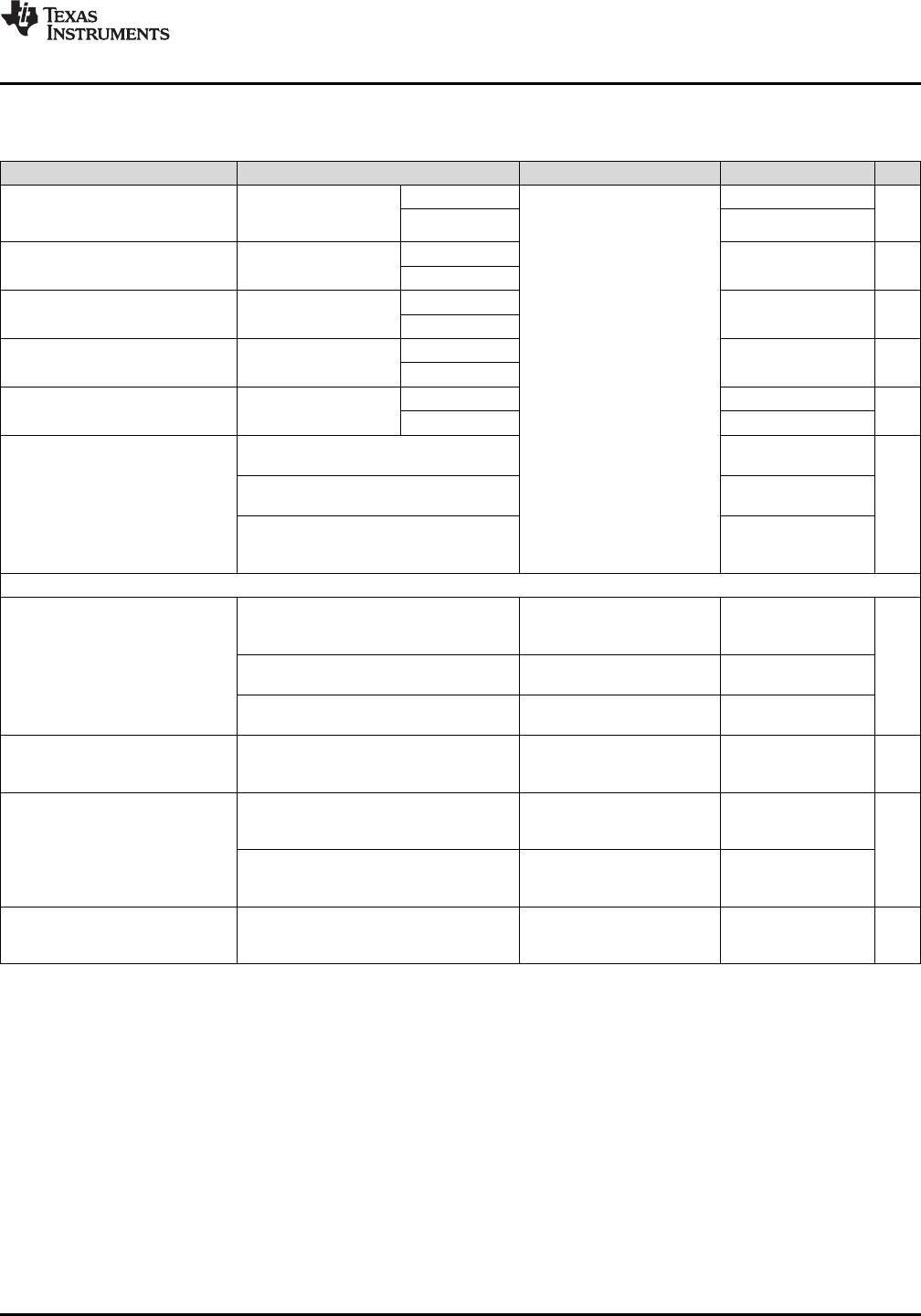
DS90UR124-Q1
,
DS90UR241-Q1
www.ti.com
SNLS231O –SEPTEMBER 2006–REVISED APRIL 2015
Electrical Characteristics (continued)
over recommended operating supply and temperature ranges unless otherwise specified
PARAMETER TEST CONDITIONS PIN/FREQ. MIN TYP MAX UNIT
RL= 100 Ω, without VODSEL = L 380 500 630
Output Differential
VOD pre-emphasis mV
Voltage (DOUT+)–(DOUT−)VODSEL = H 500 900 1100
Figure 12
VODSEL = L
Output Differential RL= 100 Ω,
ΔVOD 1 50 mV
Voltage Unbalance without pre-emphasis VODSEL = H
VODSEL = L
RL= 100 Ω,
VOS Offset Voltage 1 1.25 1.50 V
without pre-emphasis VODSEL = H
VODSEL = L
Offset Voltage RL= 100 Ω,
ΔVOS 3 50 mV
Unbalance without pre-emphasis VODSEL = H Tx: DOUT+, DOUT−
VODSEL = L –2 –5 –8
Output Short Circuit DOUT = 0 V, DIN = H,
IOS mA
Current TPWDNB = 2.4 V VODSEL = H –4.5 –7.9 –14
TPWDNB = 0 V, –15 ±1 15
DOUT = 0 V OR VDD
TPWDNB = 2.4 V, DEN = 0 V –15 ±1 15
IOZ Tri-state Output Current DOUT = 0 V OR VDD µA
TPWDNB = 2.4 V, DEN = 2.4 V,
DOUT = 0 V OR VDD –15 ±1 15
NO LOCK (NO TCLK)
SER/DES SUPPLY CURRENT (DVDD*, PVDD* AND AVDD* PINS) *DIGITAL, PLL, AND ANALOG VDDS
f = 43 MHz,
RL= 100 Ω, PRE = OFF, checkerboard pattern 60 85
RAOFF = H, VODSEL = L Figure 3
Serializer
IDDT Total Supply Current RL= 100 Ω, PRE = 12 kΩ, mA
65 90
(includes load current) RAOFF = H, VODSEL = L
RL= 100 Ω, PRE = OFF, f = 43 MHz, 66 90
RAOFF = H, VODSEL = H random pattern
Serializer TPWDNB = 0V
IDDTZ Supply Current Power- 45 µA
(All other LVCMOS Inputs = 0 V)
down
f = 43 MHz,
CL= 4 pF, checkerboard pattern 85 105
SLEW = H
Deserializer LVCMOS Output Figure 4
IDDR Total Supply Current mA
f = 43 MHz,
(includes load current) CL= 4 pF, random pattern 80 100
SLEW = H LVCMOS Output
Deserializer RPWDNB = 0 V
IDDRZ Supply Current Power- (All other LVCMOS Inputs = 0 V, 50 µA
down RIN+/RIN- = 0 V)
Copyright © 2006–2015, Texas Instruments Incorporated Submit Documentation Feedback 9
Product Folder Links: DS90UR124-Q1 DS90UR241-Q1
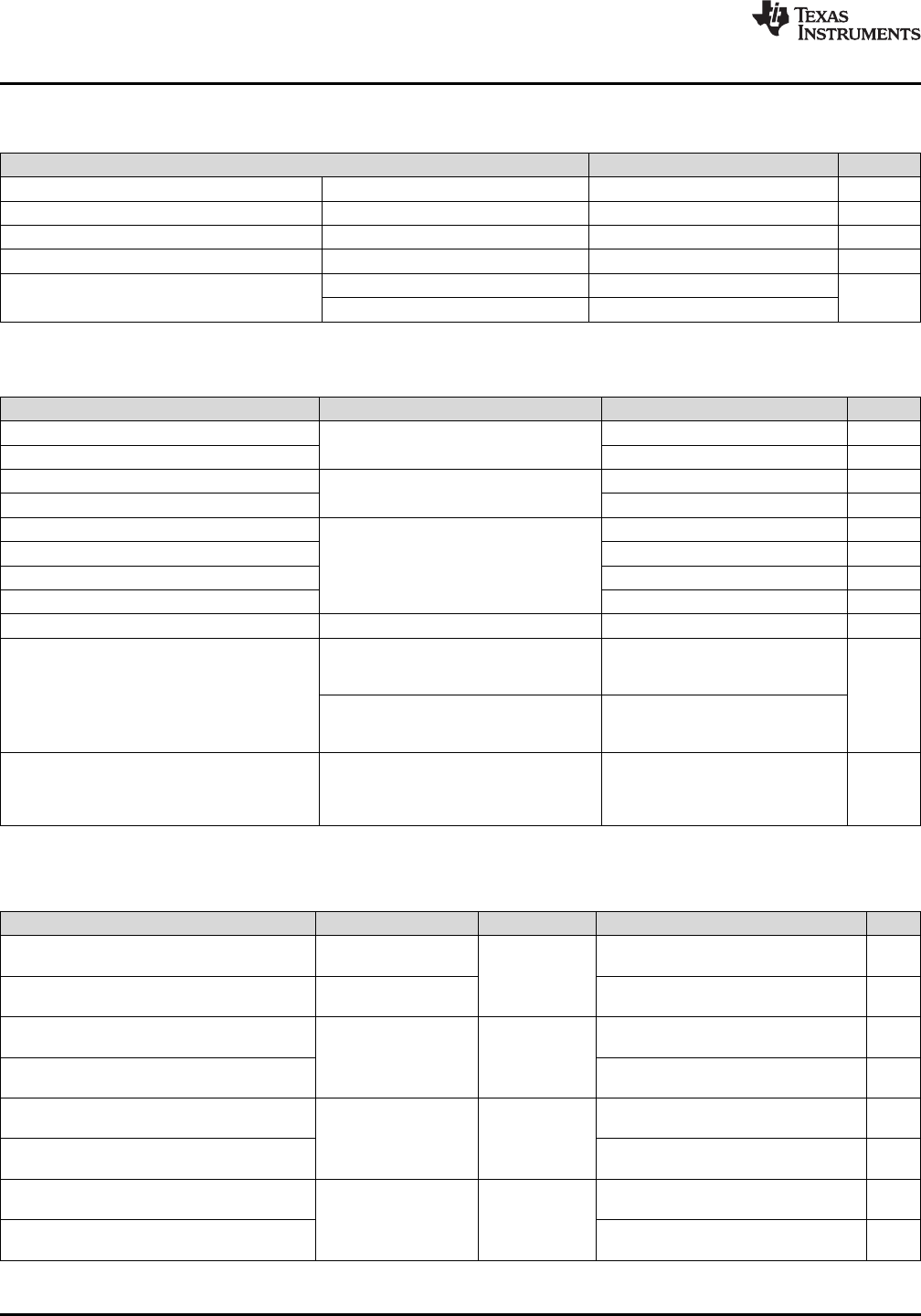
DS90UR124-Q1
,
DS90UR241-Q1
SNLS231O –SEPTEMBER 2006–REVISED APRIL 2015
www.ti.com
7.6 Serializer Input Timing Requirements for TCLK
over recommended operating supply and temperature ranges unless otherwise specified
MIN NOM MAX UNIT
tTCP Transmit Clock Period Figure 7 23.25 T 200 ns
tTCIH Transmit Clock High Time 0.3 T 0.5 T 0.7 T ns
tTCIL Transmit Clock Low Time 0.3 T 0.5 T 0.7 T ns
tCLKT TCLK Input Transition Time Figure 6 2.5 ns
f = 43 MHz ±100
tJIT TCLK Input Jitter ps
f = 33 MHz ±130
7.7 Serializer Switching Characteristics
over recommended operating supply and temperature ranges unless otherwise specified
PARAMETER TEST CONDITIONS MIN TYP MAX UNIT
tLLHT LVDS Low-to-High Transition Time 245 550 ps
RL= 100 Ω, VODSEL = L,
CL= 10 pF to GND, Figure 5
tLHLT LVDS High-to-Low Transition Time 264 550 ps
tDIS DIN (0:23) Setup to TCLK 4 ns
RL= 100 Ω, CL= 10 pF to GND
Figure 7
tDIH DIN (0:23) Hold from TCLK 4 ns
tHZD DOUT ± HIGH to Tri-state Delay 10 15 ns
RL= 100 Ω,
tLZD DOUT ± LOW to Tri-state Delay 10 15 ns
CL= 10 pF to GND
tZHD DOUT ± Tri-state to HIGH Delay 75 150 ns
Figure 8
tZLD DOUT ± Tri-state to LOW Delay 75 150 ns
tPLD Serializer PLL Lock Time RL= 100 Ω10 ms
RL= 100 Ω, PRE = OFF,
RAOFF = L, TRFB = H, 3.5T+2 3.5T+10
Figure 10
tSD Serializer Delay ns
RL= 100 Ω, PRE = OFF,
RAOFF = L, TRFB = L, 3.5T+2 3.5T+10
Figure 10
5 MHz–43 MHz,
TxOUT TxOUT_Eye_Opening. RL= 100 Ω, CL= 10 pF to GND, 0.76 0.84 UI
_E_O TxOUT_E_O centered on (tBIT/)2 RANDOM pattern
Figure 11
7.8 Deserializer Switching Characteristics
over recommended operating supply and temperature ranges unless otherwise specified
PARAMETER TEST CONDITIONS PIN/FREQ. MIN TYP MAX UNIT
tRCP = tTCP,
tRCP Receiver out Clock Period 23.25 T 200 ns
PTOSEL = H RCLK
Figure 17
PTOSEL = H,
tRDC RCLK Duty Cycle 45% 50% 55%
SLEW = L
LVCMOS Low-to-High Transition
tCLH 1.5 2.5 ns
CL= 4 pF
Time ROUT [0:23],
(lumped load), RCLK, LOCK
LVCMOS High-to-Low Transition SLEW = H
tCHL 1.5 2.5 ns
Time
LVCMOS Low-to-High Transition
tCLH 2.0 3.5 ns
CL= 4 pF
Time ROUT [0:23],
(lumped load), RCLK, LOCK
LVCMOS High-to-Low Transition SLEW = L
tCHL 2.0 3.5 ns
Time
ROUT (0:7) Setup Data to RCLK (0.5×tRCP)–
tROS (0.35)× tRCP ns
PTOSEL = L,
(Group 1) 3 UI
SLEW = H, ROUT[0:7]
ROUT (0:7) Hold Data to RCLK (0.5×tRCP)–
Figure 18
tROH (0.35)× tRCP ns
(Group 1) 3 UI
10 Submit Documentation Feedback Copyright © 2006–2015, Texas Instruments Incorporated
Product Folder Links: DS90UR124-Q1 DS90UR241-Q1
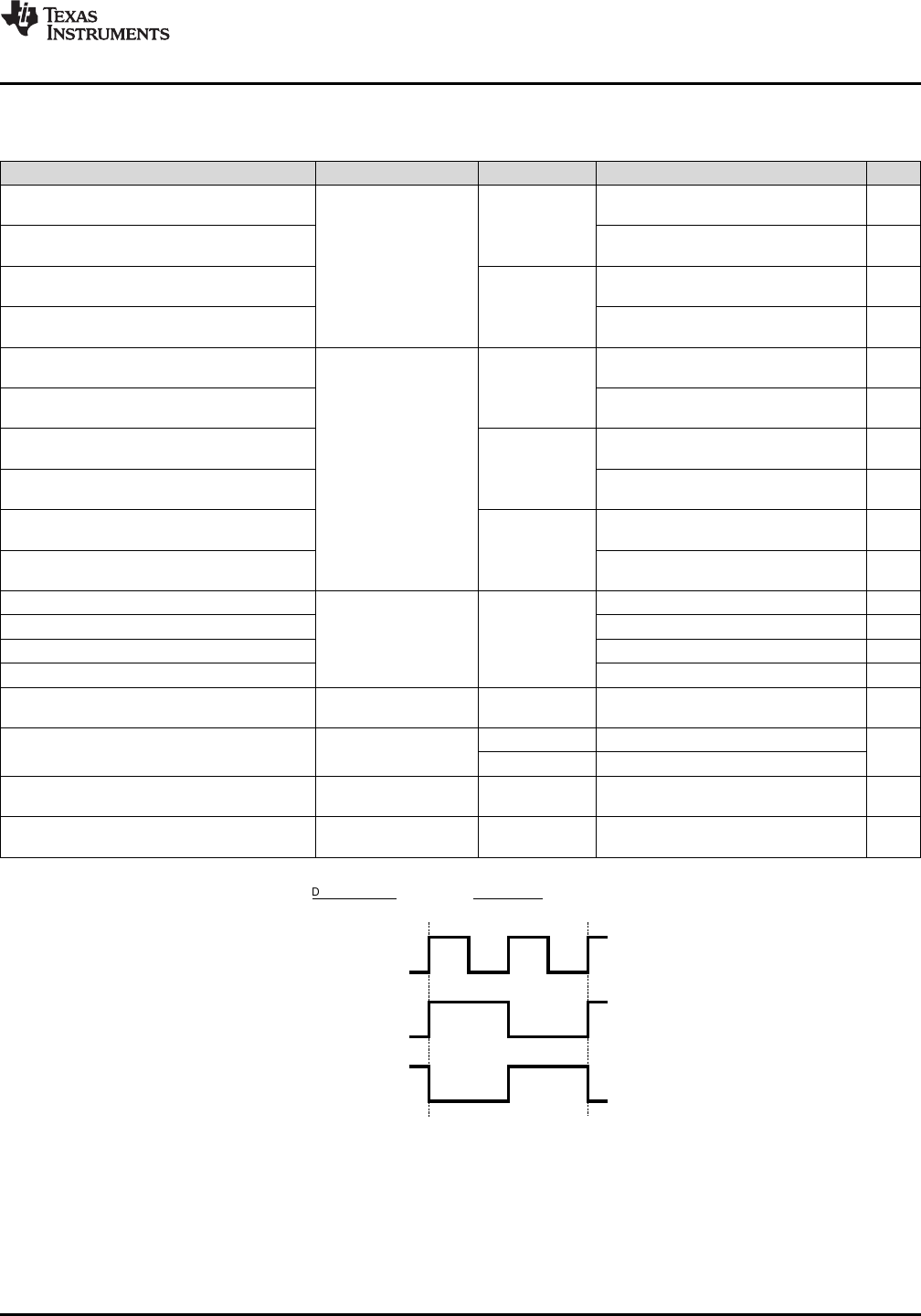
TCLK
ODD DIN
EVEN DIN
Signal PatternDevice Pin Name
DS90UR124-Q1
,
DS90UR241-Q1
www.ti.com
SNLS231O –SEPTEMBER 2006–REVISED APRIL 2015
Deserializer Switching Characteristics (continued)
over recommended operating supply and temperature ranges unless otherwise specified
PARAMETER TEST CONDITIONS PIN/FREQ. MIN TYP MAX UNIT
ROUT (8:15) Setup Data to RCLK (0.5×tRCP)–
tROS (0.35)× tRCP ns
(Group 2) 3 UI
ROUT [8:15],
LOCK
ROUT (8:15) Hold Data to RCLK (0.5×tRCP)–
tROH (0.35)× tRCP ns
PTOSEL = L,
(Group 2) 3 UI
SLEW = H,
ROUT (16:23) Setup Data to RCLK (0.5×tRCP)–
Figure 18
tROS (0.35)× tRCP ns
(Group 3) 3 UI
ROUT [16:23]
ROUT (16:23) Setup Data to RCLK (0.5×tRCP)–
tROH (0.35)× tRCP ns
(Group 3) 3 UI
ROUT (0:7) Setup Data to RCLK (0.5×tRCP)–
tROS (0.35)× tRCP ns
(Group 1) 2 UI
ROUT[0:7]
ROUT (0:7) Hold Data to RCLK (0.5×tRCP)+
tROH (0.35)× tRCP ns
(Group 1) 2 UI
ROUT (8:15) Setup Data to RCLK (0.5×tRCP)−
tROS (0.35)× tRCP ns
PTOSEL = H,
(Group 2) 1 UI
ROUT [8:15],
SLEW = H, LOCK
ROUT (8:15) Hold Data to RCLK (0.5×tRCP)+
Figure 17
tROH (0.35)× tRCP ns
(Group 2) 1 UI
ROUT (16:23) Setup Data to RCLK (0.5×tRCP)+
tROS (0.35)× tRCP ns
(Group 3) 1 UI
ROUT [16:23]
ROUT (16:23) Setup Data to RCLK (0.5×tRCP)–
tROH (0.35)× tRCP ns
(Group 3) 1 UI
tHZR HIGH to Tri-state Delay 3 10 ns
tLZR LOW to Tri-state Delay 3 10 ns
PTOSEL = H, ROUT [0:23],
Figure 16 RCLK, LOCK
tZHR Tri-state to HIGH Delay 3 10 ns
tZLR Tri-state to LOW Delay 3 10 ns
PTOSEL = H, [5+(5/56)]T [5+(5/56)]T
tDD Deserializer Delay RCLK ns
Figure 14 +3.7 +8
5 MHz 128k*T
Deserializer PLL Lock Time from
tDSR See Figure 16 ms
Powerdown 43 MHz 128k*T
RxIN_T See
Receiver INput TOLerance Left 5 MHz–43 MHz 0.25 UI
OL-L Figure 19
RxIN_T See
Receiver INput TOLerance Right 5 MHz–43 MHz 0.25 UI
OL-R Figure 19
Figure 3. Serializer Input Checkerboard Pattern
Copyright © 2006–2015, Texas Instruments Incorporated Submit Documentation Feedback 11
Product Folder Links: DS90UR124-Q1 DS90UR241-Q1
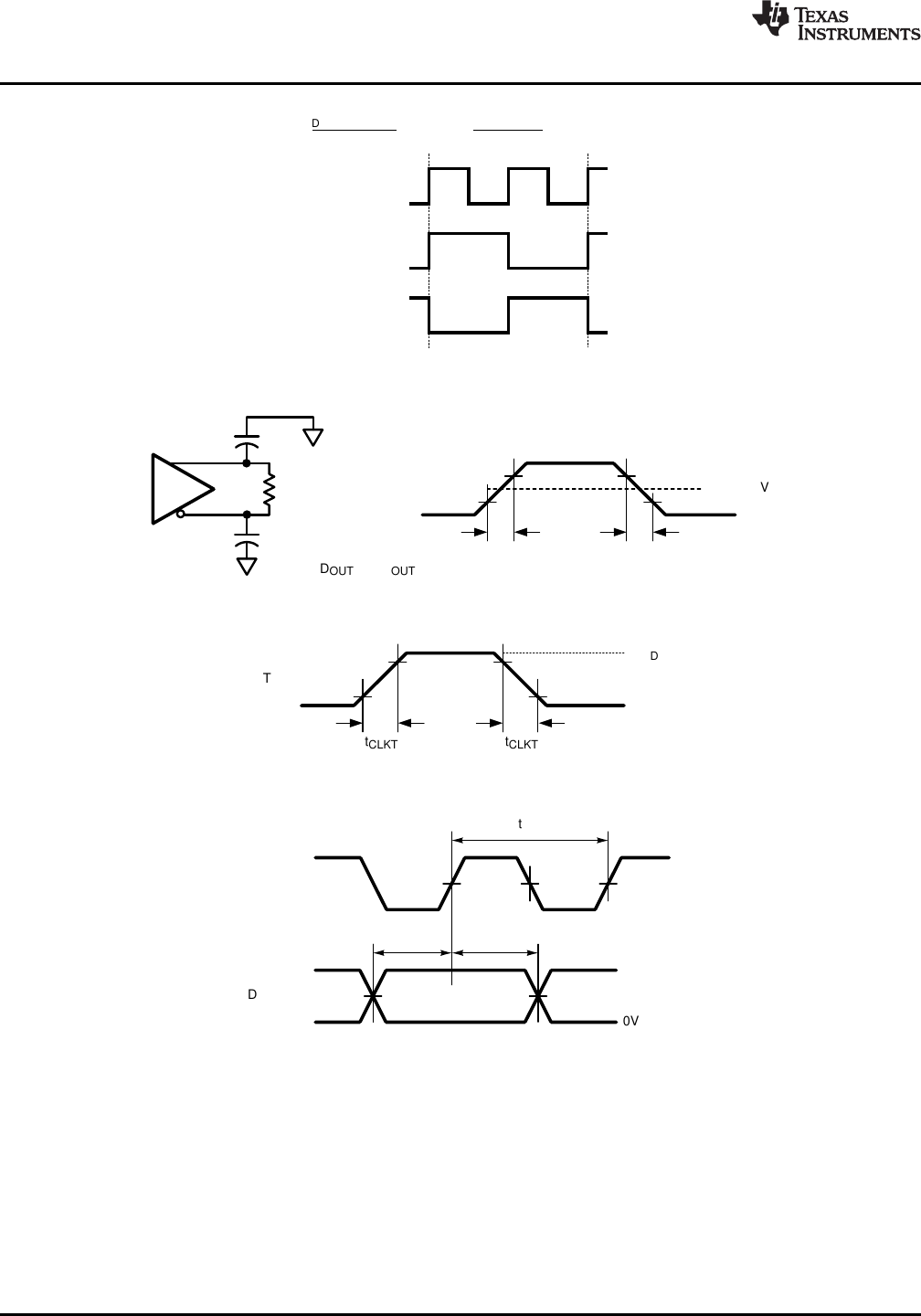
Setup
VDD/2 Hold
tDIH
tDIS
TCLK
DIN [0:23]
tTCP
0V
VDD/2
VDD/2 VDD/2VDD/2
VDD
80%
20%
80%
20%
tCLKT tCLKT
TCLK
VDD
0V
80%
20%
80%
20% Vdiff = 0V
tLLHT tLHLT
Vdiff
Vdiff = (DOUT+) - (DOUT-)
100:
DOUT+
DOUT-10 pF
10 pF
RCLK
ODD ROUT
EVEN ROUT
Signal PatternDevice Pin Name
DS90UR124-Q1
,
DS90UR241-Q1
SNLS231O –SEPTEMBER 2006–REVISED APRIL 2015
www.ti.com
Figure 4. Deserializer Output Checkerboard Pattern
Figure 5. Serializer LVDS Output Load and Transition Times
Figure 6. Serializer Input Clock Transition Times
Figure 7. Serializer Setup and Hold Times
12 Submit Documentation Feedback Copyright © 2006–2015, Texas Instruments Incorporated
Product Folder Links: DS90UR124-Q1 DS90UR241-Q1
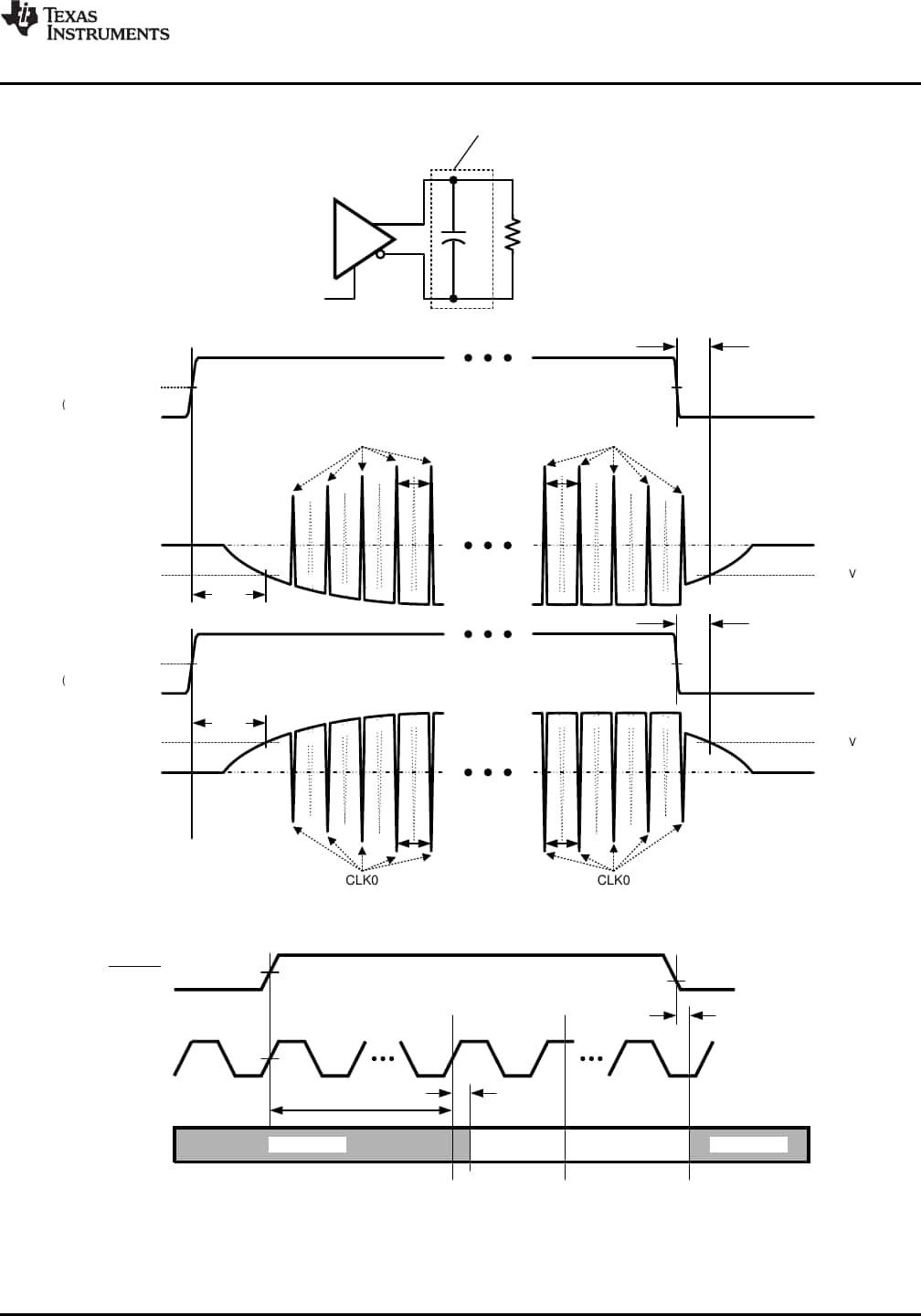
2.0V 0.8V
TCLK
DOUT±
tHZD or
tLZD
tZHD or
tZLD
Output
Active
tPLD
PWDWN
TRI-STATE TRI-STATE
DEN
DOUT-
DOUT+5 pF 100:
Parasitic package and
Trace capacitance
200 mV DCA DCA DCA DCA $OOGDWD³0´V
CLK1
tZLD
tTCP
DCADCADCADCA
CLK1
tTCP
200 mV
DEN
(single-ended)
200 mV DCA DCA DCA DCA $OOGDWD³1´V
CLK0
tZHD
tTCP
DCADCA
DCA
DCA
CLK0
tTCP
200 mV
DOUT±
(differential)
VCC/2
0V
DOUT±
(differential)
0V
VCC/2
tHZD
DEN
(single-ended)
VCC/2
0V 0V
VCC/2
tLZD
DS90UR124-Q1
,
DS90UR241-Q1
www.ti.com
SNLS231O –SEPTEMBER 2006–REVISED APRIL 2015
Figure 8. Serializer Tri-State Test Circuit and Delay
Figure 9. Serializer PLL Lock Time, and TPWDNB Tri-State Delays
Copyright © 2006–2015, Texas Instruments Incorporated Submit Documentation Feedback 13
Product Folder Links: DS90UR124-Q1 DS90UR241-Q1

80%
20%
80%
20%
tCLH
Deserializer
4 pF
lumped
tCHL
PARALLEL-TO-SERIAL
DOUT+
DOUT-
24
DIN RL
TCLK
20194528
Ideal Center Position (tBIT/2)
tBIT (1 UI)
Ideal Data Bit
End
Ideal Data Bit
Beginning
tBIT(1/2 UI) tBIT(1/2 UI)
TxOUT_E_O
23210
||
START
BIT
STOP
BIT
SYMBOL N
23210
||
START
BIT
STOP
BIT
SYMBOL N-1
23210
||
START
BIT
STOP
BIT
SYMBOL N-2
23210
||
START
BIT
STOP
BIT
SYMBOL N-3
23210
STOP
BIT
SYMBOL N-4
||
DOUT0-23
DCA, DCB
|
TCLK
tSD
DIN SYMBOL N+1SYMBOL N SYMBOL N+2 SYMBOL N+3
| |
DS90UR124-Q1
,
DS90UR241-Q1
SNLS231O –SEPTEMBER 2006–REVISED APRIL 2015
www.ti.com
Figure 10. Serializer Delay
Figure 11. Transmitter Output Eye Opening (TxOUT_E_O)
VOD = (DOUT+) – (DOUT−)
Differential output signal is shown as (DOUT+) – (DOUT−), device in Data Transfer mode.
Figure 12. Serializer VOD Diagram
Figure 13. Deserializer LVCMOS Output Load and Transition Times
14 Submit Documentation Feedback Copyright © 2006–2015, Texas Instruments Incorporated
Product Folder Links: DS90UR124-Q1 DS90UR241-Q1
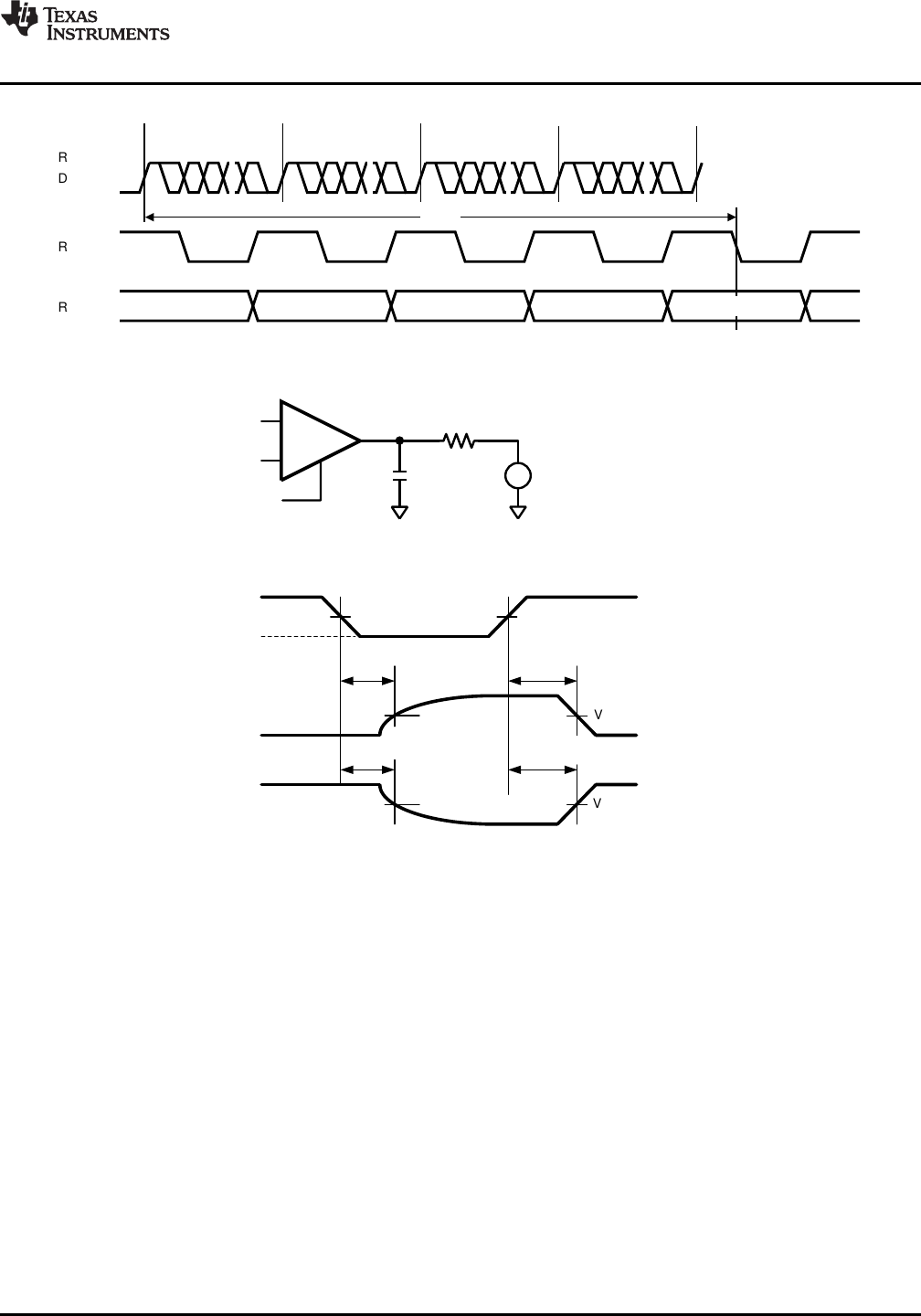
VOH
REN
VOL + 0.5V
VOL
ROUT [23:0]
VOL + 0.5V
tLZR
500:
VREF = VDD/2 for tZLR or tLZR,
VOH - 0.5V VOH + 0.5V
tZLR
tHZR tZHR
VDD/2 VDD/2
VOH
VOL
REN
VREF +
-VREF = 0V for tZHR or tHZR
CL = 8 pF
NOTE:
CL includes instrumentation and fixture capacitance within 6 cm of ROUT [23:0].
23210
||
START
BIT
STOP
BIT
SYMBOL N+3
23210
||
START
BIT
STOP
BIT
SYMBOL N+2
23210
||
START
BIT
STOP
BIT
SYMBOL N+1
23210
||
START
BIT
STOP
BIT
SYMBOL N
RIN0-23
DCA, DCB
RCLK
tDD
ROUT0-23 SYMBOL N-1 SYMBOL NSYMBOL N-2SYMBOL N-3
DS90UR124-Q1
,
DS90UR241-Q1
www.ti.com
SNLS231O –SEPTEMBER 2006–REVISED APRIL 2015
Figure 14. Deserializer Delay
Figure 15. Deserializer Tri-State Test Circuit and Timing
Copyright © 2006–2015, Texas Instruments Incorporated Submit Documentation Feedback 15
Product Folder Links: DS90UR124-Q1 DS90UR241-Q1
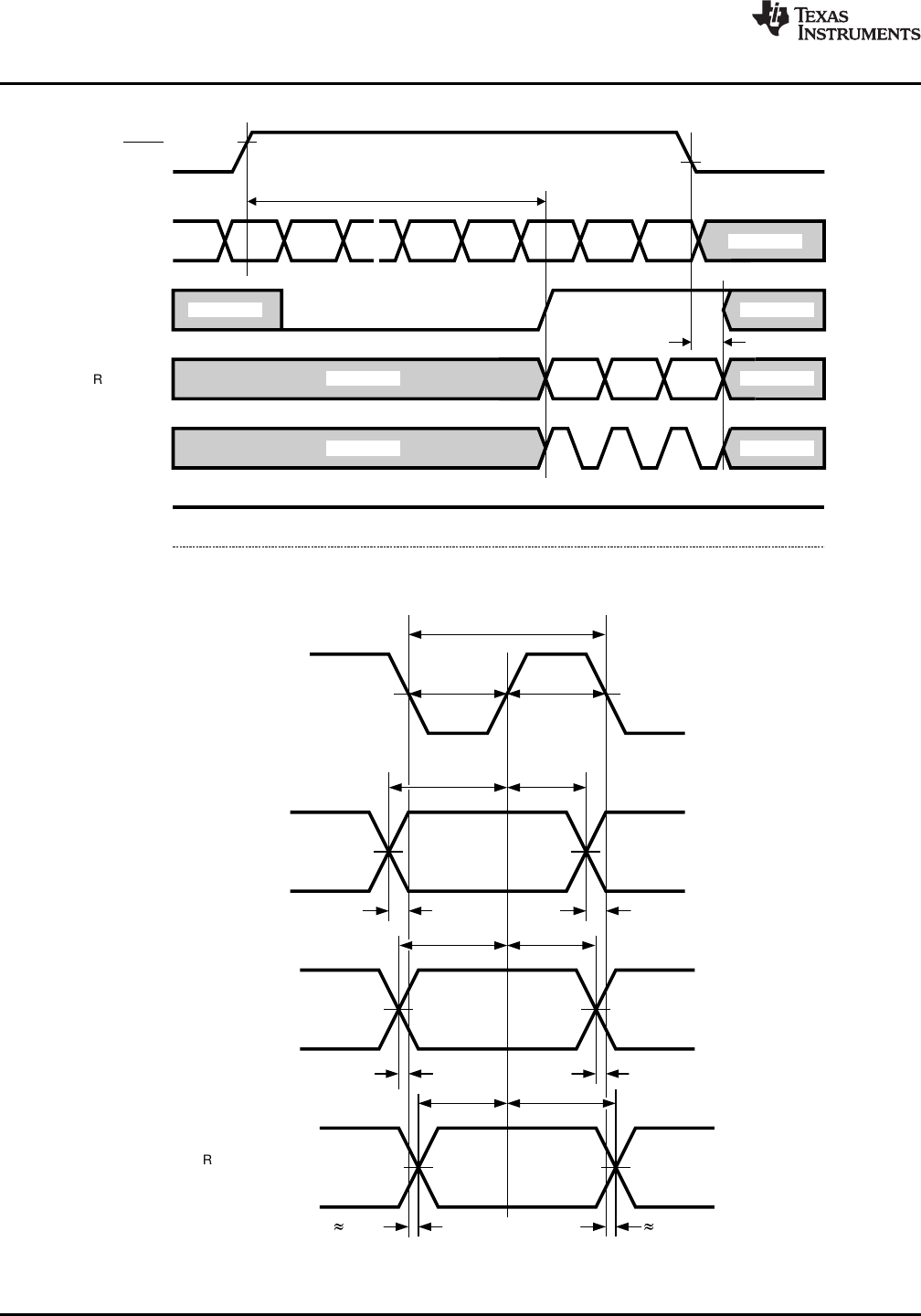
ROUT [7:0]
(group 1)
ROUT [15:8]
(group 2)
Data Valid
Before RCLK Data Valid
After RCLK VDD/2
ROUT [23:16]
(group 3)
RCLK tRDC tRDC
tROS tROH
tROS tROH
tROS tROH
VDD/2
VDD/2VDD/2
VDD/2VDD/2
VDD/2VDD/2
| -2 UI
| -1 UI
| +2 UI
| +1 UI
| +1 UI | -1 UI
tRCP
Data Valid
Before RCLK Data Valid
After RCLK
Data Valid
Before RCLK Data Valid
After RCLK
RIN±
||
TRI-STATE
TRI-STATE
TRI-STATE
TRI-STATE
TRI-STATE
ROUT [0:23]
RCLK
TRI-STATE
LOCK
}v[
tHZR or tLZR
tDSR
REN
PWDN
2.0V
0.8V
DS90UR124-Q1
,
DS90UR241-Q1
SNLS231O –SEPTEMBER 2006–REVISED APRIL 2015
www.ti.com
Figure 16. Deserializer PLL Lock Times and RPWDNB Tri-State Delay
Figure 17. Deserializer Setup and Hold Times and PTO, PTOSEL = H
16 Submit Documentation Feedback Copyright © 2006–2015, Texas Instruments Incorporated
Product Folder Links: DS90UR124-Q1 DS90UR241-Q1
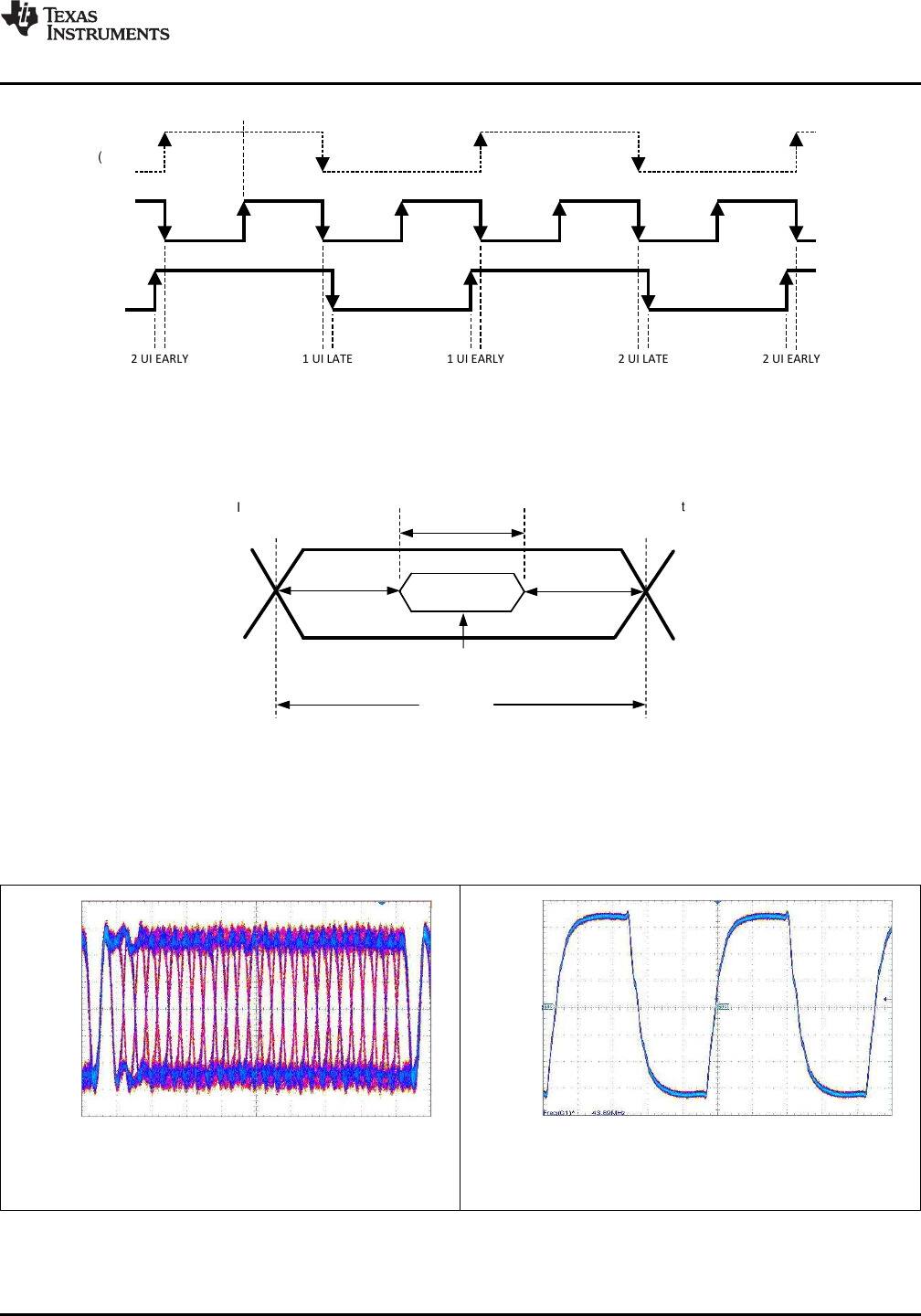
Magnitude (100 mV/DIV)
Time (2.5 ns/DIV)
Magnitude (500 mV/DIV)
Time (5 ns/DIV)
tBIT (1 UI)
Sampling
Window Ideal Data Bit
End
Ideal Data Bit
Beginning
RxIN_TOL -L RxIN_TOL -R
Ideal Center Position (tBIT/2)
½ Symbol
RCLK
½ Symbol
ROUT
(Ideal)
ROUT
GRP1 1 + 3/28 Symbol 1 - 2/28 Symbol 1 + 3/28 Symbol 1 - 4/28 Symbol
2 UI EARLY 1 UI LATE 1 UI EARLY 2 UI LATE 2 UI EARLY
DS90UR124-Q1
,
DS90UR241-Q1
www.ti.com
SNLS231O –SEPTEMBER 2006–REVISED APRIL 2015
Group 1 will be latched internally by sequence of (early 2UI, late 1UI, early 1UI, late 2UI).
Group 2 will be latched internally by sequence of (late 1UI, early 1UI, late 2UI, early 2UI).
Group 3 will be latched internally by sequence of (early 1UI, late 2UI, early 2UI, late 1UI).
Figure 18. Deserializer Setup and Hold Times and PTO Spread, PTOSEL = L
RxIN_TOL_L is the ideal noise margin on the left of the figure, with respect to ideal.
RxIN_TOL_R is the ideal noise margin on the right of the figure, with respect to ideal.
Figure 19. Receiver Input Tolerance (RxIN_TOL) and Sampling Window
7.9 Typical Characteristics
Figure 20. DS90UR241 DOUT± With PCLK at 43 MHz Figure 21. DS90UR124 PCLK Output at 43 MHz
Measured at RIN± Termination
Copyright © 2006–2015, Texas Instruments Incorporated Submit Documentation Feedback 17
Product Folder Links: DS90UR124-Q1 DS90UR241-Q1

DEN
RAOFF
DIN
TRFB
24
REN
RAOFF
TCLK
TPWDNB
SERIALIZER ± DS90UR241
PLL
Timing
and
Control
DOUT-
RT = 100:
RT = 100:
RIN-
DESERIALIZER ± DS90UR124
DOUT+ RIN+
PLL Timing
and
Control
24 ROUT
LOCK
RCLK
Clock
Recovery
Output Latch
Serial to Parallel
DC Balance Decoder
Input Latch
Parallel to Serial
DC Balance Encoder
PRE
PASS
RRFB
RPWDNB
BISTEN
BISTM
SLEW
PTOSEL
VODSEL
DS90UR124-Q1
,
DS90UR241-Q1
SNLS231O –SEPTEMBER 2006–REVISED APRIL 2015
www.ti.com
8 Detailed Description
8.1 Overview
The DS90UR241 Serializer and DS90UR124 Deserializer chipset is an easy-to-use transmitter and receiver pair
that sends 24-bits of parallel LVCMOS data over a single serial LVDS link from 120 Mbps to 1.03 Gbps
throughput. The DS90UR241 transforms a 24-bit wide parallel LVCMOS data into a single high speed LVDS
serial data stream with embedded clock and scrambles / DC Balances the data to enhance signal quality to
support AC coupling. The DS90UR124 receives the LVDS serial data stream and converts it back into a 24-bit
wide parallel data and recovered clock. The 24-bit Serializer/Deserializer chipset is designed to transmit data up
to 10 meters over shielded twisted pair (STP) at clock speeds from 5 MHz to 43 MHz.
The Deserializer can attain lock to a data stream without the use of a separate reference clock source, greatly
simplifying system complexity and overall cost. The Deserializer synchronizes to the Serializer regardless of data
pattern, delivering true automatic “plug and lock” performance. It will lock to the incoming serial stream without
the need of special training patterns or sync characters. The Deserializer recovers the clock and data by
extracting the embedded clock information and validating data integrity from the incoming data stream and then
deserializes the data. The Deserializer monitors the incoming clock information, determines lock status, and
asserts the LOCK output high when lock occurs.
In addition, the Deserializer also supports an optional @SPEED BIST (Built In Self Test) mode, BIST error flag,
and LOCK status reporting pin. Signal quality on the wide parallel output is controlled by the SLEW control and
bank slew (PTOSEL) inputs to help reduce noise and system EMI. Each device has a power down control to
enable efficient operation in various applications.
8.2 Functional Block Diagram
8.3 Feature Description
8.3.1 Initialization and Locking Mechanism
Initialization of the DS90UR241 and DS90UR124 must be established before each device sends or receives
data. Initialization refers to synchronizing the Serializer’s and Deserializer’s PLL’s together. After the Serializers
locks to the input clock source, the Deserializer synchronizes to the Serializers as the second and final
initialization step.
18 Submit Documentation Feedback Copyright © 2006–2015, Texas Instruments Incorporated
Product Folder Links: DS90UR124-Q1 DS90UR241-Q1
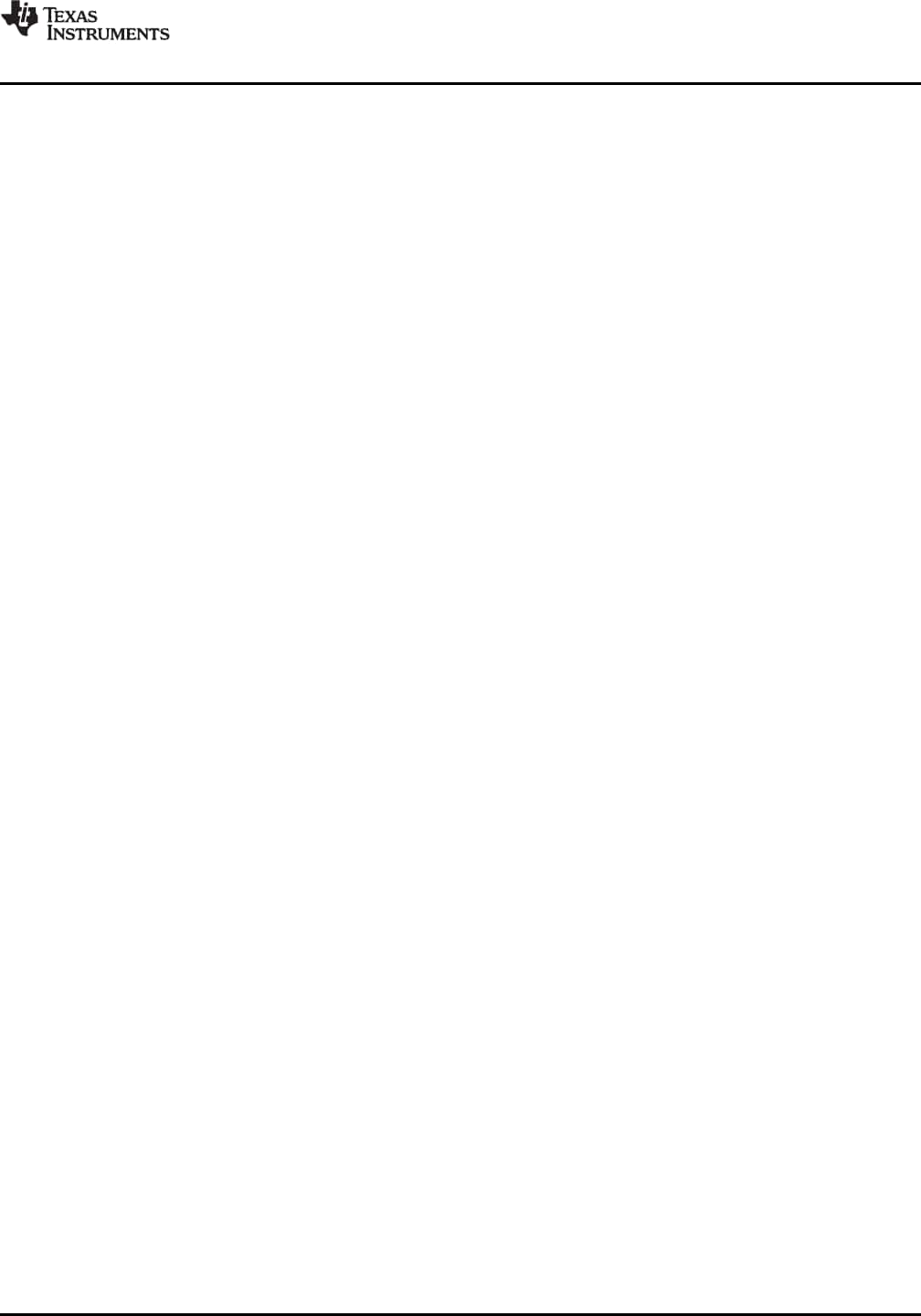
DS90UR124-Q1
,
DS90UR241-Q1
www.ti.com
SNLS231O –SEPTEMBER 2006–REVISED APRIL 2015
Feature Description (continued)
Step 1: When VDD is applied to both Serializer and/or Deserializer, the respective outputs are held in Tri-state
and internal circuitry is disabled by on-chip power-on circuitry. When VDD reaches VDD OK (approximately 2.2 V)
the PLL in Serializer begins locking to a clock input. For the Serializer, the local clock is the transmit clock,
TCLK. The Serializer outputs are held in Tri-state while the PLL locks to the TCLK. After locking to TCLK, the
Serializer block is now ready to send data patterns. The Deserializer output will remain in Tri-state while its PLL
locks to the embedded clock information in serial data stream. Also, the Deserializer LOCK output will remain low
until its PLL locks to incoming data and sync-pattern on the RIN± pins.
Step 2: The Deserializer PLL acquires lock to a data stream without requiring the Serializer to send special
patterns. The Serializer that is generating the stream to the Deserializer will automatically send random (non-
repetitive) data patterns during this step of the Initialization State. The Deserializer will lock onto embedded clock
within the specified amount of time. An embedded clock and data recovery (CDR) circuit locks to the incoming bit
stream to recover the high-speed receive bit clock and re-time incoming data. The CDR circuit expects a coded
input bit stream. In order for the Deserializer to lock to a random data stream from the Serializer, it performs a
series of operations to identify the rising clock edge and validates data integrity, then locks to it. Because this
locking procedure is independent on the data pattern, total random locking duration may vary. At the point when
the Deserializer’s CDR locks to the embedded clock, the LOCK pin goes high and valid RCLK/data appears on
the outputs. Note that the LOCK signal is synchronous to valid data appearing on the outputs. The Deserializer’s
LOCK pin is a convenient way to ensure data integrity is achieved on receiver side.
8.3.2 Data Transfer
After Serializer lock is established, the inputs DIN0–DIN23 are used to input data to the Serializer. Data is
clocked into the Serializer by the TCLK input. The edge of TCLK used to strobe the data is selectable via the
TRFB pin. TRFB high selects the rising edge for clocking data and low selects the falling edge. The Serializer
outputs (DOUT±) are intended to drive point-to-point connections.
CLK1, CLK0, DCA, DCB are four overhead bits transmitted along the single LVDS serial data stream (Figure 30).
The CLK1 bit is always high and the CLK0 bit is always low. The CLK1 and CLK0 bits function as the embedded
clock bits in the serial stream. DCB functions as the DC Balance control bit. It does not require any pre-coding of
data on transmit side. The DC Balance bit is used to minimize the short and long-term DC bias on the signal
lines. This bit operates by selectively sending the data either unmodified or inverted. The DCA bit is used to
validate data integrity in the embedded data stream. Both DCA and DCB coding schemes are integrated and
automatically performed within Serializer and Deserializer.
The chipset supports clock frequency ranges of 5 MHz to 43 MHz. Every clock cycle, 24 databits are sent along
with 4 additional overhead control bits. Thus the line rate is 1.20 Gbps maximum (140Mbps minimum). The link is
extremely efficient at 86% (24/28). Twenty five (24 data + 1 clock) plus associated ground signals are reduced to
only 1 single LVDS pair providing a compression ratio of better then 25 to 1.
In the serialized data stream, data/embedded clock & control bits (24+4 bits) are transmitted from the Serializer
data output (DOUT±) at 28 times the TCLK frequency. For example, if TCLK is 43 MHz, the serial rate is 43 × 28
= 1.20 Giga bits per second. Since only 24 bits are from input data, the serial “payload” rate is 24 times the
TCLK frequency. For instance, if TCLK = 43 MHz, the payload data rate is 43 x 24 = 1.03 Gbps. TCLK is
provided by the data source and must be in the range of 5 MHz to 43 MHz nominal. The Serializer outputs
(DOUT±) can drive a point-to-point connection as shown in Figure 29. The outputs transmit data when the enable
pin (DEN) is high and TPWDNB is high. The DEN pin may be used to Tri-state the outputs when driven low.
When the Deserializer channel attains lock to the input from a Serializer, it drives its LOCK pin high and
synchronously delivers valid data and recovered clock on the output. The Deserializer locks onto the embedded
clock, uses it to generate multiple internal data strobes, and then drives the recovered clock to the RCLK pin.
The recovered clock (RCLK output pin) is synchronous to the data on the ROUT[23:0] pins. While LOCK is high,
data on ROUT[23:0] is valid. Otherwise, ROUT[23:0] is invalid. The polarity of the RCLK edge is controlled by the
RRFB input. ROUT[23:0], LOCK and RCLK outputs will each drive a maximum of 4-pF load with a 43-MHz clock.
REN controls Tri-state for ROUTn and the RCLK pin on the Deserializer.
Copyright © 2006–2015, Texas Instruments Incorporated Submit Documentation Feedback 19
Product Folder Links: DS90UR124-Q1 DS90UR241-Q1
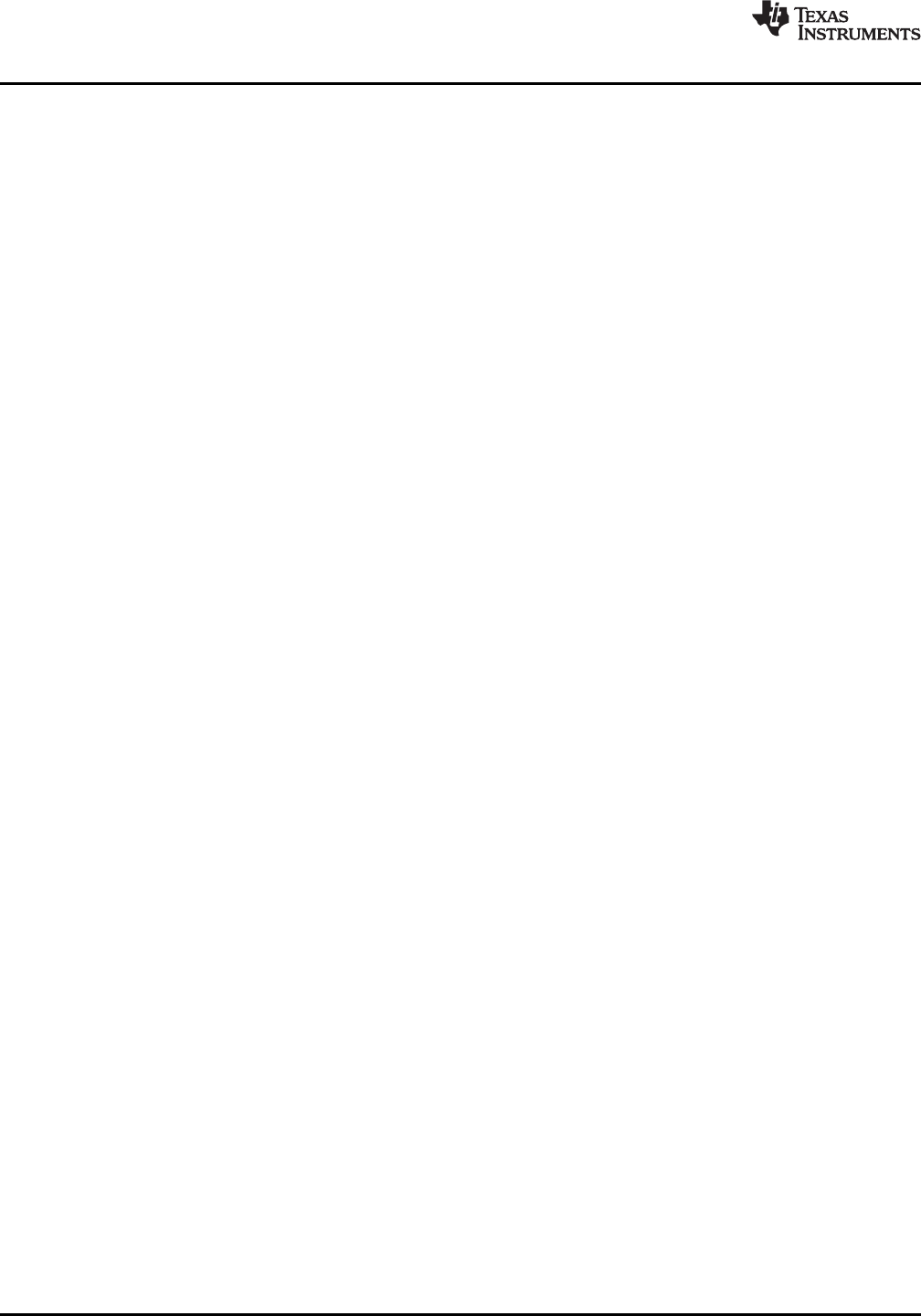
DS90UR124-Q1
,
DS90UR241-Q1
SNLS231O –SEPTEMBER 2006–REVISED APRIL 2015
www.ti.com
Feature Description (continued)
8.3.3 Resynchronization
If the Deserializer loses lock, it will automatically try to re-establish lock. For example, if the embedded clock
edge is not detected one time in succession, the PLL loses lock and the LOCK pin is driven low. The Deserializer
then enters the operating mode where it tries to lock to a random data stream. It looks for the embedded clock
edge, identifies it, and then proceeds through the locking process.
The logic state of the LOCK signal indicates whether the data on ROUT is valid; when it is high, the data is valid.
The system may monitor the LOCK pin to determine whether data on the ROUT is valid.
8.3.4 Powerdown
The Powerdown state is a low power sleep mode that the Serializer and Deserializer may use to reduce power
when no data is being transferred. The TPWDNB and RPWDNB are used to set each device into powerdown
mode, which reduces supply current to the µA range. The Serializer enters powerdown when the TPWDNB pin is
driven low. In powerdown, the PLL stops and the outputs go into Tri-state, disabling load current and reducing
current supply. To exit Powerdown, TPWDNB must be driven high. When the Serializer exits Powerdown, its PLL
must lock to TCLK before it is ready for the Initialization state. The system must then allow time for Initialization
before data transfer can begin. The Deserializer enters powerdown mode when RPWDNB is driven low. In
powerdown mode, the PLL stops and the outputs enter Tri-state. To bring the Deserializer block out of the
powerdown state, the system drives RPWDNB high.
Both the Serializer and Deserializer must reinitialize and relock before data can be transferred. The Deserializer
will initialize and assert LOCK high when it is locked to the embedded clock.
8.3.5 Tri-State
For the Serializer, Tri-state is entered when the DEN or TPWDNB pin is driven low. This will Tri-state both driver
output pins (DOUT+ and DOUT−). When DEN is driven high, the serializer will return to the previous state as
long as all other control pins remain static (TPWDNB, TRFB).
When you drive the REN or RPWDNB pin low, the Deserializer enters Tri-state. Consequently, the receiver
output pins (ROUT0–ROUT23) and RCLK will enter Tri-state. The LOCK output remains active, reflecting the
state of the PLL. The Deserializer input pins are high impedance during receiver powerdown (RPWDNB low) and
power-off (VDD = 0 V).
8.3.6 Pre-Emphasis
The DS90UR241 features a Pre-Emphasis function used to compensate for long or lossy transmission media.
Cable drive is enhanced with a user selectable Pre-Emphasis feature that provides additional output current
during transitions to counteract cable loading effects. The transmission distance will be limited by the loss
characteristics and quality of the media. Pre-Emphasis adds extra current during LVDS logic transition to reduce
the cable loading effects and increase driving distance. In addition, Pre-Emphasis helps provide faster
transitions, increased eye openings, and improved signal integrity. The ability of the DS90UR241 to use the Pre-
Emphasis feature will extend the transmission distance up to 10 meters in most cases.
To enable the Pre-Emphasis function, the “PRE” pin requires one external resistor (Rpre) to Vss in order to set
the additional current level. Values of Rpre should be between 6 kΩand 100 MΩ. Values less than 6 kΩshould
not be used. A lower input resistor value on the ”PRE” pin increases the magnitude of dynamic current during
data transition. The additional source current is based on the following formula: PRE = (RPRE ≥6 kΩ); IMAX = [48 /
RPRE]. For example if Rpre = 15 kΩ, then the Pre-Emphasis current is increase by an additional 3.2 mA.
The amount of Pre-Emphasis for a given media will depend on the transmission distance of the application. In
general, too much Pre-Emphasis can cause over or undershoot at the receiver input pins. This can result in
excessive noise, crosstalk and increased power dissipation. For short cables or distances, Pre-Emphasis may
not be required. Signal quality measurements are recommended to determine the proper amount of Pre-
Emphasis for each application.
20 Submit Documentation Feedback Copyright © 2006–2015, Texas Instruments Incorporated
Product Folder Links: DS90UR124-Q1 DS90UR241-Q1
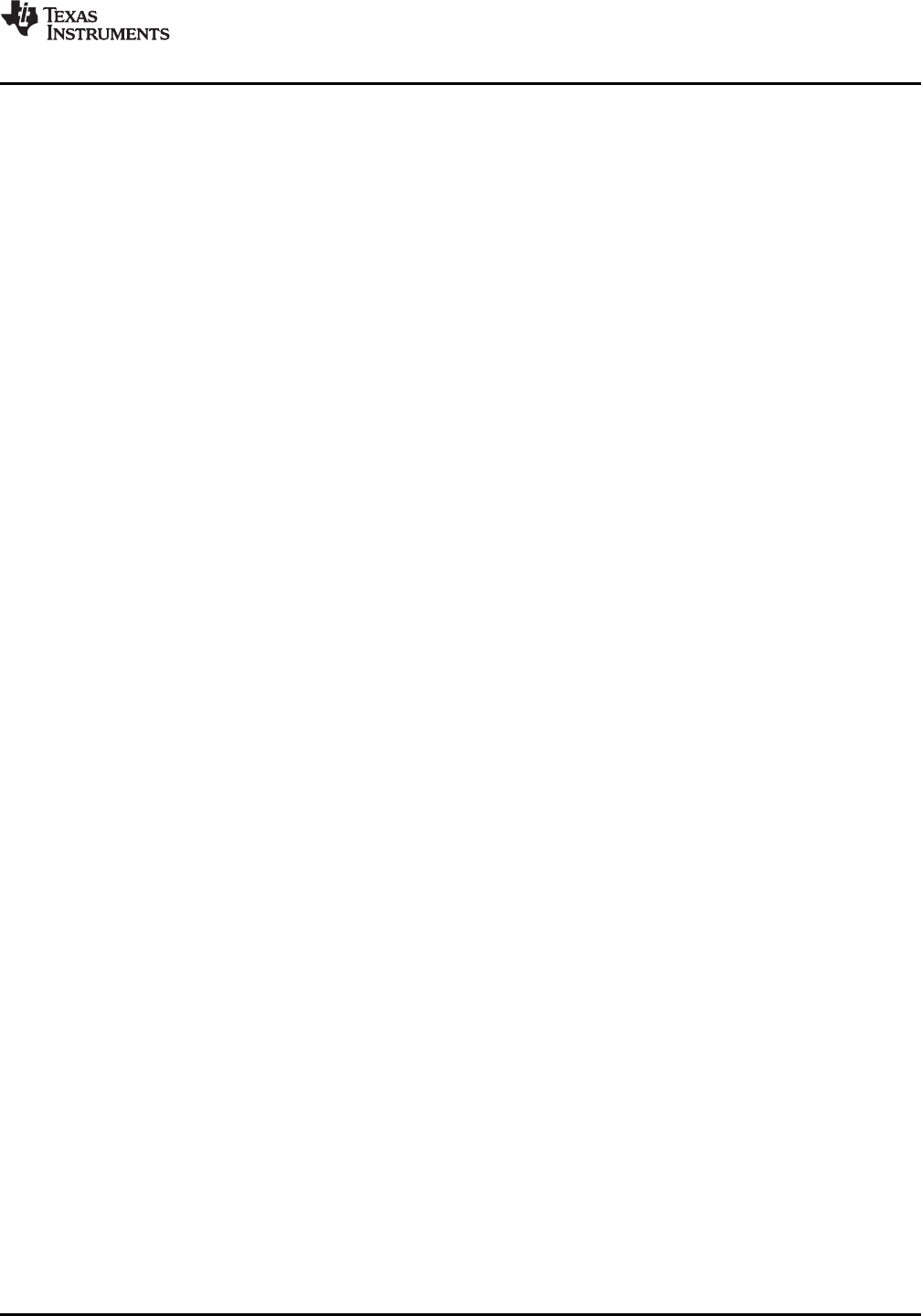
DS90UR124-Q1
,
DS90UR241-Q1
www.ti.com
SNLS231O –SEPTEMBER 2006–REVISED APRIL 2015
Feature Description (continued)
8.3.7 AC-Coupling and Termination
The DS90UR241 and DS90UR124 supports AC-coupled interconnects through integrated DC balanced
encoding/decoding scheme. To use the Serializer and Deserializer in an AC-coupled application, insert external
AC-coupling capacitors in series in the LVDS signal path as illustrated in Figure 29. The Deserializer input stage
is designed for AC-coupling by providing a built-in AC bias network which sets the internal VCM to +1.8V. With AC
signal coupling, capacitors provide the AC-coupling path to the signal input.
For the high-speed LVDS transmissions, the smallest available package should be used for the AC-coupling
capacitor. This will help minimize degradation of signal quality due to package parasitics. The most common
used capacitor value for the interface is a 100 nF (0.1 uF). NPO class 1 or X7R class 2 type capacitors are
recommended. 50 WVDC should be the minimum used for the best system-level ESD performance.
A termination resistor across DOUT± and RIN± is also required for proper operation to be obtained. The
termination resistor should be equal to the differential impedance of the media being driven. This should be in the
range of 90 to 132 Ω. 100 Ωis a typical value common used with standard 100-Ωtransmission media. This
resistor is required for control of reflections and also completes the current loop. It should be placed as close to
the Serializer DOUT± outputs and Deserializer RIN± inputs to minimize the stub length from the pins. To match
with the deferential impedance on the transmission line, the LVDS I/O are terminated with 100-Ωresistors on
Serializer DOUT± outputs pins and Deserializer RIN± input pins.
8.3.7.1 Receiver Termination Option 1
A single 100-Ωtermination resistor is placed across the RIN± pins (see Figure 29). This provides the signal
termination at the Receiver inputs. Other options may be used to increase noise tolerance.
8.3.7.2 Receiver Termination Option 2
For additional EMI tolerance, two 50-Ωresistors may be used in place of the single 100-Ωresistor. A small
capacitor is tied from the center point of the 50-Ωresistors to ground (see Figure 31). This provides a high-
frequency low impedance path for noise suppression. Value is not critical, 4.7 nF may be used with general
applications.
8.3.7.3 Receiver Termination Option 3
For high noise environments, an additional voltage divider network may be connected to the center point. This
has the advantage of a providing a DC low-impedance path for noise suppression. Use resistor values in the
range of 100Ω-2KΩfor the pullup and pulldown. Ratio the resistor values to bias the center point at 1.8 V. For
example (see Figure 32): VDD=3.3 V, Rpullup=1 KΩ, Rpulldown=1.2 KΩ; or Rpullup=100 Ω, Rpulldown=120 Ω
(strongest). The smaller values will consume more bias current, but will provide enhanced noise suppression.
8.3.8 Signal Quality Enhancers
The DS90UR124 Deserializer supports two signal quality enhancers. The SLEW pin is used to increase the drive
strength of the LVCMOS outputs when driving heavy loads. SLEW allows output drive strength for high or low
current drive. Default setting is LOW for low drive at 2 mA and HIGH for high drive at 4 mA.
There are two types of Progressive Turnon modes (Fixed and PTO Frequency Spread) to help reduce EMI:
simultaneous switching noise and system ground bounce. The PTOSEL pin introduces bank skew in the
data/clock outputs to limit the number of outputs switching simultaneously. For Fixed-PTO mode, the Deserializer
ROUT[23:0] outputs are grouped into three groups of eight, with each group switching about 2 or 1 UI apart in
phase from RCLK for Group 1 and Groups 2, 3, respectively (see Figure 17). In the PTO Frequency Spread
mode, ROUT[23:0] are also grouped into three groups of eight, with each group is separated out of phase with
the adjacent groups (see Figure 18) per every 4 cycles. Note that in the PTO Frequency Spread operating mode
RCLK is also spreading and separated by 1 UI.
Copyright © 2006–2015, Texas Instruments Incorporated Submit Documentation Feedback 21
Product Folder Links: DS90UR124-Q1 DS90UR241-Q1
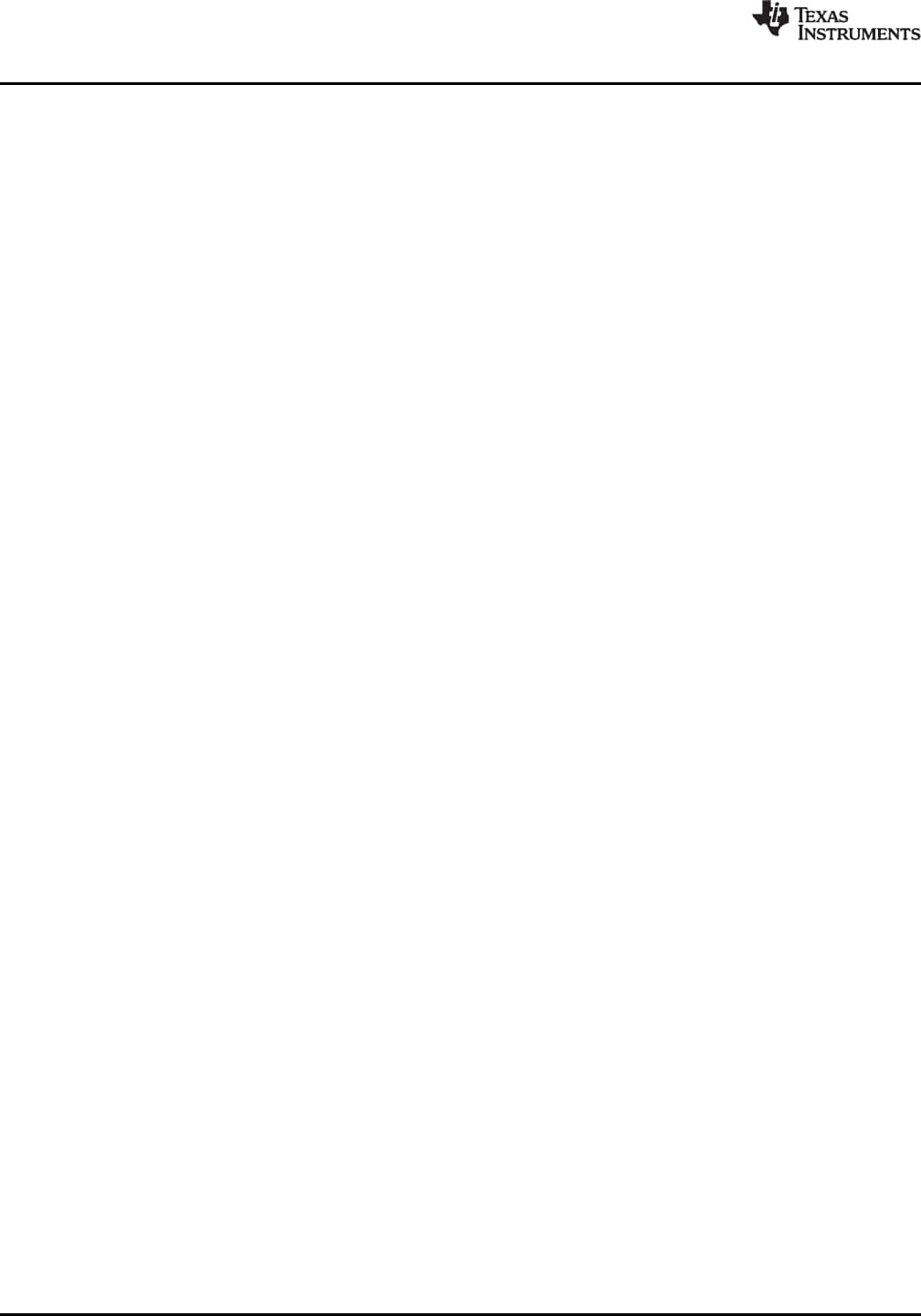
DS90UR124-Q1
,
DS90UR241-Q1
SNLS231O –SEPTEMBER 2006–REVISED APRIL 2015
www.ti.com
Feature Description (continued)
8.3.9 @SPEED-BIST Test Feature
To assist vendors with test verification, the DS90UR241 and DS90UR124 is equipped with built-in self-test
(BIST) capability to support both system manufacturing and field diagnostics. BIST mode is intended to check the
entire high-speed serial link at full link-speed, without the use of specialized and expensive test equipment. This
feature provides a simple method for a system host to perform diagnostic testing of both Serializer and
Deserializer. The BIST function is easily configured through the 2 control pins on the DS90UR124. When the
BIST mode is activated, the Serializer has the ability to transfer an internally generated PRBS data pattern. This
pattern traverses across interconnecting links to the Deserializer. The DS90UR124 includes an on-chip PRBS
pattern verification circuit that checks the data pattern for bit errors and reports any errors on the data output pins
on the Deserializer.
The @SPEED-BIST feature uses 2 signal pins (BISTEN and BISTM) on the DS90UR124 Deserializer. The
BISTEN and BISTM pins together determine the functions of the BIST mode. The BISTEN signal (HIGH)
activates the test feature on the Deserializer. After the BIST mode is enabled, all the data input channels
DIN[23:0] on the DS90UR241 Serializer must be set logic LOW or floating in order for Deserializer to start
accepting data. An input clock signal (TCLK) for the Serializer must also be applied during the entire BIST
operation. The BISTM pin selects error reporting status mode of the BIST function. When BIST is configured in
the error status mode (BISTM = LOW), each of the ROUT[23:0] outputs will correspond to bit errors on a cycle-
by-cycle basis. The result of bit mismatches are indicated on the respective parallel inputs on the ROUT[23:0]
data output pins. In the BIST error-count accumulator mode (BISTM = HIGH), an 8-bit counter on ROUT[7:0] is
used to represent the number of errors detected (0 to 255 max). The successful completion of the BIST test is
reported on the PASS pin on the Deserializer. The Deserializer's PLL must first be locked to ensure the PASS
status is valid. The PASS status pin will stay LOW and then transition to HIGH once a BER of 1x10-9 is achieved
across the transmission link.
8.3.10 Backward-Compatible Mode With DS90C241 and DS90C124
The RAOFF pin allows a backward-compatible mode with DS90C241 and DS90C124 devices. To interface with
either DS90C241 Serializer or DS90C124 Deserializer, the RAOFF pin on DS90UR241 or DS90UR124 must be
tied HIGH to disable the additional LSFR coding. For normal operation directly with DS90UR241 to DS90UR124,
RAOFF pins are set LOW. See Table 1 and Table 2 for more details.
22 Submit Documentation Feedback Copyright © 2006–2015, Texas Instruments Incorporated
Product Folder Links: DS90UR124-Q1 DS90UR241-Q1

DS90UR124-Q1
,
DS90UR241-Q1
www.ti.com
SNLS231O –SEPTEMBER 2006–REVISED APRIL 2015
8.4 Device Functional Modes
Table 1. DS90UR241 Serializer Truth Table
TPWDNB DEN RAOFF Tx PLL Status LVDS Outputs
(Pin 9) (Pin 18) (Pin 12) (Internal) (Pins 19 and 20)
L X X X Hi-Z
H L X X Hi-Z
H H X Not Locked Hi-Z
H H L Locked Serialized Data with Embedded Clock
(DS90UR124 compatible)
H H H Locked Serialized Data with Embedded Clock
(DS90C124 compatible)
Table 2. DS90UR124 Deserializer Truth Table
RPWDNB REN RAOFF Rx PLL Status ROUTn and RCLK LOCK
(Pin 48) (Pin 60) (Pin 63) (Internal) (See Pin Diagram) (Pin 23)
L X X X Hi Z Hi Z
H L X X Hi Z L = PLL Unocked;
H = PLL Locked
H H X Not Locked Hi Z L
H H L Locked Data and RCLK Active H
(DS90UR241 compatible)
H H H Locked Data and RCLK Active H
(DS90C241 compatible)
Copyright © 2006–2015, Texas Instruments Incorporated Submit Documentation Feedback 23
Product Folder Links: DS90UR124-Q1 DS90UR241-Q1
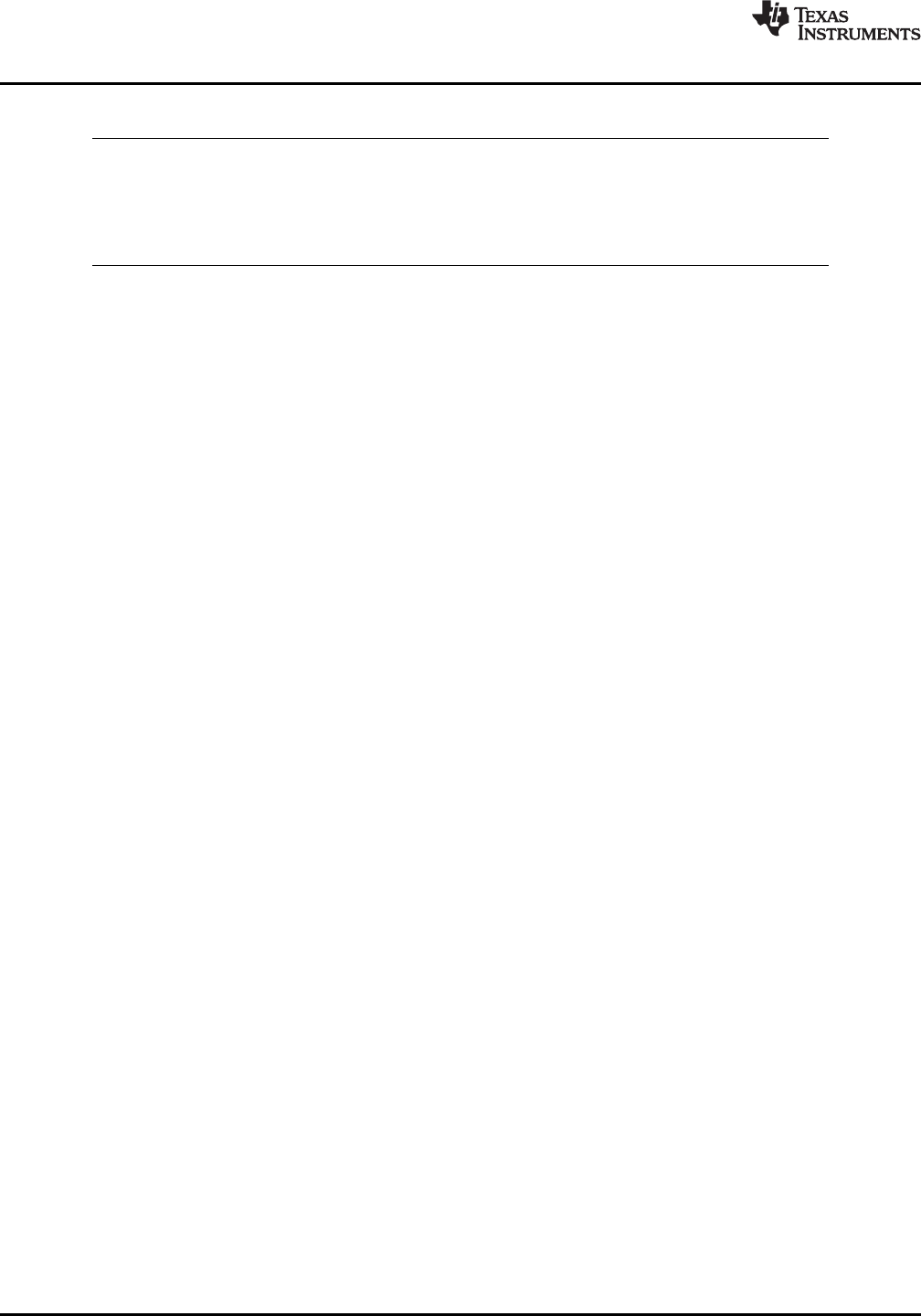
DS90UR124-Q1
,
DS90UR241-Q1
SNLS231O –SEPTEMBER 2006–REVISED APRIL 2015
www.ti.com
9 Application and Implementation
NOTE
Information in the following applications sections is not part of the TI component
specification, and TI does not warrant its accuracy or completeness. TI’s customers are
responsible for determining suitability of components for their purposes. Customers should
validate and test their design implementation to confirm system functionality.
9.1 Application Information
9.1.1 Using the DS90UR241 and DS90UR124
The DS90UR241/DS90UR124 Serializer/Deserializer (SERDES) pair sends 24 bits of parallel LVCMOS data
over a serial LVDS link up to 1.03 Gbps. Serialization of the input data is accomplished using an onboard PLL at
the Serializer which embeds clock with the data. The Deserializer extracts the clock/control information from the
incoming data stream and deserializes the data. The Deserializer monitors the incoming clock information to
determine lock status and will indicate lock by asserting the LOCK output high.
9.1.2 Display Application
The DS90URxxx-Q1 chipset is intended for interface between a host (graphics processor) and a Display. It
supports an 18-bit color depth (RGB666) and up to 1280 × 480 display formats. In a RGB666 configuration 18
color bits (R[5:0], G[5:0], B[5:0]), Pixel Clock (PCLK) and 3 control bits (VS, HS and DE) along with 3 spare bits
are supported across the serial link with PCLK rates from 5 to 43 MHz.
9.1.3 Typical Application Connection
Figure 22 shows a typical application of the DS90UR241 Serializer (SER). The LVDS outputs use a 100-Ω
termination and 100-nF coupling capacitors to the line. Bypass capacitors are placed near the power supply pins.
At a minimum, three 0.1-uF capacitors should be used for local bypassing. A system GPO (General Purpose
Output) controls the TPWDNB pin. In this application the TRFB pin is tied High to latch data on the rising edge of
the TCLK. The DEN signal is not used and is tied High also. The application is to the companion Deserializer
(DS90UR124) so the RAOFF pin is tied low to scramble the data and improve link signal quality. In this
application the link is typical, therefore the VODSEL pin is tied Low for the standard LVDS swing. The pre-
emphasis input uses a resistor to ground to set the amount of pre-emphasis desired by the application.
Figure 26 shows a typical application of the DS90UR124 Deserializer (DES). The LVDS inputs use a 100-Ω
termination and 100-nF coupling capacitors to the line. Bypass capacitors are placed near the power supply pins.
At a minimum, four 0.1-uF capacitors should be used for local bypassing. A system GPO (general-purpose
output) controls the RPWDNB pin. In this application the RRFB pin is tied High to strobe the data on the rising
edge of the RCLK. The REN signal is not used and is tied High also. The application is to the companion
Serializer (DS90UR241) so the RAOFF pin is tied low to descramble the data. Output (LVCMOS) signal quality is
set by the SLEW pin, and the PTOSEL pin can be used to reduce simultaneous output switching by introducing a
small amount of delay between output banks.
24 Submit Documentation Feedback Copyright © 2006–2015, Texas Instruments Incorporated
Product Folder Links: DS90UR124-Q1 DS90UR241-Q1
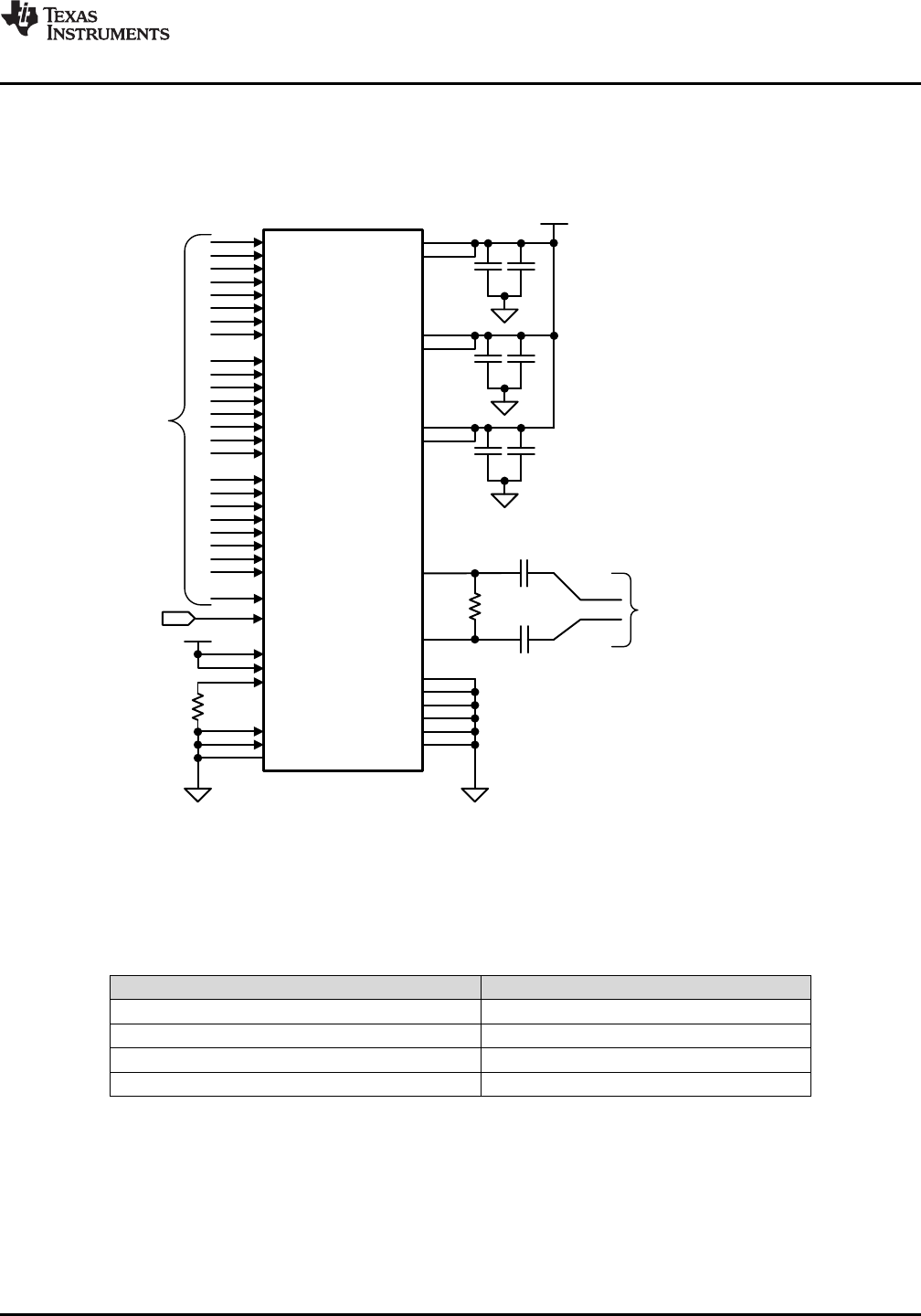
DIN0
DIN1
DIN2
DIN3
DIN4
DIN5
DIN6
DIN7
DIN8
DIN9
DIN10
DIN11
DIN12
DIN13
DIN14
DIN15
DIN16
DIN17
DIN18
DIN19
DIN20
DIN21
DIN22
DIN23
TCLK
TPWDNB
DEN
TRFB
RAOFF
VODSEL
PRE
RES0(3)
DOUT+
DOUT-
VDD
VSS
VDD
VSS
VSS
VSS
VSS
VSS
VDD
VDD
VDD
VDD
Notes:
TPWDNB = System GPO
DEN = High (ON)
TRFB = High (Rising edge)
RAOFF = Low (Default)
VODSEL = Low (500 mV)
PRE = Rpre
RES0 = Low
3.3V
3.3V
DS90UR241 (SER)
C4 C1
C5 C2
C6 C3
C7
C8
R1
R2 C1 to C3 = 0.1 PF
C4 to C6 = 0.01 PF (optional)
C7 to C8 = 100 nF50WVDC, NPO or X7R
R1 = 100 :
R2 = Open (OFF)
or Rpre 8 6 k: (ON) (cable specific)
LVCMOS
Parallel
Interface
Serial
LVDS
Interface
GPOs if used, or tie High (ON)
DS90UR124-Q1
,
DS90UR241-Q1
www.ti.com
SNLS231O –SEPTEMBER 2006–REVISED APRIL 2015
9.2 Typical Applications
9.2.1 DS90UR241-Q1 Typical Application Connection
Figure 22. DS90UR241 Connection Diagram
9.2.1.1 Design Requirements
Table 3. DS90UR241 Design Parameter
DESIGN PARAMETER EXAMPLE VALUE
VDD 3.3 V
AC Coupling Capacitor for DOUT± 100 nF
DOUT± External Termination 100 Ω
PCLK Frequency 33 MHz
9.2.1.2 Detailed Design Procedure
Figure 22 shows a typical application of the DS90UR241 serializer for an 33-MHz 18-bit Color Display
Application. The DOUT± outputs must have a series external 0.1-μF AC-coupling capacitor and 100-Ωparallel
termination on the high-speed serial lines. The serializer does not have an internal termination. Bypass
capacitors are placed near the power supply pins. At a minimum, three 0.1-μF capacitors should be used for
local device bypassing. Additional capacitors may be needed as the number and values of the capacitors will
depend on meeting the power noise specification of the part. Ferrite beads may be needed on the VDDs for
effective noise suppression. The interface to the graphics source is with 3.3-V LVCMOS levels. An RC delay is
placed on the PDB signal to delay the enabling of the device until power is stable.
Copyright © 2006–2015, Texas Instruments Incorporated Submit Documentation Feedback 25
Product Folder Links: DS90UR124-Q1 DS90UR241-Q1
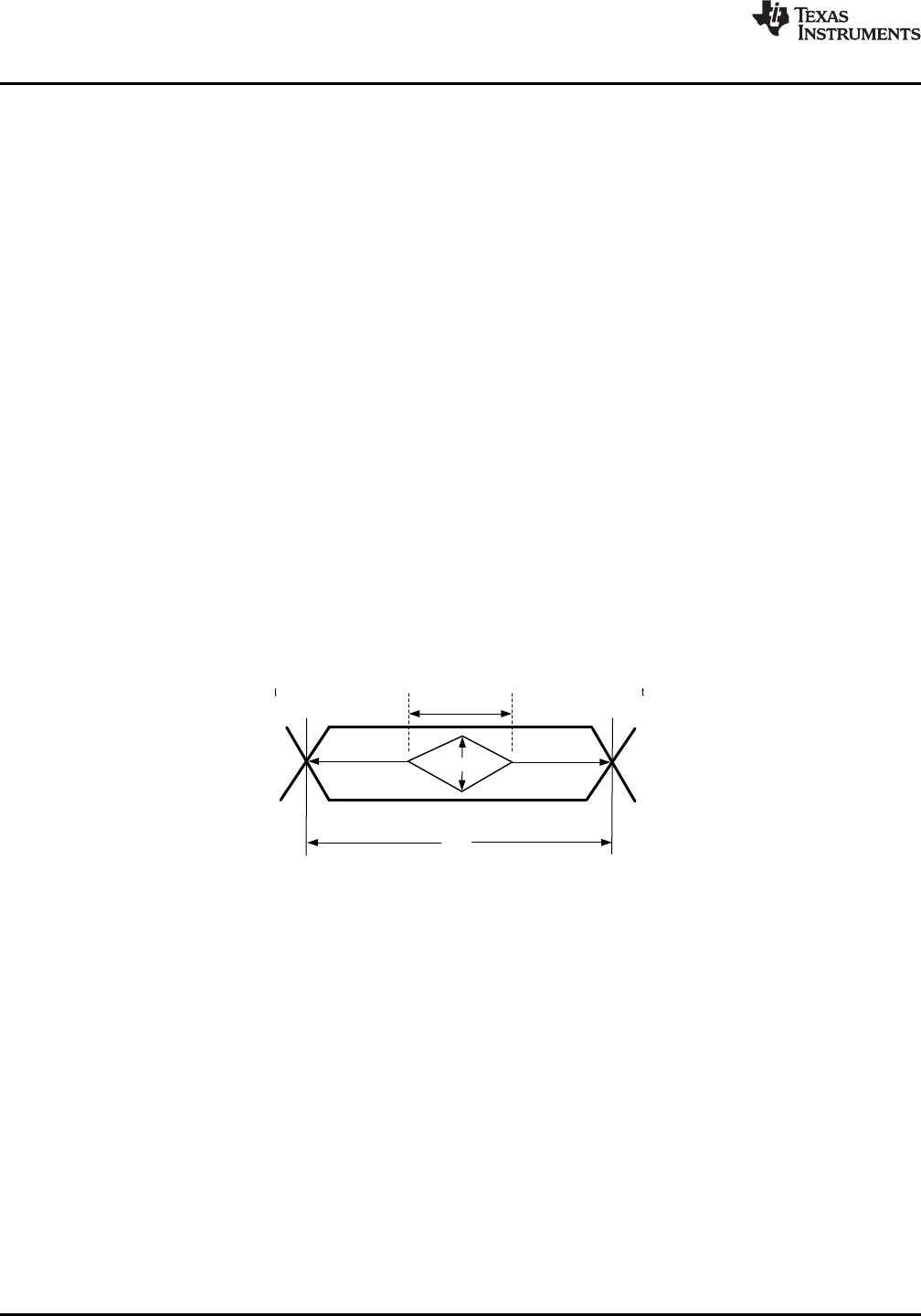
tBIT
(1UI)
Minimum Eye
Width Ideal Data Bit
End
Ideal Data Bit
Beginning
RxIN_TOL -L RxIN_TOL -R
VTH - VTL
DS90UR124-Q1
,
DS90UR241-Q1
SNLS231O –SEPTEMBER 2006–REVISED APRIL 2015
www.ti.com
9.2.1.2.1 Power Considerations
An all LVCMOS design of the Serializer and Deserializer makes them inherently low-power devices. Additionally,
the constant current source nature of the LVDS outputs minimizes the slope of the speed vs. IDD curve of
LVCMOS designs.
9.2.1.2.2 Noise Margin
The Deserializer noise margin is the amount of input jitter (phase noise) that the Deserializer can tolerate and still
reliably recover data. Various environmental and systematic factors include:
• Serializer: VDD noise, TCLK jitter (noise bandwidth and out-of-band noise)
• Media: ISI, VCM noise
• Deserializer: VDD noise
For a graphical representation of noise margin, see Figure 19.
9.2.1.2.3 Transmission Media
The Serializer and Deserializer are to be used in point-to-point configuration, through a PCB trace, or through
twisted pair cable. In a point-to-point configuration, the transmission media needs be terminated at both ends of
the transmitter and receiver pair. Interconnect for LVDS typically has a differential impedance of 100 Ω. Use
cables and connectors that have matched differential impedance to minimize impedance discontinuities. In most
applications that involve cables, the transmission distance will be determined on data rates involved, acceptable
bit error rate and transmission medium.
The resulting signal quality at the receiving end of the transmission media may be assessed by monitoring the
differential eye opening of the serial data stream. The Receiver Input Tolerance and Differential Threshold
Voltage specifications define the acceptable data eye opening. A differential probe should be used to measure
across the termination resistor at the DS90UR124 inputs. Figure 23 illustrates the eye opening and relationship
to the Receiver Input Tolerance and Differential Threshold Voltage specifications.
Figure 23. Receiver Input Eye Opening
9.2.1.2.4 Live Link Insertion
The Serializer and Deserializer devices support live pluggable applications. The automatic receiver lock to
random data “plug and go” hot insertion capability allows the DS90UR124 to attain lock to the active data stream
during a live insertion event.
26 Submit Documentation Feedback Copyright © 2006–2015, Texas Instruments Incorporated
Product Folder Links: DS90UR124-Q1 DS90UR241-Q1
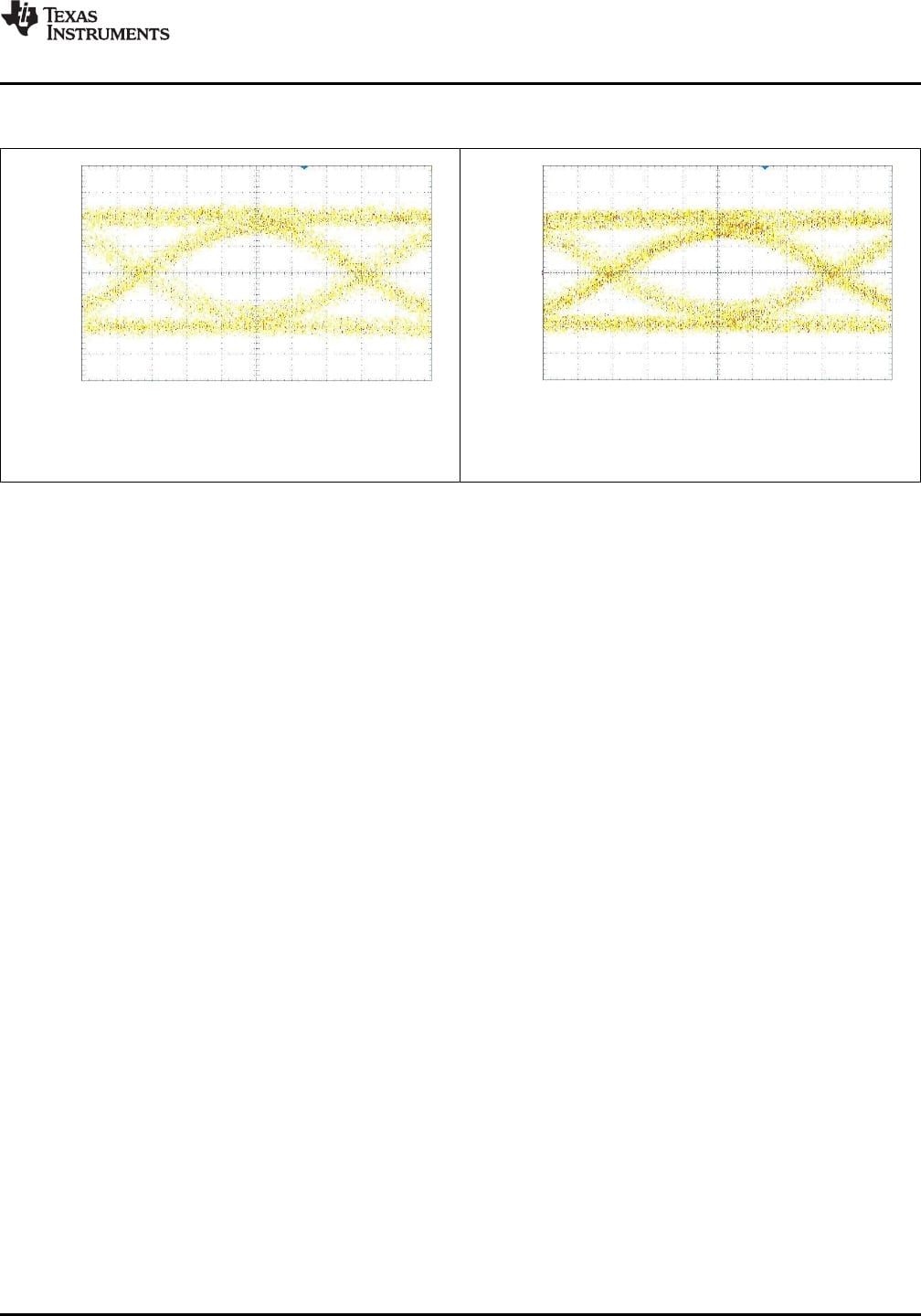
Magnitude (100 mV/DIV)
Time (125 ps/DIV)
Magnitude (200 mV/DIV)
Time (125 ps/DIV)
DS90UR124-Q1
,
DS90UR241-Q1
www.ti.com
SNLS231O –SEPTEMBER 2006–REVISED APRIL 2015
9.2.1.3 Application Curves
Figure 24. DS90UR241 DOUT± at 1.2 Gbps Measured at Figure 25. DS90UR241 DOUT± at 1.2 Gbps Measured at
RIN± Termination; VODSEL=LOW RIN± Termination; VODSEL=HIGH
Copyright © 2006–2015, Texas Instruments Incorporated Submit Documentation Feedback 27
Product Folder Links: DS90UR124-Q1 DS90UR241-Q1
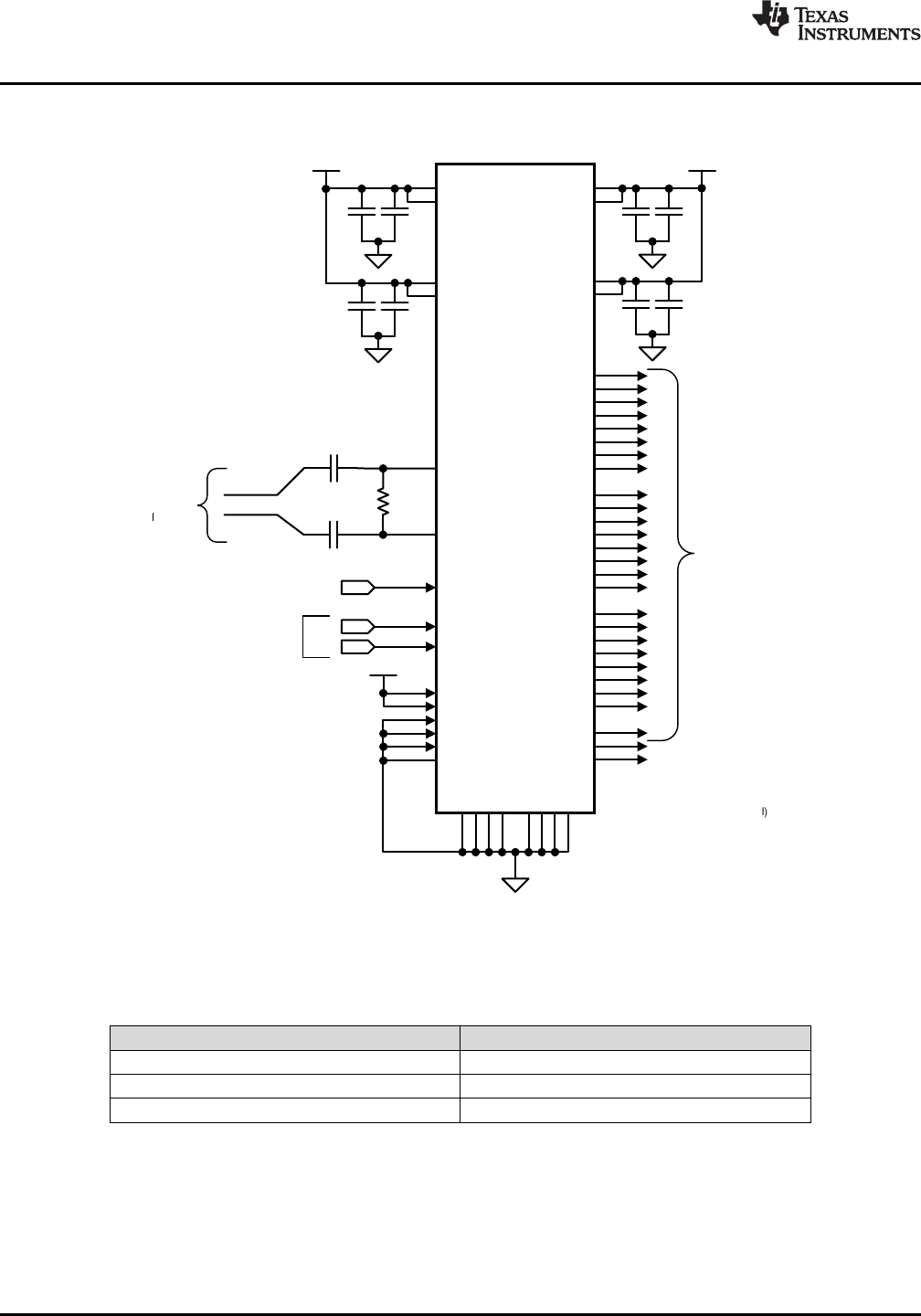
ROUT0
ROUT1
ROUT2
ROUT3
ROUT4
ROUT5
ROUT6
ROUT7
ROUT8
ROUT9
ROUT10
ROUT11
ROUT12
ROUT13
ROUT14
ROUT15
ROUT16
ROUT17
ROUT18
ROUT19
ROUT20
ROUT21
ROUT22
ROUT23
RCLK
RPWDNB
REN
RRFB
RAOFF
PTOSEL
SLEW
RES0(11)
RIN+
RIN-
VDD
VDD VDD
VDD
VDD
VDD
LVCMOS
Parallel
Interface
Notes:
RPWDNB = System GPO
REN = High (ON)
RRFB = High (Rising edge)
RAOFF = Low (Default)
PTOSEL = Low (Defaut)
SLEW = Low (Default)
RES0 = Low
BISTEN = GPO or Low
BISTM = GPO or Low
GPO if used, or tie High (ON)
3.3V
3.3V
DS90UR124 (DES)
C7 C3
C8 C4
C9
C10
R1
C1 C5
VDD
VDD
VSS
VSS
VSS
VSS
VSS
VSS
VSS
VSS
BISTEN
BISTM
LOCK
PASS
GPOs if used,
or tie Low (OFF)
C6C2
3.3V
C1 to C4 = 0.1 PF
C5 to C8 = 0.01 PF (optional)
C9 to C10 = 100 nF;
50WVDC, NPO or X7R
R1 = 100:
Serial
LVDS
Interface
DS90UR124-Q1
,
DS90UR241-Q1
SNLS231O –SEPTEMBER 2006–REVISED APRIL 2015
www.ti.com
9.2.2 DS90UR124 Typical Application Connection
Figure 26. DS90UR124 Connection Diagram
9.2.2.1 Design Requirements
Table 4. DS90UR124 Design Parameters
DESIGN PARAMETER EXAMPLE VALUE
VDD 3.3 V
DS90UR124-Q1 AC-Coupling Capacitor for RIN± 100 nF
DS90UR124-Q1 Termination for RIN± 100 Ω
28 Submit Documentation Feedback Copyright © 2006–2015, Texas Instruments Incorporated
Product Folder Links: DS90UR124-Q1 DS90UR241-Q1

43 MHz RX
Pixel Clock
Output
(1 V/DIV)
1.2 Gbps TX
Serial Data
Output
(200 mV/DIV)
Time (10 ns/DIV)
Magnitude (500 mV/DIV)
Time (5 ns/DIV)
DS90UR124-Q1
,
DS90UR241-Q1
www.ti.com
SNLS231O –SEPTEMBER 2006–REVISED APRIL 2015
9.2.2.2 Detailed Design Procedure
Figure 26 shows a typical application of the DS90UR124 deserializer for an 33-MHz 18-bit Color Display
Application. The RIN± inputs must have an external series 0.1-μF AC-coupling capacitor and 100-Ωparallel
termination on the high-speed serial lines. The deserializer does not have an internal termination. Bypass
capacitors are placed near the power supply pins. At a minimum, four 0.1-μF capacitors should be used for local
device bypassing. Ferrite beads may be needed on the VDDs for effective noise suppression. Additional
capacitors may be needed as the number and values of the capacitors will depend on meeting the power noise
specification of the part. The interface to the display is with 3.3-V LVCMOS levels. An RC delay is placed on the
PDB signal to delay the enabling of the device until power is stable.
9.2.2.3 Application Curves
Figure 27. DS90UR241 Serial Stream and DS90UR124 Figure 28. DS90UR124 PCLK Output at 43 MHz (Enlarged)
43-MHz PCLK Output
10 Power Supply Recommendations
This device is designed to operate from an input core voltage supply of 3.3 V. Some devices provide separate
power and ground pins for different portions of the circuit. This is done to isolate switching noise effects between
different sections of the circuit. Separate planes on the PCB are typically. Pin description tables typically provide
guidance on which circuit blocks are connected to which power pin pairs. In some cases, an external filter may
be used to provide clean power to sensitive circuits such as PLLs.
Copyright © 2006–2015, Texas Instruments Incorporated Submit Documentation Feedback 29
Product Folder Links: DS90UR124-Q1 DS90UR241-Q1
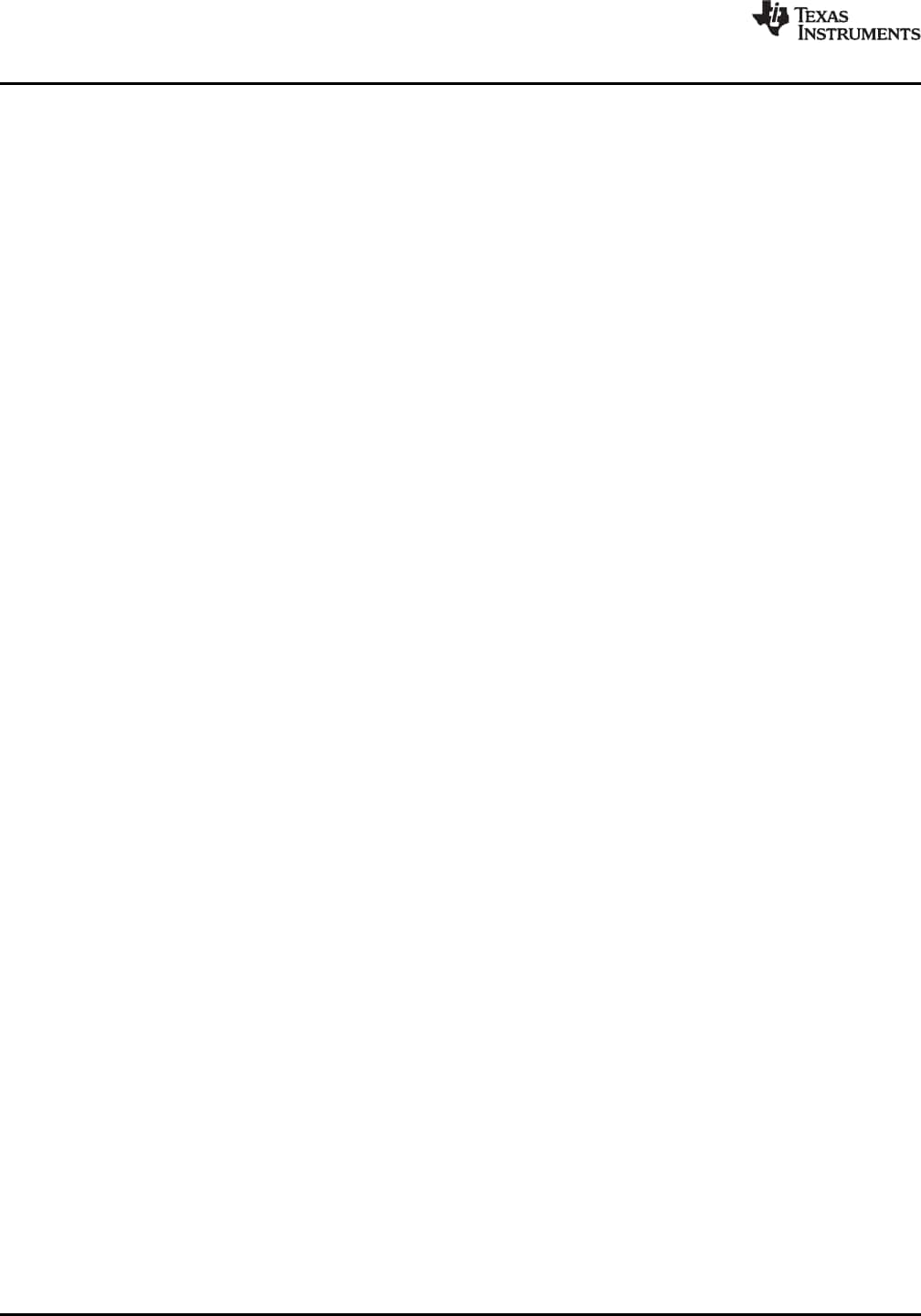
DS90UR124-Q1
,
DS90UR241-Q1
SNLS231O –SEPTEMBER 2006–REVISED APRIL 2015
www.ti.com
11 Layout
11.1 Layout Guidelines
11.1.1 PCB Layout and Power System Considerations
Circuit board layout and stack-up for the LVDS SERDES devices should be designed to provide low-noise power
feed to the device. Good layout practice will also separate high-frequency or high-level inputs and outputs to
minimize unwanted stray noise pickup, feedback and interference. Power system performance may be greatly
improved by using thin dielectrics (2 to 4 mils) for power / ground sandwiches. This arrangement provides plane
capacitance for the PCB power system with low-inductance parasitics, which has proven especially effective at
high frequencies, and makes the value and placement of external bypass capacitors less critical. External bypass
capacitors should include both RF ceramic and tantalum electrolytic types. RF capacitors may use values in the
range of 0.01 μF to 0.1 μF. Tantalum capacitors may be in the range of 2.2 μF to 10 μF. Voltage rating of the
tantalum capacitors should be at least 5× the power supply voltage being used.
Surface-mount capacitors are recommended due to their smaller parasitics. When using multiple capacitors per
supply pin, locate the smaller value closer to the pin. A large bulk capacitor is recommend at the point of power
entry. This is typically in the 50-uF to 100-uF range and will smooth low frequency switching noise. TI
recommends connecting power and ground pins directly to the power and ground planes with bypass capacitors
connected to the plane with via on both ends of the capacitor. Connecting power or ground pins to an external
bypass capacitor will increase the inductance of the path.
A small body size X7R chip capacitor, such as 0603, is recommended for external bypass. Its small body size
reduces the parasitic inductance of the capacitor. The user must pay attention to the resonance frequency of
these external bypass capacitors, usually in the range of 20 MHz to 30 MHz. To provide effective bypassing,
multiple capacitors are often used to achieve low impedance between the supply rails over the frequency of
interest. At high frequency, it is also a common practice to use two vias from power and ground pins to the
planes, reducing the impedance at high frequency.
Some devices provide separate power and ground pins for different portions of the circuit. This is done to isolate
switching noise effects between different sections of the circuit. Separate planes on the PCB are typically not
required. Pin description tables typically provide guidance on which circuit blocks are connected to which power
pin pairs. In some cases, an external filter many be used to provide clean power to sensitive circuits such as
PLLs.
Use at least a 4-layer board with a power and ground plane. Locate LVCMOS signals away from the LVDS lines
to prevent coupling from the LVCMOS lines to the LVDS lines. Closely coupled differential lines of 100 Ωare
typically recommended for LVDS interconnect. The closely coupled lines help to ensure that coupled noise will
appear as common-mode and thus is rejected by the receivers. The tightly coupled lines will also radiate less.
Termination of the LVDS interconnect is required. For point-to-point applications, termination should be located at
both ends of the devices. Nominal value is 100 Ωto match the differential impedance of the line. Place the
resistor as close to the transmitter DOUT± outputs and receiver RIN± inputs as possible to minimize the resulting
stub between the termination resistor and device.
11.1.2 LVDS Interconnect Guidelines
See AN-1108 (SNLA008) and AN-905 (SNLA035) for full details.
• Use 100-Ωcoupled differential pairs
• Use the S/2S/3S rule in spacings
– S = space between the pair
– 2S = space between pairs
– 3S = space to LVCMOS signal
• Minimize the number of vias
• Use differential connectors when operating above 500-Mbps line speed
• Maintain balance of the traces
• Minimize skew within the pair
• Terminate as close to the TX outputs and RX inputs as possible
30 Submit Documentation Feedback Copyright © 2006–2015, Texas Instruments Incorporated
Product Folder Links: DS90UR124-Q1 DS90UR241-Q1
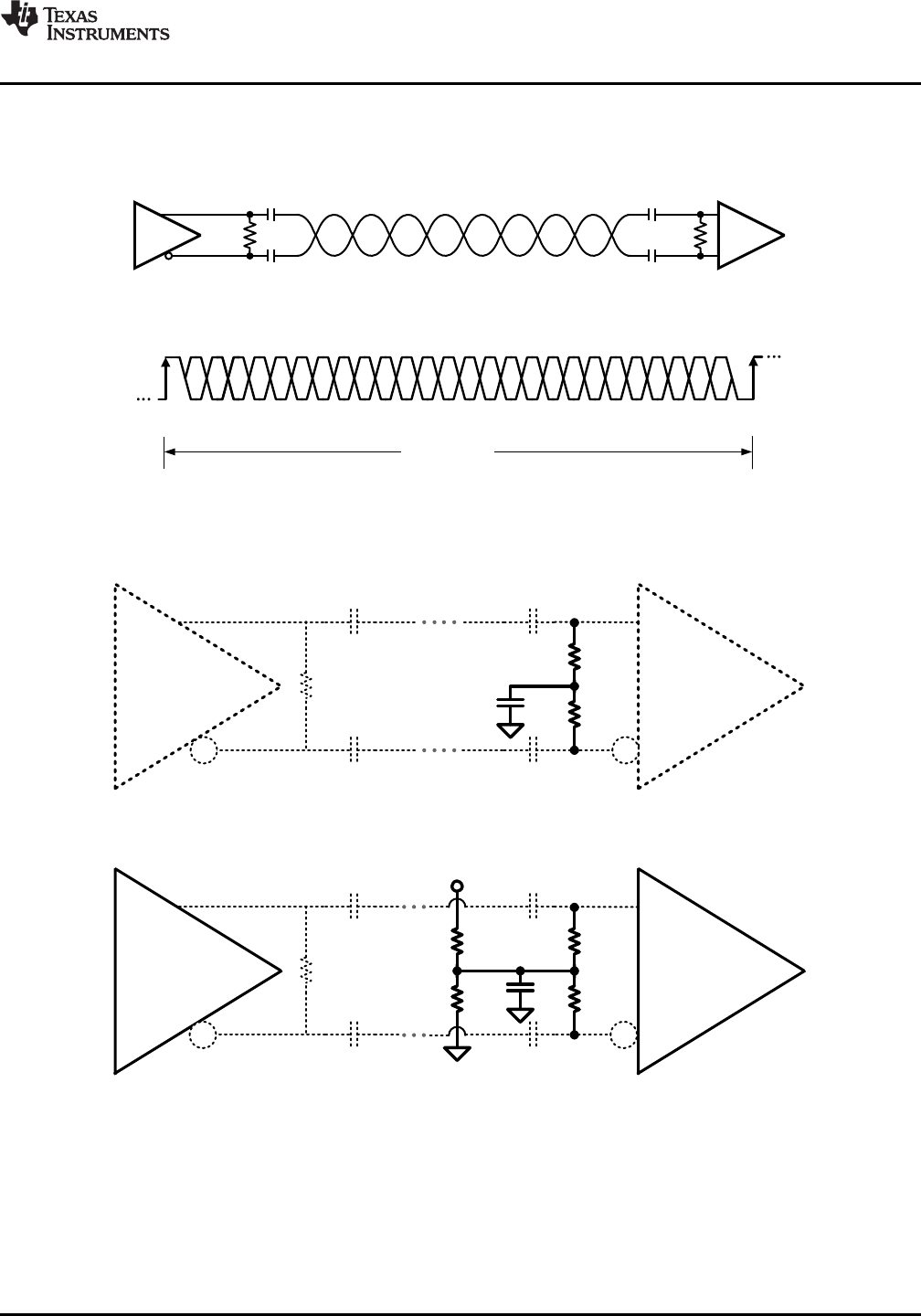
0.1 PF
0.1 PF
50:
50:
4.7 nF
DS90UR124
100:
0.1 PF
0.1 PF
DS90UR241
RPU
VDD
RPD
RIN+
RIN-
RIN+
RIN-
0.1 PF
0.1 PF
50:
50:
4.7 nF DS90UR124
100:
0.1 PF
0.1 PF
DS90UR241
CLK1
bit0
bit1
bit2
bit3
bit4
bit5
bit6
bit7
bit8
bit9
bit10
bit11
DCA
DCB
bit12
bit13
bit14
bit15
bit16
bit17
bit18
bit19
bit20
bit21
bit22
bit23
CLK0
1 CLK cycle
100:
100 nF
100 nF
100:
100 nF
100 nF
DOUT-
DOUT+
RIN-
RIN+
DS90UR124-Q1
,
DS90UR241-Q1
www.ti.com
SNLS231O –SEPTEMBER 2006–REVISED APRIL 2015
Layout Guidelines (continued)
Additional general guidance can be found in the LVDS Owner’s Manual (SNLA187) - available in PDF format
from the TI web site at: www.ti.com/lvds
Figure 29. AC-Coupled Application
*Note: bits [0-23] are not physically located in positions shown above since bits [0-23] are scrambled and DC
Balanced
Figure 30. Single Serialized LVDS Bitstream*
Figure 31. Receiver Termination Option 2
Figure 32. Receiver Termination Option 3
Copyright © 2006–2015, Texas Instruments Incorporated Submit Documentation Feedback 31
Product Folder Links: DS90UR124-Q1 DS90UR241-Q1
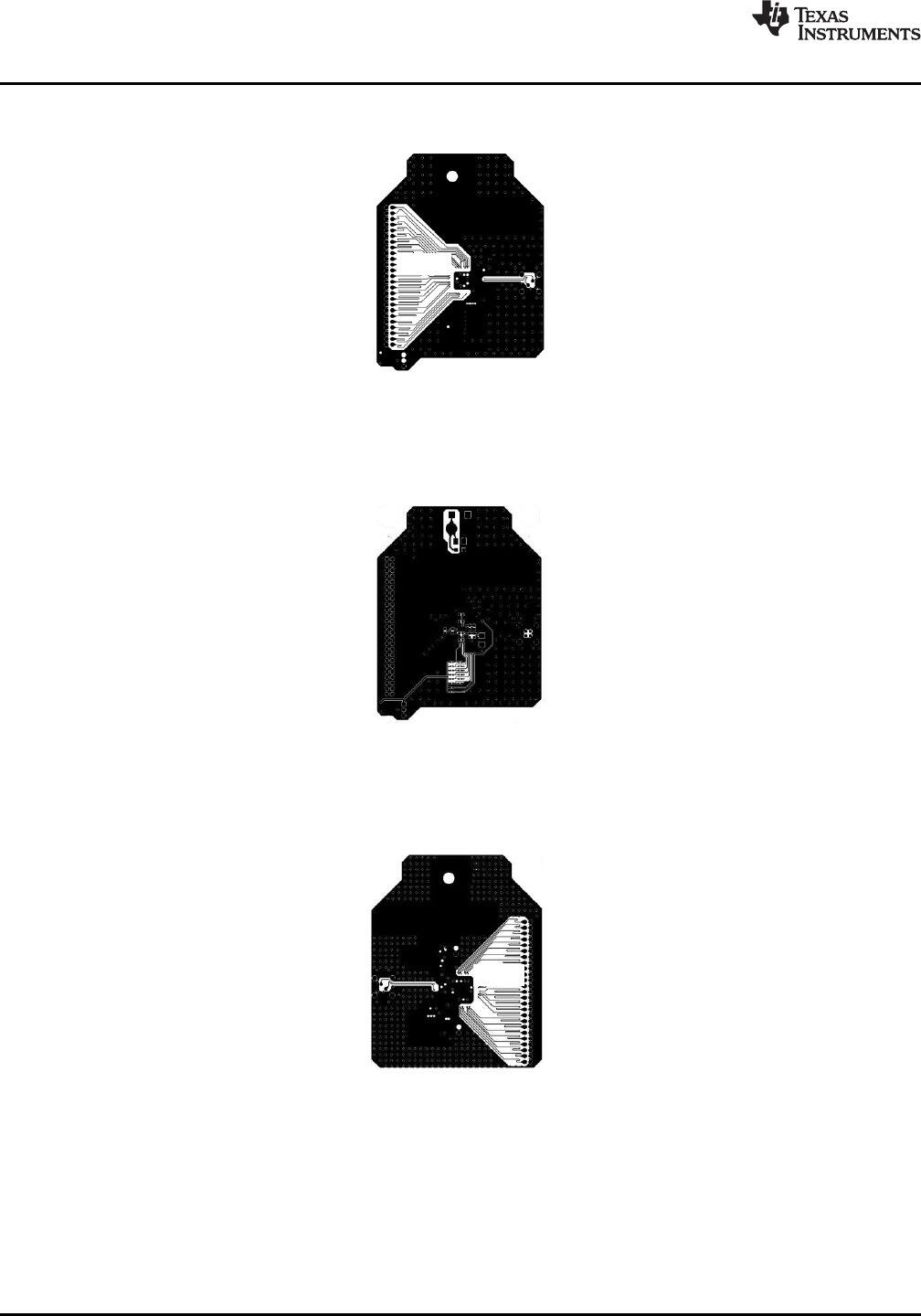
LVCMOS
OUTPUTS
HIGH
SPEED
SERIAL
INPUTS
AC DECOUPLING
CAPS PLACEMENT
LVCMOS
INPUTS
HIGH
SPEED
SERIAL
STREAM
DS90UR124-Q1
,
DS90UR241-Q1
SNLS231O –SEPTEMBER 2006–REVISED APRIL 2015
www.ti.com
11.2 Layout Examples
Figure 33. Example DS90UR241-Q1 EMC Layout
Figure 34. DS90UR241-Q1 EMC EVM Layer 4
Figure 35. Example DS90UR124-Q1 EMC Layout
32 Submit Documentation Feedback Copyright © 2006–2015, Texas Instruments Incorporated
Product Folder Links: DS90UR124-Q1 DS90UR241-Q1
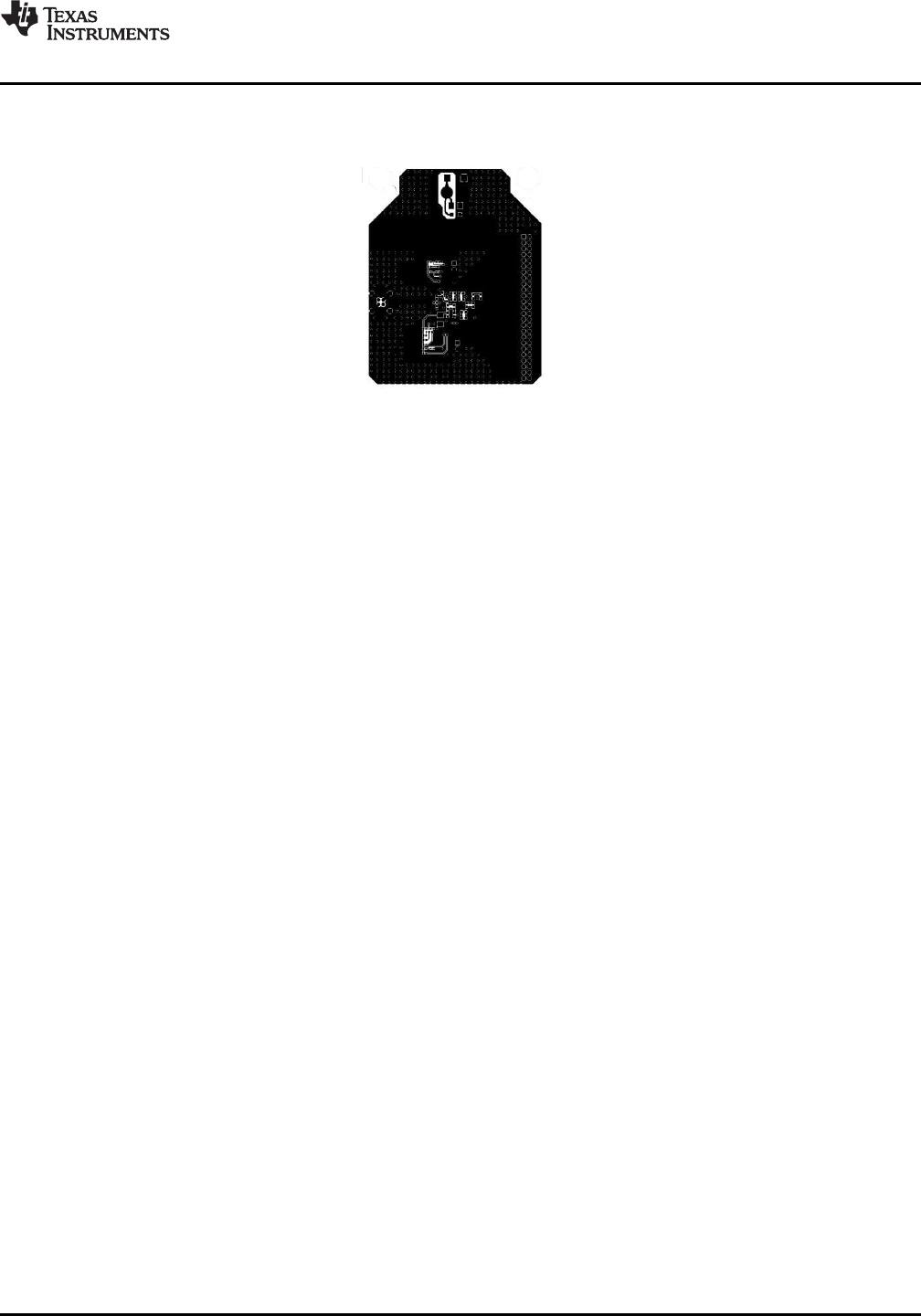
AC
DECOUPLING
CAPS
PLACEMENT
DS90UR124-Q1
,
DS90UR241-Q1
www.ti.com
SNLS231O –SEPTEMBER 2006–REVISED APRIL 2015
Layout Examples (continued)
Figure 36. DS90UR124-Q1 EMC EVM Layer 4
Copyright © 2006–2015, Texas Instruments Incorporated Submit Documentation Feedback 33
Product Folder Links: DS90UR124-Q1 DS90UR241-Q1

DS90UR124-Q1
,
DS90UR241-Q1
SNLS231O –SEPTEMBER 2006–REVISED APRIL 2015
www.ti.com
12 Device and Documentation Support
12.1 Device Support
12.1.1 Third-Party Products Disclaimer
TI'S PUBLICATION OF INFORMATION REGARDING THIRD-PARTY PRODUCTS OR SERVICES DOES NOT
CONSTITUTE AN ENDORSEMENT REGARDING THE SUITABILITY OF SUCH PRODUCTS OR SERVICES
OR A WARRANTY, REPRESENTATION OR ENDORSEMENT OF SUCH PRODUCTS OR SERVICES, EITHER
ALONE OR IN COMBINATION WITH ANY TI PRODUCT OR SERVICE.
12.2 Documentation Support
12.2.1 Related Documentation
For related documentation see the following:
•LVDS Interconnect Guidelines AN-1108,SNLA008
•LVDS Interconnect Guidelines AN-905,SNLA035
12.3 Related Links
The table below lists quick access links. Categories include technical documents, support and community
resources, tools and software, and quick access to sample or buy.
Table 5. Related Links
TECHNICAL TOOLS & SUPPORT &
PARTS PRODUCT FOLDER SAMPLE & BUY DOCUMENTS SOFTWARE COMMUNITY
DS90UR124-Q1 Click here Click here Click here Click here Click here
DS90UR241-Q1 Click here Click here Click here Click here Click here
12.4 Trademarks
All trademarks are the property of their respective owners.
12.5 Electrostatic Discharge Caution
These devices have limited built-in ESD protection. The leads should be shorted together or the device placed in conductive foam
during storage or handling to prevent electrostatic damage to the MOS gates.
12.6 Glossary
SLYZ022 —TI Glossary.
This glossary lists and explains terms, acronyms, and definitions.
13 Mechanical, Packaging, and Orderable Information
The following pages include mechanical, packaging, and orderable information. This information is the most
current data available for the designated devices. This data is subject to change without notice and revision of
this document. For browser-based versions of this data sheet, refer to the left-hand navigation.
34 Submit Documentation Feedback Copyright © 2006–2015, Texas Instruments Incorporated
Product Folder Links: DS90UR124-Q1 DS90UR241-Q1
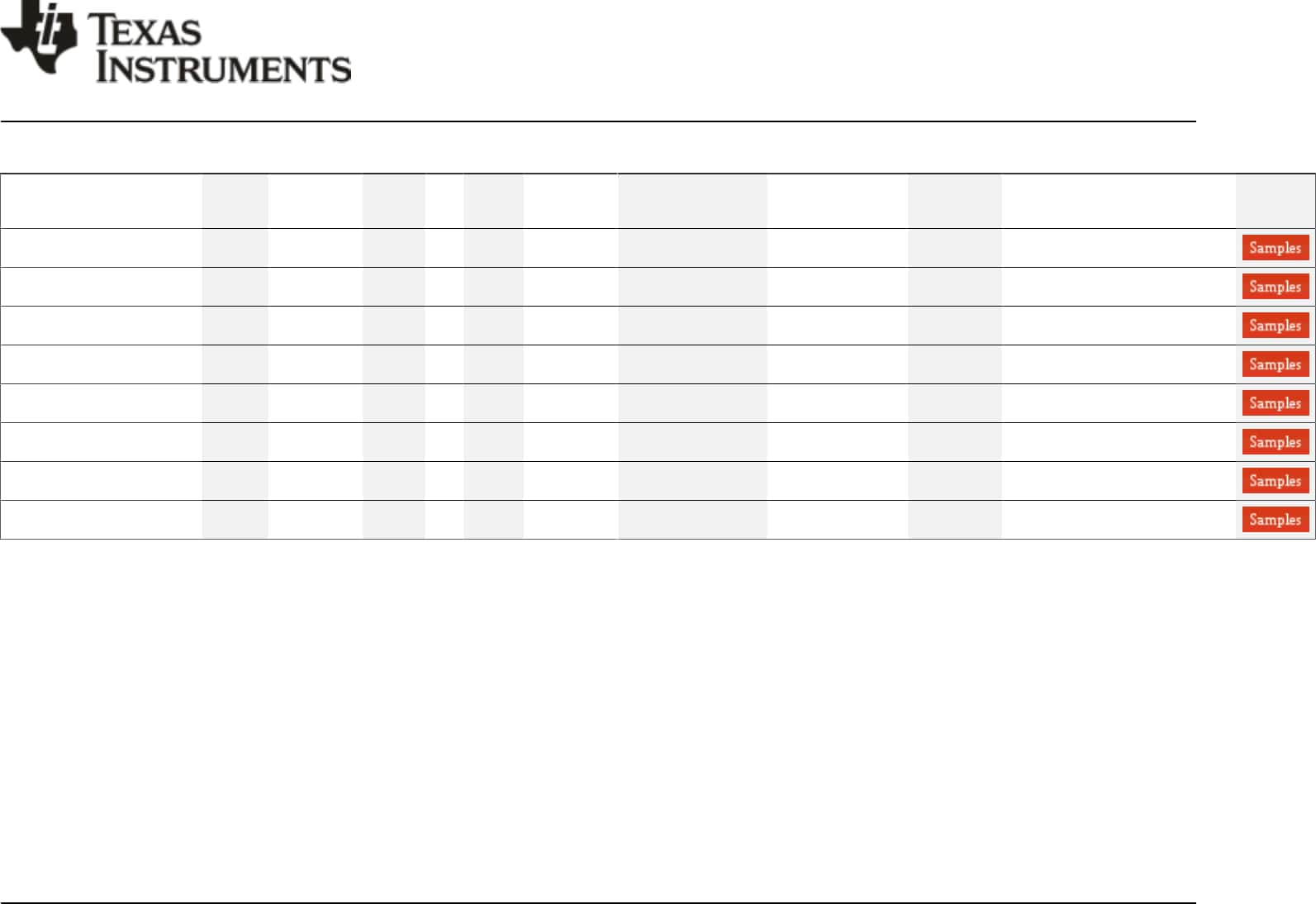
PACKAGE OPTION ADDENDUM
www.ti.com 10-Dec-2020
Addendum-Page 1
PACKAGING INFORMATION
Orderable Device Status
(1)
Package Type Package
Drawing Pins Package
Qty Eco Plan
(2)
Lead finish/
Ball material
(6)
MSL Peak Temp
(3)
Op Temp (°C) Device Marking
(4/5)
Samples
DS90UR124IVS/NOPB ACTIVE TQFP PAG 64 160 RoHS & Green SN Level-3-260C-168 HR -40 to 105 DS90UR124
IVS
DS90UR124IVSX/NOPB ACTIVE TQFP PAG 64 1000 RoHS & Green SN Level-3-260C-168 HR -40 to 105 DS90UR124
IVS
DS90UR124QVS/NOPB ACTIVE TQFP PAG 64 160 RoHS & Green SN Level-3-260C-168 HR -40 to 105 DS90UR124
QVS
DS90UR124QVSX/NOPB ACTIVE TQFP PAG 64 1000 RoHS & Green SN Level-3-260C-168 HR -40 to 105 DS90UR124
QVS
DS90UR241IVS/NOPB ACTIVE TQFP PFB 48 250 RoHS & Green SN Level-3-260C-168 HR -40 to 105 DS90UR24
1IVS
DS90UR241IVSX/NOPB ACTIVE TQFP PFB 48 1000 RoHS & Green SN Level-3-260C-168 HR -40 to 105 DS90UR24
1IVS
DS90UR241QVS/NOPB ACTIVE TQFP PFB 48 250 RoHS & Green SN Level-3-260C-168 HR -40 to 105 DS90UR24
1QVS
DS90UR241QVSX/NOPB ACTIVE TQFP PFB 48 1000 RoHS & Green SN Level-3-260C-168 HR -40 to 105 DS90UR24
1QVS
(1) The marketing status values are defined as follows:
ACTIVE: Product device recommended for new designs.
LIFEBUY: TI has announced that the device will be discontinued, and a lifetime-buy period is in effect.
NRND: Not recommended for new designs. Device is in production to support existing customers, but TI does not recommend using this part in a new design.
PREVIEW: Device has been announced but is not in production. Samples may or may not be available.
OBSOLETE: TI has discontinued the production of the device.
(2) RoHS: TI defines "RoHS" to mean semiconductor products that are compliant with the current EU RoHS requirements for all 10 RoHS substances, including the requirement that RoHS substance
do not exceed 0.1% by weight in homogeneous materials. Where designed to be soldered at high temperatures, "RoHS" products are suitable for use in specified lead-free processes. TI may
reference these types of products as "Pb-Free".
RoHS Exempt: TI defines "RoHS Exempt" to mean products that contain lead but are compliant with EU RoHS pursuant to a specific EU RoHS exemption.
Green: TI defines "Green" to mean the content of Chlorine (Cl) and Bromine (Br) based flame retardants meet JS709B low halogen requirements of <=1000ppm threshold. Antimony trioxide based
flame retardants must also meet the <=1000ppm threshold requirement.
(3) MSL, Peak Temp. - The Moisture Sensitivity Level rating according to the JEDEC industry standard classifications, and peak solder temperature.
(4) There may be additional marking, which relates to the logo, the lot trace code information, or the environmental category on the device.
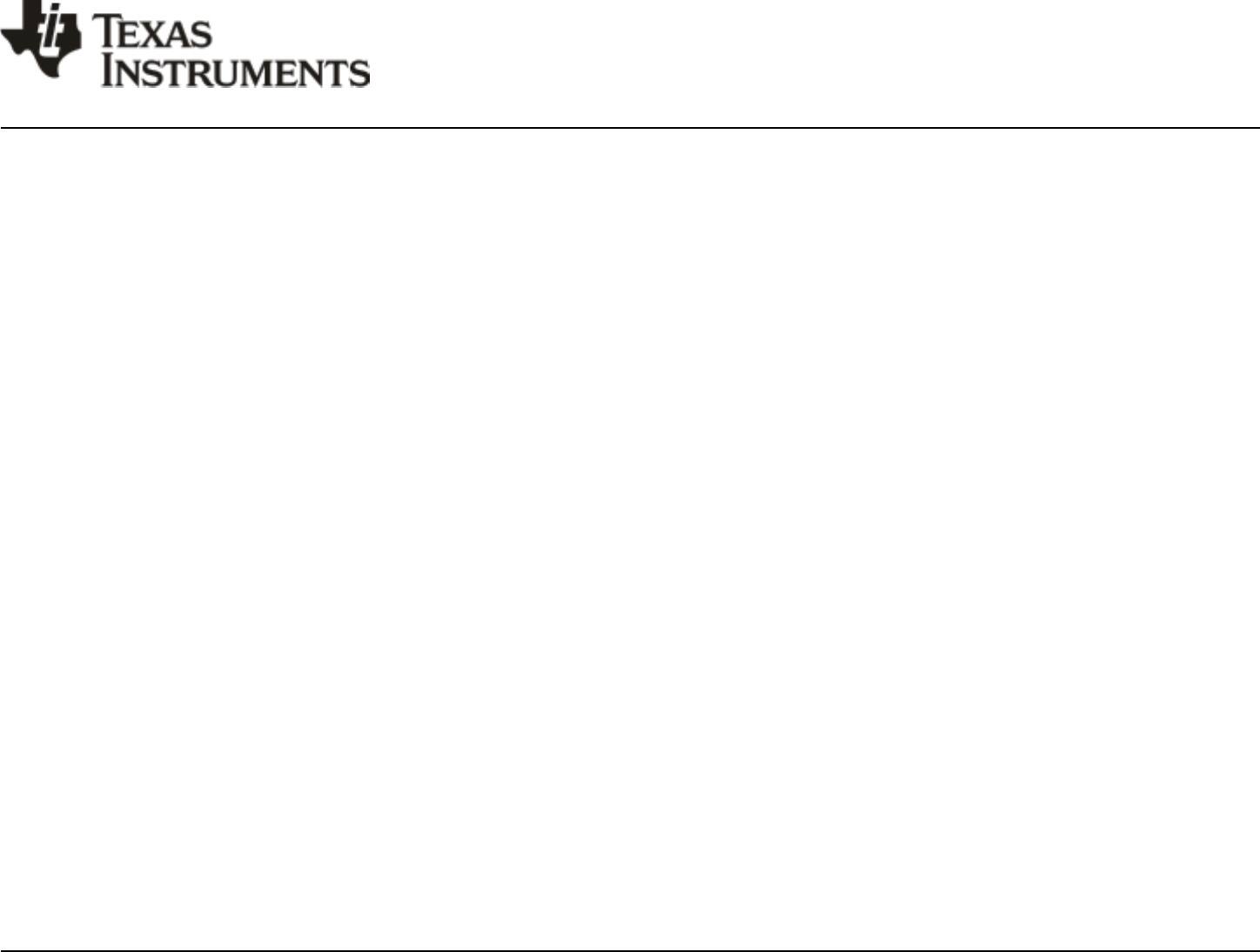
PACKAGE OPTION ADDENDUM
www.ti.com 10-Dec-2020
Addendum-Page 2
(5) Multiple Device Markings will be inside parentheses. Only one Device Marking contained in parentheses and separated by a "~" will appear on a device. If a line is indented then it is a continuation
of the previous line and the two combined represent the entire Device Marking for that device.
(6) Lead finish/Ball material - Orderable Devices may have multiple material finish options. Finish options are separated by a vertical ruled line. Lead finish/Ball material values may wrap to two
lines if the finish value exceeds the maximum column width.
Important Information and Disclaimer:The information provided on this page represents TI's knowledge and belief as of the date that it is provided. TI bases its knowledge and belief on information
provided by third parties, and makes no representation or warranty as to the accuracy of such information. Efforts are underway to better integrate information from third parties. TI has taken and
continues to take reasonable steps to provide representative and accurate information but may not have conducted destructive testing or chemical analysis on incoming materials and chemicals.
TI and TI suppliers consider certain information to be proprietary, and thus CAS numbers and other limited information may not be available for release.
In no event shall TI's liability arising out of such information exceed the total purchase price of the TI part(s) at issue in this document sold by TI to Customer on an annual basis.
OTHER QUALIFIED VERSIONS OF DS90UR124, DS90UR124-Q1, DS90UR241, DS90UR241-Q1 :
•Catalog: DS90UR124, DS90UR241
•Automotive: DS90UR124-Q1, DS90UR241-Q1
NOTE: Qualified Version Definitions:
•Catalog - TI's standard catalog product
•Automotive - Q100 devices qualified for high-reliability automotive applications targeting zero defects

TAPE AND REEL INFORMATION
*All dimensions are nominal
Device Package
Type Package
Drawing Pins SPQ Reel
Diameter
(mm)
Reel
Width
W1 (mm)
A0
(mm) B0
(mm) K0
(mm) P1
(mm) W
(mm) Pin1
Quadrant
DS90UR124IVSX/NOPB TQFP PAG 64 1000 330.0 24.4 13.0 13.0 1.45 16.0 24.0 Q2
DS90UR124QVSX/NOPB TQFP PAG 64 1000 330.0 24.4 13.0 13.0 1.45 16.0 24.0 Q2
DS90UR241IVSX/NOPB TQFP PFB 48 1000 330.0 16.4 9.3 9.3 2.2 12.0 16.0 Q2
DS90UR241QVSX/NOPB TQFP PFB 48 1000 330.0 16.4 9.3 9.3 2.2 12.0 16.0 Q2
PACKAGE MATERIALS INFORMATION
www.ti.com 9-Apr-2022
Pack Materials-Page 1
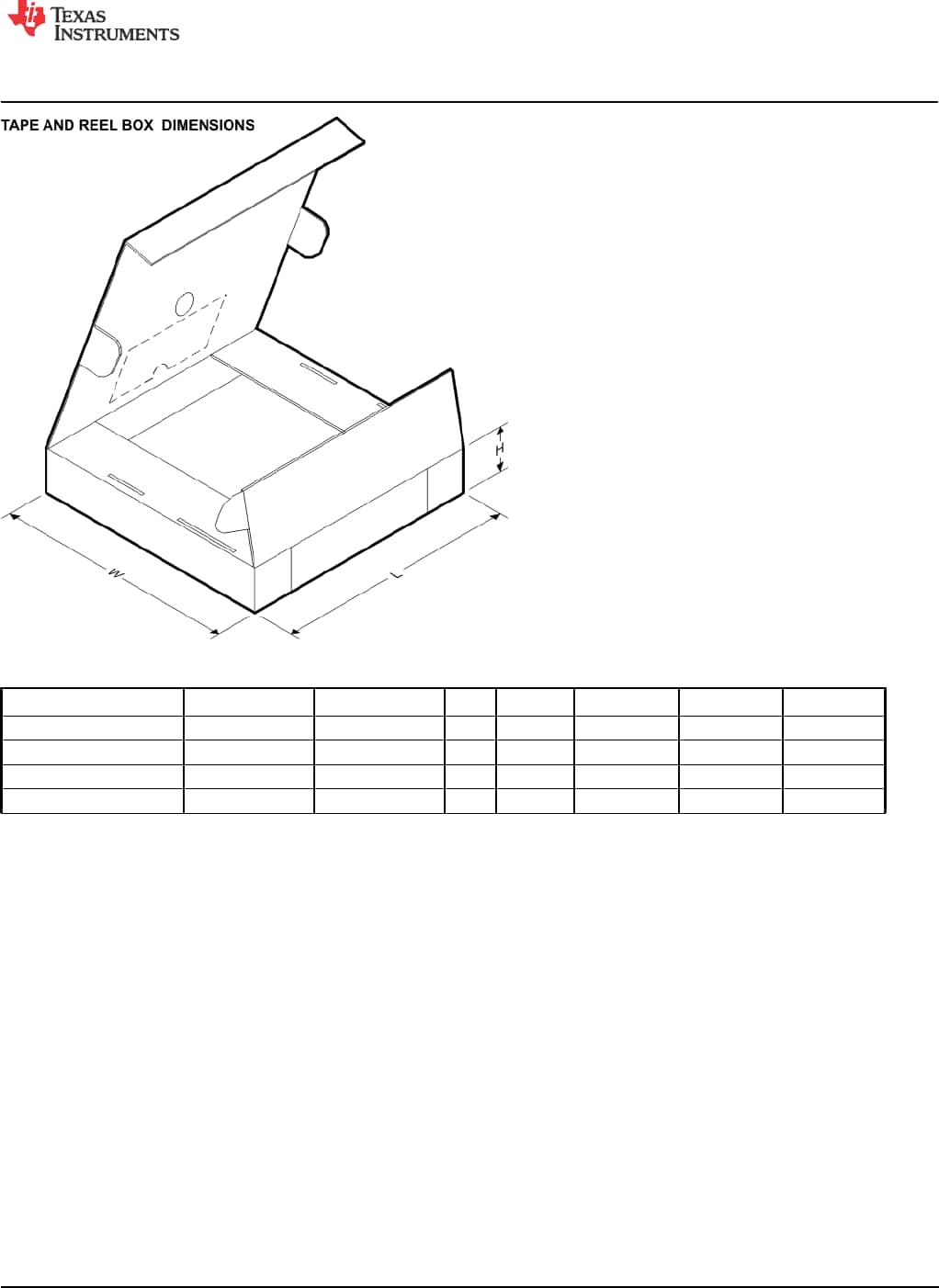
*All dimensions are nominal
Device Package Type Package Drawing Pins SPQ Length (mm) Width (mm) Height (mm)
DS90UR124IVSX/NOPB TQFP PAG 64 1000 367.0 367.0 45.0
DS90UR124QVSX/NOPB TQFP PAG 64 1000 367.0 367.0 45.0
DS90UR241IVSX/NOPB TQFP PFB 48 1000 356.0 356.0 35.0
DS90UR241QVSX/NOPB TQFP PFB 48 1000 356.0 356.0 35.0
PACKAGE MATERIALS INFORMATION
www.ti.com 9-Apr-2022
Pack Materials-Page 2
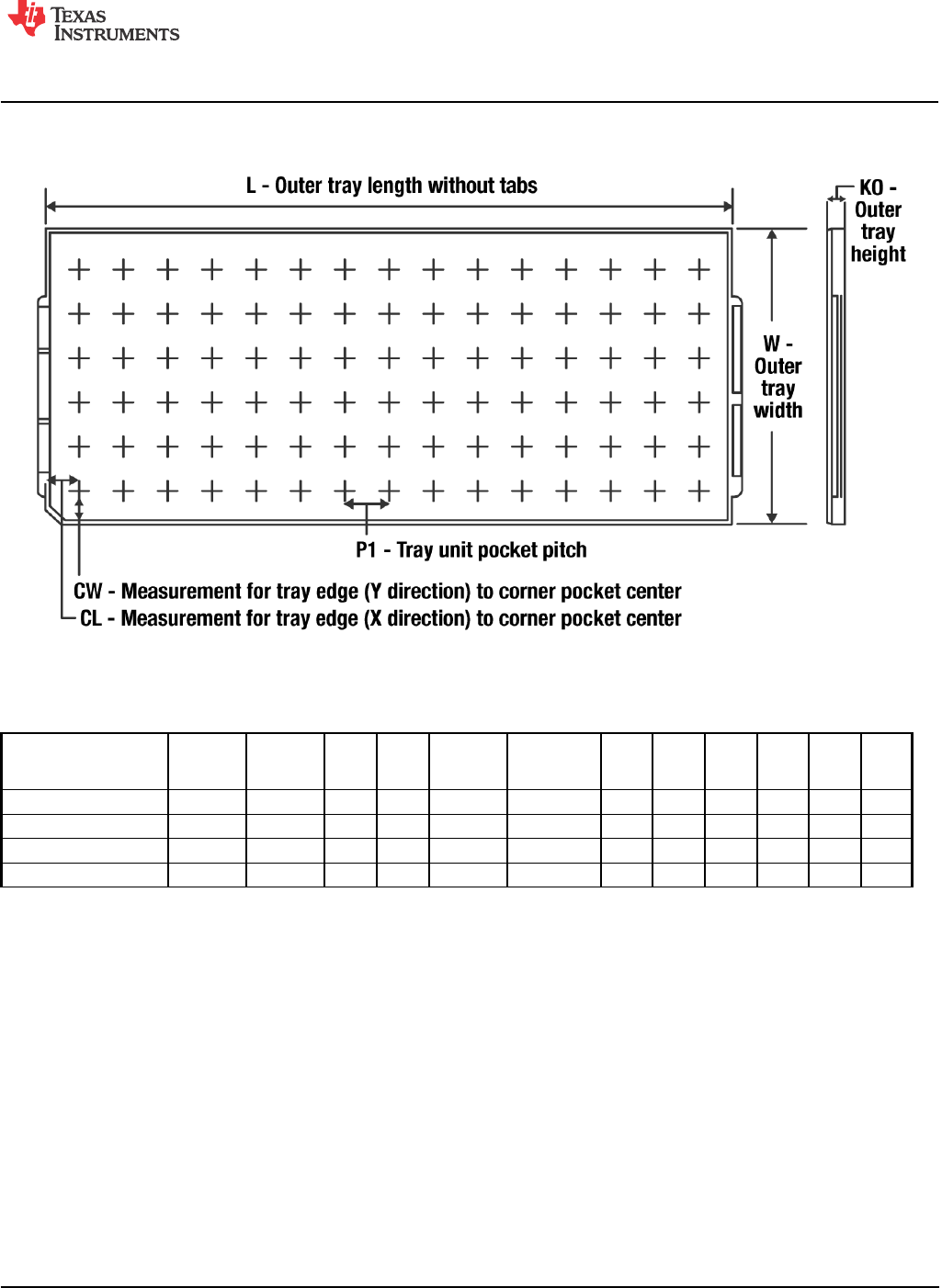
TRAY
Chamfer on Tray corner indicates Pin 1 orientation of packed units.
*All dimensions are nominal
Device Package
Name Package
Type Pins SPQ Unit array
matrix Max
temperature
(°C)
L (mm) W
(mm) K0
(µm) P1
(mm) CL
(mm) CW
(mm)
DS90UR124IVS/NOPB PAG TQFP 64 160 8 X 20 150 322.6 135.9 7620 15.2 13.1 13
DS90UR124QVS/NOPB PAG TQFP 64 160 8 X 20 150 322.6 135.9 7620 15.2 13.1 13
DS90UR241IVS/NOPB PFB TQFP 48 250 10 x 25 150 315 135.9 7620 12.2 11.1 11.25
DS90UR241QVS/NOPB PFB TQFP 48 250 10 x 25 150 315 135.9 7620 12.2 11.1 11.25
PACKAGE MATERIALS INFORMATION
www.ti.com 9-Apr-2022
Pack Materials-Page 3

MECHANICAL DATA
MTQF006A – JANUARY 1995 – REVISED DECEMBER 1996
POST OFFICE BOX 655303 • DALLAS, TEXAS 75265
PAG (S-PQFP-G64) PLASTIC QUAD FLATPACK
0,13 NOM
0,25
0,45
0,75
Seating Plane
0,05 MIN
4040282/C 11/96
Gage Plane
33
0,17
0,27
16
48
1
7,50 TYP
49
64
SQ
9,80
1,05
0,95
11,80
12,20
1,20 MAX
10,20 SQ
17
32
0,08
0,50 M
0,08
0°–7°
NOTES: A. All linear dimensions are in millimeters.
B. This drawing is subject to change without notice.
C. Falls within JEDEC MS-026

MECHANICAL DATA
MTQF019A – JANUARY 1995 – REVISED JANUARY 1998
POST OFFICE BOX 655303 • DALLAS, TEXAS 75265
PFB (S-PQFP-G48) PLASTIC QUAD FLATPACK
4073176/B 10/96
Gage Plane
0,13 NOM
0,25
0,45
0,75
Seating Plane
0,05 MIN
0,17
0,27
24
25
13
12
SQ
36
37
7,20
6,80
48
1
5,50 TYP
SQ
8,80
9,20
1,05
0,95
1,20 MAX 0,08
0,50 M
0,08
0°–7°
NOTES: A. All linear dimensions are in millimeters.
B. This drawing is subject to change without notice.
C. Falls within JEDEC MS-026
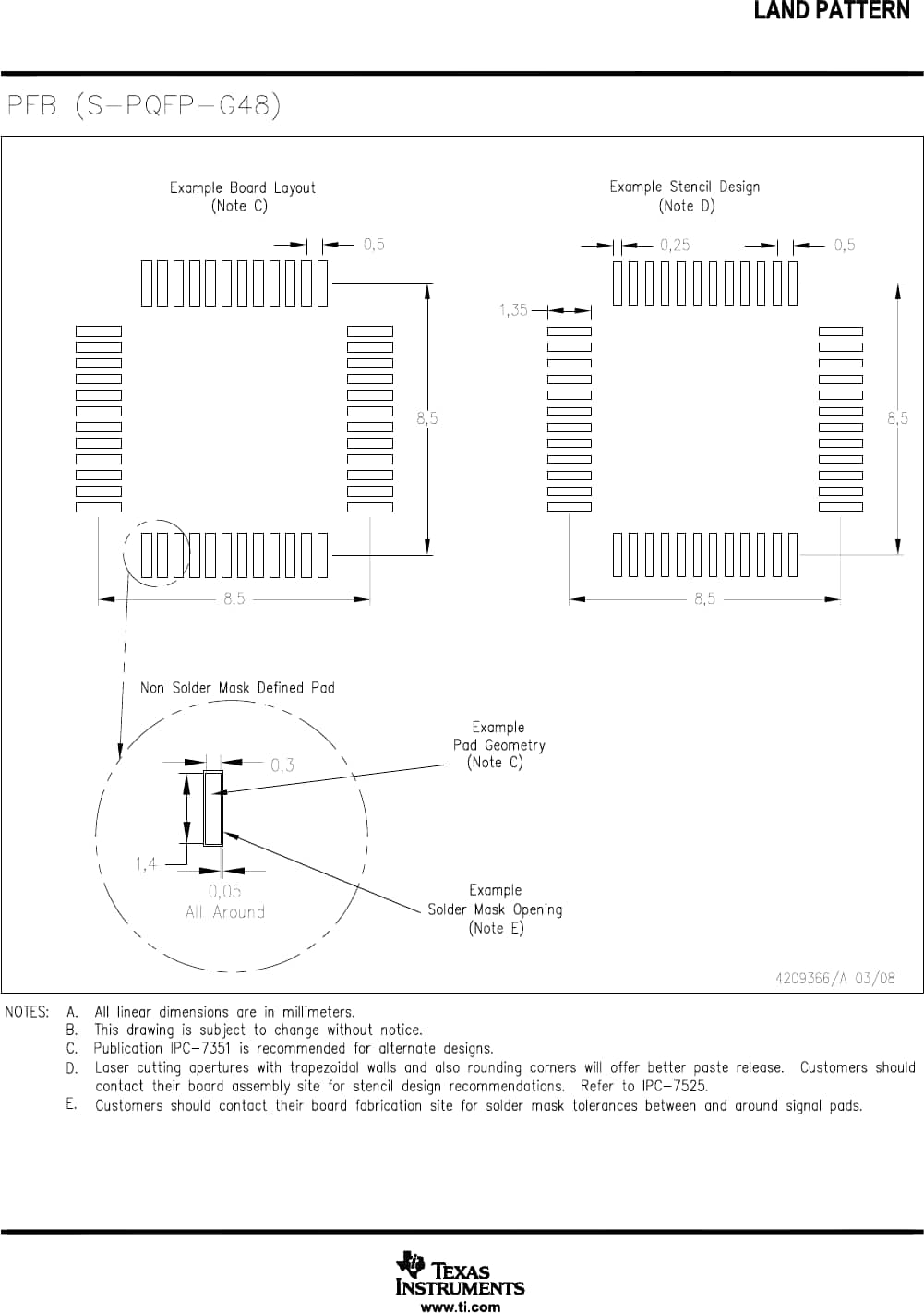
IMPORTANT NOTICE AND DISCLAIMER
TI PROVIDES TECHNICAL AND RELIABILITY DATA (INCLUDING DATA SHEETS), DESIGN RESOURCES (INCLUDING REFERENCE
DESIGNS), APPLICATION OR OTHER DESIGN ADVICE, WEB TOOLS, SAFETY INFORMATION, AND OTHER RESOURCES “AS IS”
AND WITH ALL FAULTS, AND DISCLAIMS ALL WARRANTIES, EXPRESS AND IMPLIED, INCLUDING WITHOUT LIMITATION ANY
IMPLIED WARRANTIES OF MERCHANTABILITY, FITNESS FOR A PARTICULAR PURPOSE OR NON-INFRINGEMENT OF THIRD
PARTY INTELLECTUAL PROPERTY RIGHTS.
These resources are intended for skilled developers designing with TI products. You are solely responsible for (1) selecting the appropriate
TI products for your application, (2) designing, validating and testing your application, and (3) ensuring your application meets applicable
standards, and any other safety, security, regulatory or other requirements.
These resources are subject to change without notice. TI grants you permission to use these resources only for development of an
application that uses the TI products described in the resource. Other reproduction and display of these resources is prohibited. No license
is granted to any other TI intellectual property right or to any third party intellectual property right. TI disclaims responsibility for, and you
will fully indemnify TI and its representatives against, any claims, damages, costs, losses, and liabilities arising out of your use of these
resources.
TI’s products are provided subject to TI’s Terms of Sale or other applicable terms available either on ti.com or provided in conjunction with
such TI products. TI’s provision of these resources does not expand or otherwise alter TI’s applicable warranties or warranty disclaimers for
TI products.
TI objects to and rejects any additional or different terms you may have proposed. IMPORTANT NOTICE
Mailing Address: Texas Instruments, Post Office Box 655303, Dallas, Texas 75265
Copyright © 2022, Texas Instruments Incorporated