Texas Instruments 的 AWR1243 规格书
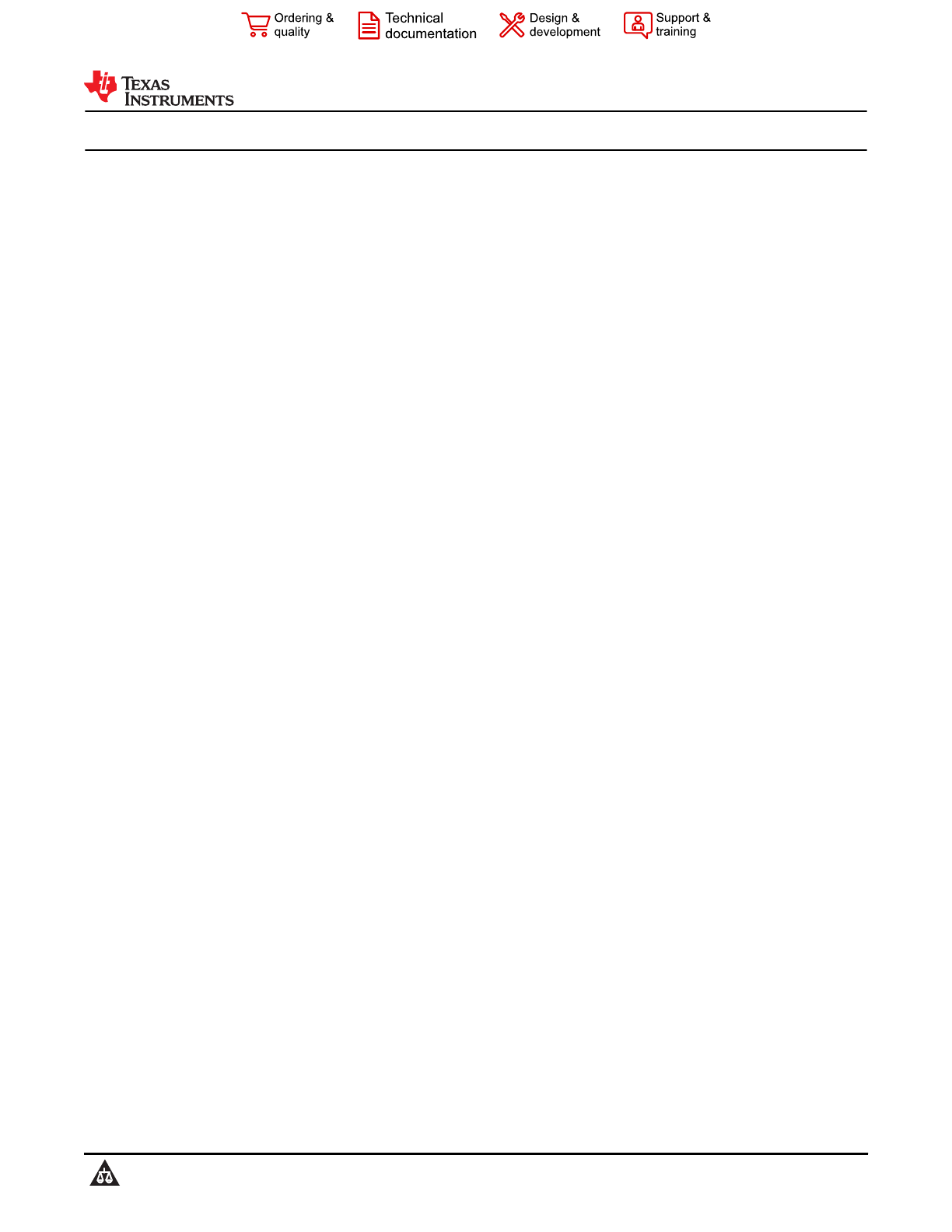
AWR1243 Single-Chip 77- and 79-GHz FMCW Transceiver
1 Features
• FMCW transceiver
– Integrated PLL, transmitter, receiver, Baseband,
and ADC
– 76- to 81-GHz coverage with 4 GHz available
bandwidth
– Four receive channels
– Three transmit channels (two can be used
simultaneously)
– Ultra-accurate chirp engine based on fractional-
N PLL
– TX power: 12 dBm
– RX noise figure:
• 14 dB (76 to 77 GHz)
• 15 dB (77 to 81 GHz)
– Phase noise at 1 MHz:
• –95 dBc/Hz (76 to 77 GHz)
• –93 dBc/Hz (77 to 81 GHz)
• Built-in calibration and self-test
– Built-in firmware (ROM)
– Self-calibrating system across process and
temperature
• Host interface
– Control interface with external processor over
SPI
– Data interface with external processor over
MIPI D-PHY and CSI2 V1.1
– Interrupts for fault reporting
•Functional Safety-Compliant
– Developed for functional safety applications
– Documentation available to aid ISO 26262
functional safety system design up to ASIL-D
– Hardware integrity up to ASIL-B
– Safety-related certification
• ISO 26262 certified upto ASIL B by TUV
SUD
• AEC-Q100 qualified
• Device advanced features
– Embedded self-monitoring with no host
processor involvement
– Complex baseband architecture
– Embedded interference detection capability
• Power management
– Built-in LDO network for enhanced PSRR
– I/Os support dual voltage 3.3 V/1.8 V
• Clock source
– Supports externally driven clock (square/sine)
at 40 MHz
– Supports 40 MHz crystal connection with load
capacitors
• Easy hardware design
– 0.65-mm pitch, 161-pin 10.4 mm × 10.4 mm
flip chip BGA package for easy assembly and
low-cost PCB design
– Small solution size
• Operating Conditions
– Junction temp range: –40°C to 125°C
AWR1243
SWRS188D – MAY 2017 – REVISED DECEMBER 2021
An IMPORTANT NOTICE at the end of this data sheet addresses availability, warranty, changes, use in safety-critical applications,
intellectual property matters and other important disclaimers. PRODUCTION DATA.
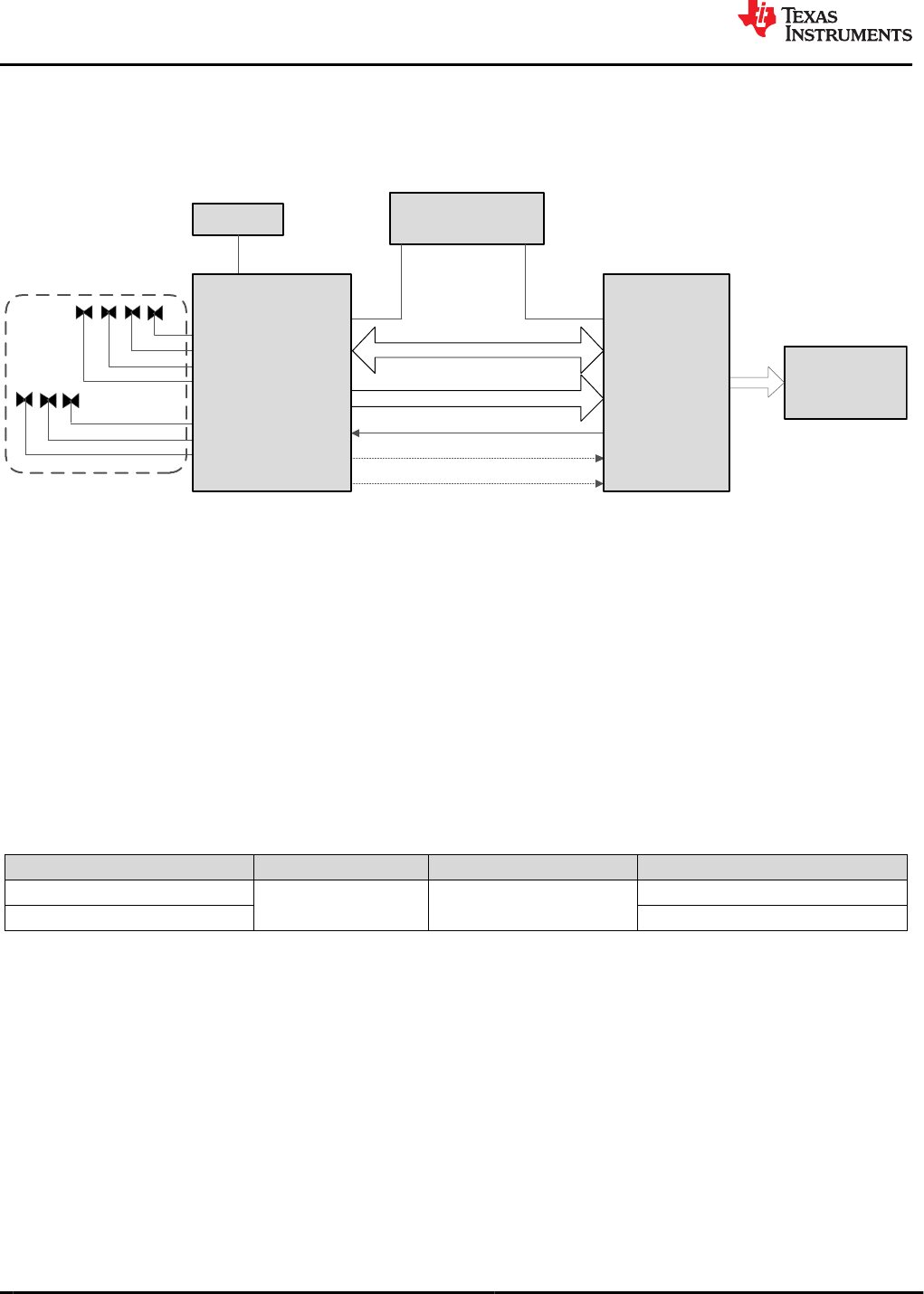
2 Applications
•Automotive Sensor for measuring range, velocity
and angle
•Automated highway driving
•Automatic emergency braking
•Adaptive cruise control
Antenna
Structure SPI/I2C
Power Management Crystal
Interface to
External
Peripherals
CSI2 (4 Lane Data + 1 Clock lane)
Reset
Error
MCU Clock
mmWave Sensor
RX1
RX2
RX3
RX4
TX1
TX2
TX3
External
MCU
Figure 2-1. Autonomous Radar Sensor For Automotive Applications
3 Description
The AWR1243 device is an integrated single-chip FMCW transceiver capable of operation in the 76- to 81-GHz
band. The device enables unprecedented levels of integration in an extremely small form factor. AWR1243 is an
ideal solution for low power, self-monitored, ultra-accurate radar systems in the automotive space.
The AWR1243 device is a self-contained FMCW transceiver single-chip solution that simplifies the
implementation of Automotive Radar sensors in the band of 76 to 81 GHz. It is built on TI’s low-power 45-nm
RFCMOS process, which enables a monolithic implementation of a 3TX, 4RX system with built-in PLL and ADC
converters. Simple programming model changes can enable a wide variety of sensor implementation (Short,
Mid, Long) with the possibility of dynamic reconfiguration for implementing a multimode sensor. Additionally,
the device is provided as a complete platform solution including TI reference designs, software drivers, sample
configurations, API guides, and user documentation.
Device Information
PART NUMBER(2) PACKAGE(1) BODY SIZE TRAY / TAPE AND REEL
AWR1243FBIGABLQ1 FCBGA (161) 10.4 mm × 10.4 mm Tray
AWR1243FBIGABLRQ1 Tape and Reel
(1) For more information, see Section 13, Mechanical, Packaging, and Orderable Information.
(2) For more information, see Section 12.1, Device Nomenclature.
AWR1243
SWRS188D – MAY 2017 – REVISED DECEMBER 2021 www.ti.com
2Submit Document Feedback Copyright © 2021 Texas Instruments Incorporated
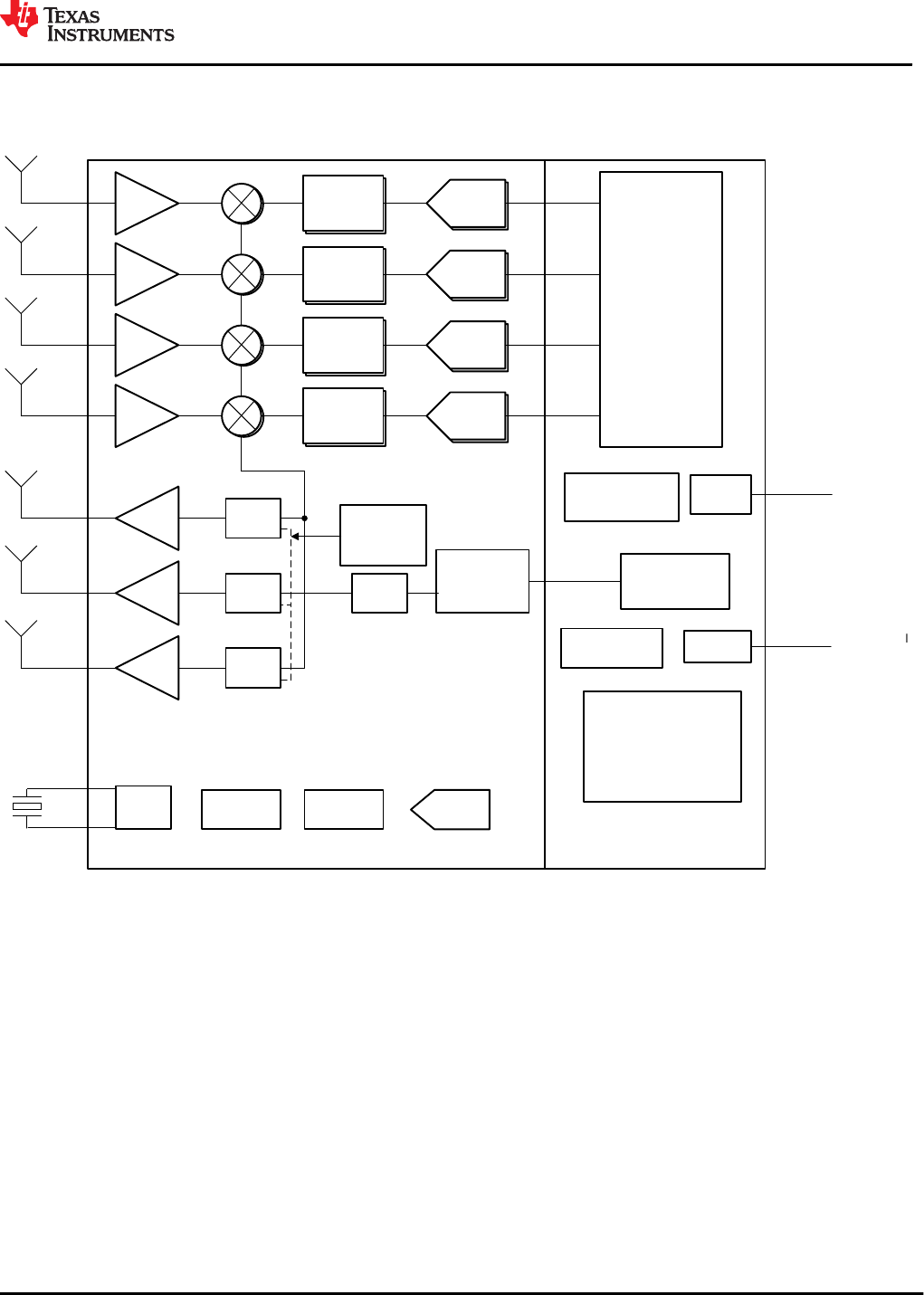
4 Functional Block Diagram
Figure 4-1 shows the functional block diagram of the device.
ADC Buffer
16KB PING/PONG
IF ADC
Digital Front-end
(Decimation filter
chain)
LNA
IF ADC
LNA
IF ADC
LNA
IF ADC
LNA
PA û-
PA û-
PA û-
Synth
(20 GHz) Ramp Generator
x4
Osc.
RF Control / BIST
GPADCVMON Temp(B)
SPI/I2C
CSI2
RF/Analog Subsystem
Host control
interface
ADC output
interface
Digital
Synth Cycle
Counter
Phase
Shifter
Control (A)
A. Phase Shift Control:
• 0° / 180° BPM for AWR1243
B. Internal temperature sensor accuracy is ± 7 °C.
Figure 4-1. Functional Block Diagram
www.ti.com
AWR1243
SWRS188D – MAY 2017 – REVISED DECEMBER 2021
Copyright © 2021 Texas Instruments Incorporated Submit Document Feedback 3

Table of Contents
1 Features............................................................................1
2 Applications..................................................................... 2
3 Description.......................................................................2
4 Functional Block Diagram.............................................. 3
5 Revision History.............................................................. 5
6 Device Comparison......................................................... 6
6.1 Related Products........................................................ 7
7 Terminal Configuration and Functions..........................8
7.1 Pin Diagram................................................................ 8
7.2 Signal Descriptions................................................... 12
8 Specifications................................................................ 16
8.1 Absolute Maximum Ratings...................................... 16
8.2 ESD Ratings............................................................. 16
8.3 Power-On Hours (POH)............................................ 17
8.4 Recommended Operating Conditions.......................17
8.5 Power Supply Specifications.....................................18
8.6 Power Consumption Summary................................. 19
8.7 RF Specification........................................................20
8.8 Thermal Resistance Characteristics for FCBGA
Package [ABL0161].....................................................21
8.9 Timing and Switching Characteristics....................... 21
9 Detailed Description......................................................33
9.1 Overview................................................................... 33
9.2 Functional Block Diagram......................................... 33
9.3 Subsystems.............................................................. 34
9.4 Other Subsystems.................................................... 37
10 Monitoring and Diagnostics....................................... 39
10.1 Monitoring and Diagnostic Mechanisms................. 39
11 Applications, Implementation, and Layout............... 42
11.1 Application Information............................................42
11.2 Short-, Medium-, and Long-Range Radar ..............42
11.3 Reference Schematic..............................................43
12 Device and Documentation Support..........................44
12.1 Device Nomenclature..............................................44
12.2 Tools and Software................................................. 45
12.3 Documentation Support.......................................... 45
12.4 Support Resources................................................. 45
12.5 Trademarks.............................................................46
12.6 Electrostatic Discharge Caution..............................46
12.7 Glossary..................................................................46
13 Mechanical, Packaging, and Orderable
Information.................................................................... 47
13.1 Packaging Information............................................ 47
13.2 Tray Information for ................................................47
AWR1243
SWRS188D – MAY 2017 – REVISED DECEMBER 2021 www.ti.com
4Submit Document Feedback Copyright © 2021 Texas Instruments Incorporated

5 Revision History
Changes from May 1, 2020 to December 8, 2021 (from Revision C (May 2020) to Revision D
(December 2021)) Page
•Global: Updated to reflect Functional Safety-Compliance and relevant certification collateral...........................1
•Global: Replaced "A2D" with "ADC"; Changed Masters Subsystem and Masters R4F to Main Subsystem and
Main R4F; Shift to more inclusive langauge made in terms of Master/Slave terminology..................................1
•(Features) : Mentioned the specific operating temperature range for the mmWave Sensor.............................. 1
•(Applications) :Revised the figure and updated application links........................................................................2
• (Device Information): Removed a pre-production orderable part number (XA1243FPBGABL) from the table
and its assosiated features. ............................................................................................................................... 2
• Updated/Changed Functional Block Diagram to remove XA1243FPBGABL OPN specific features................. 3
•(Device Comparison) : Removed a row on Functionaly-Safety compliance and instead added a table-note for
this and LVDS Interface; modified the existing table-note on simultaneous TX operation; Additional
information on Device security added.................................................................................................................6
•(Device Comparison) : Updated/Changed RF Specification Receiver from "Max real sampling rate (Msps)" to
"Max real/complex 2x sampling rate (Msps)"; and "Max complex sampling rate (Msps)" to "Max complex 1x
sampling rate (Msps)".........................................................................................................................................6
•(Signal Descriptions): Removed XA1243FPBGABL OPN specific pin functions; updated descriptions for
CLKP and CLKM pins for Reference Oscillator................................................................................................ 12
•(Absolute Maximum Ratings): Added entries for externally supplied power on the RF inputs (TX and RX) and
a table-note for the signal level applied on TX..................................................................................................16
•(Power Supply Specifications): Updated/Changed footnote in Table 8-1 ........................................................ 18
• (Maximum Current Rating at Power Terminals): Updated footnotes section to add estimation assumption for
VIOIN rail.......................................................................................................................................................... 19
•(Average Power Consumption at Power Terminals): Removed 3TX, 4RX power numbers since only 2TX are
operational simultaneously in the device.......................................................................................................... 19
•(RF Specification): Updated/Changed RF Specification Receiver from "A2D sampling rate (complex)" to "ADC
sampling rate (complex 1x)"; and "A2D sampling rate (real)" to "ADC sampling rate (real/complex 2x)"........ 20
•(RF Specification): Updated/Changed the table to remove XA1243FPBGABL specific features.....................20
•(Synchronized Frame Triggering): Updated the maximum pulse width to 4ns................................................. 22
•(Clock Specifications): Updated/Changed Table 8-6 to reflect correct device operating temperature range... 24
•(Table. External Clock Mode Specifications): Revised frequency tolerance specs from +/-50 to +/-100 ppm..24
•(Switching Characteristics for Output Timing versus Load Capacitance): Updated/Modified the table to
remove Slew Rate = 1 condition; removed a footnote......................................................................................30
•Figure 9-1: Updated the figure to remove XA1243FPBGABL OPN specific features. .....................................33
•(Monitoring and Diagnostic Mechanisms): Added a new section..................................................................... 39
•(Reference Schematics) : Added weblinks to AWR1243 EVM documentation collateral ................................ 43
•(Device Nomenclature):Updated/changed Device Nomenclature ................................................................... 44
www.ti.com
AWR1243
SWRS188D – MAY 2017 – REVISED DECEMBER 2021
Copyright © 2021 Texas Instruments Incorporated Submit Document Feedback 5

6 Device Comparison
FUNCTION AWR1243(1) AWR1443 AWR1642 AWR1843
Number of receivers 4 4 4 4
Number of transmitters 3 3 2 3
On-chip memory — 576KB 1.5MB 2MB
Max I/F (Intermediate Frequency) (MHz) 15 5 5 10
Max real/complex 2x sampling rate (Msps) 37.5 12.5 12.5 25
Max complex 1x sampling rate (Msps) 18.75 6.25 6.25 12.5
Device Security(2) — — Yes Yes
Processor
MCU (R4F) — Yes Yes Yes
DSP (C674x) — — Yes Yes
Peripherals
Serial Peripheral Interface (SPI) ports 1 1 2 2
Quad Serial Peripheral Interface (QSPI) — Yes Yes Yes
Inter-Integrated Circuit (I2C) interface — 1 1 1
Controller Area Network (DCAN) interface — Yes Yes Yes
CAN-FD — — Yes Yes
Trace — — Yes Yes
PWM — — Yes Yes
Hardware In Loop (HIL/DMM) — — Yes Yes
GPADC — Yes Yes Yes
LVDS/Debug(3) Yes Yes Yes Yes
CSI2 Yes — — —
Hardware accelerator — Yes — Yes
1-V bypass mode Yes Yes Yes Yes
Cascade (20-GHz sync) — — — —
JTAG — Yes Yes Yes
Number of Tx that can be simultaneously used 2 2 2 3(4)
Per chirp configurable Tx phase shifter — — — Yes
Product
status(5)
PRODUCT PREVIEW (PP),
ADVANCE INFORMATION (AI),
or PRODUCTION DATA (PD)
PD PD PD PD
(1) Developed for Functional Safety applications, the device supports hardware integrity upto ASIL-B. Refer to the related documentation
for more details.
(2) Device security features including Secure Boot and Customer Programmable Keys are available in select devices for only select part
variants as indicated by the Device Type identifier in Section 3, Device Information table.
(3) The LVDS interface is not a production interface and is only used for debug.
(4) 3 Tx Simultaneous operation is supported only in AWR1843 with 1V LDO bypass and PA LDO disable mode. In this mode 1V supply
needs to be fed on the VOUT PA pin. Rest of the other devices only support simultaneous operation of 2 Transmitters.
(5) PRODUCTION DATA information is current as of publication date. Products conform to specifications per the terms of the Texas
Instruments standard warranty. Production processing does not necessarily include testing of all parameters.
AWR1243
SWRS188D – MAY 2017 – REVISED DECEMBER 2021 www.ti.com
6Submit Document Feedback Copyright © 2021 Texas Instruments Incorporated
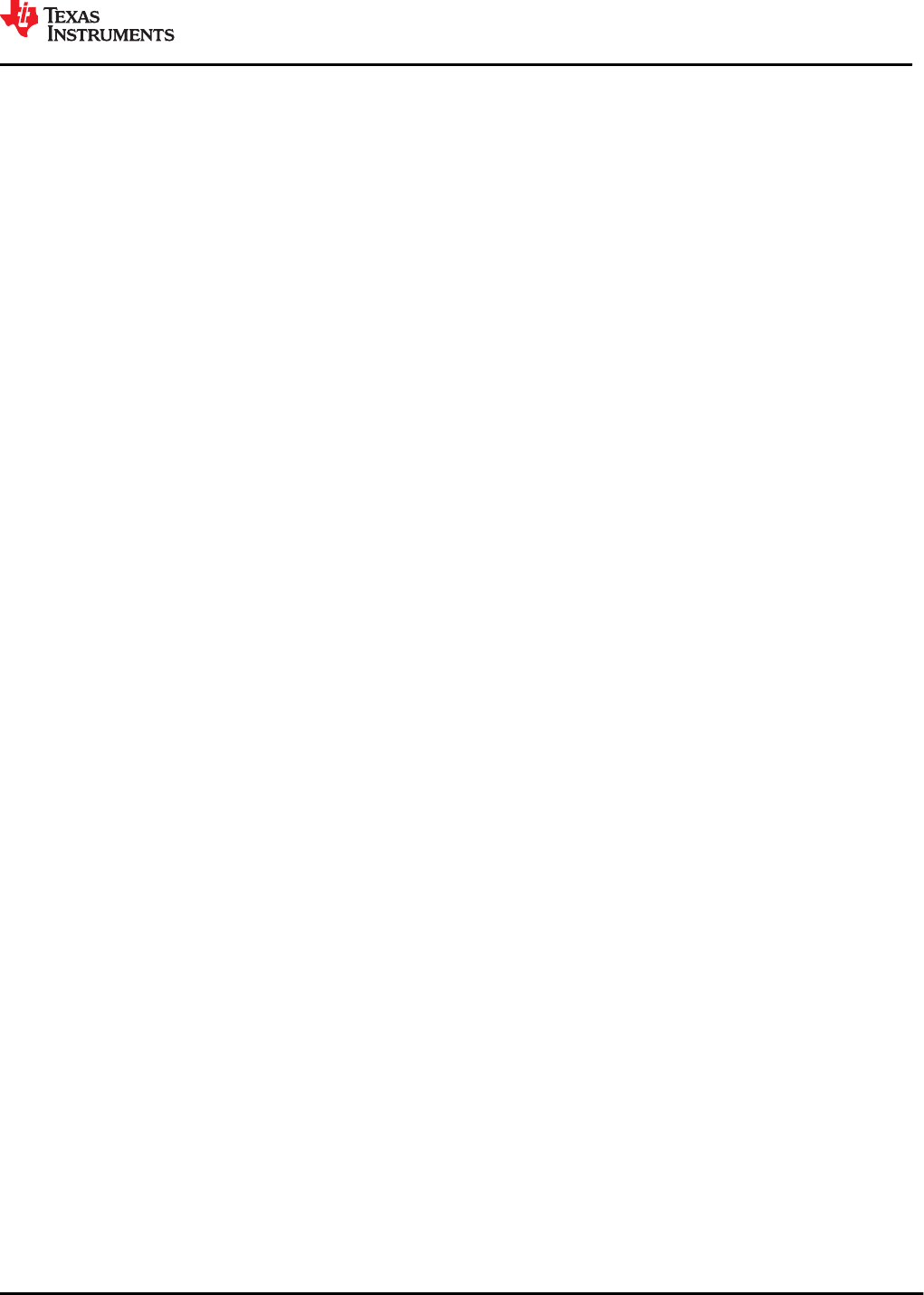
6.1 Related Products
For information about other devices in this family of products or related products see the links that follow.
mmWave Sensors TI’s mmWave sensors rapidly and accurately sense range, angle and velocity with
less power using the smallest footprint mmWave sensor portfolio for automotive
applications.
Automotive mmWave
Sensors
TI’s automotive mmWave sensor portfolio offers high-performance radar front end to
ultra-high resolution, small and low-power single-chip radar solutions. TI’s scalable
sensor portfolio enables design and development of ADAS system solution for every
performance, application and sensor configuration ranging from comfort functions to
safety functions in all vehicles.
Companion Products
for AWR1243
Review products that are frequently purchased or used in conjunction with this product.
www.ti.com
AWR1243
SWRS188D – MAY 2017 – REVISED DECEMBER 2021
Copyright © 2021 Texas Instruments Incorporated Submit Document Feedback 7

7 Terminal Configuration and Functions
7.1 Pin Diagram
Figure 7-1 shows the pin locations for the 161-pin FCBGA package. Figure 7-2, Figure 7-3, Figure 7-4, and
Figure 7-5 show the same pins, but split into four quadrants.
1 2 3 4 5 6 7 8 9 10 11 12 13 14 15
A
B
C
D
E
F
G
H
J
K
L
M
N
P
R
Not to scale
VSSA VOUT_PA VSSA VSSA VSSA VSSA VOUT
_14APLL
VOUT
_14SYNTH
OSC
_CLKOUT VSSA
FM_CW
_SYNCIN1 VOUT_PA VSSA TX1 VSSA TX2 VSSA TX3 VSSA VBGAP VIN
_18CLK
VIN
_18VCO VSSA VSSA FM_CW
_CLKOUT
VSSA VIN
_13RF2 VSSA VSSA VSSA VSSA VSSA VSSA VSSA VSSA
FM_CW
_SYNCOUT
VIN
_13RF2
VIOIN
_18DIFF
FM_CW
_SYNCIN2
VSSA VSSA VSSA VSS VSS VSS VSS VSS VSSA CLKP VSSA
RX4 VSSA VIN_18BB VSS VSS VDDIN CLKM
VSSA VSSA VSSA VIN
_13RF1 VSS VSS VSS VSS Reserved CSI2
_TXM[0]
CSI2
_TXP[0]
RX3 VSSA VIN
_13RF1 VSS VSS VSS TDI CSI2
_TXM[1]
CSI2
_TXP[1]
VSSA VSSA VSSA VIN
_13RF1 VSS VSS VSS VSS TDO CSI2_CLKM CSI2_CLKP
RX2 VSSA VIN_18BB VSS VSS VSS VSS VSS VIOIN_18 CSI2
_TXM[2]
CSI2
_TXP[2]
VSSA VSSA VSSA VSS VSS VSS VSS TMS CSI2
_TXM[3]
CSI2
_TXP[3]
RX1 TCK HS_M
_Debug1
HS_P
_Debug1
VSSA VSSA VSSA GPIO[0] RS232_RX RS232_TX GPIO[1] NERROR_OUTMCU_CLK_OUT Sync_in VDDIN WARM
_RESET GPIO[2] HS_M
_Debug2
HS_P
_Debug2
Reserved MISO_1 SPI_HOST_INTR_1NERROR_IN QSPI_CS QSPI[1] QSPI[3] Sync_out NRESET PMIC_CLK_OUT VNWA VDDIN
VSSA Reserved Reserved Reserved VDDIN SPI_CS_1 MOSI_1 SPI_CLK_1 QSPI_CLK QSPI[0] QSPI[2] VIOIN VIN_SRAM VSS
ANAMUX VSENSE
VSSA
Analog Test 1 Analog Test 2 Analog Test 3
Analog Test 4
Figure 7-1. Pin Diagram
AWR1243
SWRS188D – MAY 2017 – REVISED DECEMBER 2021 www.ti.com
8Submit Document Feedback Copyright © 2021 Texas Instruments Incorporated
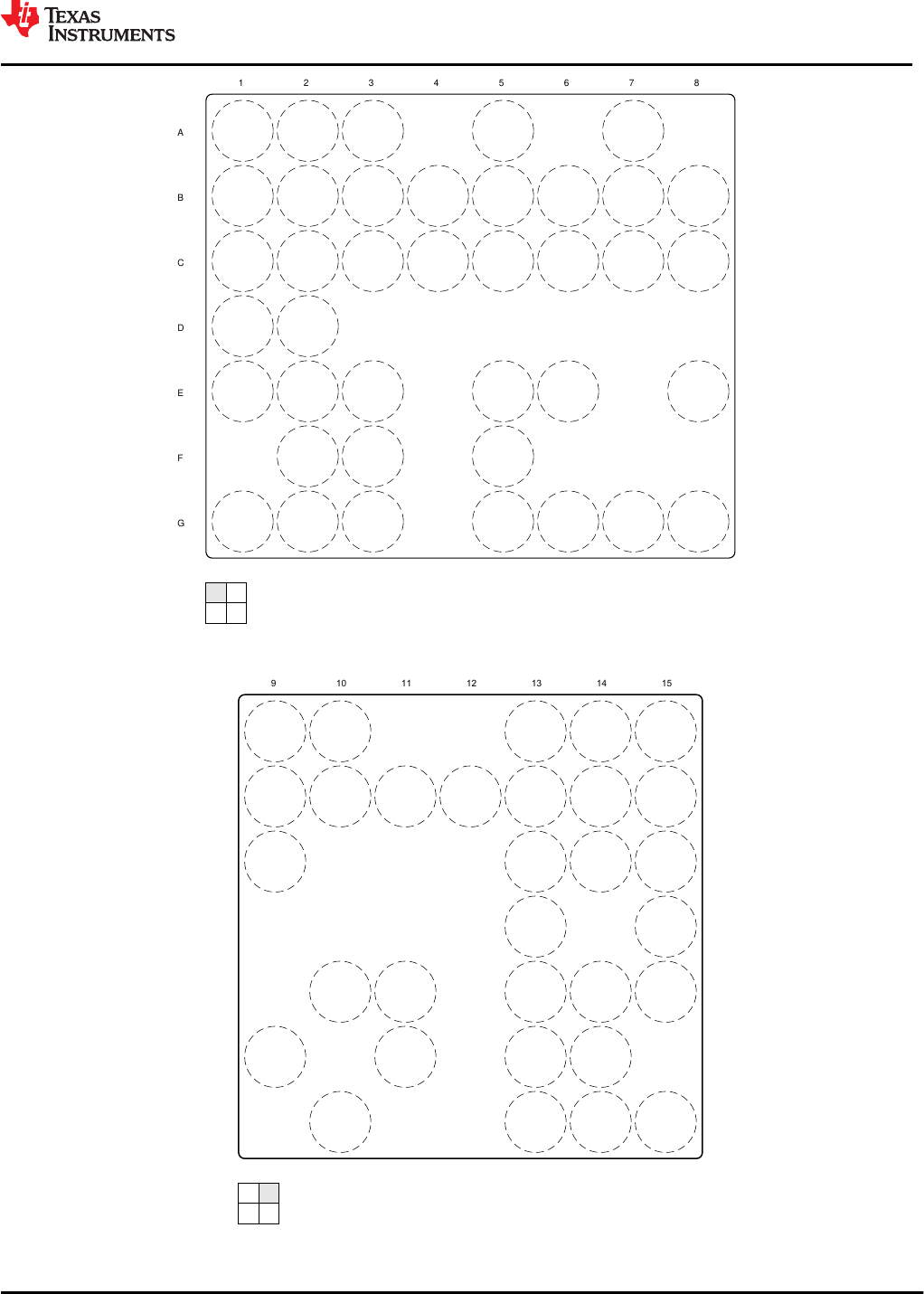
1 2 3 4 5 6 7 8
A
B
C
D
E
F
G
Not to scale
VSSA VOUT_PA VSSA VSSA VSSA
FM_CW
_SYNCIN1 VOUT_PA VSSA TX1 VSSA TX2 VSSA TX3
VSSA VIN
_13RF2 VSSA VSSA VSSA VSSA VSSA VSSA
FM_CW
_SYNCOUT
VIN
_13RF2
VSSA VSSA VSSA VSS VSS VSS
RX4 VSSA VIN_18BB
VSSA VSSA VSSA VIN
_13RF1 VSS VSS VSS
1
3
2
4
Figure 7-2. Top Left Quadrant
9 10 11 12 13 14 15
A
B
C
D
E
F
G
Not to scale
VSSA VOUT
_14APLL
VOUT
_14SYNTH
OSC
_CLKOUT VSSA
VSSA VBGAP VIN
_18CLK
VIN
_18VCO VSSA VSSA FM_CW
_CLKOUT
VSSA VSSA
VIOIN
_18DIFF
FM_CW
_SYNCIN2
VSS VSS VSSA CLKP VSSA
VSS VSS VDDIN CLKM
VSS Reserved CSI2
_TXM[0]
CSI2
_TXP[0]
1
3
2
4
ANAMUX VSENSE
Figure 7-3. Top Right Quadrant
www.ti.com
AWR1243
SWRS188D – MAY 2017 – REVISED DECEMBER 2021
Copyright © 2021 Texas Instruments Incorporated Submit Document Feedback 9

12345678
H
J
K
L
M
N
P
R
Not to scale
RX3 VSSA VIN
_13RF1 VSS
VSSA VSSA VSSA VIN
_13RF1 VSS VSS VSS
RX2 VSSA VIN_18BB VSS VSS
VSSA VSSA VSSA VSS VSS VSS
RX1
VSSA VSSA VSSA GPIO[0] RS232_RX RS232_TX GPIO[1] NERROR_OUT
Reserved MISO_1 SPI_HOST_INTR_1NERROR_IN QSPI_CS
VSSA Reserved Reserved Reserved VDDIN SPI_CS_1 MOSI_1
1
3
2
4
VSSA
Analog Test 1 Analog Test 2 Analog Test 3
Analog Test 4
Figure 7-4. Bottom Left Quadrant
AWR1243
SWRS188D – MAY 2017 – REVISED DECEMBER 2021 www.ti.com
10 Submit Document Feedback Copyright © 2021 Texas Instruments Incorporated
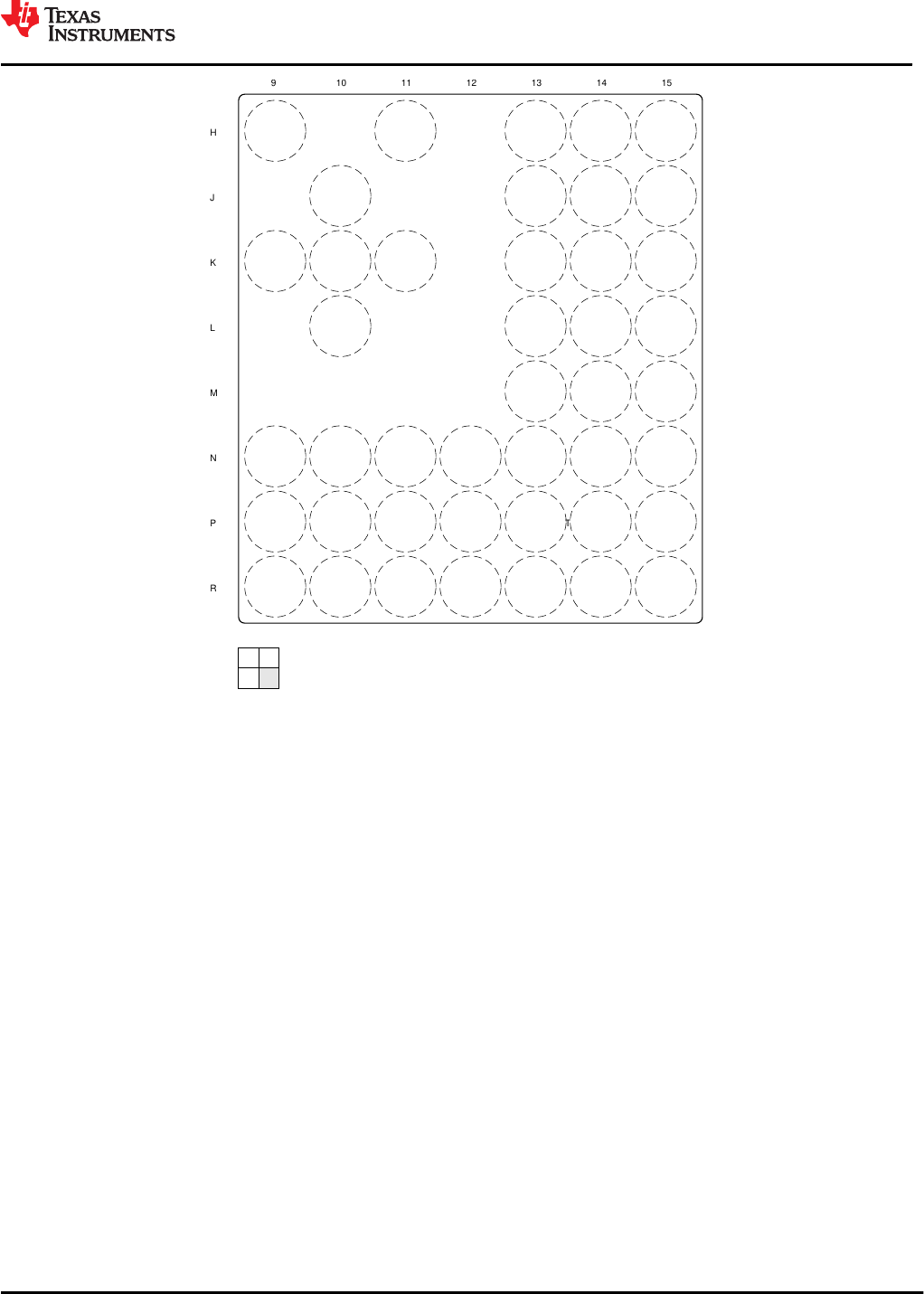
9 10 11 12 13 14 15
H
J
K
L
M
N
P
R
Not to scale
VSS VSS TDI CSI2
_TXM[1]
CSI2
_TXP[1]
VSS TDO CSI2_CLKM CSI2_CLKP
VSS VSS VSS VIOIN_18 CSI2
_TXM[2]
CSI2
_TXP[2]
VSS TMS CSI2
_TXM[3]
CSI2
_TXP[3]
TCK HS_M
_Debug1
HS_P
_Debug1
MCU_CLK_OUT Sync_in VDDIN WARM
_RESET GPIO[2] HS_M
_Debug2
HS_P
_Debug2
QSPI[1] QSPI[3] Sync_out NRESET PMIC_CLK_OUT VNWA VDDIN
SPI_CLK_1 QSPI_CLK QSPI[0] QSPI[2] VIOIN VIN_SRAM VSS
1
3
2
4
Figure 7-5. Bottom Right Quadrant
www.ti.com
AWR1243
SWRS188D – MAY 2017 – REVISED DECEMBER 2021
Copyright © 2021 Texas Instruments Incorporated Submit Document Feedback 11

7.2 Signal Descriptions
Section 7.2.1 lists the pins by function and describes that function.
Note
All IO pins of the device (except NERROR IN, NERROR_OUT, and WARM_RESET) are non-failsafe;
hence, care needs to be taken that they are not driven externally without the VIO supply being present
to the device.
7.2.1 Signal Descriptions
FUNCTION SIGNAL NAME PIN
NUMBER
PIN
TYPE
DEFAULT PULL
STATUS(1) DESCRIPTION
Transmitters
TX1 B4 O — Single-ended transmitter1 o/p
TX2 B6 O — Single-ended transmitter2 o/p
TX3 B8 O — Single-ended transmitter3 o/p
Receivers
RX1 M2 I — Single-ended receiver1 i/p
RX2 K2 I — Single-ended receiver2 i/p
RX3 H2 I — Single-ended receiver3 i/p
RX4 F2 I — Single-ended receiver4 i/p
CSI2 TX
CSI2_TXP[0] G15 O — Differential data Out – Lane 0 (for CSI and LVDS
debug interface)
CSI2_TXM[0] G14 O —
CSI2_CLKP J15 O — Differential clock Out (for CSI and LVDS debug
interface)
CSI2_CLKM J14 O —
CSI2_TXP[1] H15 O — Differential data Out – Lane 1 (for CSI and LVDS
debug interface)
CSI2_TXM[1] H14 O —
CSI2_TXP[2] K15 O — Differential data Out – Lane 2 (for CSI and LVDS
debug interface)
CSI2_TXM[2] K14 O —
CSI2_TXP[3] L15 O — Differential data Out – Lane 3 (for CSI and LVDS
debug interface)
CSI2_TXM[3] L14 O —
HS_DEBUG1_P M15 O — Differential debug port 1 (for LVDS debug interface)
HS_DEBUG1_M M14 O —
HS_DEBUG2_P N15 O — Differential debug port 2 (for LVDS debug interface)
HS_DEBUG2_M N14 O —
Reserved
Space
FM_CW_CLKOUT B15 O — Reserved Signal. Not applicable in AWR1243.
FM_CW_SYNCOUT D1
FM_CW_SYNCIN1 B1 I — Reserved Signal. Not applicable in AWR1243.
FM_CW_SYNCIN2 D15
Reference clock OSC_CLKOUT A14 O —
Reference clock output from clocking subsystem
after cleanup PLL. Can be used by peripheral chip
in multichip cascading
System
synchronization
SYNC_OUT P11 O Pull Down
Low-frequency frame synchronization signal output.
Can be used by peripheral chip in multichip
cascading
SYNC_IN N10 I Pull Down
Low-frequency frame synchronization signal input.
This signal could also be used as a hardware trigger
for frame start
AWR1243
SWRS188D – MAY 2017 – REVISED DECEMBER 2021 www.ti.com
12 Submit Document Feedback Copyright © 2021 Texas Instruments Incorporated
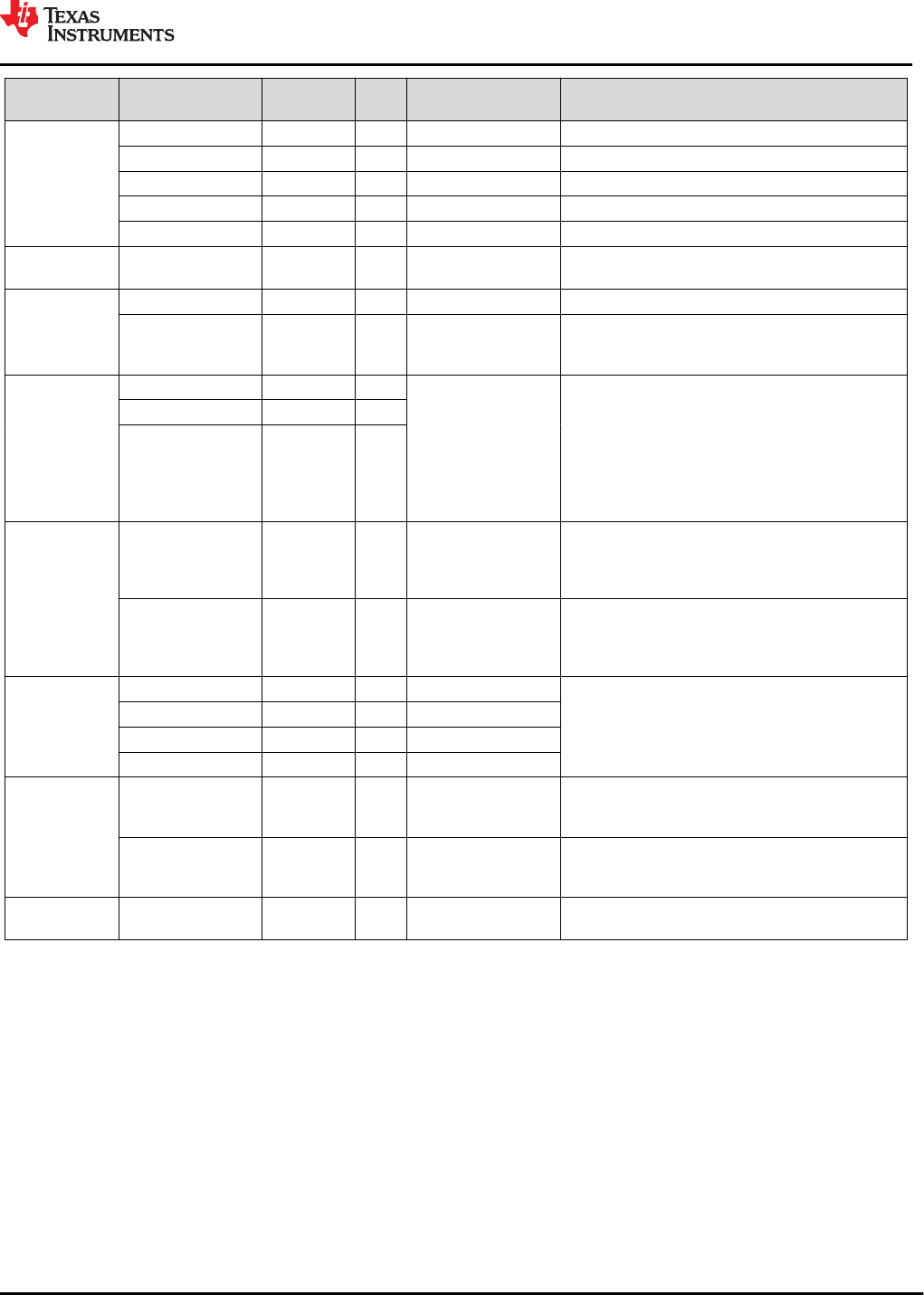
FUNCTION SIGNAL NAME PIN
NUMBER
PIN
TYPE
DEFAULT PULL
STATUS(1) DESCRIPTION
SPI control
interface from
external MCU
(default
peripheral
mode)
SPI_CS_1 R7 I Pull Up SPI chip select
SPI_CLK_1 R9 I Pull Down SPI clock
MOSI_1 R8 I Pull Up SPI data input
MISO_1 P5 O Pull Up SPI data output
SPI_HOST_INTR_1 P6 O Pull Down SPI interrupt to host
RESERVED R3, R4, R5,
P4 —
Reset
NRESET P12 I — Power on reset for chip. Active low
WARM_RESET(2) N12 IO Open Drain
Open-drain fail-safe warm reset signal. Can be
driven from PMIC for diagnostic or can be used as
status signal that the device is going through reset.
SOP2 P13 I The SOP pins are driven externally (weak drive)
and the AWR device senses the state of these pins
during bootup to decide the bootup mode. After boot
the same pins have other functionality.
[SOP2 SOP1 SOP0] = [0 0 1] → Functional SPI
mode
[SOP2 SOP1 SOP0] = [1 0 1] → Flashing mode
[SOP2 SOP1 SOP0] = [0 1 1] → debug mode
Sense on Power SOP1 P11 I —
SOP0 J13 I
Safety
NERROR_OUT N8 O Open Drain
Open-drain fail-safe output signal. Connected to
PMIC/Processor/MCU to indicate that some severe
criticality fault has happened. Recovery would be
through reset.
NERROR_IN P7 I Open Drain
Fail-safe input to the device. Error output from
any other device can be concentrated in the error
signaling monitor module inside the device and
appropriate action can be taken by firmware
JTAG
TMS L13 I Pull Up
JTAG port for TI internal development
TCK M13 I Pull Down
TDI H13 I Pull Up
TDO J13 O —
Reference
oscillator
CLKP E14 I —
In XTAL mode: Input for the reference crystal
In External clock mode: Single ended input
reference clock port
CLKM F14 O —
In XTAL mode: Feedback drive for the reference
crystal
In External clock mode: Connect this port to ground
Band-gap
voltage VBGAP B10 O —
www.ti.com
AWR1243
SWRS188D – MAY 2017 – REVISED DECEMBER 2021
Copyright © 2021 Texas Instruments Incorporated Submit Document Feedback 13
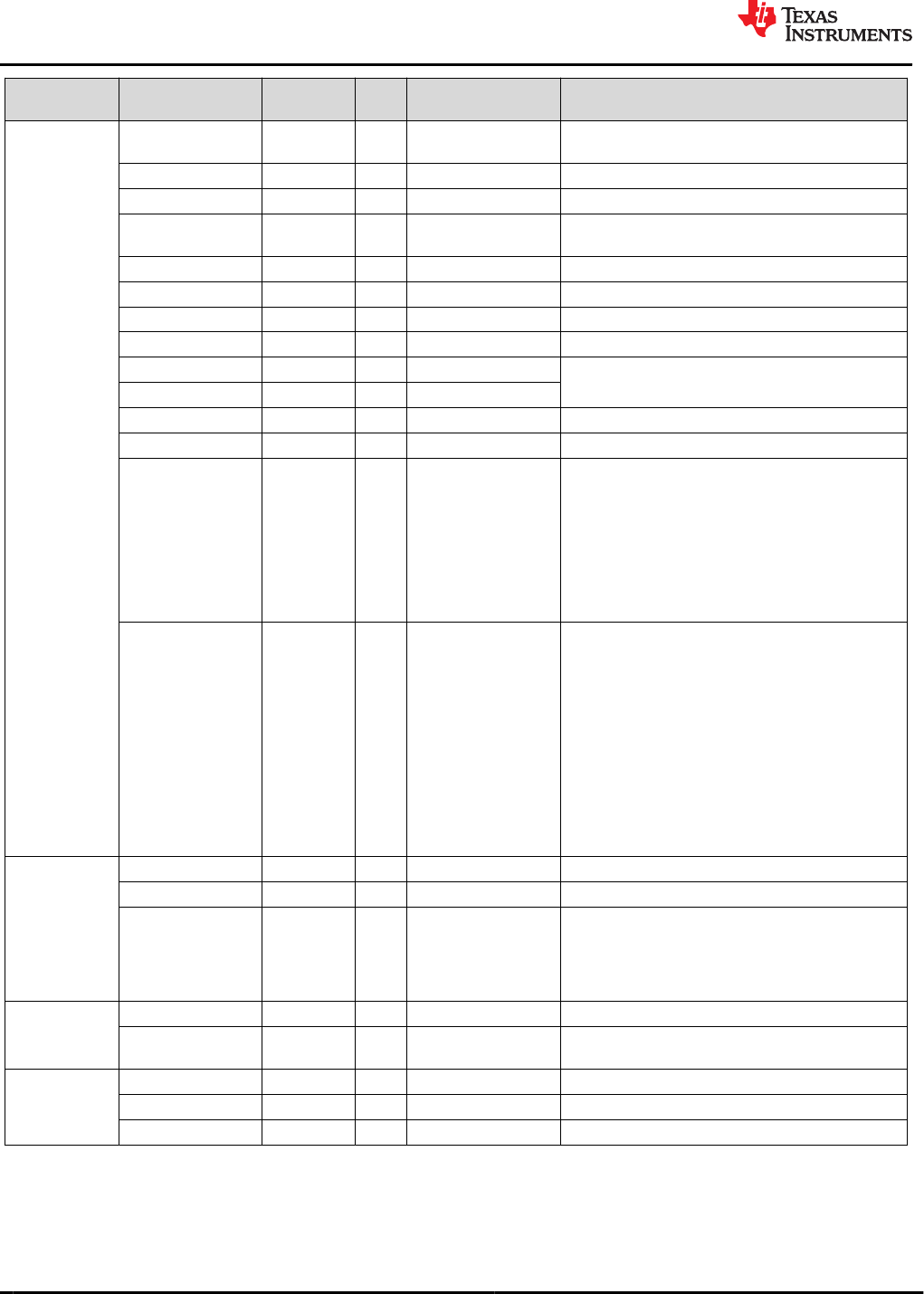
FUNCTION SIGNAL NAME PIN
NUMBER
PIN
TYPE
DEFAULT PULL
STATUS(1) DESCRIPTION
Power supply
VDDIN F13,N11,P15
,R6 POW — 1.2-V digital power supply
VIN_SRAM R14 POW — 1.2-V power rail for internal SRAM
VNWA P14 POW — 1.2-V power rail for SRAM array back bias
VIOIN R13 POW — I/O supply (3.3-V or 1.8-V): All CMOS I/Os would
operate on this supply.
VIOIN_18 K13 POW — 1.8-V supply for CMOS IO
VIN_18CLK B11 POW — 1.8-V supply for clock module
VIOIN_18DIFF D13 POW — 1.8-V supply for CSI2 port
Reserved G13 POW — No connect
VIN_13RF1 G5,J5,H5 POW — 1.3-V Analog and RF supply,VIN_13RF1 and
VIN_13RF2 could be shorted on the board
VIN_13RF2 C2,D2 POW —
VIN_18BB K5,F5 POW — 1.8-V Analog baseband power supply
VIN_18VCO B12 POW — 1.8-V RF VCO supply
VSS
E5,E6,E8,E1
0,E11,F9,F1
1,G6,G7,G8,
G10,H7,H9,
H11,J6,J7,J8
,J10,K7,K8,K
9,K10,K11,L
5,L6,L8,L10,
R15
GND — Digital ground
VSSA
A1,A3,A5,A7
,A9,A15,B3,
B5,B7,B9,B1
3,B14,C1,C3
,C4,C5,C6,C
7,C8,C9,C15
,E1,E2,E3,E
13,E15,F3,G
1,G2,G3,H3,
J1,J2,J3,K3,
L1,L2,L3,
M3,N1,N2,N
3,R1
GND — Analog ground
Internal LDO
output/inputs
VOUT_14APLL A10 O —
VOUT_14SYNTH A13 O —
VOUT_PA A2,B2 IO —
When internal PA LDO is used this pin provides the
output voltage of the LDO. When the internal PA
LDO is bypassed and disabled 1V supply should
be fed on this pin. This is mandatory in 3TX
simultaneous use case.
External clock
out
PMIC_CLK_OUT P13 O — Dithered clock input to PMIC
MCU_CLK_OUT N9 O — Programmable clock given out to external MCU or
the processor
General-
purpose I/Os
GPIO[0] N4 IO Pull Down General-purpose IO
GPIO[1] N7 IO Pull Down General-purpose IO
GPIO[2] N13 IO Pull Down General-purpose IO
AWR1243
SWRS188D – MAY 2017 – REVISED DECEMBER 2021 www.ti.com
14 Submit Document Feedback Copyright © 2021 Texas Instruments Incorporated
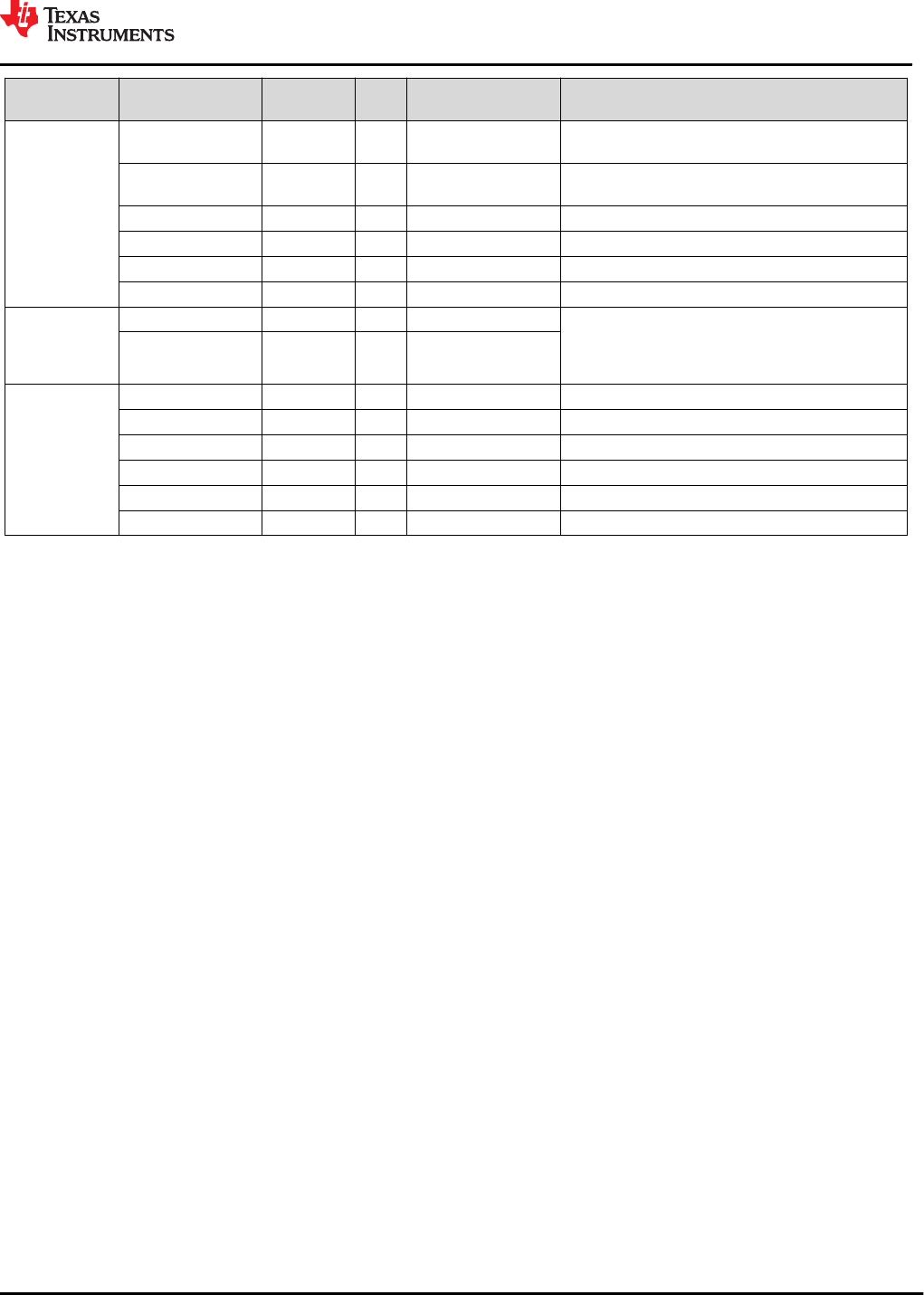
FUNCTION SIGNAL NAME PIN
NUMBER
PIN
TYPE
DEFAULT PULL
STATUS(1) DESCRIPTION
QSPI for Serial
Flash
QSPI_CS P8 O Pull Up Chip-select output from the device. Device is a
controller connected to serial flash peripheral.
QSPI_CLK R10 O Pull Down Clock output from the device. Device is a controller
connected to serial flash peripheral.
QSPI[0] R11 IO Pull Down Data IN/OUT
QSPI[1] P9 IO Pull Down Data IN/OUT
QSPI[2] R12 IO Pull Up Data IN/OUT
QSPI[3] P10 IO Pull Up Data IN/OUT
Flash
programming
and RS232
UART
RS232_TX N6 O Pull Down
UART pins for programming external flash
RS232_RX N5 I Pull Up
Test and Debug
output for
preproduction
phase. Can be
pinned out on
production
hardware for
field debug
Analog Test1 P1 IO — Internal test signal
Analog Test2 P2 IO — Internal test signal
Analog Test3 P3 IO — Internal test signal
Analog Test4 R2 IO — Internal test signal
ANAMUX C13 IO — Internal test signal
VSENSE C14 IO — Internal test signal
(1) Status of PULL structures associated with the IO after device POWER UP.
(2) For the AWR1243 WARM_RESET can be used as an output only pin for status indication.
www.ti.com
AWR1243
SWRS188D – MAY 2017 – REVISED DECEMBER 2021
Copyright © 2021 Texas Instruments Incorporated Submit Document Feedback 15
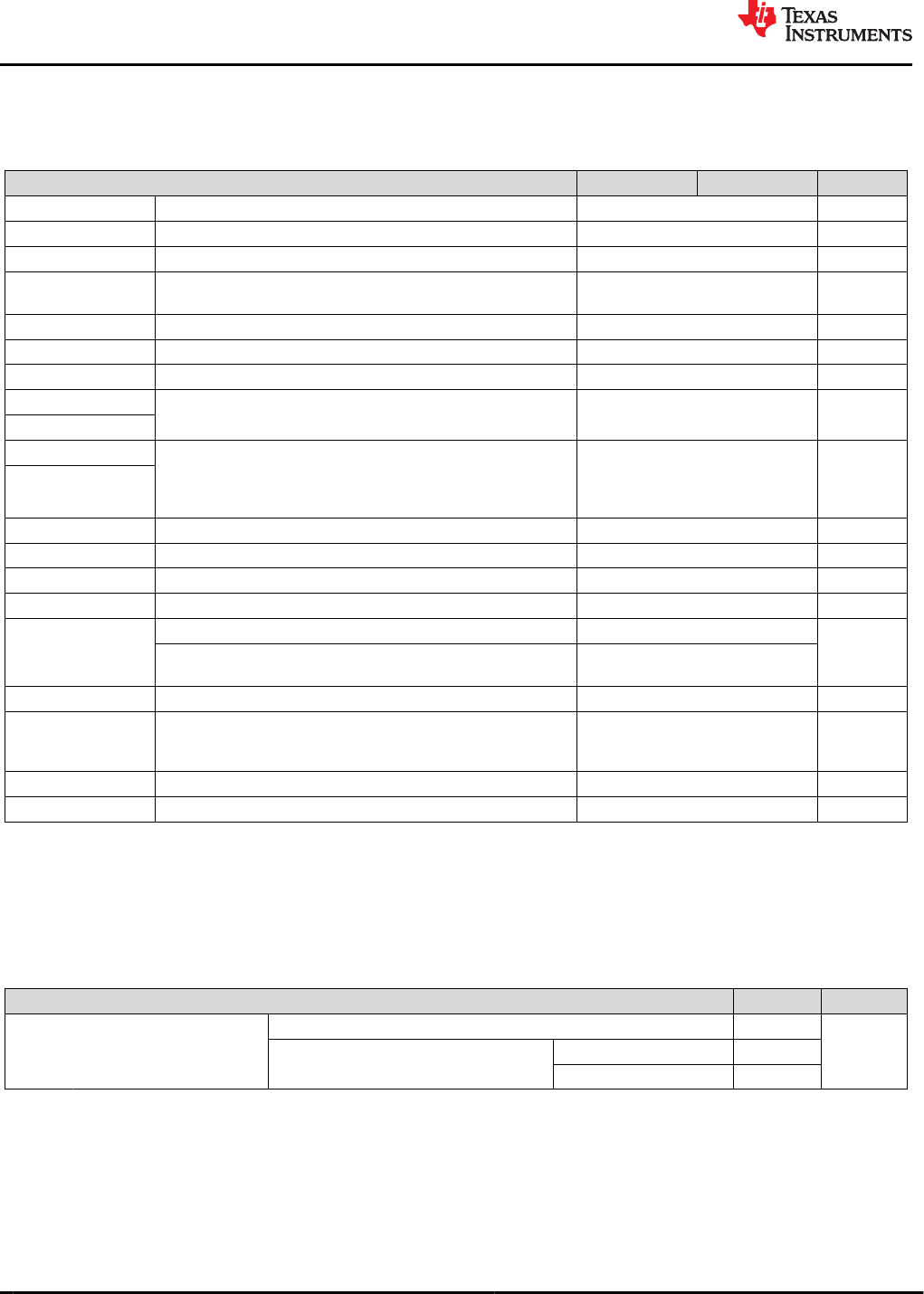
8 Specifications
8.1 Absolute Maximum Ratings
over operating free-air temperature range (unless otherwise noted)
PARAMETERS(1) (2) MIN MAX UNIT
VDDIN 1.2 V digital power supply –0.5 1.4 V
VIN_SRAM 1.2 V power rail for internal SRAM –0.5 1.4 V
VNWA 1.2 V power rail for SRAM array back bias –0.5 1.4 V
VIOIN I/O supply (3.3 V or 1.8 V): All CMOS I/Os would operate on this
supply. –0.5 3.8 V
VIOIN_18 1.8 V supply for CMOS IO –0.5 2 V
VIN_18CLK 1.8 V supply for clock module –0.5 2 V
VIOIN_18DIFF 1.8 V supply for CSI2 port –0.5 2 V
VIN_13RF1 1.3 V Analog and RF supply, VIN_13RF1 and VIN_13RF2 could
be shorted on the board. –0.5 1.45 V
VIN_13RF2
VIN_13RF1 1-V Internal LDO bypass mode. Device supports mode
where external Power Management block can supply 1 V on
VIN_13RF1 and VIN_13RF2 rails. In this configuration, the
internal LDO of the device would be kept bypassed.
–0.5 1.4 V
VIN_13RF2
VIN_18BB 1.8-V Analog baseband power supply –0.5 2 V
VIN_18VCO supply 1.8-V RF VCO supply –0.5 2 V
RX1-4 Externally applied power on RF inputs 10 dBm
TX1-3 Externally applied power on RF outputs(3) 10 dBm
Input and output
voltage range
Dual-voltage LVCMOS inputs, 3.3 V or 1.8 V (Steady State) –0.3V VIOIN + 0.3
V
Dual-voltage LVCMOS inputs, operated at 3.3 V/1.8 V
(Transient Overshoot/Undershoot) or external oscillator input
VIOIN + 20% up to
20% of signal period
CLKP, CLKM Input ports for reference crystal –0.5 2 V
Clamp current
Input or Output Voltages 0.3 V above or below their respective
power rails. Limit clamp current that flows through the internal
diode protection cells of the I/O.
–20 20 mA
TJOperating junction temperature range –40 125 °C
TSTG Storage temperature range after soldered onto PC board –55 150 °C
(1) Stresses beyond those listed under Absolute Maximum Ratings may cause permanent damage to the device. These are stress ratings
only, and functional operation of the device at these or any other conditions beyond those indicated under Recommended Operating
Conditions is not implied. Exposure to absolute-maximum-rated conditions for extended periods may affect device reliability.
(2) All voltage values are with respect to VSS, unless otherwise noted.
(3) This value is for an externally applied signal level on the TX. Additionally, a reflection coefficient up to Gamma = 1 can be applied on
the TX output.
8.2 ESD Ratings
VALUE UNIT
V(ESD) Electrostatic discharge
Human-body model (HBM), per AEC Q100-002(1) ±2000
V
Charged-device model (CDM), per AEC
Q100-011
All other pins ±500
Corner pins ±750
(1) AEC Q100-002 indicates that HBM stressing shall be in accordance with the ANSI/ESDA/JEDEC JS-001 specification.
AWR1243
SWRS188D – MAY 2017 – REVISED DECEMBER 2021 www.ti.com
16 Submit Document Feedback Copyright © 2021 Texas Instruments Incorporated
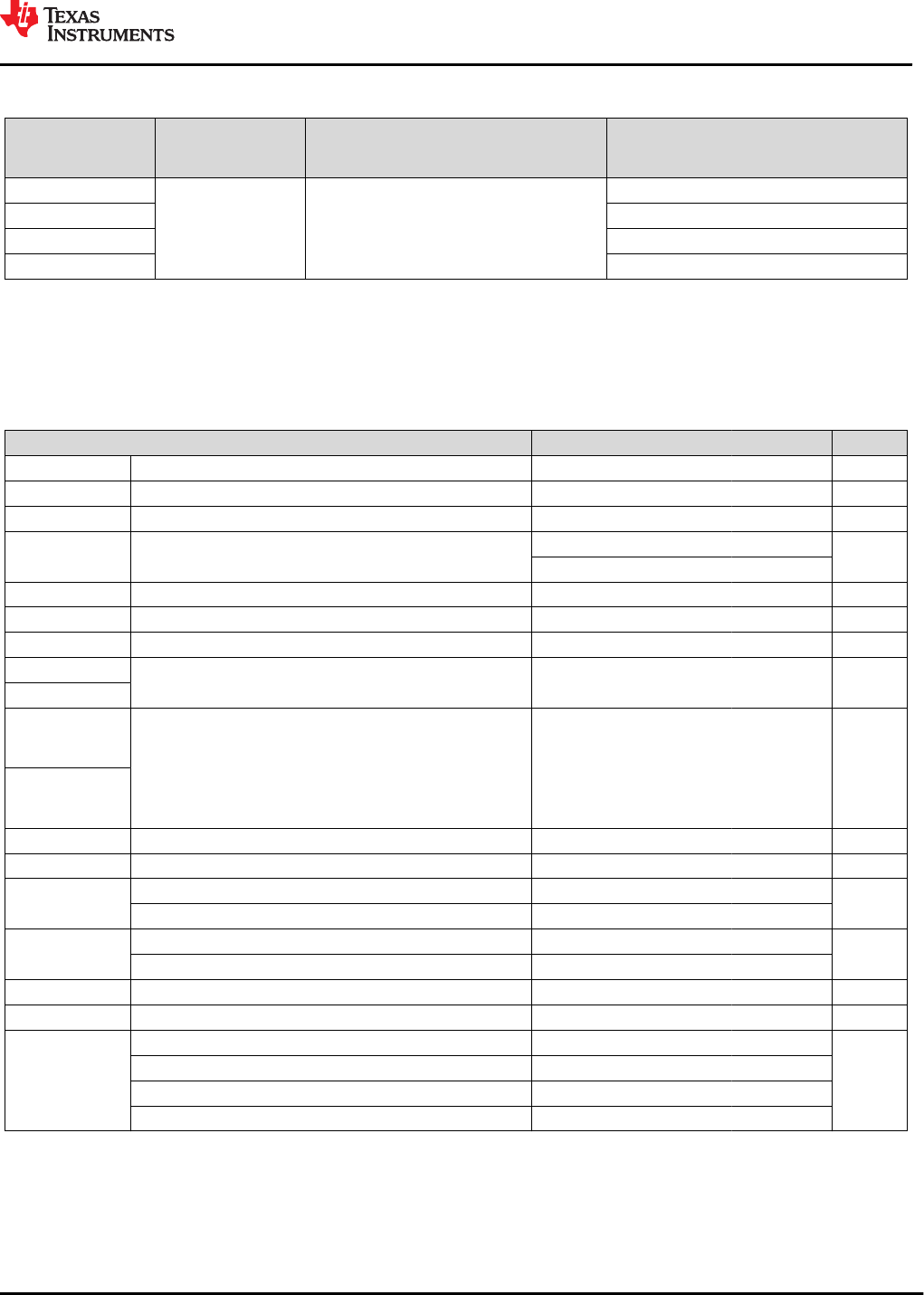
8.3 Power-On Hours (POH)
JUNCTION
TEMPERATURE (Tj)
(1) (2)
OPERATING
CONDITION NOMINAL CVDD VOLTAGE (V) POWER-ON HOURS [POH] (HOURS)
–40°C
100% duty cycle 1.2
600 (6%)
75°C 2000 (20%)
95°C 6500 (65%)
125°C 900 (9%)
(1) This information is provided solely for your convenience and does not extend or modify the warranty provided under TI's standard
terms and conditions for TI semiconductor products.
(2) The specified POH are applicable with max Tx output power settings using the default firmware gain tables. The specified POH would
not be applicable, if the Tx gain table is overwritten using an API.
8.4 Recommended Operating Conditions
over operating free-air temperature range (unless otherwise noted)
MIN NOM MAX UNIT
VDDIN 1.2 V digital power supply 1.14 1.2 1.32 V
VIN_SRAM 1.2 V power rail for internal SRAM 1.14 1.2 1.32 V
VNWA 1.2 V power rail for SRAM array back bias 1.14 1.2 1.32 V
VIOIN I/O supply (3.3 V or 1.8 V):
All CMOS I/Os would operate on this supply.
3.135 3.3 3.465 V
1.71 1.8 1.89
VIOIN_18 1.8 V supply for CMOS IO 1.71 1.8 1.9 V
VIN_18CLK 1.8 V supply for clock module 1.71 1.8 1.9 V
VIOIN_18DIFF 1.8 V supply for CSI2 port 1.71 1.8 1.9 V
VIN_13RF1 1.3 V Analog and RF supply. VIN_13RF1 and VIN_13RF2
could be shorted on the board 1.23 1.3 1.36 V
VIN_13RF2
VIN_13RF1
(1-V Internal LDO
bypass mode) 0.95 1 1.05 V
VIN_13RF2
(1-V Internal LDO
bypass mode)
VIN18BB 1.8-V Analog baseband power supply 1.71 1.8 1.9 V
VIN_18VCO 1.8V RF VCO supply 1.71 1.8 1.9 V
VIH
Voltage Input High (1.8 V mode) 1.17 V
Voltage Input High (3.3 V mode) 2.25
VIL
Voltage Input Low (1.8 V mode) 0.3*VIOIN V
Voltage Input Low (3.3 V mode) 0.62
VOH High-level output threshold (IOH = 6 mA) VIOIN – 450 mV
VOL Low-level output threshold (IOL = 6 mA) 450 mV
NRESET
SOP[2:0]
VIL (1.8V Mode) 0.2
V
VIH (1.8V Mode) 0.96
VIL (3.3V Mode) 0.3
VIH (3.3V Mode) 1.57
www.ti.com
AWR1243
SWRS188D – MAY 2017 – REVISED DECEMBER 2021
Copyright © 2021 Texas Instruments Incorporated Submit Document Feedback 17

8.5 Power Supply Specifications
Table 8-1 describes the four rails from an external power supply block of the AWR1243 device.
Table 8-1. Power Supply Rails Characteristics
SUPPLY DEVICE BLOCKS POWERED FROM THE SUPPLY RELEVANT IOS IN THE DEVICE
1.8 V Synthesizer and APLL VCOs, crystal oscillator, IF
Amplifier stages, ADC, CSI2
Input: VIN_18VCO, VIN18CLK, VIN_18BB,
VIOIN_18DIFF, VIOIN_18IO
LDO Output: VOUT_14SYNTH, VOUT_14APLL
1.3 V (or 1 V in internal
LDO bypass mode)(1)
Power Amplifier, Low Noise Amplifier, Mixers and LO
Distribution
Input: VIN_13RF2, VIN_13RF1
LDO Output: VOUT_PA
3.3 V (or 1.8 V for 1.8 V
I/O mode) Digital I/Os Input VIOIN
1.2 V Core Digital and SRAMs Input: VDDIN, VIN_SRAM
(1) The device only supports simultanoeus operation of 2 transmitters. In the 1-V LDO bypass mode, 1V supply needs to be fed on the
VOUT PA pin.
The 1.3-V (1.0 V) and 1.8-V power supply ripple specifications mentioned in Table 8-2 are defined to meet
a target spur level of –105 dBc (RF Pin = –15 dBm) at the RX. The spur and ripple levels have a dB-to-dB
relationship, for example, a 1-dB increase in supply ripple leads to a ~1 dB increase in spur level. Values quoted
are rms levels for a sinusoidal input applied at the specified frequency.
Table 8-2. Ripple Specifications
FREQUENCY (kHz)
RF RAIL VCO/IF RAIL
1.0 V (INTERNAL LDO BYPASS)
(µVRMS)1.3 V (µVRMS) 1.8 V (µVRMS)
137.5 7 648 83
275 5 76 21
550 3 22 11
1100 2 4 6
2200 11 82 13
4400 13 93 19
6600 22 117 29
AWR1243
SWRS188D – MAY 2017 – REVISED DECEMBER 2021 www.ti.com
18 Submit Document Feedback Copyright © 2021 Texas Instruments Incorporated
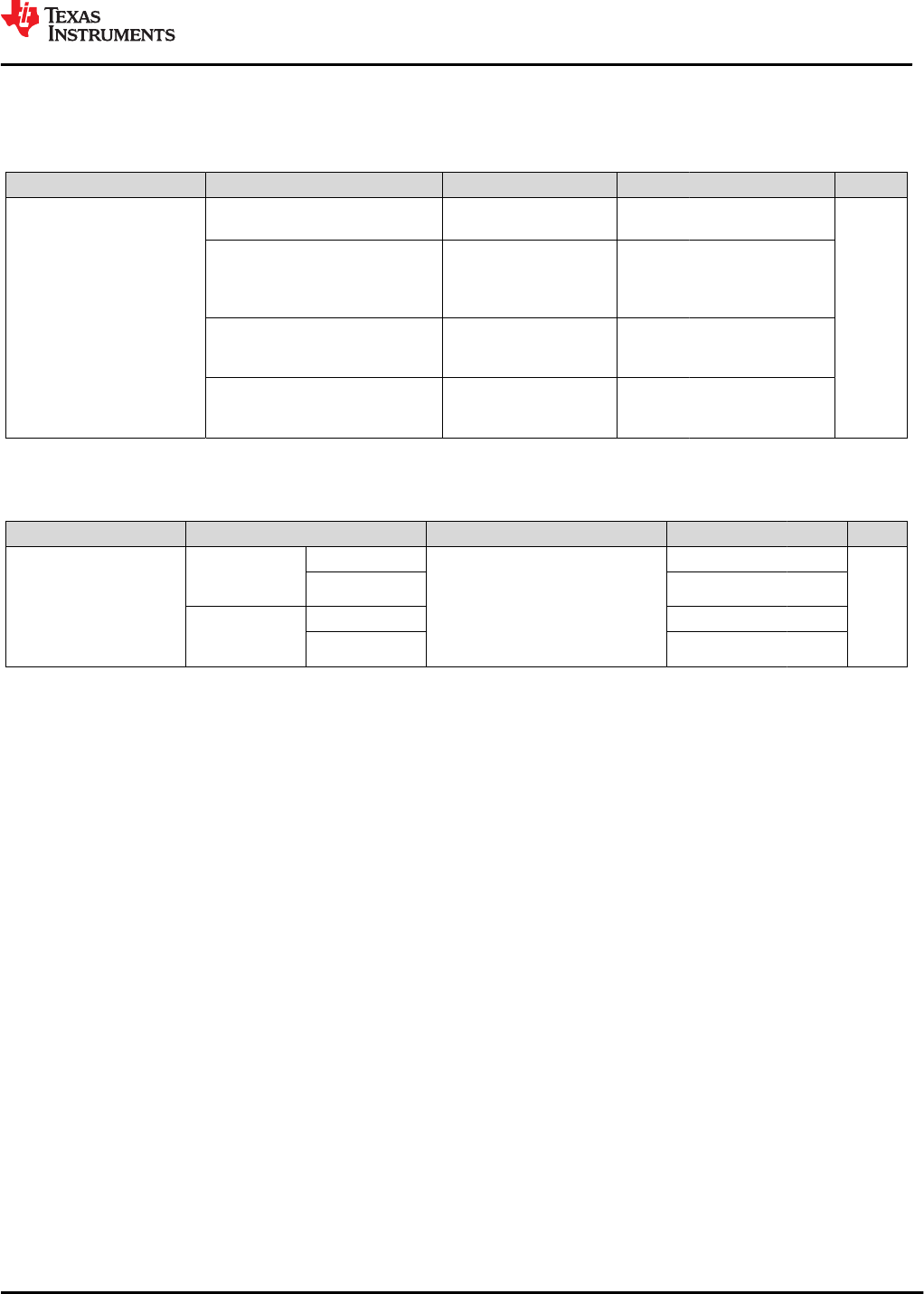
8.6 Power Consumption Summary
Table 8-3 and Table 8-4 summarize the power consumption at the power terminals.
Table 8-3. Maximum Current Ratings at Power Terminals
PARAMETER SUPPLY NAME DESCRIPTION MIN TYP MAX UNIT
Current consumption(1)
VDDIN, VIN_SRAM, VNWA Total current drawn by all
nodes driven by 1.2V rail 500
mA
VIN_13RF1, VIN_13RF2
Total current drawn by all
nodes driven by 1.3V (or
1V in LDO Bypass mode)
rail
2000
VIOIN_18, VIN_18CLK,
VIOIN_18DIFF, VIN_18BB,
VIN_18VCO
Total current drawn by all
nodes driven by 1.8V rail 850
VIOIN
Total current drawn by
all nodes driven by 3.3V
rail(2)
50
(1) The specified current values are at typical supply voltage level.
(2) The exact VIOIN current depends on the peripherals used and their frequency of operation.
Table 8-4. Average Power Consumption at Power Terminals
PARAMETER CONDITION DESCRIPTION MIN TYP MAX UNIT
Average power
consumption
1.0-V internal
LDO bypass
mode
1TX, 4RX Sampling: 16.66 MSps complex
Transceiver, 40-ms frame time, 512
chirps, 512 samples/chirp, 8.5-μs
interchirp time (50% duty cycle)
Data Port: MIPI-CSI-2
1.62
W
2TX, 4RX 1.79
1.3-V internal
LDO enabled
mode
1TX, 4RX 1.80
2TX, 4RX 2.01
www.ti.com
AWR1243
SWRS188D – MAY 2017 – REVISED DECEMBER 2021
Copyright © 2021 Texas Instruments Incorporated Submit Document Feedback 19
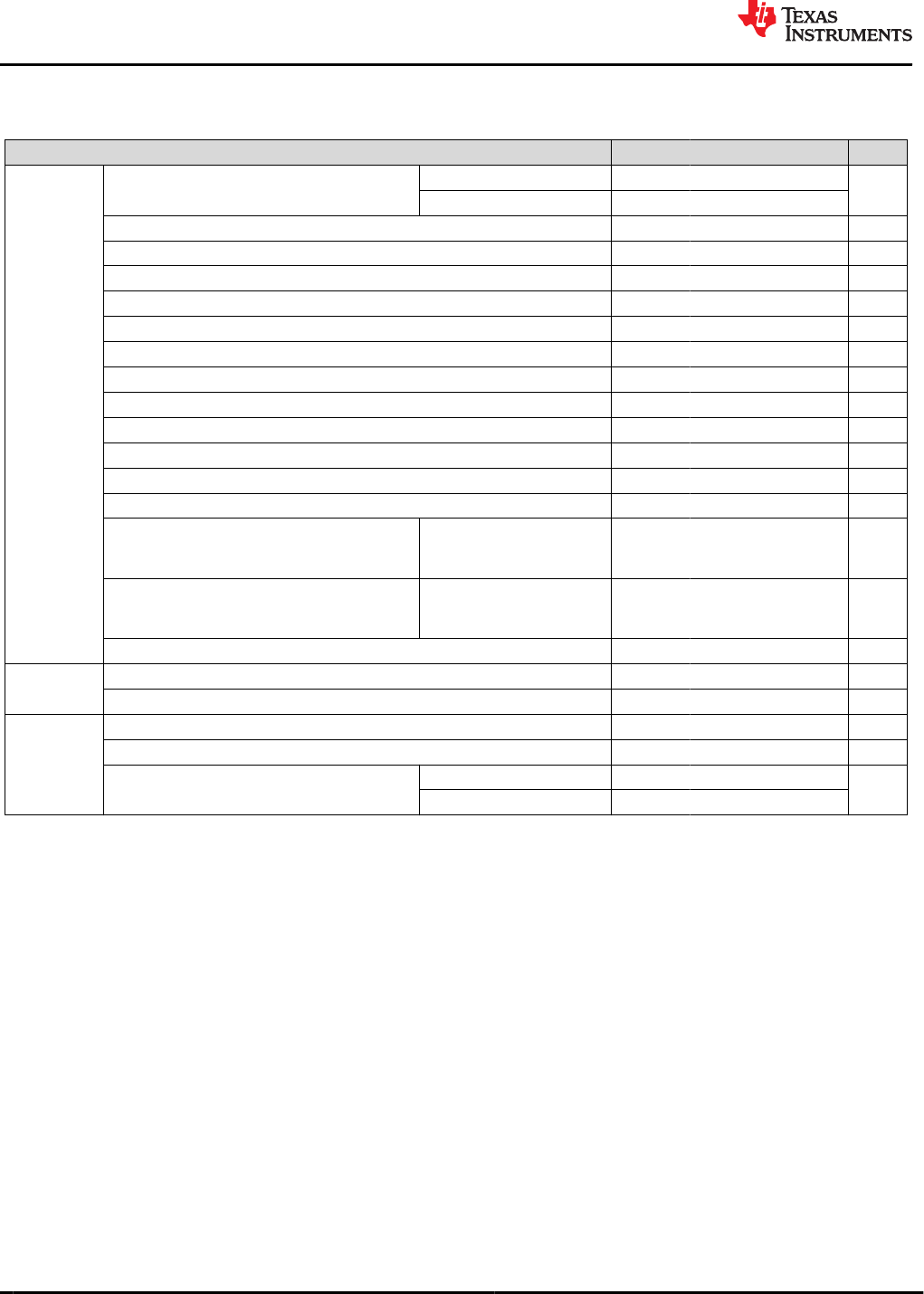
8.7 RF Specification
over recommended operating conditions and with run time calibrations enabled (unless otherwise noted)
PARAMETER MIN TYP MAX UNIT
Receiver
Noise figure 76 to 77 GHz (VCO1) 14 dB
77 to 81 GHz (VCO2) 15
1-dB compression point (Out Of Band)(1) –8 dBm
Maximum gain 48 dB
Gain range 24 dB
Gain step size 2 dB
Image Rejection Ratio (IMRR) 30 dB
IF bandwidth(2) 15 MHz
ADC sampling rate (real/complex 2x) 37.5 Msps
ADC sampling rate (complex 1x) 18.75 Msps
ADC resolution 12 Bits
Return loss (S11) <–10 dB
Gain mismatch variation (over temperature) ±0.5 dB
Phase mismatch variation (over temperature) ±3 °
In-band IIP2
RX gain = 30dB
IF = 1.5, 2 MHz at
–12 dBFS
16 dBm
Out-of-band IIP2
RX gain = 24dB
IF = 10 kHz at -10dBm,
1.9 MHz at -30 dBm
24 dBm
Idle Channel Spurs –90 dBFS
Transmitter Output power 12 dBm
Amplitude noise –145 dBc/Hz
Clock
subsystem
Frequency range 76 81 GHz
Ramp rate 100 MHz/µs
Phase noise at 1-MHz offset 76 to 77 GHz (VCO1) –95 dBc/Hz
77 to 81 GHz (VCO2) –93
(1) 1-dB Compression Point (Out Of Band) is measured by feed a Continuous wave Tone (10 kHz) well below the lowest HPF cut-off
frequency.
(2) The analog IF stages include high-pass filtering, with two independently configurable first-order high-pass corner frequencies. The set
of available HPF corners is summarized as follows:
Available HPF Corner Frequencies (kHz)
HPF1 HPF2
175, 235, 350, 700 350, 700, 1400, 2800
The filtering performed by the digital baseband chain is targeted to provide:
• Less than ±0.5 dB pass-band ripple/droop, and
• Better than 60 dB anti-aliasing attenuation for any frequency that can alias back into the pass-band.
Figure 8-1 shows variations of noise figure and in-band P1dB parameters with respect to receiver gain
programmed.
AWR1243
SWRS188D – MAY 2017 – REVISED DECEMBER 2021 www.ti.com
20 Submit Document Feedback Copyright © 2021 Texas Instruments Incorporated
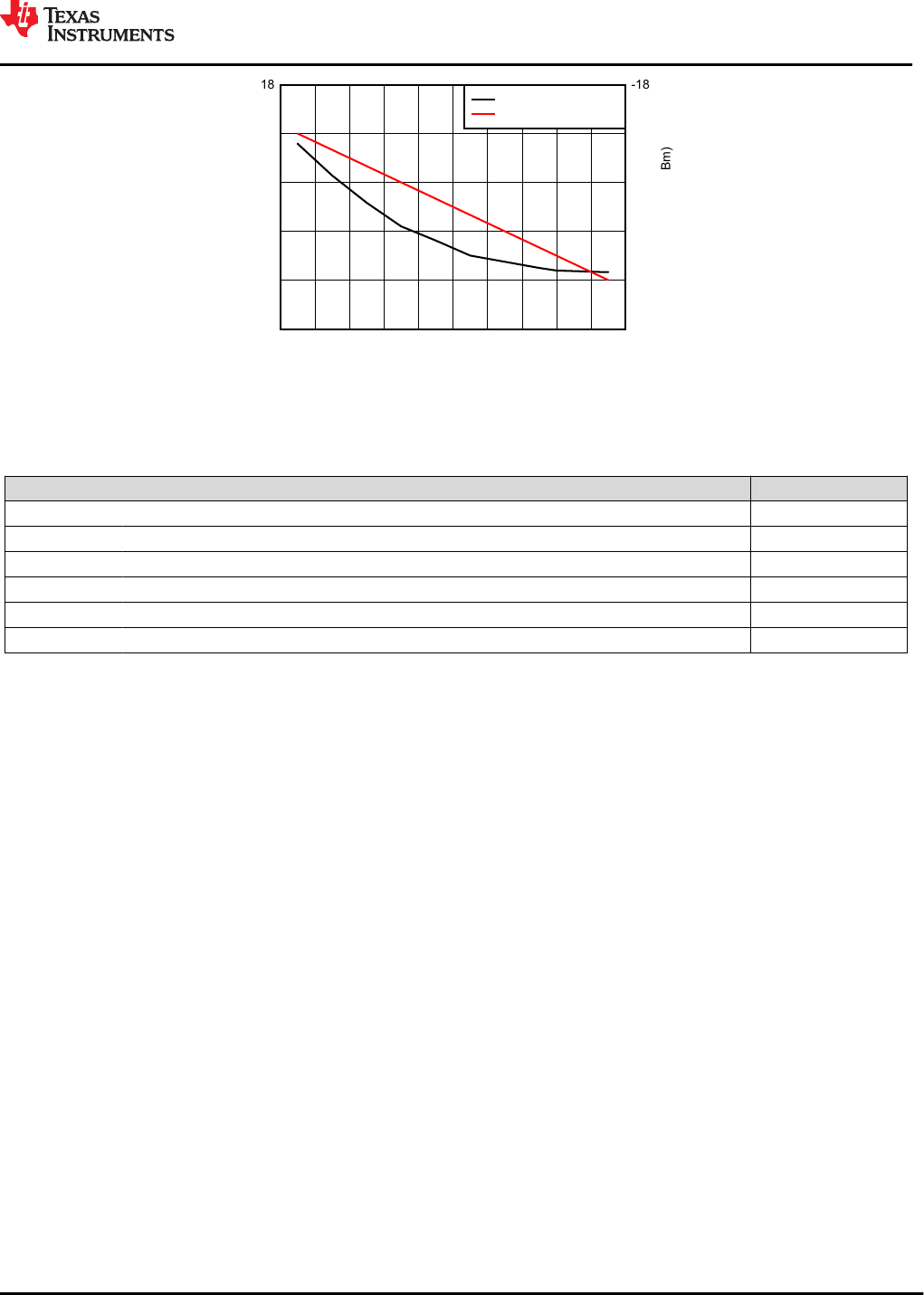
RX Gain (dB)
NF (dB)
In-band P1DB (dBm)
8 -48
10 -42
12 -36
14 -30
16 -24
18 -18
30 32 34 36 38 40 42 44 46 48
NF (dB)
In-band P1DB (dBm)
Figure 8-1. Noise Figure, In-band P1dB vs Receiver Gain
8.8 Thermal Resistance Characteristics for FCBGA Package [ABL0161]
THERMAL METRICS(1) °C/W(2) (3)
RΘJC Junction-to-case 5
RΘJB Junction-to-board 5.9
RΘJA Junction-to-free air 21.6
RΘJMA Junction-to-moving air 15.3 (4)
PsiJT Junction-to-package top 0.69
PsiJB Junction-to-board 5.8
(1) For more information about traditional and new thermal metrics, see Semiconductor and IC Package Thermal Metrics.
(2) °C/W = degrees Celsius per watt.
(3) These values are based on a JEDEC-defined 2S2P system (with the exception of the Theta JC [RΘJC] value, which is based on
a JEDEC-defined 1S0P system) and will change based on environment as well as application. For more information, see these
EIA/JEDEC standards:
• JESD51-2, Integrated Circuits Thermal Test Method Environmental Conditions - Natural Convection (Still Air)
• JESD51-3, Low Effective Thermal Conductivity Test Board for Leaded Surface Mount Packages
• JESD51-7, High Effective Thermal Conductivity Test Board for Leaded Surface Mount Packages
• JESD51-9, Test Boards for Area Array Surface Mount Package Thermal Measurements
(4) Air flow = 1 m/s
8.9 Timing and Switching Characteristics
8.9.1 Power Supply Sequencing and Reset Timing
The AWR1243 device expects all external voltage rails and SOP lines to be stable before reset is deasserted.
Figure 8-2 describes the device wake-up sequence.
www.ti.com
AWR1243
SWRS188D – MAY 2017 – REVISED DECEMBER 2021
Copyright © 2021 Texas Instruments Incorporated Submit Document Feedback 21

VDDIN,
VIN_SRAM
VNWA
WARMRESET
OUTPUT
VIOIN_18
VIN18_CLK
VIOIN_18DIFF
VIN18_BB
VIN_13RF1
VIN_13RF2
VIOIN
nRESET
SOP[2.1.0]
VBGAP
OUTPUT
CLKP, CLKM
Using Crystal
MCUCLK
OUTPUT (1)
QSPI_CS
OUTPUT
DC power
Stable before
nRESET
release
SOP
Setup
Time
SOP
Hold time to
nRESET
DC
Power
OK
MSS
BOOT
START
QSPI
READ
nRESET
ASSERT
tPGDEL
DC
Power
notOK
Warm reset
delay for crystal
or ext osc
7ms (XTAL Mode)
500 µs (REFCLK Mode)
Figure 8-2. Device Wake-up Sequence
8.9.2 Synchronized Frame Triggering
The AWR1243 device supports a hardware based mechanism to trigger radar frames. An external host can
pulse the SYNC_IN signal to start radar frames. The typical time difference between the rising edge of
the external pulse and the frame transmission on air (Tlag) is about 160 ns. There is also an additional
programmable delay that the user can set to control the frame start time.
The periodicity of the external SYNC_IN pulse should be always greater than the programmed frame periodic in
the frame configurations in all instances.
AWR1243
SWRS188D – MAY 2017 – REVISED DECEMBER 2021 www.ti.com
22 Submit Document Feedback Copyright © 2021 Texas Instruments Incorporated

SYNC_IN
(Hardware
Trigger)
Radar
Frames
Tlag
Frame-1 Frame-2
Tactive_frame
Tpulse
Figure 8-3. Sync In Hardware Trigger
Table 8-5. Frame Trigger Timing
PARAMETER DESCRIPTION MIN MAX UNIT
Tactive_frame Active frame duration User defined ns
Tpulse 25 4000
www.ti.com
AWR1243
SWRS188D – MAY 2017 – REVISED DECEMBER 2021
Copyright © 2021 Texas Instruments Incorporated Submit Document Feedback 23

8.9.3 Input Clocks and Oscillators
8.9.3.1 Clock Specifications
An external crystal is connected to the device pins. Figure 8-4 shows the crystal implementation.
40 MHz
CLKP
CLKM
Cf1
Cf2
Cp
Figure 8-4. Crystal Implementation
Note
The load capacitors, Cf1 and Cf2 in Figure 8-4, should be chosen such that Equation 1 is satisfied.
CL in the equation is the load specified by the crystal manufacturer. All discrete components used
to implement the oscillator circuit should be placed as close as possible to the associated oscillator
CLKP and CLKM pins.Note that Cf1 and Cf2 include the parasitic capacitances due to PCB routing.
f 2
L f1 P
f1 f 2
C
C C C
C C
= ´ +
+
(1)
Table 8-6 lists the electrical characteristics of the clock crystal.
Table 8-6. Crystal Electrical Characteristics (Oscillator Mode)
NAME DESCRIPTION MIN TYP MAX UNIT
fPParallel resonance crystal frequency 40 MHz
CLCrystal load capacitance 5 8 12 pF
ESR Crystal ESR 50 Ω
Temperature range Expected temperature range of operation –40 125 °C
Frequency
tolerance Crystal frequency tolerance(1) (2) –200 200 ppm
Drive level 50 200 µW
(1) The crystal manufacturer's specification must satisfy this requirement.
(2) Includes initial tolerance of the crystal, drift over temperature, aging and frequency pulling due to incorrect load capacitance.
In the case where an external clock is used as the clock resource, the signal is fed to the CLKP pin only; CLKM
is grounded. The phase noise requirement is very important when a 40-MHz clock is fed externally. Table 8-7
lists the electrical characteristics of the external clock signal.
AWR1243
SWRS188D – MAY 2017 – REVISED DECEMBER 2021 www.ti.com
24 Submit Document Feedback Copyright © 2021 Texas Instruments Incorporated
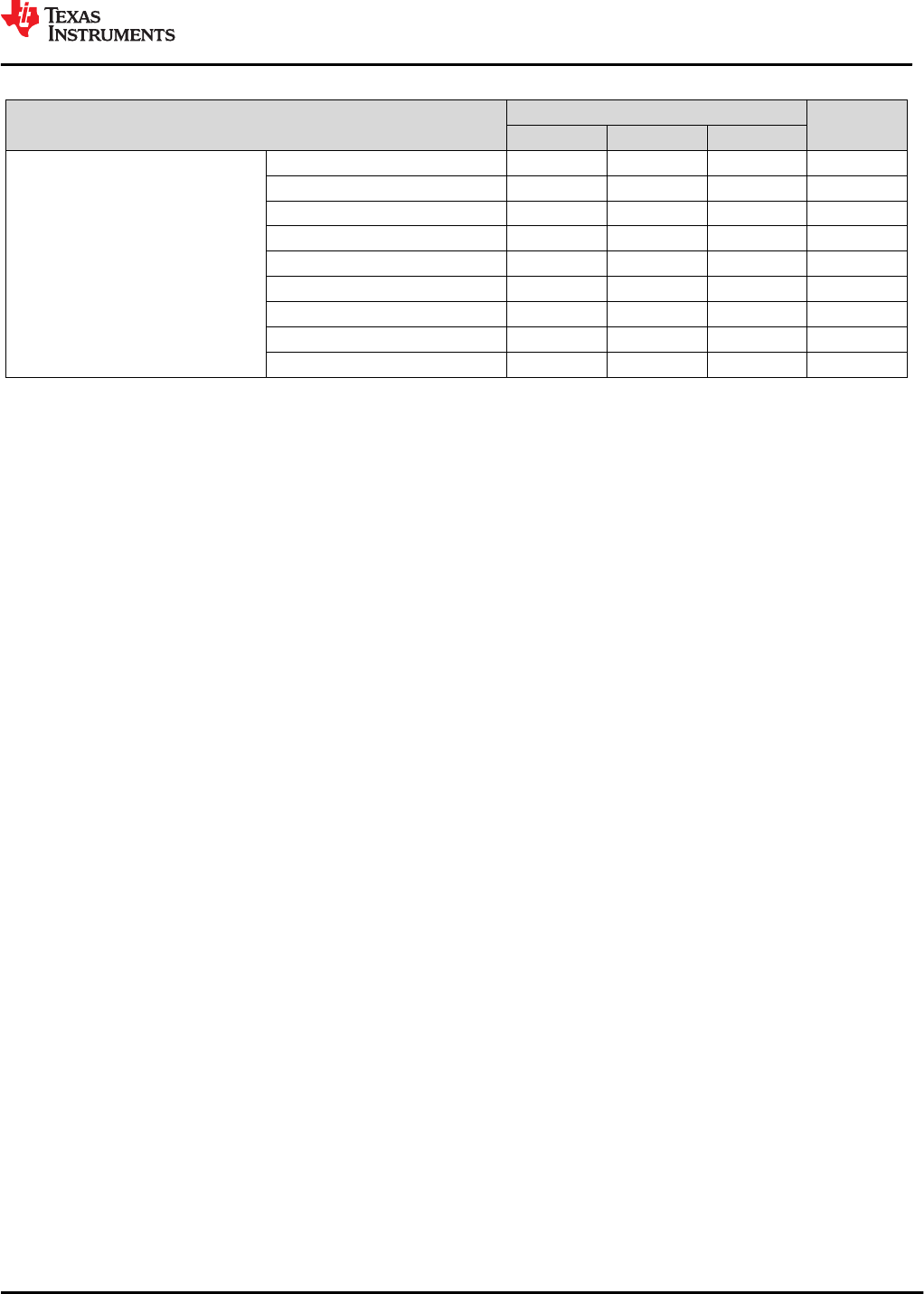
Table 8-7. External Clock Mode Specifications
PARAMETER SPECIFICATION UNIT
MIN TYP MAX
Input Clock:
External AC-coupled sine wave or DC-
coupled square wave
Phase Noise referred to 40 MHz
Frequency 40 MHz
AC-Amplitude 700 1200 mV (pp)
DC-trise/fall 10 ns
Phase Noise at 1 kHz –132 dBc/Hz
Phase Noise at 10 kHz –143 dBc/Hz
Phase Noise at 100 kHz –152 dBc/Hz
Phase Noise at 1 MHz –153 dBc/Hz
Duty Cycle 35 65 %
Freq Tolerance –100 100 ppm
www.ti.com
AWR1243
SWRS188D – MAY 2017 – REVISED DECEMBER 2021
Copyright © 2021 Texas Instruments Incorporated Submit Document Feedback 25
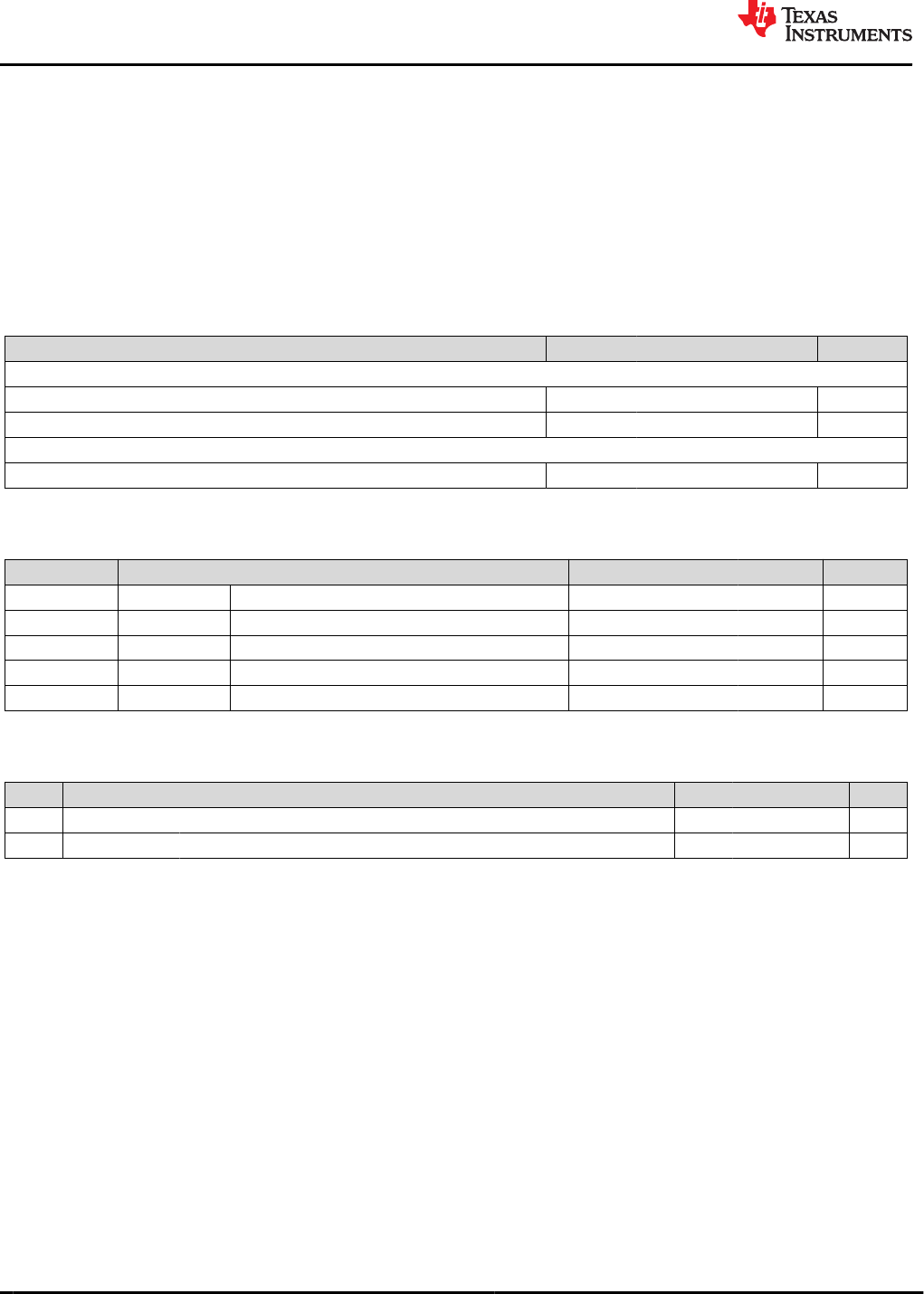
8.9.4 Multibuffered / Standard Serial Peripheral Interface (MibSPI)
8.9.4.1 Peripheral Description
The SPI uses a MibSPI Protocol by TI.
The MibSPI/SPI is a high-speed synchronous serial input/output port that allows a serial bit stream to be shifted
into and out of the device at a programmed bit-transfer rate. The MibSPI/SPI is normally used for communication
between the microcontroller and external peripherals or another microcontroller.
Section 8.9.4.1.2 and Section 8.9.4.1.3 assume the operating conditions stated in Section 8.9.4.1.1. Section
8.9.4.1.2, Section 8.9.4.1.3, and Figure 8-5 describe the timing and switching characteristics of the MibSPI.
8.9.4.1.1 SPI Timing Conditions
MIN TYP MAX UNIT
Input Conditions
tRInput rise time 1 3 ns
tFInput fall time 1 3 ns
Output Conditions
CLOAD Output load capacitance 2 15 pF
8.9.4.1.2 SPI Peripheral Mode Switching Parameters (SPICLK = input, SPISIMO = input,
and SPISOMI = output)
NO. PARAMETER MIN TYP MAX UNIT
1 tc(SPC)S Cycle time, SPICLK 25 ns
2 tw(SPCH)S Pulse duration, SPICLK high 10 ns
3 tw(SPCL)S Pulse duration, SPICLK low 10 ns
4 td(SPCL-SOMI)S Delay time, SPISOMI valid after SPICLK low 10 ns
5 th(SPCL-SOMI)S Hold time, SPISOMI data valid after SPICLK low 2 ns
8.9.4.1.3 SPI Peripheral Mode Timing Requirements (SPICLK = input, SPISIMO = input,
and SPISOMI = output)
NO. MIN TYP MAX UNIT
6 tsu(SIMO-SPCH)S Setup time, SPISIMO before SPICLK high 3 ns
7 th(SPCH-SIMO)S Hold time, SPISIMO data valid after SPICLK high 1 ns
AWR1243
SWRS188D – MAY 2017 – REVISED DECEMBER 2021 www.ti.com
26 Submit Document Feedback Copyright © 2021 Texas Instruments Incorporated

Figure 8-5. SPI Peripheral Mode External Timing
www.ti.com
AWR1243
SWRS188D – MAY 2017 – REVISED DECEMBER 2021
Copyright © 2021 Texas Instruments Incorporated Submit Document Feedback 27

8.9.4.2 Typical Interface Protocol Diagram (Peripheral Mode)
1. Host should ensure that there is a delay of at least two SPI clocks between CS going low and start of SPI
clock.
2. Host should ensure that CS is toggled for every 16 bits of transfer through SPI.
Figure 8-6 shows the SPI communication timing of the typical interface protocol.
Figure 8-6. SPI Communication
AWR1243
SWRS188D – MAY 2017 – REVISED DECEMBER 2021 www.ti.com
28 Submit Document Feedback Copyright © 2021 Texas Instruments Incorporated
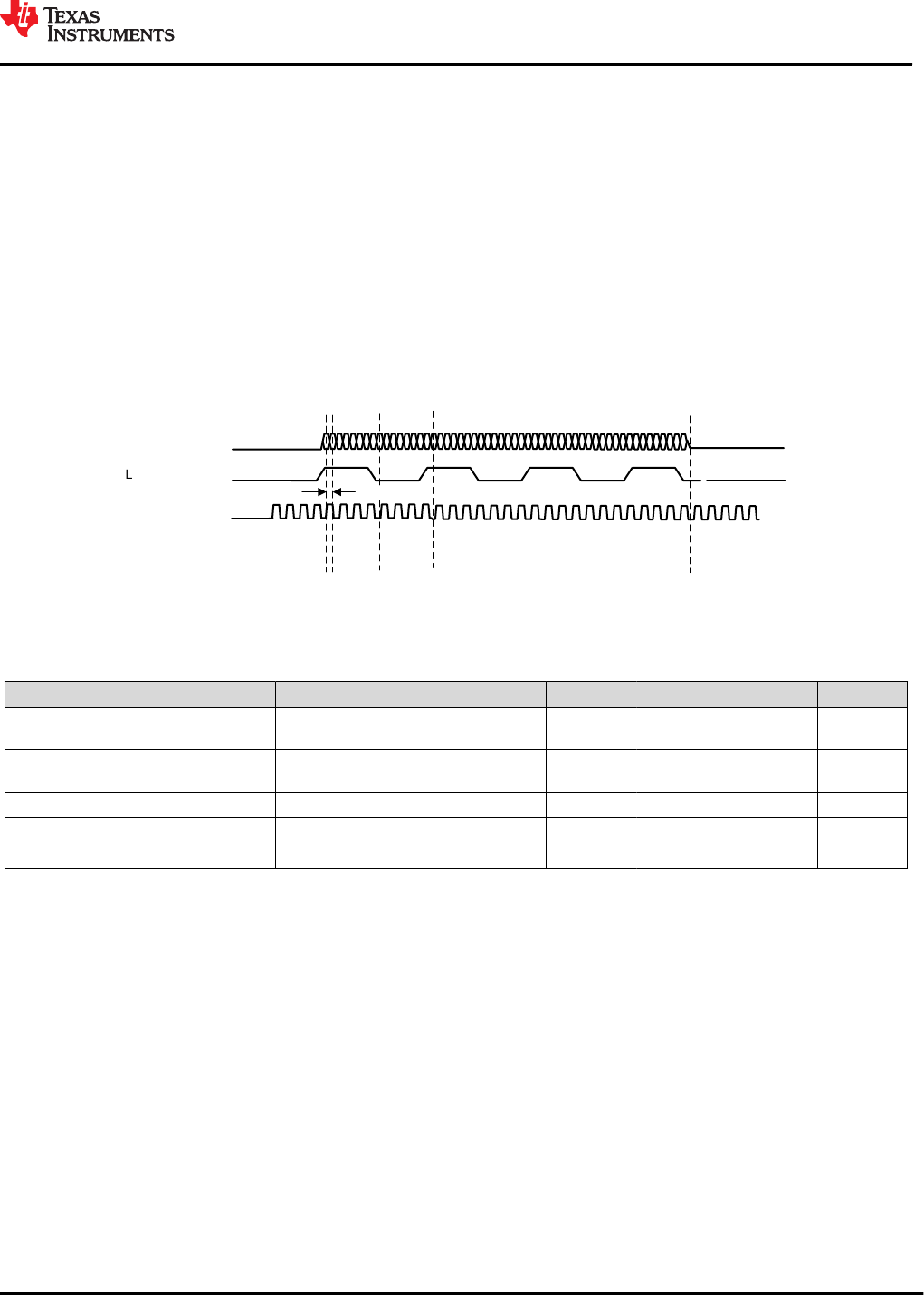
8.9.5 LVDS Interface Configuration
The AWR1243 supports seven differential LVDS IOs/Lanes to support debug where raw ADC data could
be extracted. The lane configuration supported is four Data lanes (LVDS_TXP/M), one Bit Clock lane
(LVDS_CLKP/M) one Frame clock lane (LVDS_FRCLKP/M). The LVDS interface supports the following data
rates:
• 900 Mbps (450 MHz DDR Clock)
• 600 Mbps (300 MHz DDR Clock)
• 450 Mbps (225 MHz DDR Clock)
• 400 Mbps (200 MHz DDR Clock)
• 300 Mbps (150 MHz DDR Clock)
• 225 Mbps (112.5 MHz DDR Clock)
• 150 Mbps (75 MHz DDR Clock)
Note that the bit clock is in DDR format and hence the numbers of toggles in the clock is equivalent to data.
LVDS_FRCLKP/M
LVDS_TXP/M
LVDS_CLKP/M
Data bitwidth
Figure 8-7. LVDS Interface Lane Configuration And Relative Timings
8.9.5.1 LVDS Interface Timings
Table 8-8. LVDS Electrical Characteristics
PARAMETER TEST CONDITIONS MIN TYP MAX UNIT
Duty Cycle Requirements max 1 pF lumped capacitive load on
LVDS lanes
48% 52%
Output Differential Voltage peak-to-peak single-ended with 100 Ω
resistive load between differential pairs 250 450 mV
Output Offset Voltage 1125 1275 mV
Trise and Tfall 20%-80%, 900 Mbps 330 ps
Jitter (pk-pk) 900 Mbps 80 ps
www.ti.com
AWR1243
SWRS188D – MAY 2017 – REVISED DECEMBER 2021
Copyright © 2021 Texas Instruments Incorporated Submit Document Feedback 29

Trise
LVDS_CLK
LVDS_TXP/M
LVDS_FRCLKP/M
1100 ps
Clock Jitter = 6sigma
Figure 8-8. Timing Parameters
8.9.6 General-Purpose Input/Output
Section 8.9.6.1 lists the switching characteristics of output timing relative to load capacitance.
8.9.6.1 Switching Characteristics for Output Timing versus Load Capacitance (CL)
PARAMETER(1) TEST CONDITIONS VIOIN = 1.8V VIOIN = 3.3V UNIT
trMax rise time
CL = 20 pF 2.8 3.0
nsCL = 50 pF 6.4 6.9
CL = 75 pF 9.4 10.2
tfMax fall time
CL = 20 pF 2.8 2.8
nsCL = 50 pF 6.4 6.6
CL = 75 pF 9.4 9.8
(1) The rise/fall time is measured as the time taken by the signal to transition from 10% and 90% of VIOIN voltage.
AWR1243
SWRS188D – MAY 2017 – REVISED DECEMBER 2021 www.ti.com
30 Submit Document Feedback Copyright © 2021 Texas Instruments Incorporated
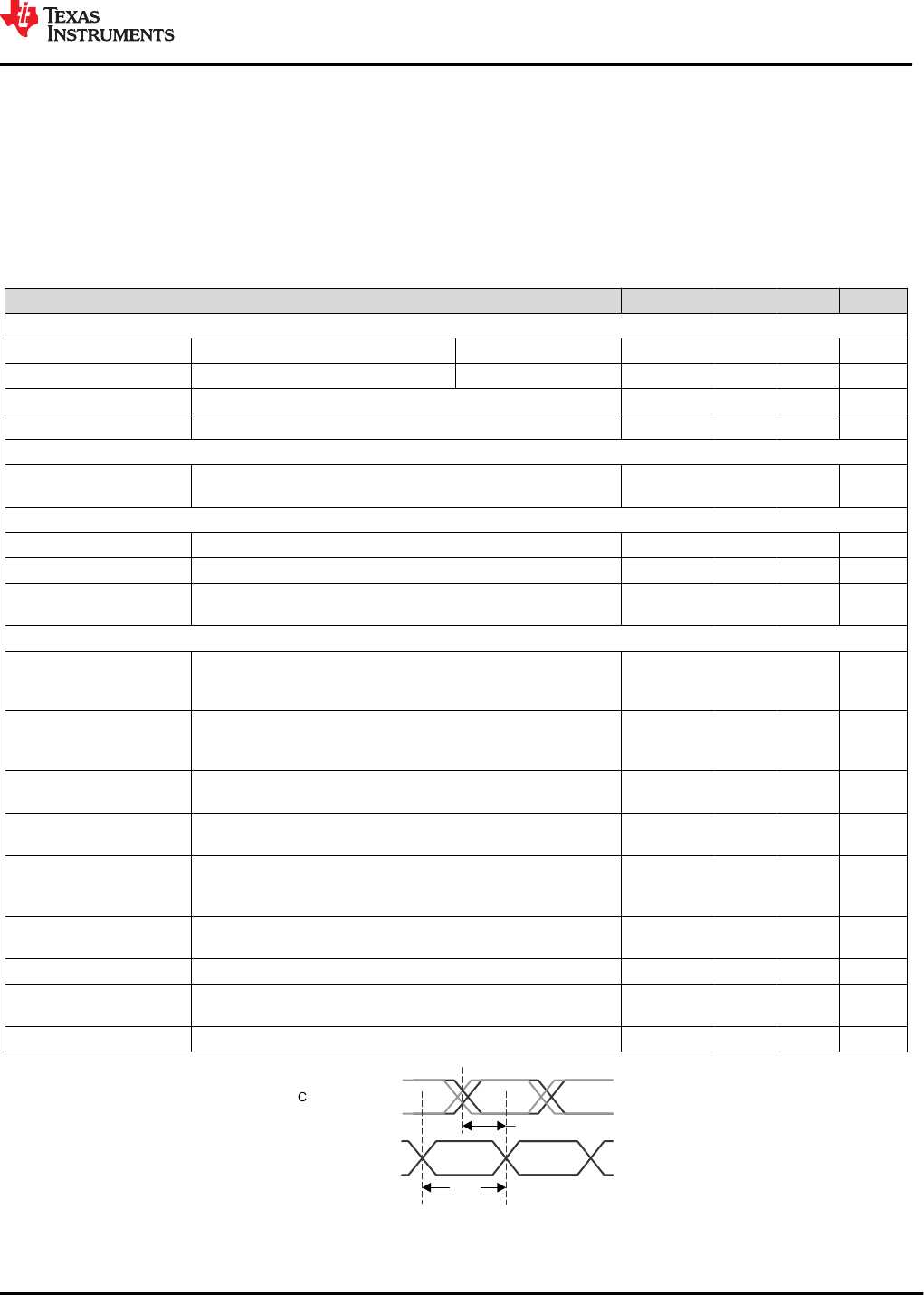
8.9.7 Camera Serial Interface (CSI)
The CSI is a MIPI D-PHY compliant interface for connecting this device to a camera receiver module. This
interface is made of four differential lanes; each lane is configurable for carrying data or clock. The polarity of
each wire of a lane is also configurable. Section 8.9.7.1, Figure 8-9, Figure 8-10, and Figure 8-11 describe the
clock and data timing of the CSI.The clock is always ON once the CSI IP is enabled. Hence it remains in HS
mode.
8.9.7.1 CSI Switching Characteristics
over operating free-air temperature range (unless otherwise noted)
PARAMETER MIN TYP MAX UNIT
HPTX
HSTXDBR Data bit rate (1/2/4 data lane PHY) 150 600 Mbps
fCLK DDR clock frequency (1/2/4 data lane PHY) 75 300 MHz
ΔVCMTX(LF) Common-level variation –50 50 mV
tR and tF20% to 80% rise time and fall time 0.3 UI
LPTX DRIVER
tEOT Time from start of THS-TRAIL period to start of LP-11 state 105 +
12*UI
ns
DATA-CLOCK Timing Specification
UINOM Nominal Unit Interval 1.67 13.33 ns
UIINST,MIN Minimum instantaneous Unit Interval 1.131 ns
TSKEW[TX] Data to clock skew measured at transmitter –0.15 0.15 UIINST,
MIN
CSI2 TIMING SPECIFICATION
TCLK-PRE Time that the HS clock shall be driven by the transmitter before
any associated data lane beginning the transition from LP to HS
mode.
8 ns
TCLK-PREPARE Time that the transmitter drives the clock lane LP-00 line
state immediately before the HS-0 line state starting the HS
transmission.
38 95 ns
TCLK-PREPARE + TCLK-ZERO TCLK-PREPARE + time that the transmitter drives the HS-0 state
before starting the clock.
300 ns
TEOT Transmitted time interval from the start of THS-TRAIL or TCLKTRAIL,
to the start of the LP-11 state following a HS burst.
105 ns
+ 12*UI
ns
THS-PREPARE Time that the transmitter drives the data lane LP-00 line
state immediately before the HS-0 line state starting the HS
transmission
40 + 4*UI 85 +
6*UI
ns
THS-PREPARE + THS-ZERO THS-PREPARE + time that the transmitter drives the HS-0 state prior
to transmitting the Sync sequence.
145 ns +
10*UI
ns
THS-EXIT Time that the transmitter drives LP-11 following a HS burst. 100 ns
THS-TRAIL Time that the transmitter drives the flipped differential state after
last payload data bit of a HS transmission burst
max(8*UI, 60
ns + 4*UI)
ns
TLPX TXXXransmitted length of any low-power state period 50 ns
CSI2_CLK(P/M)
CSI2_TX(P/M)
1 UI
0.5UI + Tskew
Figure 8-9. Clock and Data Timing in HS Transmission
www.ti.com
AWR1243
SWRS188D – MAY 2017 – REVISED DECEMBER 2021
Copyright © 2021 Texas Instruments Incorporated Submit Document Feedback 31
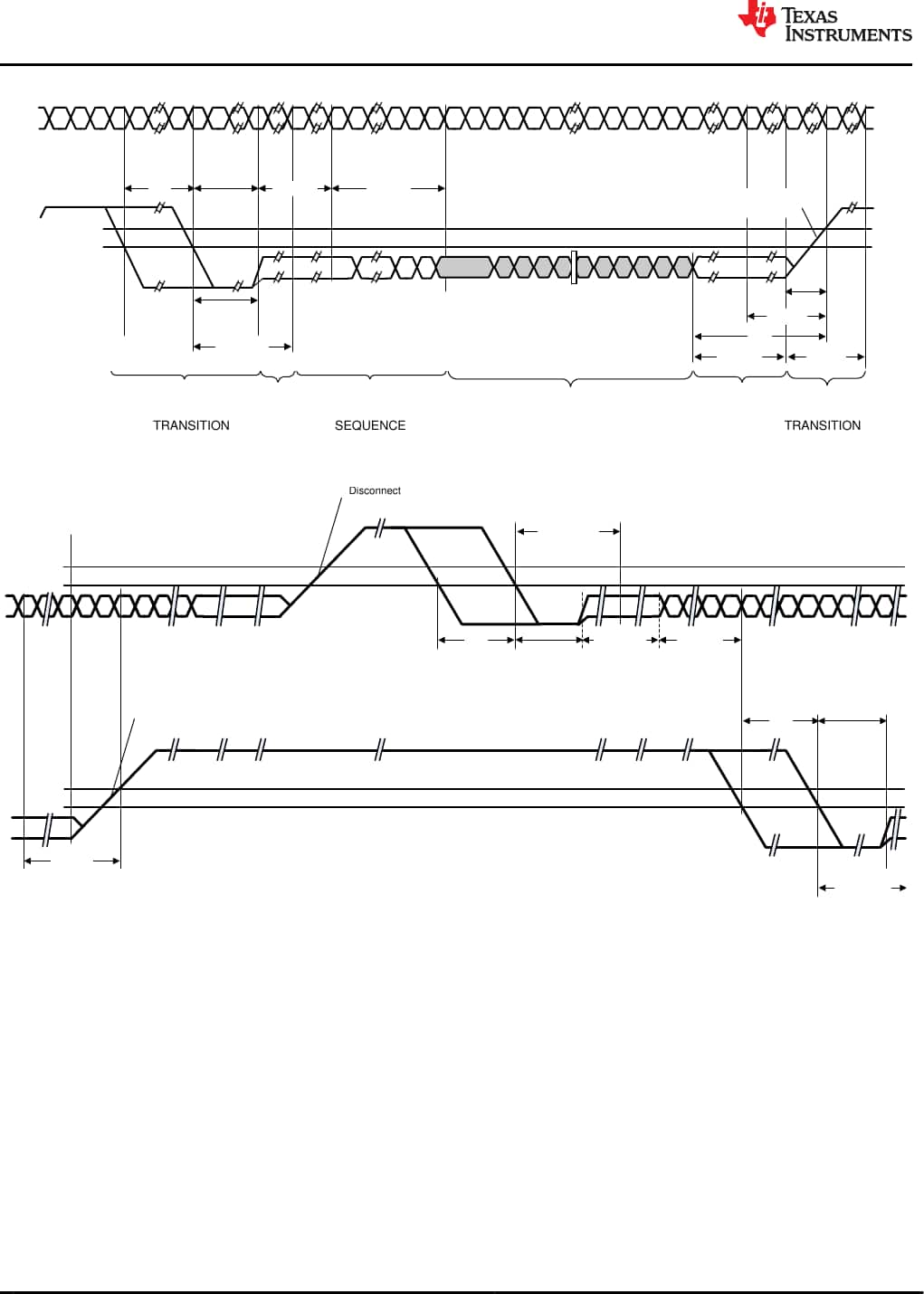
TLPX
THS-SETTLE THS-TRAIL THS-EXIT
TEOT
THS-SKIP
THS-ZERO THS-SYNC
VIH(min)
VIL(max)
Clock
Lane
Data Lane
Dp/Dn
Disconnect
Terminator
LP-11 LP-01 LP-00
LP-11
Capture
1st Data Bit
THS-PREPARE
TD-TERM-EN
TREOT
LOW-POWER TO
HIGH-SPEED
TRANSITION
HS-ZERO
START OF
TRANSMISSION
SEQUENCE
HIGH-SPEED DATA
TRANSMISSION HS-TRAIL
HIGH-SPEED TO
LOW-POWER
TRANSITION
VOH
VOL
Figure 8-10. High-Speed Data Transmission Burst
Clock Lane
Dp/Dn
VIH(min)
VIL(max)
THS-SKIP
Data Lane
Dp/Dn
TCLK-SETTLE
TLPX TCLK-ZERO TCLK-PRE
THS-SETTLE
TLPX
VIH(min)
VIL(max)
Disconnect
Terminator
Disconnect
Terminator
TCLK-PREPARE
THS-PREPARE
A. The HS to LP transition of the CLK does not actually take place since the CLK is always ON in HS mode.
Figure 8-11. Switching the Clock Lane Between Clock Transmission and Low-Power Mode
AWR1243
SWRS188D – MAY 2017 – REVISED DECEMBER 2021 www.ti.com
32 Submit Document Feedback Copyright © 2021 Texas Instruments Incorporated

9 Detailed Description
9.1 Overview
The AWR1243 device is a single-chip highly integrated 77-GHz transceiver and front end that includes three
transmit and four receive chains. The device can be used in long-range automotive radar applications such
as automatic emergency braking and automatic adaptive cruise control. The AWR1243 has extremely small
form factor and provides ultra-high resolution with very low power consumption. This device, when used with
the TDA3X or TD2X, offers higher levels of performance and flexibility through a programmable digital signal
processor (DSP); thus addressing the standard short-, mid-, and long-range automotive radar applications.
9.2 Functional Block Diagram
ADC Buffer
16KB PING/PONG
IF ADC
Digital Front-end
(Decimation filter
chain)
LNA
IF ADC
LNA
IF ADC
LNA
IF ADC
LNA
PA û-
PA û-
PA û-
Synth
(20 GHz) Ramp Generator
x4
Osc.
RF Control / BIST
GPADCVMON Temp(B)
SPI/I2C
CSI2
RF/Analog Subsystem
Host control
interface
ADC output
interface
Digital
Synth Cycle
Counter
Phase
Shifter
Control (A)
A. Phase Shift Control:
• 0° / 180° BPM for AWR1243
B. Internal temperature sensor accuracy is ± 7 °C.
Figure 9-1. Functional Block Diagram
www.ti.com
AWR1243
SWRS188D – MAY 2017 – REVISED DECEMBER 2021
Copyright © 2021 Texas Instruments Incorporated Submit Document Feedback 33
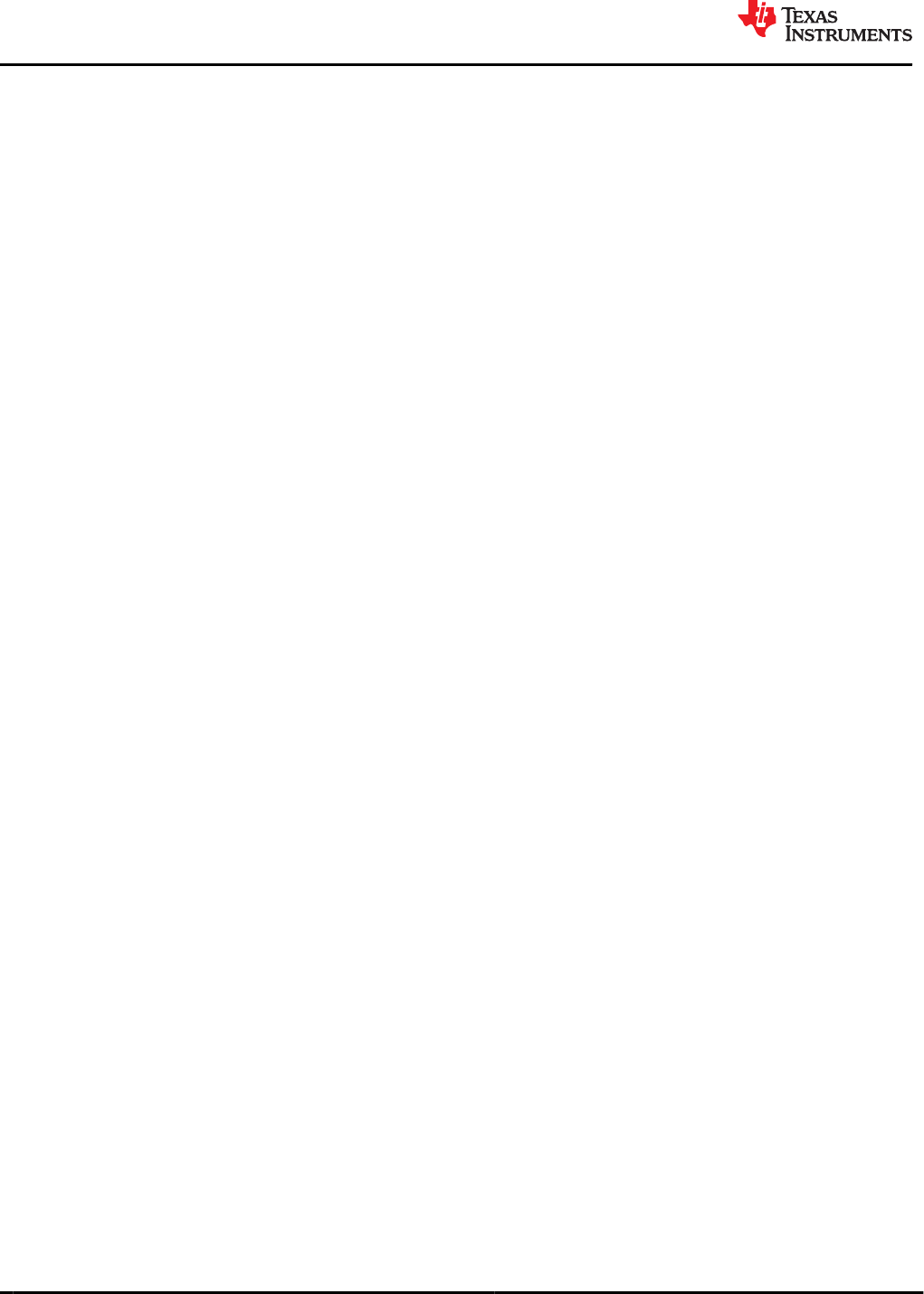
9.3 Subsystems
9.3.1 RF and Analog Subsystem
The RF and analog subsystem includes the RF and analog circuitry – namely, the synthesizer, PA, LNA, mixer,
IF, and ADC. This subsystem also includes the crystal oscillator and temperature sensors. The three transmit
channels can be operated simultaneously for transmit beamforming purpose as required; whereas the four
receive channels can all be operated simultaneously.
Please note that AWR1243 device supports simultaneous operation of 2 transmitters only.
AWR1243
SWRS188D – MAY 2017 – REVISED DECEMBER 2021 www.ti.com
34 Submit Document Feedback Copyright © 2021 Texas Instruments Incorporated
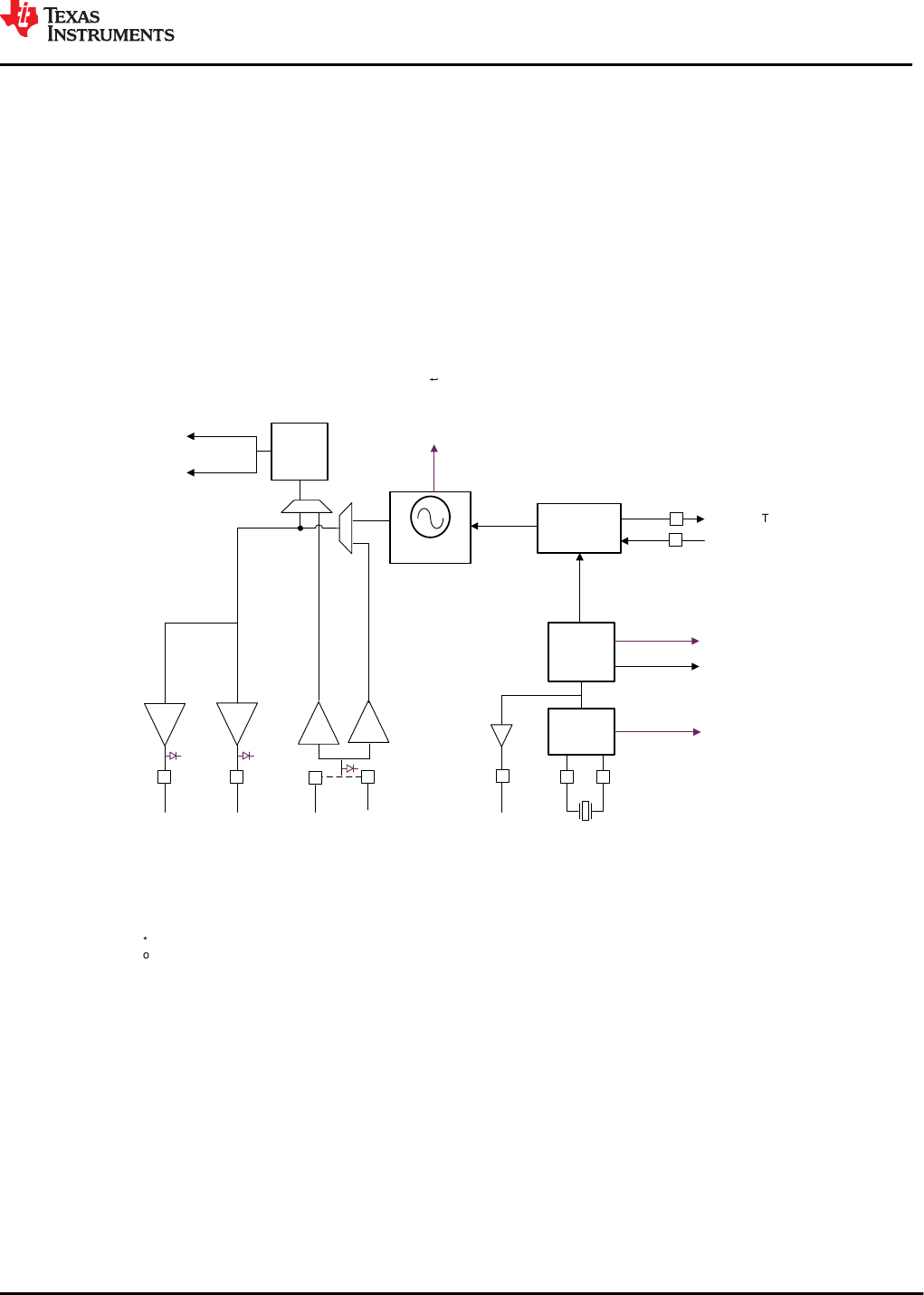
9.3.1.1 Clock Subsystem
The AWR1243 clock subsystem generates 76 to 81 GHz from an input reference of 40-MHz crystal. It has
a built-in oscillator circuit followed by a clean-up PLL and a RF synthesizer circuit. The output of the RF
synthesizer is then processed by an X4 multiplier to create the required frequency in the 76 to 81 GHz spectrum.
The RF synthesizer output is modulated by the timing engine block to create the required waveforms for effective
sensor operation.
The output of the RF synthesizer is available at the device pin boundary for multichip cascaded configuration.
The clean-up PLL also provides a reference clock for the host processor after system wakeup.
The clock subsystem also has built-in mechanisms for detecting the presence of a crystal and monitoring the
quality of the generated clock.
Figure 9-2 describes the clock subsystem.
Clean-Up
PLL
x4
MULT
RFSYNTH
Timing
Engine
RX LO
XO /
Slicer
SoC Clock
40 MHz
CLK Detect
Lock Detect
SYNC_IN
OSC_CLKOUT
Lock Detect
TX LO
FM_CW_SYNCIN2*
FM_CW_SYNCOUT
FM_CW_CLKOUT
FM_CW_SYNCIN1*
SYNC_OUT
* These pins are 20GHz LO input pins. Connect LO to one pin while grounding the
other pin.
Figure 9-2. Clock Subsystem
www.ti.com
AWR1243
SWRS188D – MAY 2017 – REVISED DECEMBER 2021
Copyright © 2021 Texas Instruments Incorporated Submit Document Feedback 35
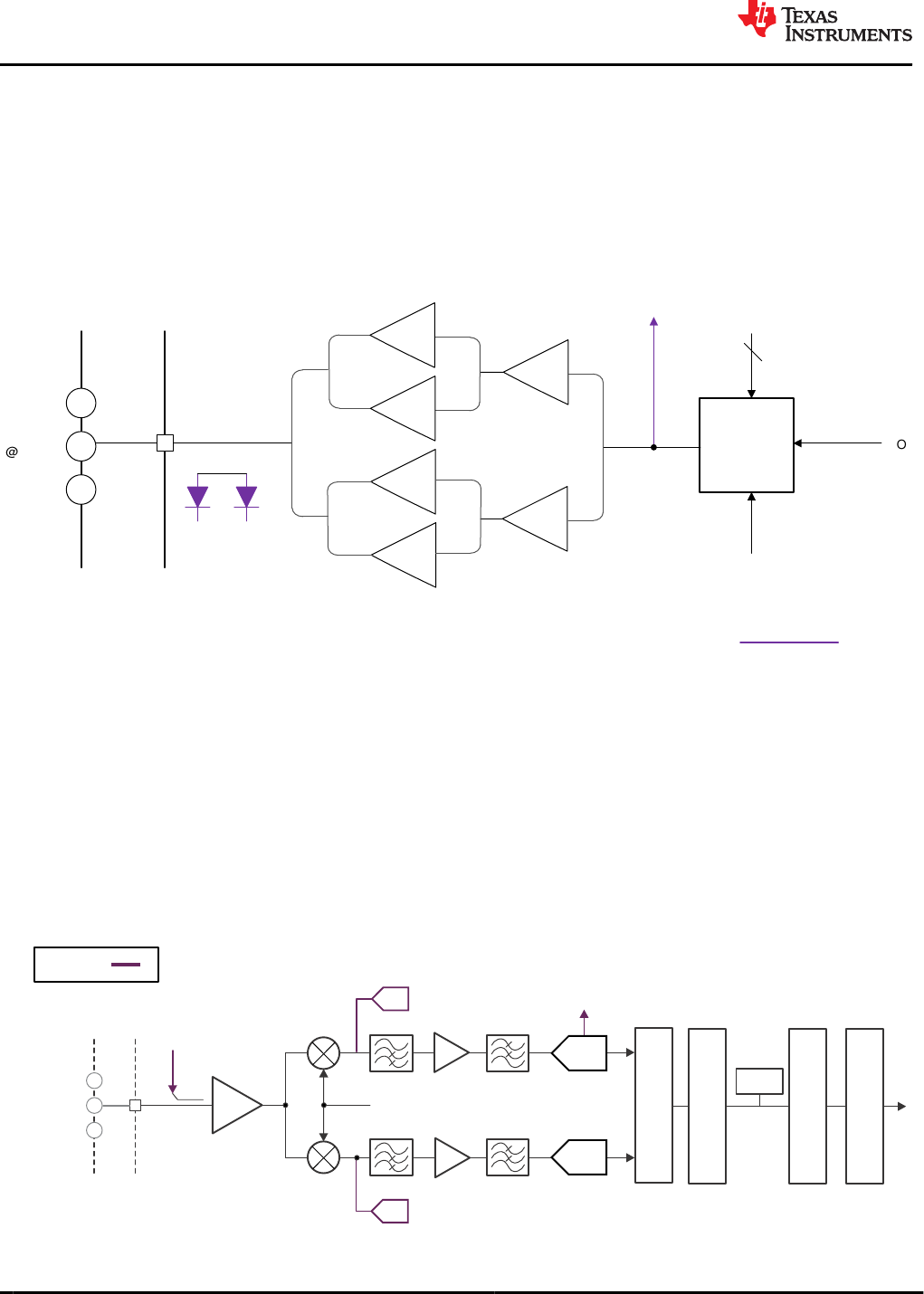
9.3.1.2 Transmit Subsystem
The AWR1243 transmit subsystem consists of three parallel transmit chains, each with independent phase and
amplitude control. A maximum of two transmit chains can be operational at the same time, however all three
chains can be operated together in a time-multiplexed fashion. The device supports binary phase modulation for
MIMO radar and interference mitigation.
Each transmit chain can deliver a maximum of 12 dBm at the antenna port on the PCB. The transmit chains also
support programmable backoff for system optimization.
Figure 9-3 describes the transmit subsystem.
û-
0/180°
(from Timing Engine)
6 bits
Loopback Path Fine Phase Shifter Control
PCB
Package
Chip
12dBm
@ 50 Ÿ LO
Self Test
Figure 9-3. Transmit Subsystem (Per Channel)
9.3.1.3 Receive Subsystem
The AWR1243 receive subsystem consists of four parallel channels. A single receive channel consists of an
LNA, mixer, IF filtering, ADC conversion, and decimation. All four receive channels can be operational at the
same time an individual power-down option is also available for system optimization.
Unlike conventional real-only receivers, the AWR1243 device supports a complex baseband architecture, which
uses quadrature mixer and dual IF and ADC chains to provide complex I and Q outputs for each receiver
channel. The AWR1243 is targeted for fast chirp systems. The band-pass IF chain has configurable lower cutoff
frequencies above 175 kHz and can support bandwidths up to 15 MHz.
Figure 9-4 describes the receive subsystem.
Self Test
Chip
Package
PCB
50 W
GSG
Loopback
Path
DAC
DSM
DSM
RSSI
I
Q
LO
Saturation
Detect
DAC
Decimation
Image Rejection
ADC Buffer
I/Q Correction
Figure 9-4. Receive Subsystem (Per Channel)
AWR1243
SWRS188D – MAY 2017 – REVISED DECEMBER 2021 www.ti.com
36 Submit Document Feedback Copyright © 2021 Texas Instruments Incorporated
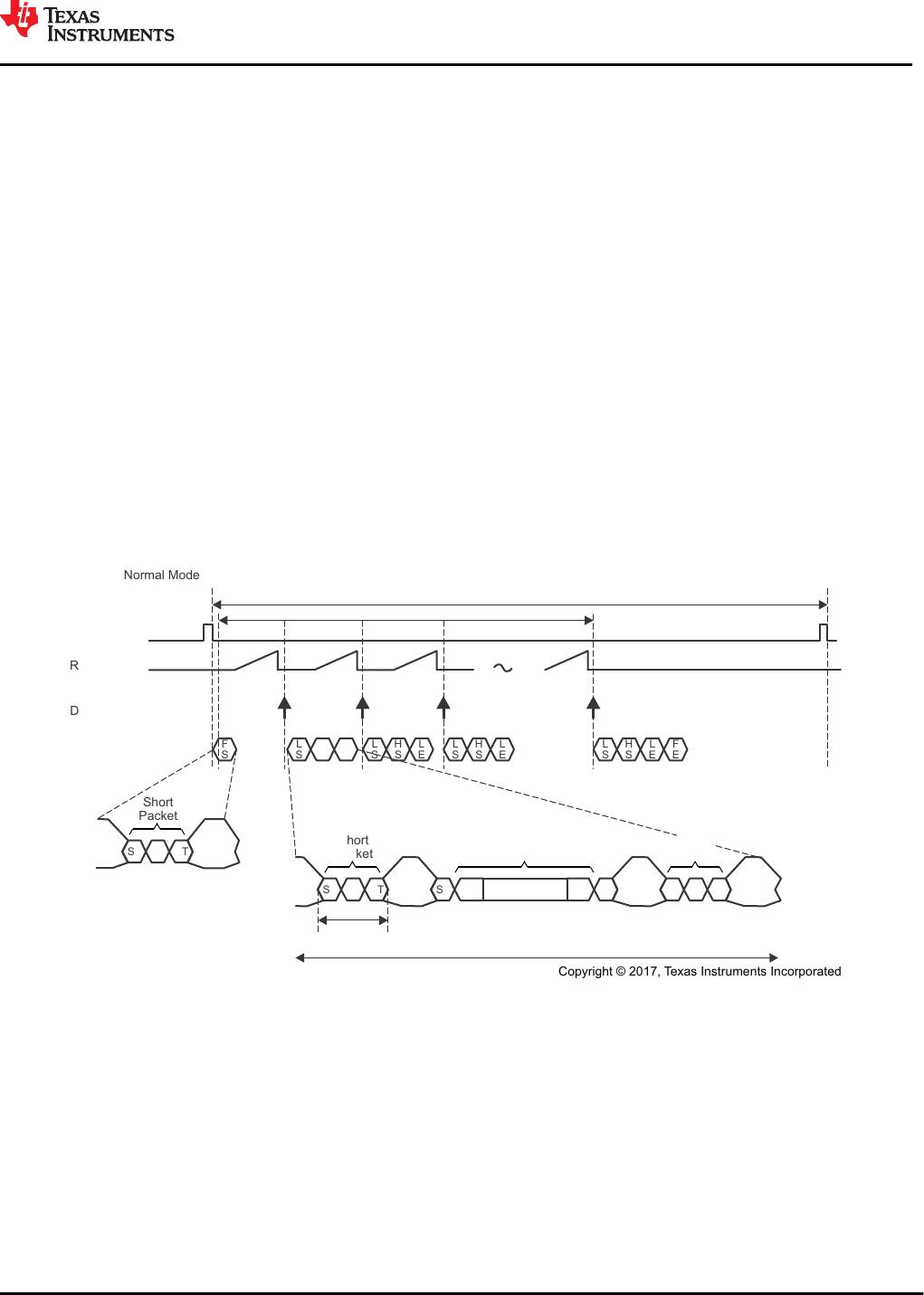
9.3.2 Host Interface
The AWR1243 device communicates with the host radar processor over the following main interfaces:
• Reference Clock – Reference clock available for host processor after device wakeup
• Control – 4-port standard SPI (peripheral) for host control along with HOST INTR pin for async events.. All
radio control commands (and response) flow through this interface.
• Data – High-speed serial port following the MIPI CSI2 format. Four data and one clock lane (all differential).
Data from different receive channels can be multiplexed on a single data lane to optimize board routing. This
is a unidirectional interface used for data transfer only.
• Reset – Active-low reset for device wakeup from host
• Out-of-band interrupt
• Error – Used for notifying the host in case the radio controller detects a fault
9.4 Other Subsystems
9.4.1 ADC Data Format Over CSI2 Interface
The AWR1243 device uses MIPI D-PHY / CSI2-based format to transfer the raw ADC samples to the external
MCU. This is shown in Figure 9-5.
• Supports four data lanes
• CSI-2 data rate scalable from 150 Mbps to 600 Mbps per lane
• Virtual channel based
• CRC generation
1 2 3 N
Frame Period
Acquisition Period
F
S
Frame
Ramp/Chirp
Data Ready
L
S
H
S
L
E
L
S
H
S
L
E
L
S
H
S
L
E
ST SP ET
Short
Packet
LPS
ST SP ET
Short
Packet
LPS
Chirp 1 data
Data rate/Lane should be such that "Chirp + Interchirp" period
should be able to accommodate the data transfer
L
S
H
S
L
E
F
E
ST SP ET
Short
Packet
Normal Mode
ST PH DATA
Long
Packet
PF ET LPS LPS
.5 s-.8 sμ μ
Copyright © 2017, Texas Instruments Incorporated
Frame Start – CSi2 VSYNC Start Short PacketLine Start – CSI2 HSYNC Start Short PacketLine End – CSI2 HSYNC End Short
PacketFrame End – CSi2 VSYNC End Short Packet
Figure 9-5. CSI-2 Transmission Format
www.ti.com
AWR1243
SWRS188D – MAY 2017 – REVISED DECEMBER 2021
Copyright © 2021 Texas Instruments Incorporated Submit Document Feedback 37
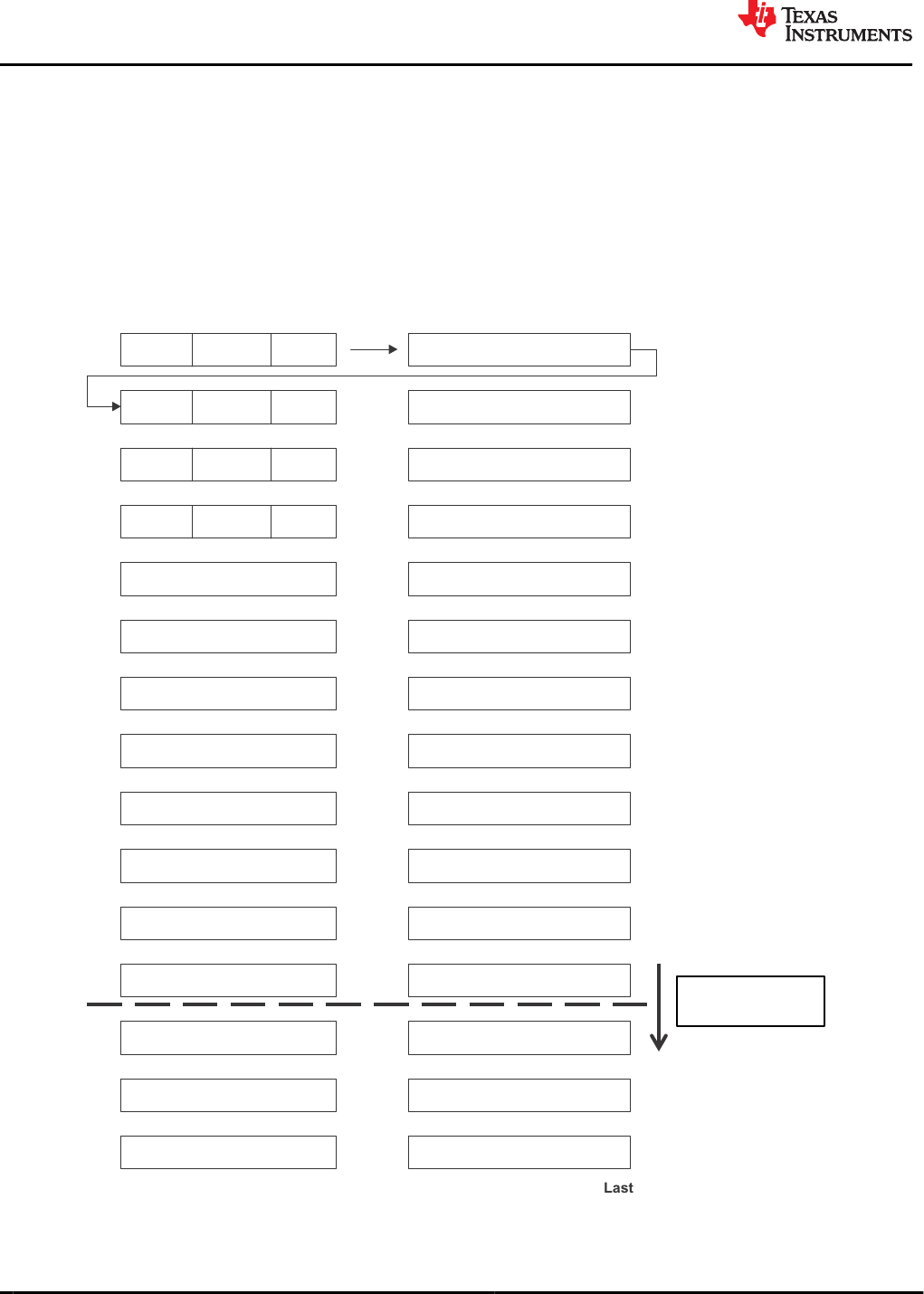
The data payload is constructed with the following three types of information:
• Chirp profile information
• The actual chirp number
• ADC data corresponding to chirps of all four channels
– Interleaved fashion
• Chirp quality data (configurable)
The payload is then split across the four physical data lanes and transmitted to the receiving D-PHY. The data
packet packing format is shown in Figure 9-6
First
11 51011 0
NU
CH Chirp
Profile
Channel
Number Chirp Num
11 51011 0
NU
CH Chirp
Profile
Channel
Number Chirp Num
11 51011 0
NU
CH Chirp
Profile
Channel
Number Chirp Num
11 51011 0
NU
CH Chirp
Profile
Channel
Number Chirp Num
11 011 0
Channel 0 Sample 0 i Channel 0 Sample 0 q
11 011 0
Channel 1 Sample 0 i Channel 1 Sample 0 q
11 011 0
Channel 2 Sample 0 i Channel 2 Sample 0 q
11 011 0
Channel 3 Sample 0 i Channel 3 Sample 0 q
11 011 0
Channel 0 Sample 1 i Channel 0 Sample 1 q
11 011 0
Channel 1 Sample 1 i Channel 1 Sample 1 q
11 011 0
Channel 2 Sample 1 i Channel 2 Sample 1 q
11 011 0
Channel 3 Sample 1 i Channel 3 Sample 1 q
11 011 0
CQ Data [11:0] CQ Data [23:12]
11 011 0
CQ Data [35:24] CQ Data [47:36]
11 011 0
CQ Data [59:48] NU CQ Data [63:60]
Last
Continues till the
last sample. Max 1023
Figure 9-6. Data Packet Packing Format for 12-Bit Complex Configuration
AWR1243
SWRS188D – MAY 2017 – REVISED DECEMBER 2021 www.ti.com
38 Submit Document Feedback Copyright © 2021 Texas Instruments Incorporated

10 Monitoring and Diagnostics
10.1 Monitoring and Diagnostic Mechanisms
Below is the list given for the main monitoring and diagnostic mechanisms available in the AWR1243.
MSS R4F is the processor used for running TI's Functional Firmware stored in the ROM that helps in the
execution of the API calls issued by the host processor (It is not a customer programmable core).
Table 10-1. Monitoring and Diagnostic Mechanisms for AWR1243
S No Feature Description
1
Boot time LBIST For MSS
R4F Core and associated
VIM
AWR1243 architecture supports hardware logic BIST (LBIST) engine self-test Controller
(STC). This logic is used to provide a very high diagnostic coverage (>90%) on the MSS
R4F CPU core and Vectored Interrupt Module (VIM) at a transistor level.
LBIST for the CPU and VIM are triggered by the bootloader.
2Boot time PBIST for MSS
R4F TCM Memories
MSS R4F has three Tightly coupled Memories (TCM) memories TCMA, TCMB0 and
TCMB1. AWR1243 architecture supports a hardware programmable memory BIST (PBIST)
engine. This logic is used to provide a very high diagnostic coverage (March-13n) on the
implemented MSS R4F TCMs at a transistor level.
PBIST for TCM memories is triggered by Bootloader at the boot time . CPU stays there in
while loop and does not proceed further if a fault is identified.
3End to End ECC for MSS
R4F TCM Memories
TCMs diagnostic is supported by Single error correction double error detection (SECDED)
ECC diagnostic. An 8-bit code word is used to store the ECC data as calculated over the
64-bit data bus. ECC evaluation is done by the ECC control logic inside the CPU. This
scheme provides end-to-end diagnostics on the transmissions between CPU and TCM. CPU
is configured to have predetermined response (Ignore or Abort generation) to single and
double bit error conditions.
4MSS R4F TCM bit
multiplexing
Logical TCM word and its associated ECC code is split and stored in two physical SRAM
banks. This scheme provides an inherent diagnostic mechanism for address decode failures
in the physical SRAM banks. Faults in the bank addressing are detected by the CPU as
an ECC fault.Further, bit multiplexing scheme implemented such that the bits accessed to
generate a logical (CPU) word are not physically adjacent. This scheme helps to reduce the
probability of physical multi-bit faults resulting in logical multi-bit faults; rather they manifest
as multiple single bit faults. As the SECDED TCM ECC can correct a single bit fault in a
logical word, this scheme improves the usefulness of the TCM ECC diagnostic.
5 Clock Monitor
AWR1243 architecture supports Three Digital Clock Comparators (DCCs) and an internal
RCOSC. Dual functionality is provided by these modules – Clock detection and Clock
Monitoring.
DCCint is used to check the availability/range of Reference clock at boot otherwise the
device is moved into limp mode (Device still boots but on 10MHz RCOSC clock source.
This provides debug capability). DCCint is only used by boot loader during boot time. It is
disabled once the APLL is enabled and locked.
DCC1 is dedicated for APLL lock detection monitoring, comparing the APLL output divided
version with the Reference input clock of the device. Initially (before configuring APLL),
DCC1 is used by bootloader to identify the precise frequency of reference input clock
against the internal RCOSC clock source. Failure detection for DCC1 would cause the
device to go into limp mode.
Clock Compare module (CCC) module is used to compare the APLL divided down
frequency with reference clock (XTAL). Failure detection is indicated by the nERROR OUT
signal.
6 RTI/WD for MSS R4F Internal watchdog is enabled by the bootloader in a windowed watchdog (DWWD) mode..
Watchdog expiry issues an internal warm reset and nERROR OUT signal to the host.
7 MPU for MSS R4F
Cortex-R4F CPU includes an MPU. The MPU logic can be used to provide spatial
separation of software tasks in the device memory. Cortex-R4F MPU supports 12 regions.
It is expected that the operating system controls the MPU and changes the MPU settings
based on the needs of each task. A violation of a configured memory protection policy
results in a CPU abort.
8PBIST for Peripheral interface
SRAMs - SPI, I2C
AWR1243 architecture supports a hardware programmable memory BIST (PBIST) engine
for Peripheral SRAMs as well.
PBIST for peripheral SRAM memories is triggered by the bootloader. The PBIST tests are
destructive to memory contents, and as such are typically run only at boot time. .
Any fault detected by the PBIST results in an error indicated in PBIST and boot status
response message.
www.ti.com
AWR1243
SWRS188D – MAY 2017 – REVISED DECEMBER 2021
Copyright © 2021 Texas Instruments Incorporated Submit Document Feedback 39
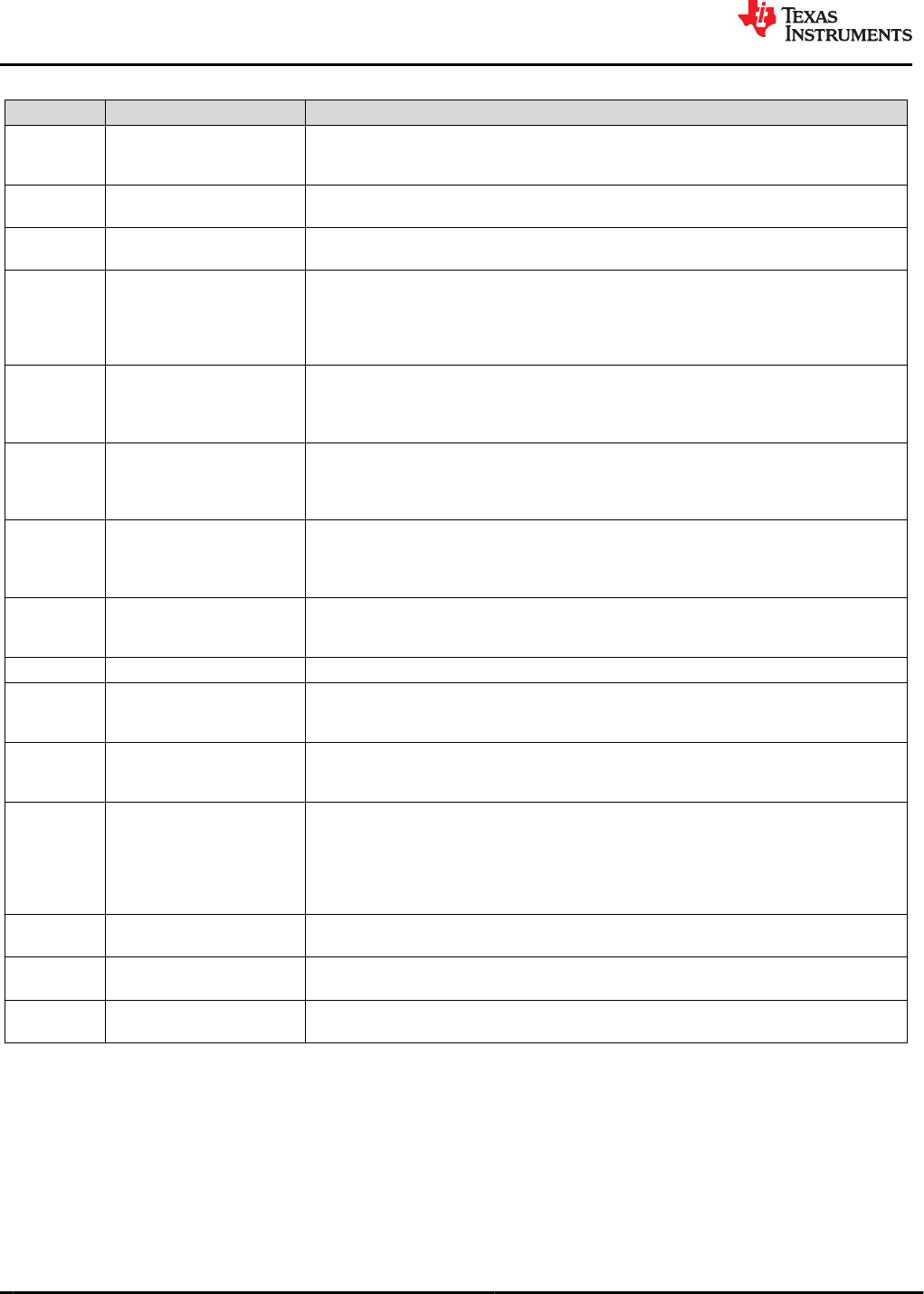
Table 10-1. Monitoring and Diagnostic Mechanisms for AWR1243 (continued)
S No Feature Description
9ECC for Peripheral interface
SRAMs – SPI, I2C
Peripheral interface SRAMs diagnostic is supported by Single error correction double error
detection (SECDED) ECC diagnostic. When a single or double bit error is detected the error
is indicated by nERROR (double bit error) or via SPI message (single bit error).
10 Cyclic Redundancy Check –
Main SS
Cyclic Redundancy Check (CRC) module is available for the Main SS. The firmware uses
this feature for data transfer checks in mailbox and SPI communication.
11 MPU for DMAs AWR1243 architecture supports MPUs on Main SS DMAs. The firmware uses this for stack
protection.
12
Boot time LBIST For BIST
R4F Core and associated
VIM
AWR1243 architecture supports hardware logic BIST (LBIST) even for BIST R4F core and
associated VIM module. This logic provides very high diagnostic coverage (>90%) on the
BIST R4F CPU core and VIM.
This is triggered by MSS R4F boot loader at boot time and it does not proceed further if the
fault is detected.
13 Boot time PBIST for BIST
R4F TCM Memories
AWR1243 architecture supports a hardware programmable memory BIST (PBIST) engine
for BIST R4F TCMs which provide a very high diagnostic coverage (March-13n) on the BIST
R4F TCMs.
PBIST is triggered at the power up of the BIST R4F.
14 End to End ECC for BIST
R4F TCM Memories
BIST R4F TCMs diagnostic is supported by Single error correction double error detection
(SECDED) ECC diagnostic. Single bit error is communicated to the BIST R4FCPU while
double bit error is communicated to MSS R4F as an interrupt which sends a async event to
the host.
15 BIST R4F TCM bit
multiplexing
Logical TCM word and its associated ECC code is split and stored in two physical SRAM
banks. This scheme provides an inherent diagnostic mechanism for address decode failures
in the physical SRAM banks and helps to reduce the probability of physical multi-bit faults
resulting in logical multi-bit faults.
16 Temperature Sensors
AWR1243 architecture supports various temperature sensors all across the device (next to
power hungry modules such as PAs, DSP etc) which is monitored during the inter-frame
period.(1)
17 Tx Power Monitors AWR1243 architecture supports power detectors at the Tx output.(2)
18 Error Signaling
Error Output
When a diagnostic detects a fault, the error must be indicated. The AWR1243 architecture
provides aggregation of fault indication from internal monitoring/diagnostic mechanisms
using nERROR signaling or async event over SPI interface.
19 Synthesizer (Chirp) frequency
monitor
Monitors Synthesizer’s frequency ramp by counting (divided-down) clock cycles and
comparing to ideal frequency ramp. Excess frequency errors above a certain threshold, if
any, are detected and reported.
20 Ball break detection for TX
ports (TX Ball break monitor)
AWR1243 architecture supports a ball break detection mechanism based on Impedance
measurement at the TX output(s) to detect and report any large deviations that can indicate
a ball break.
Monitoring is done by TIs code running on BIST R4F and failure is reported to the host.
It is completely up to customer SW to decide on the appropriate action based on the
message from BIST R4F.
21 RX loopback test Built-in TX to RX loopback to enable detection of failures in the RX path(s), including Gain,
inter-RX balance, etc.
22 IF loopback test Built-in IF (square wave) test tone input to monitor IF filter’s frequency response and detect
failure.
23 RX saturation detect Provision to detect ADC saturation due to excessive incoming signal level and/or
interference.
(1) Monitoring is done by the TI's code running on BIST R4F. There are two modes in which it could be configured to report the
temperature sensed via API by customer application.
a. Report the temperature sensed after every N frames
b. Report the condition once the temperature crosses programmed threshold.
It is completely up to customer SW to decide on the appropriate action based on the message from BIST R4Fvia Mailbox.
(2) Monitoring is done by the TI's code running on BIST R4F.
There are two modes in which it could be configured to report the detected output power via API by customer application.
a. Report the power detected after every N frames
b. Report the condition once the output power degrades by more than configured threshold from the configured.
It is completely up to customer SW to decide on the appropriate action based on the message from BIST R4F.
AWR1243
SWRS188D – MAY 2017 – REVISED DECEMBER 2021 www.ti.com
40 Submit Document Feedback Copyright © 2021 Texas Instruments Incorporated
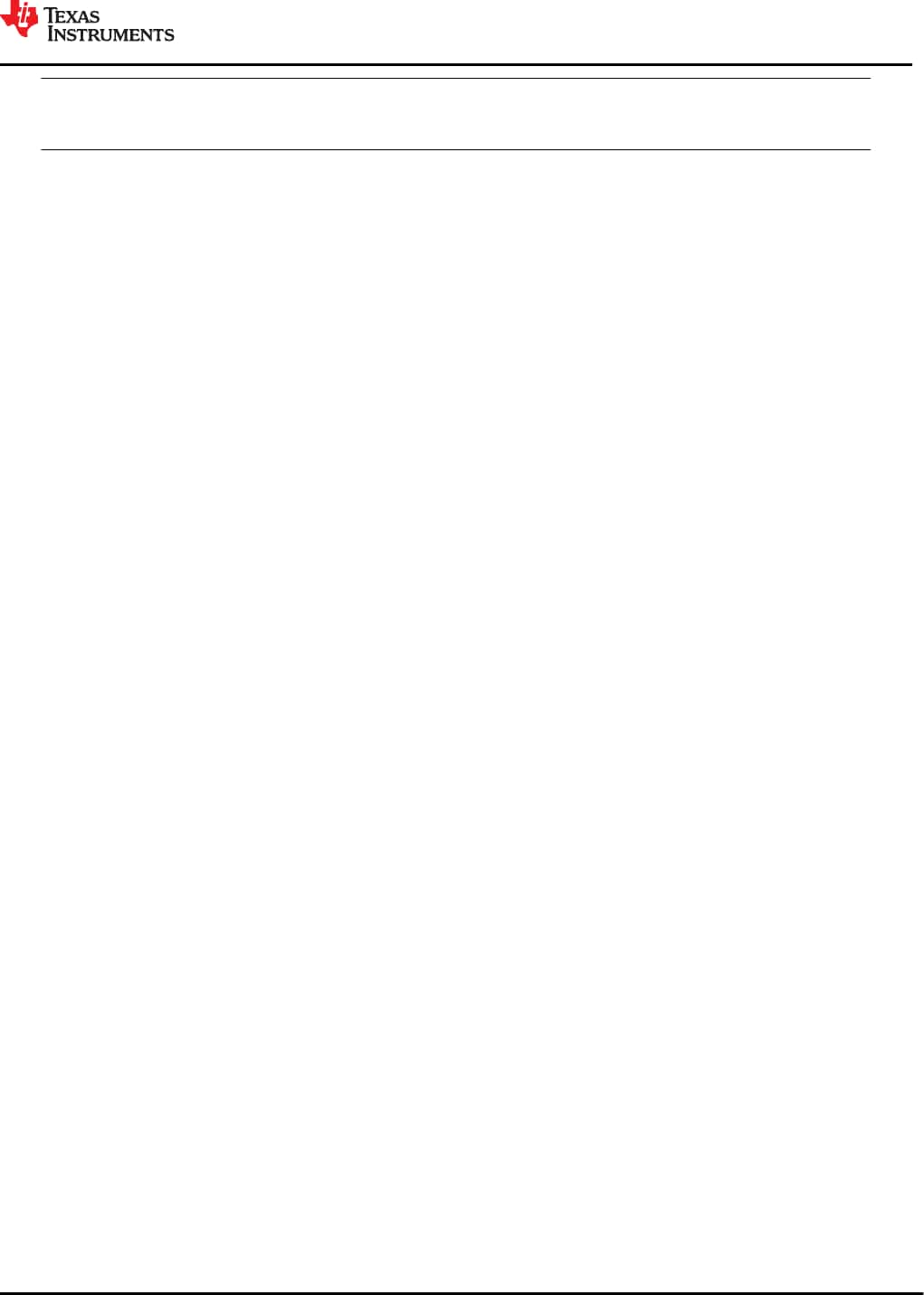
Note
Refer to the Device Safety Manual or other relevant collaterals for more details on applicability of all
diagnostics mechanisms. For certification details, refer to the device product folder.
www.ti.com
AWR1243
SWRS188D – MAY 2017 – REVISED DECEMBER 2021
Copyright © 2021 Texas Instruments Incorporated Submit Document Feedback 41

11 Applications, Implementation, and Layout
Note
Information in the following Applications section is not part of the TI component specification, and
TI does not warrant its accuracy or completeness. TI's customers are responsible for determining
suitability of components for their purposes. Customers should validate and test their design
implementation to confirm system functionality.
11.1 Application Information
A typical application addresses the standard short-, mid-, long-range, and high-performance imaging radar
applications with this radar front end and external programmable MCU. Figure 11-1 shows a short-, medium-, or
long-range radar application.
11.2 Short-, Medium-, and Long-Range Radar
Antenna
Structure SPI
Power Management Crystal
Automotive
Interface PHY
CSI2 (4 Lane Data + 1 Clock lane)
Reset
Error
MCU Clock
AWR1243
RX1
RX2
RX3
RX4
TX1
TX2
TX3
External
MCU
(For Example
TDA3x)
Copyright © 2017, Texas Instruments Incorporated
Figure 11-1. Short-, Medium-, and Long-Range Radar
AWR1243
SWRS188D – MAY 2017 – REVISED DECEMBER 2021 www.ti.com
42 Submit Document Feedback Copyright © 2021 Texas Instruments Incorporated
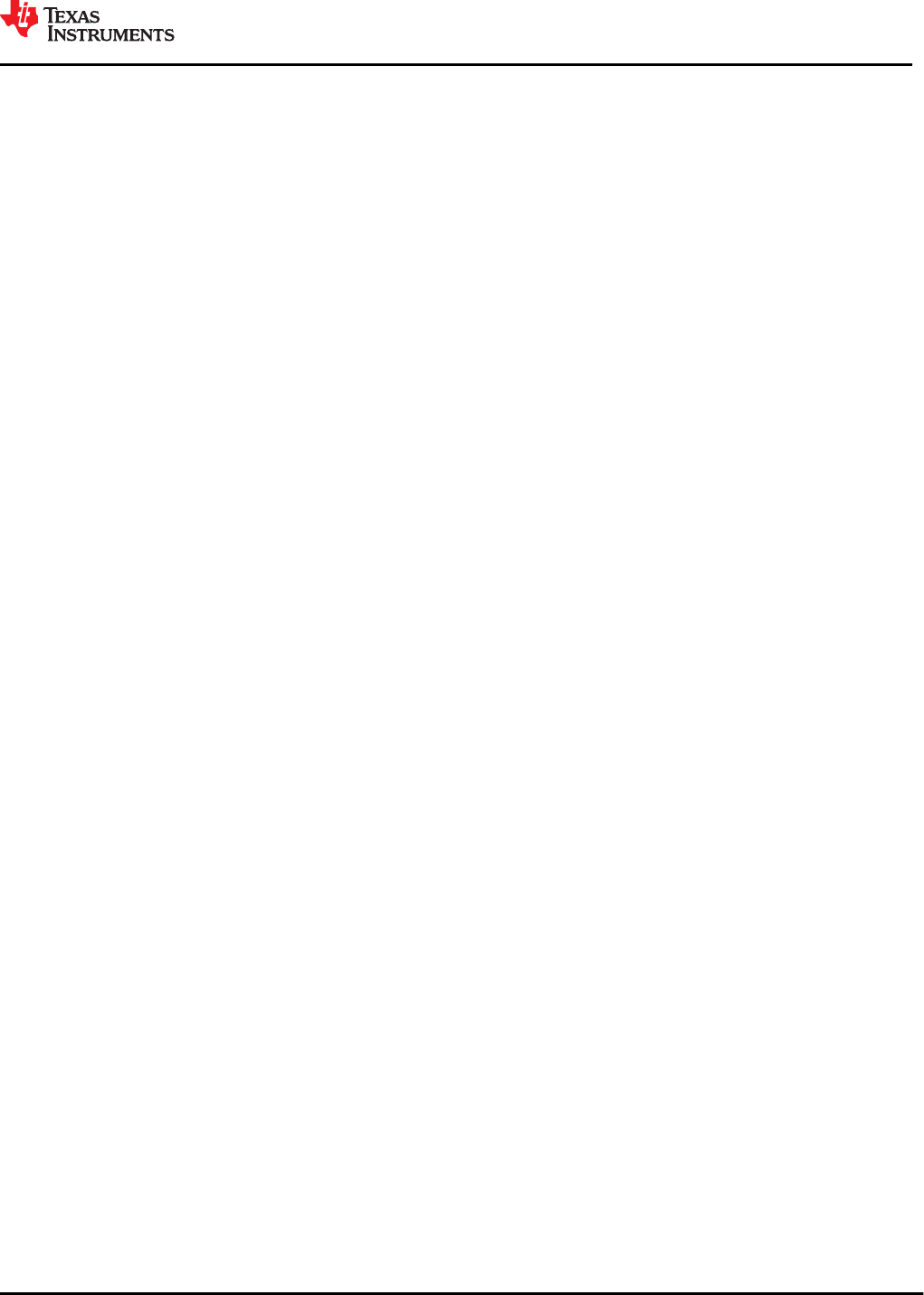
11.3 Reference Schematic
The reference schematic and power supply information can be found in the AWR1243 EVM Documentation.
Listed for convenience are: Design Files, Schematics, Layouts, and Stack up for PCB.
•Altium AWR1243 EVM Design Files
•AWR1243 EVM Schematic Drawing, Assembly Drawing, and Bill of Materials
www.ti.com
AWR1243
SWRS188D – MAY 2017 – REVISED DECEMBER 2021
Copyright © 2021 Texas Instruments Incorporated Submit Document Feedback 43
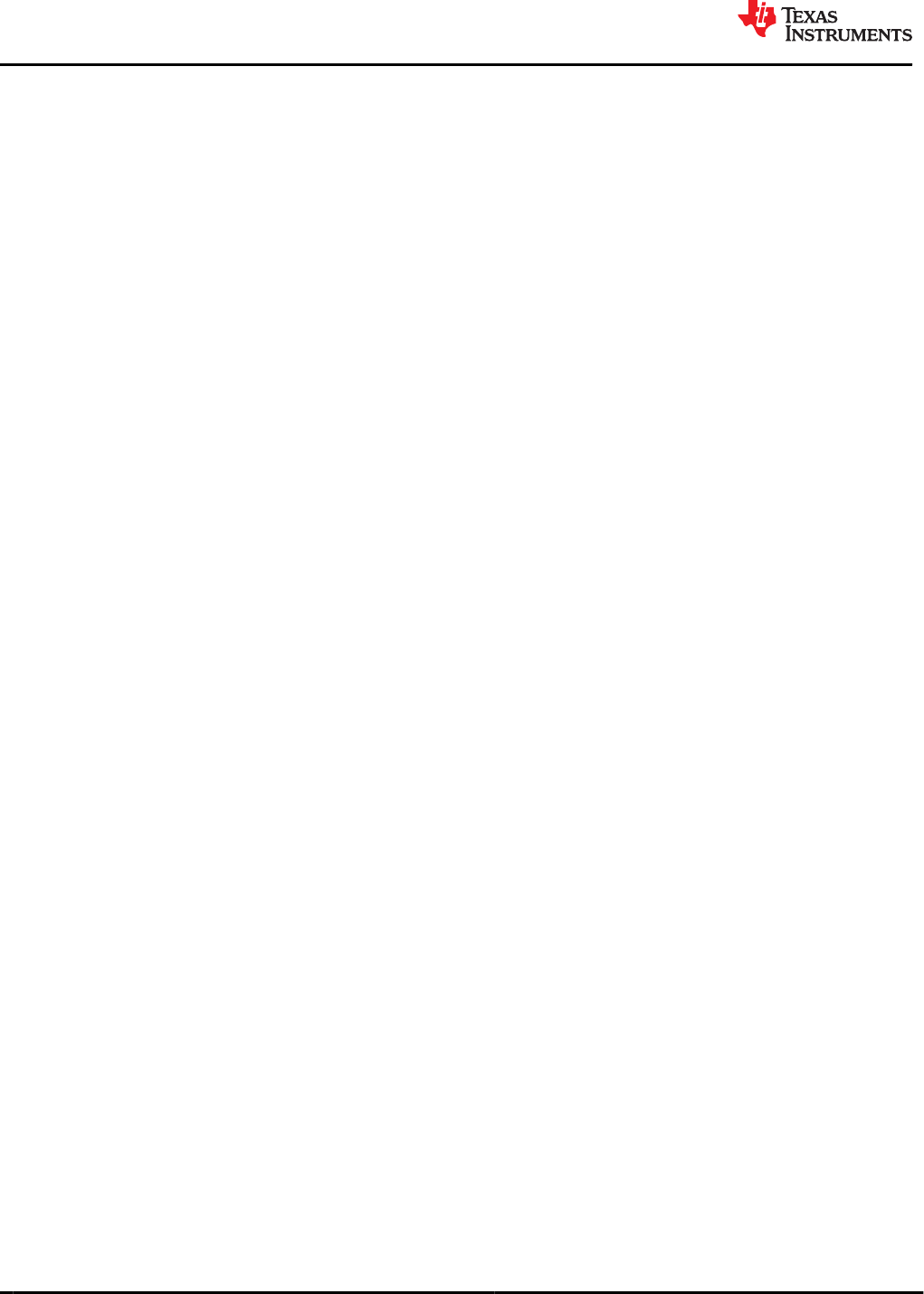
12 Device and Documentation Support
TI offers an extensive line of development tools. Tools and software to evaluate the performance of the device,
generate code, and develop solutions follow.
12.1 Device Nomenclature
To designate the stages in the product development cycle, TI assigns prefixes to the part numbers of all
microprocessors (MPUs) and support tools. Each device has one of three prefixes: X, P, or null (no prefix) (for
example, AWR1243). Texas Instruments recommends two of three possible prefix designators for its support
tools: TMDX and TMDS. These prefixes represent evolutionary stages of product development from engineering
prototypes (TMDX) through fully qualified production devices and tools (TMDS).
Device development evolutionary flow:
X Experimental device that is not necessarily representative of the final device's electrical specifications and
may not use production assembly flow.
P Prototype device that is not necessarily the final silicon die and may not necessarily meet final electrical
specifications.
null Production version of the silicon die that is fully qualified.
Support tool development evolutionary flow:
TMDX Development-support product that has not yet completed Texas Instruments internal qualification testing.
TMDS Fully-qualified development-support product.
X and P devices and TMDX development-support tools are shipped against the following disclaimer:
"Developmental product is intended for internal evaluation purposes."
Production devices and TMDS development-support tools have been characterized fully, and the quality and
reliability of the device have been demonstrated fully. TI's standard warranty applies.
Predictions show that prototype devices (X or P) have a greater failure rate than the standard production
devices. Texas Instruments recommends that these devices not be used in any production system because their
expected end-use failure rate still is undefined. Only qualified production devices are to be used.
TI device nomenclature also includes a suffix with the device family name. This suffix indicates the package
type (for example, ABL0161 ALB0161), the temperature range (for example, blank is the default commercial
temperature range). Figure 12-1 provides a legend for reading the complete device name for any AWR1243
device.
For orderable part numbers of AWR1243 devices in the ABL0161 package types, see the Package Option
Addendum of this document , the TI website (www.ti.com), or contact your TI sales representative.
For additional description of the device nomenclature markings on the die, see the AWR1243 Device Errata .
AWR1243
SWRS188D – MAY 2017 – REVISED DECEMBER 2021 www.ti.com
44 Submit Document Feedback Copyright © 2021 Texas Instruments Incorporated
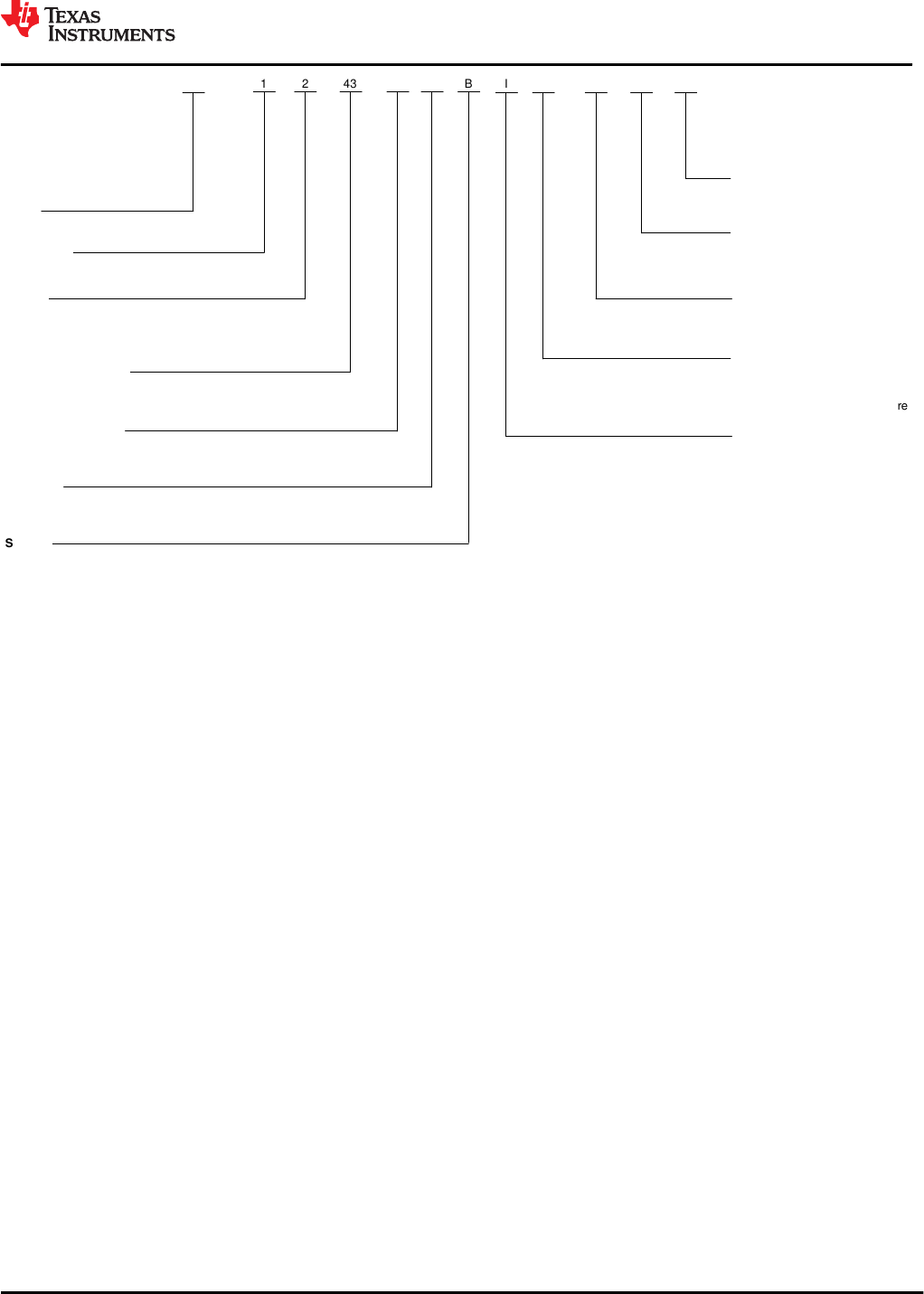
AWR 1 2 43 B I GABL
Prefix XA = Pre-Production
AWR = Production
Generation
Variant
Num RX/TX Channels
Features
Silicon PG Revision
Safety
±GHz
2 = FE
4 = FE + FFT + MCU
6 = FE + MCU + DSP
8 = FE + FFT + MCU + DSP
RX = 1,2,3,4
TX = 1,2,3
Blank = Baseline
Blank = Rev 1.0
E = Rev 2.0
B = Functional Safety Complaint, ASIL-B
Tray or Tape & Reel
Package
Security
Temperature (Tj)
R = Big Reel
Blank = Tray
ABL = BGA
G = General
S = Secure
D = Development Secure
C = 0°C to 70°C
K = ±°C to 85°C
A = ±°C to 105°C
I = ±°C to 125°C
Qualification
Q1 = AEC-Q100
Blank = no special Qual
Q1
F = Rev 3.0
Figure 12-1. Device Nomenclature
12.2 Tools and Software
Development Tools
AWR1243 cascade application note Describes TI's cascaded mmWave radar system.
Models
AWR1243 BSDL model Boundary scan database of testable input and output pins for IEEE 1149.1 of the
specific device.
AWR1x43 IBIS model IO buffer information model for the IO buffers of the device. For simulation on a
circuit board, see IBIS Open Forum.
AWR1243 checklist for
schematic review, layout
review, bringup/wakeup
A set of steps in spreadsheet form to select system functions and pinmux options.
Specific EVM schematic and layout notes to apply to customer engineering. A
bringup checklist is suggested for customers.
12.3 Documentation Support
To receive notification of documentation updates, navigate to the device product folder on ti.com. Click on
Subscribe to updates to register and receive a weekly digest of any product information that has changed. For
change details, review the revision history included in any revised document.
The current documentation that describes the DSP, related peripherals, and other technical collateral follows.
Errata
AWR1243 device errata Describes known advisories, limitations, and cautions on silicon and provides
workarounds.
12.4 Support Resources
TI E2E™ support forums are an engineer's go-to source for fast, verified answers and design help — straight
from the experts. Search existing answers or ask your own question to get the quick design help you need.
www.ti.com
AWR1243
SWRS188D – MAY 2017 – REVISED DECEMBER 2021
Copyright © 2021 Texas Instruments Incorporated Submit Document Feedback 45
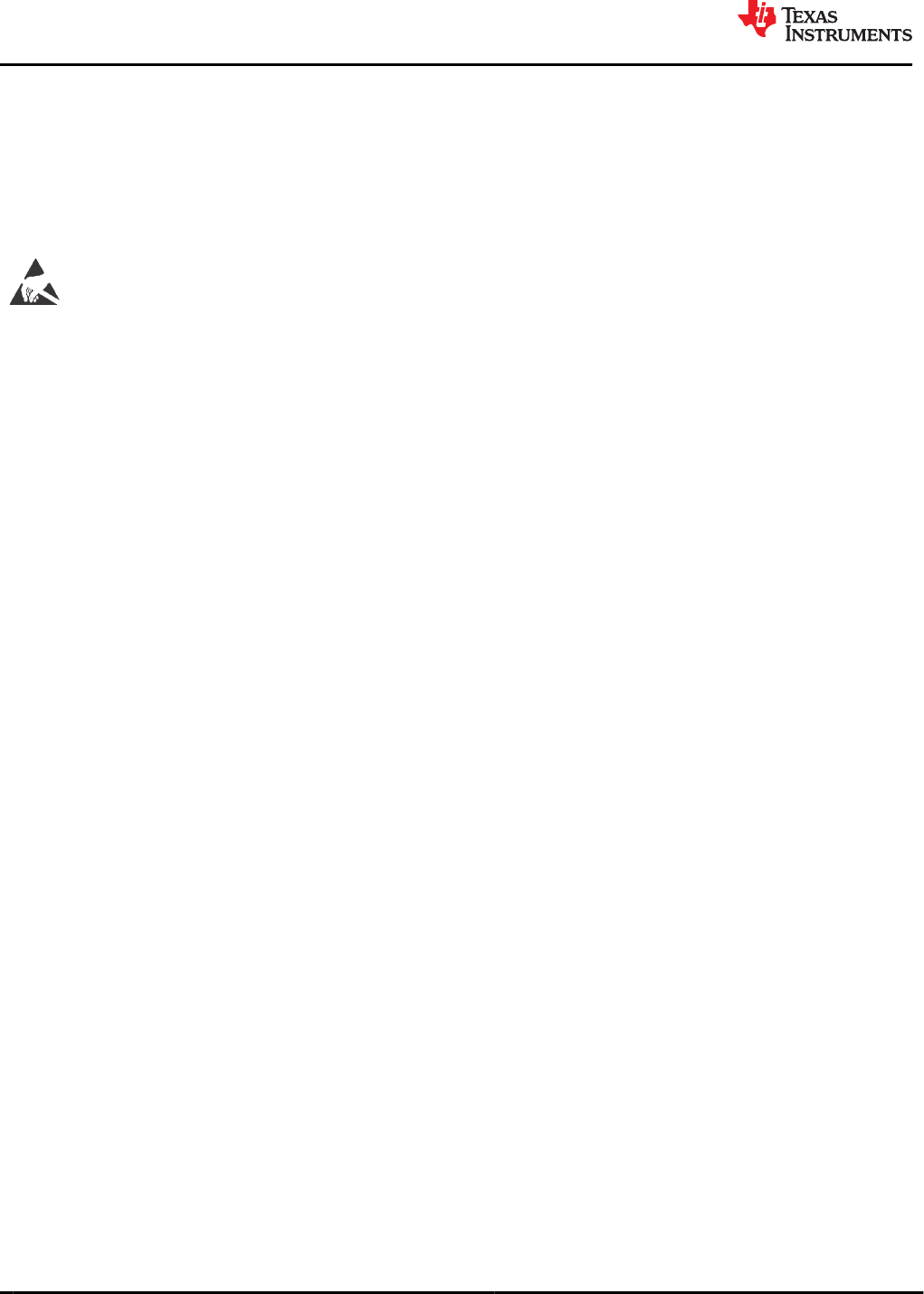
Linked content is provided "AS IS" by the respective contributors. They do not constitute TI specifications and do
not necessarily reflect TI's views; see TI's Terms of Use.
12.5 Trademarks
TI E2E™ is a trademark of Texas Instruments.
All trademarks are the property of their respective owners.
12.6 Electrostatic Discharge Caution
This integrated circuit can be damaged by ESD. Texas Instruments recommends that all integrated circuits be handled
with appropriate precautions. Failure to observe proper handling and installation procedures can cause damage.
ESD damage can range from subtle performance degradation to complete device failure. Precision integrated circuits may
be more susceptible to damage because very small parametric changes could cause the device not to meet its published
specifications.
12.7 Glossary
TI Glossary This glossary lists and explains terms, acronyms, and definitions.
AWR1243
SWRS188D – MAY 2017 – REVISED DECEMBER 2021 www.ti.com
46 Submit Document Feedback Copyright © 2021 Texas Instruments Incorporated

13 Mechanical, Packaging, and Orderable Information
13.1 Packaging Information
The following pages include mechanical, packaging, and orderable information. This information is the most
current data available for the designated devices. This data is subject to change without notice and revision of
this document. For browser-based versions of this data sheet, refer to the left-hand navigation.
13.2 Tray Information for
www.ti.com
AWR1243
SWRS188D – MAY 2017 – REVISED DECEMBER 2021
Copyright © 2021 Texas Instruments Incorporated Submit Document Feedback 47

PACKAGE OPTION ADDENDUM
www.ti.com 11-Nov-2021
Addendum-Page 1
PACKAGING INFORMATION
Orderable Device Status
(1)
Package Type Package
Drawing Pins Package
Qty Eco Plan
(2)
Lead finish/
Ball material
(6)
MSL Peak Temp
(3)
Op Temp (°C) Device Marking
(4/5)
Samples
AWR1243FBIGABLQ1 ACTIVE FCCSP ABL 161 176 RoHS & Green Call TI Level-3-260C-168 HR -40 to 125 AWR1243
IG
964FC
AWR1243FBIGABLRQ1 ACTIVE FCCSP ABL 161 1000 RoHS & Green Call TI Level-3-260C-168 HR -40 to 125 AWR1243
IG
ABL G1
964FC
(1) The marketing status values are defined as follows:
ACTIVE: Product device recommended for new designs.
LIFEBUY: TI has announced that the device will be discontinued, and a lifetime-buy period is in effect.
NRND: Not recommended for new designs. Device is in production to support existing customers, but TI does not recommend using this part in a new design.
PREVIEW: Device has been announced but is not in production. Samples may or may not be available.
OBSOLETE: TI has discontinued the production of the device.
(2) RoHS: TI defines "RoHS" to mean semiconductor products that are compliant with the current EU RoHS requirements for all 10 RoHS substances, including the requirement that RoHS substance
do not exceed 0.1% by weight in homogeneous materials. Where designed to be soldered at high temperatures, "RoHS" products are suitable for use in specified lead-free processes. TI may
reference these types of products as "Pb-Free".
RoHS Exempt: TI defines "RoHS Exempt" to mean products that contain lead but are compliant with EU RoHS pursuant to a specific EU RoHS exemption.
Green: TI defines "Green" to mean the content of Chlorine (Cl) and Bromine (Br) based flame retardants meet JS709B low halogen requirements of <=1000ppm threshold. Antimony trioxide based
flame retardants must also meet the <=1000ppm threshold requirement.
(3) MSL, Peak Temp. - The Moisture Sensitivity Level rating according to the JEDEC industry standard classifications, and peak solder temperature.
(4) There may be additional marking, which relates to the logo, the lot trace code information, or the environmental category on the device.
(5) Multiple Device Markings will be inside parentheses. Only one Device Marking contained in parentheses and separated by a "~" will appear on a device. If a line is indented then it is a continuation
of the previous line and the two combined represent the entire Device Marking for that device.
(6) Lead finish/Ball material - Orderable Devices may have multiple material finish options. Finish options are separated by a vertical ruled line. Lead finish/Ball material values may wrap to two
lines if the finish value exceeds the maximum column width.
Important Information and Disclaimer:The information provided on this page represents TI's knowledge and belief as of the date that it is provided. TI bases its knowledge and belief on information
provided by third parties, and makes no representation or warranty as to the accuracy of such information. Efforts are underway to better integrate information from third parties. TI has taken and
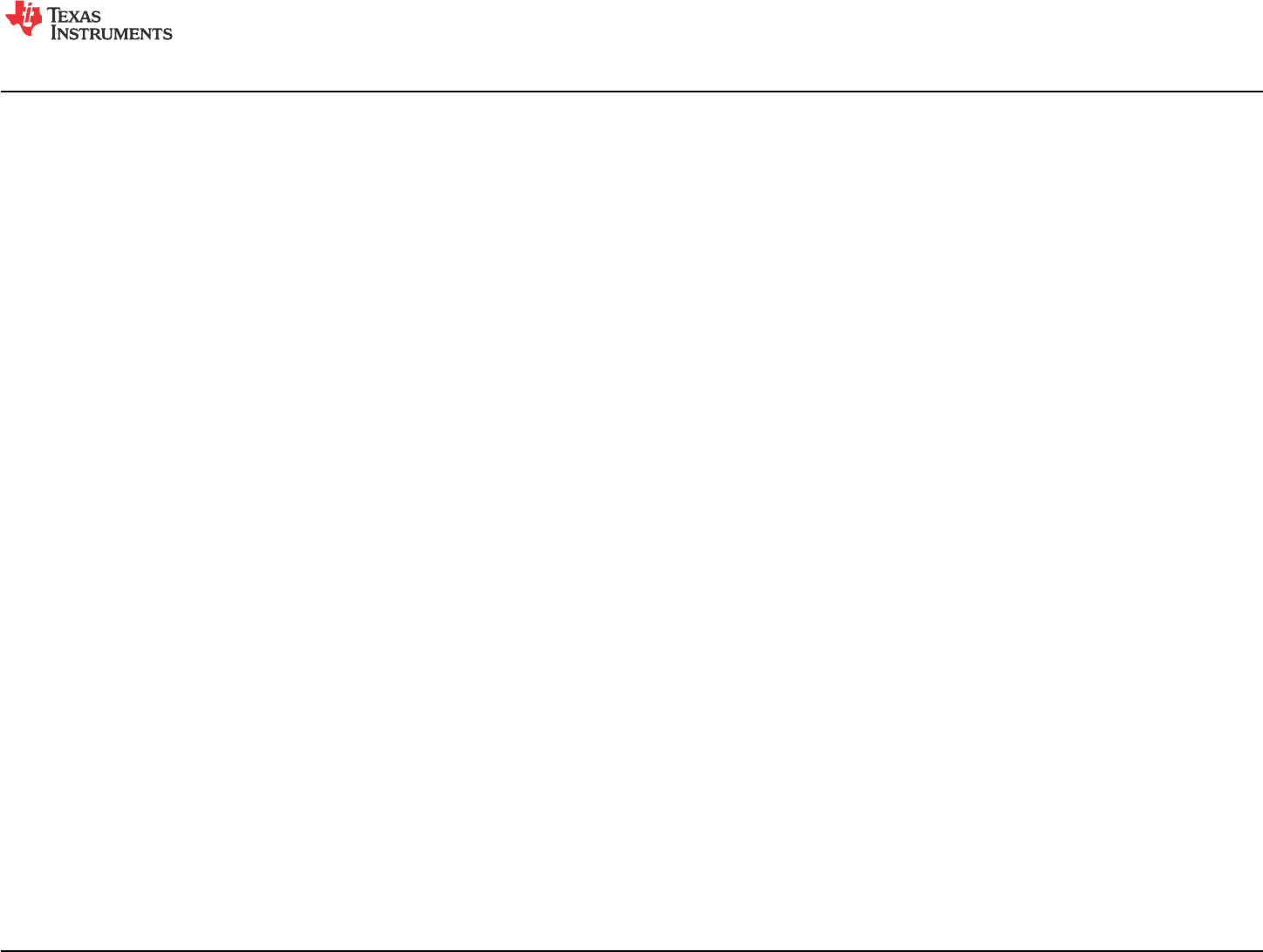
PACKAGE OPTION ADDENDUM
www.ti.com 11-Nov-2021
Addendum-Page 2
continues to take reasonable steps to provide representative and accurate information but may not have conducted destructive testing or chemical analysis on incoming materials and chemicals.
TI and TI suppliers consider certain information to be proprietary, and thus CAS numbers and other limited information may not be available for release.
In no event shall TI's liability arising out of such information exceed the total purchase price of the TI part(s) at issue in this document sold by TI to Customer on an annual basis.
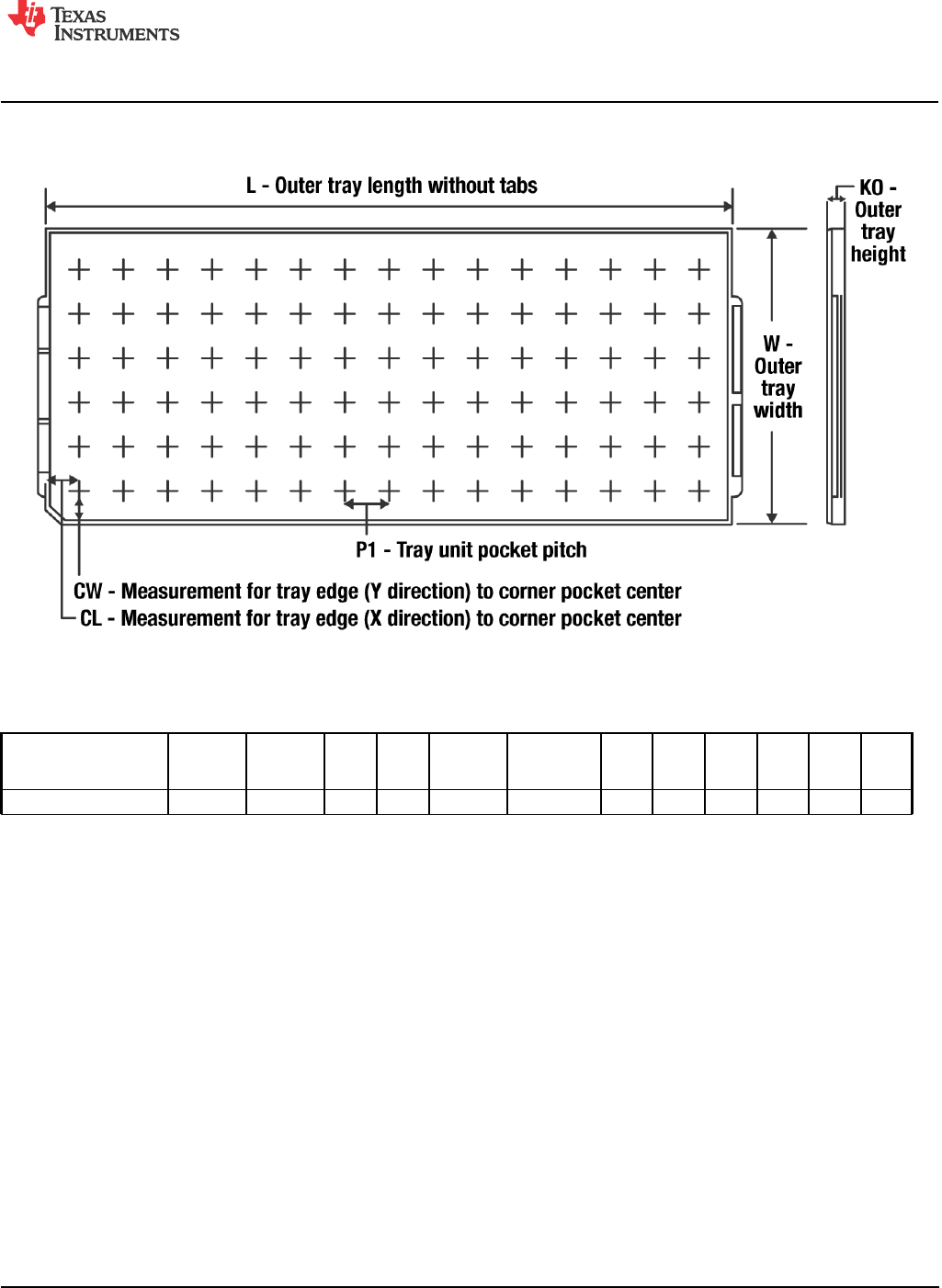
TRAY
Chamfer on Tray corner indicates Pin 1 orientation of packed units.
*All dimensions are nominal
Device Package
Name Package
Type Pins SPQ Unit array
matrix Max
temperature
(°C)
L (mm) W
(mm) K0
(µm) P1
(mm) CL
(mm) CW
(mm)
AWR1243FBIGABLQ1 ABL FCCSP 161 176 8 x 22 150 315 135.9 7620 13.4 16.8 17.2
PACKAGE MATERIALS INFORMATION
www.ti.com 5-Jan-2022
Pack Materials-Page 1
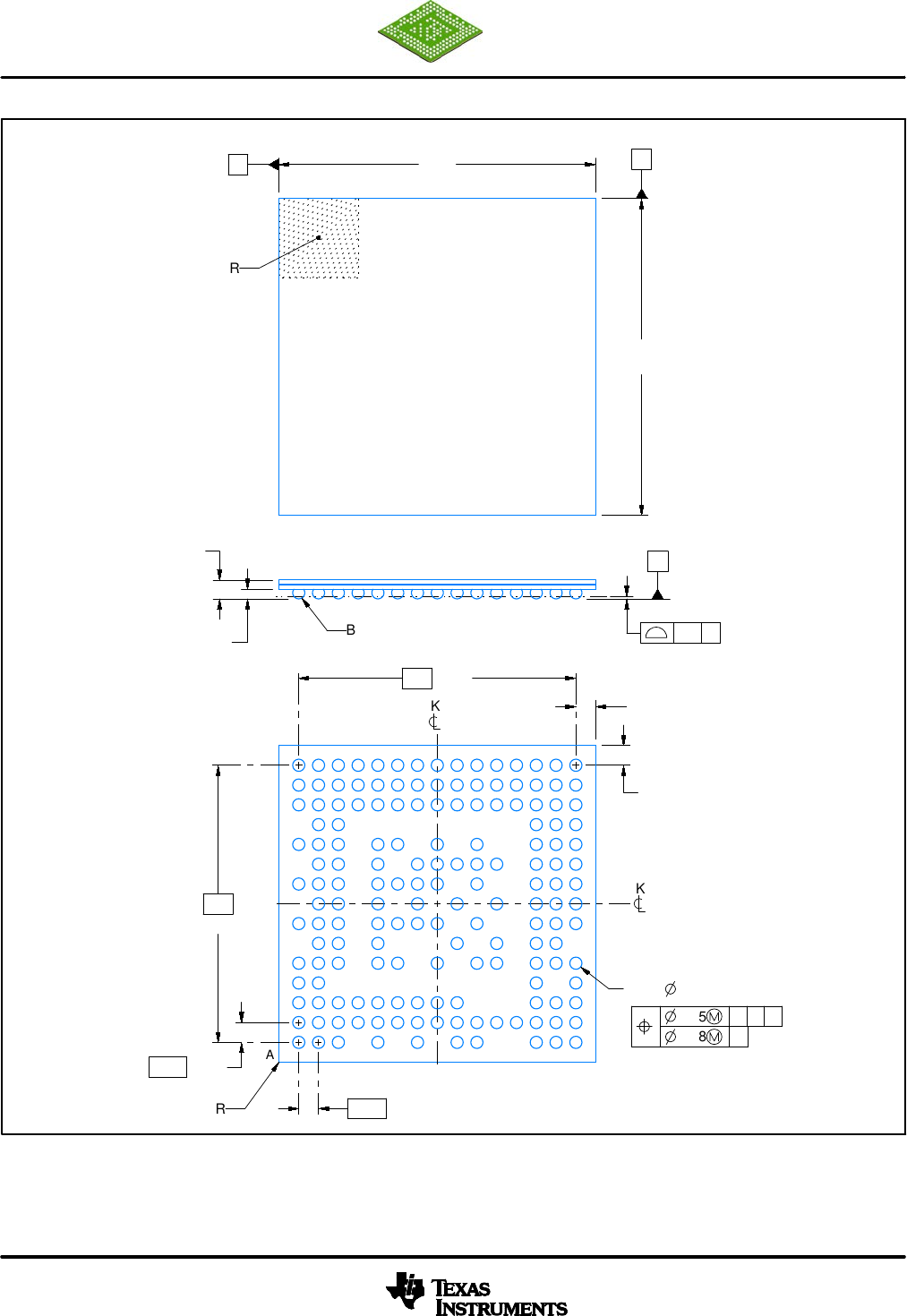
www.ti.com
PACKAGE OUTLINE
C
1.17 MAX
TYP
0.37
0.27
9.1
TYP
9.1 TYP
0.65 TYP
0.65 TYP
161X 0.45
0.35
A10.5
10.3 B
10.5
10.3
(0.65) TYP
(0.65) TYP
FCBGA - 1.17 mm max heightABL0161A
PLASTIC BALL GRID ARRAY
4222493/B 10/2016
NOTES:
1. All linear dimensions are in millimeters. Any dimensions in parenthesis are for reference only. Dimensioning and tolerancing
per ASME Y14.5M.
2. This drawing is subject to change without notice.
BALL A1 CORNER
SEATING PLANE
BALL TYP 0.1 C
0.15 C A B
0.08 C
PKG
PKG
BALL A1 CORNER
R
C
D
E
F
G
H
J
K
L
M
N
P
12345678910 11
A
B
12 13 14 15
SCALE 1.400
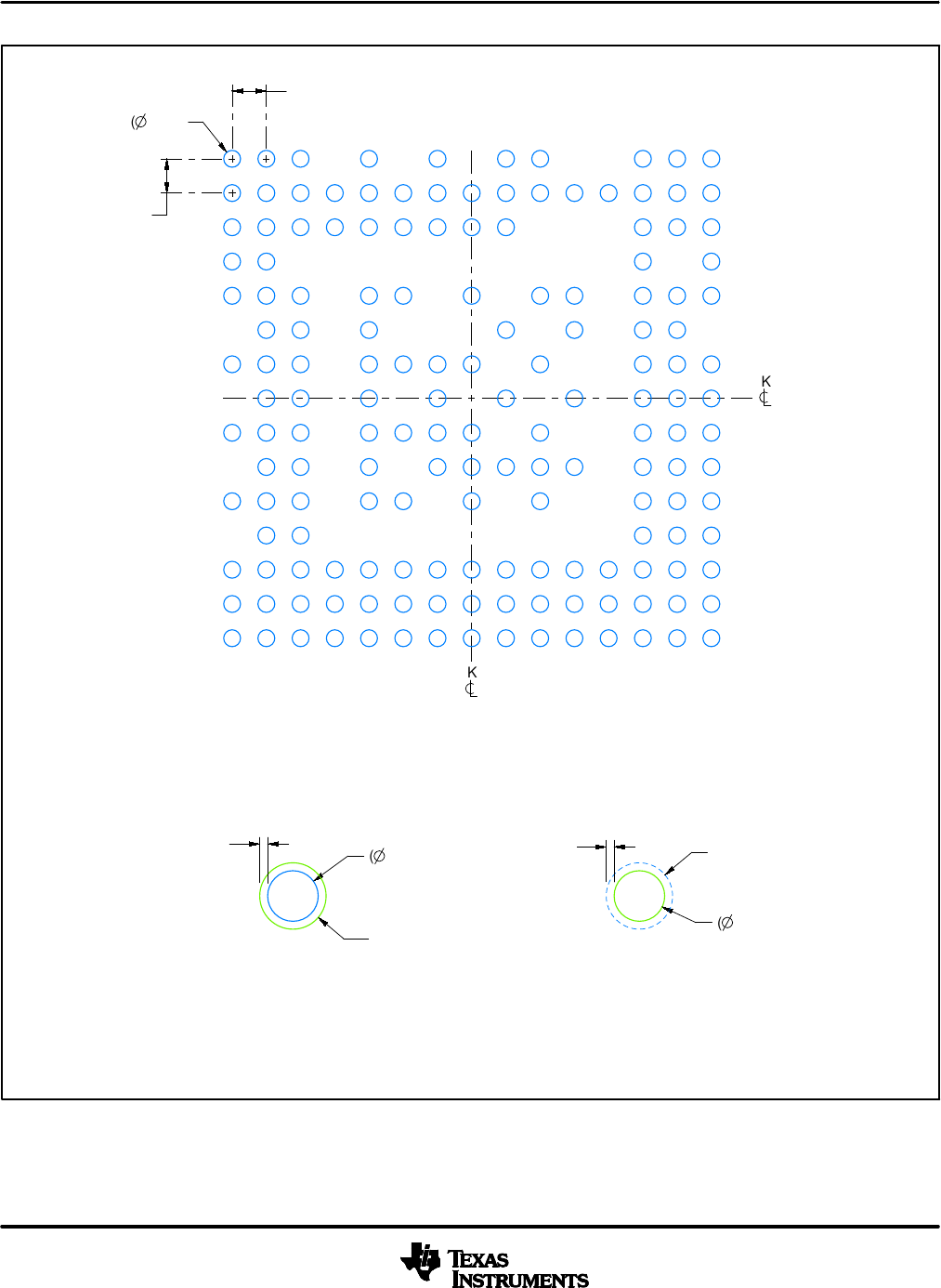
www.ti.com
EXAMPLE BOARD LAYOUT
161X ( 0.32)
(0.65) TYP
(0.65) TYP
( 0.32)
METAL
0.05 MAX
SOLDER MASK
OPENING
METAL UNDER
SOLDER MASK
( 0.32)
SOLDER MASK
OPENING
0.05 MIN
FCBGA - 1.17 mm max heightABL0161A
PLASTIC BALL GRID ARRAY
4222493/B 10/2016
NOTES: (continued)
3. Final dimensions may vary due to manufacturing tolerance considerations and also routing constraints.
For information, see Texas Instruments literature number SPRAA99 (www.ti.com/lit/spraa99).
PKG
PKG
LAND PATTERN EXAMPLE
SCALE:10X
12 3 45678910 11
A
C
D
E
F
G
H
J
K
L
M
N
P
R
B
12 13 14 15
NON-SOLDER MASK
DEFINED
(PREFERRED) SOLDER MASK DETAILS
NOT TO SCALE
SOLDER MASK
DEFINED
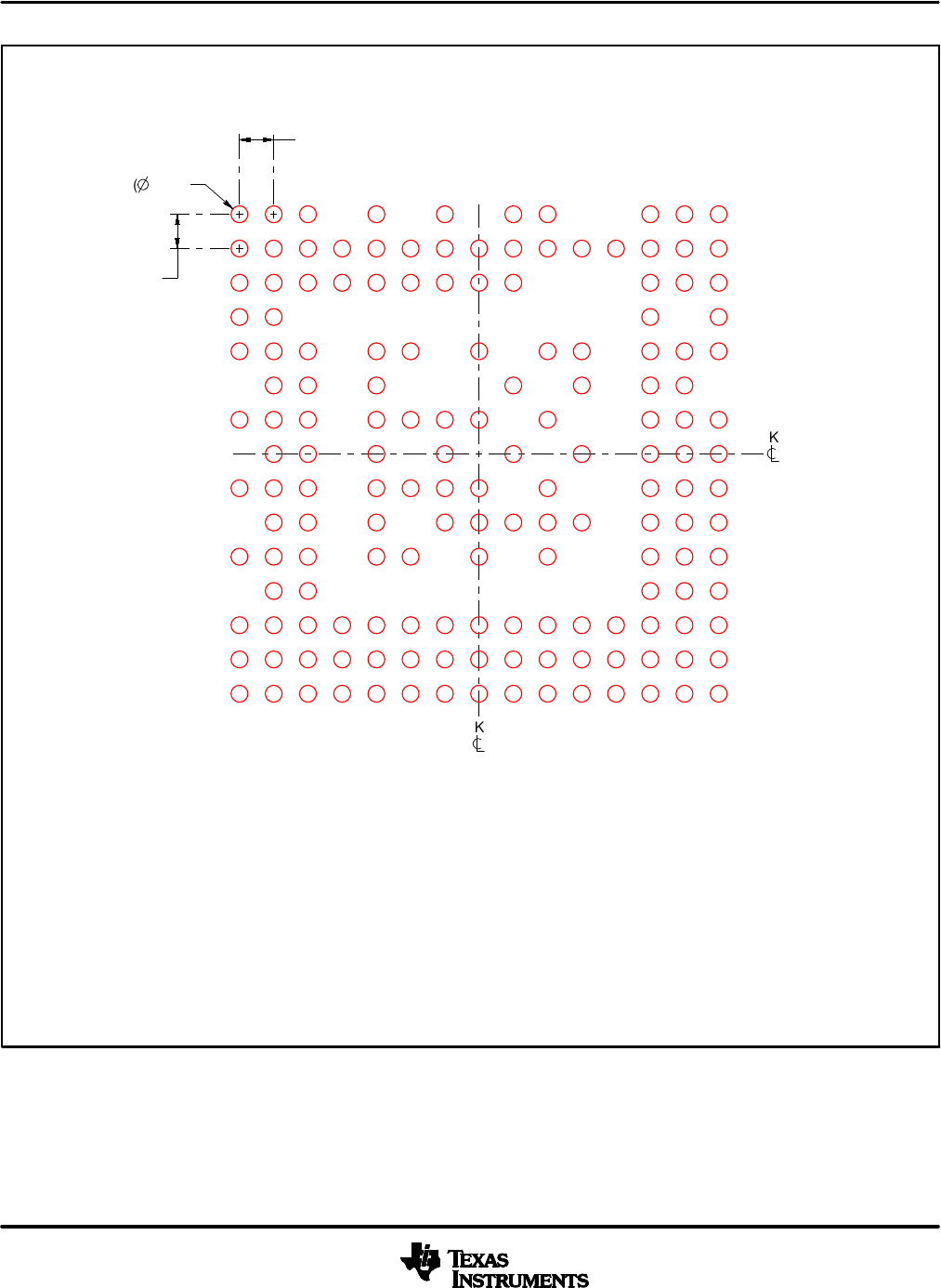
www.ti.com
EXAMPLE STENCIL DESIGN
(0.65) TYP
161X ( 0.32)
(0.65) TYP
FCBGA - 1.17 mm max heightABL0161A
PLASTIC BALL GRID ARRAY
4222493/B 10/2016
NOTES: (continued)
4. Laser cutting apertures with trapezoidal walls and rounded corners may offer better paste release.
SOLDER PASTE EXAMPLE
BASED ON 0.125 mm THICK STENCIL
SCALE:10X
PKG
PKG
12 3 45678910 11
A
C
D
E
F
G
H
J
K
L
M
N
P
R
B
12 13 14 15
IMPORTANT NOTICE AND DISCLAIMER
TI PROVIDES TECHNICAL AND RELIABILITY DATA (INCLUDING DATA SHEETS), DESIGN RESOURCES (INCLUDING REFERENCE
DESIGNS), APPLICATION OR OTHER DESIGN ADVICE, WEB TOOLS, SAFETY INFORMATION, AND OTHER RESOURCES “AS IS”
AND WITH ALL FAULTS, AND DISCLAIMS ALL WARRANTIES, EXPRESS AND IMPLIED, INCLUDING WITHOUT LIMITATION ANY
IMPLIED WARRANTIES OF MERCHANTABILITY, FITNESS FOR A PARTICULAR PURPOSE OR NON-INFRINGEMENT OF THIRD
PARTY INTELLECTUAL PROPERTY RIGHTS.
These resources are intended for skilled developers designing with TI products. You are solely responsible for (1) selecting the appropriate
TI products for your application, (2) designing, validating and testing your application, and (3) ensuring your application meets applicable
standards, and any other safety, security, regulatory or other requirements.
These resources are subject to change without notice. TI grants you permission to use these resources only for development of an
application that uses the TI products described in the resource. Other reproduction and display of these resources is prohibited. No license
is granted to any other TI intellectual property right or to any third party intellectual property right. TI disclaims responsibility for, and you
will fully indemnify TI and its representatives against, any claims, damages, costs, losses, and liabilities arising out of your use of these
resources.
TI’s products are provided subject to TI’s Terms of Sale or other applicable terms available either on ti.com or provided in conjunction with
such TI products. TI’s provision of these resources does not expand or otherwise alter TI’s applicable warranties or warranty disclaimers for
TI products.
TI objects to and rejects any additional or different terms you may have proposed. IMPORTANT NOTICE
Mailing Address: Texas Instruments, Post Office Box 655303, Dallas, Texas 75265
Copyright © 2022, Texas Instruments Incorporated