Selecting Crystals for SPC5 and STM8 Automotive MCUs
投稿人:DigiKey 北美编辑
2025-06-11
Microcontroller units (MCUs) and their associated software continue to enhance automobiles, making them smarter, safer, and more efficient. To be effective, MCUs need accurate timing sources for real-time execution, communication protocols, and general timekeeping. Despite the harsh operating environment, these time measurements must be precise, reliable, and cost-effective. Crystal oscillators are critical in ensuring accurate timing and stable operation in such applications.
Maintaining accurate timing requires crystals qualified for this vital role within the worst-case automotive environment, where there is little room for compromise. Still, few engineers master the subtleties of crystal selection, which increases the likelihood of timing errors throughout the product’s lifetime. The error risk can be mitigated using appropriate tools that streamline and simplify the selection process.
This article briefly discusses the timing issues that designers of automotive electronic systems face. It then introduces a selection tool from ECS Inc., a supplier of AEC-Q200-qualified automotive parts, and shows how it facilitates the selection and implementation of crystals for automotive MCU timing. MCUs from STMicroelectronics’ SPC5x and STM8x series are used as example targets.
Crystal oscillators
MCUs use a timebase to provide internal clocks for synchronizing operations, generating internal timing, triggering interrupts, and implementing features such as real-time operating systems. The clock timebase is a precise crystal oscillator used to assure accuracy and stability over temperature and time.
Automotive MCUs, such as the STMicroelectronics SPC5x and STM8x series, are designed with built-in oscillators that contain an inverting amplifier and a feedback resistor. The feedback resistor, connected between the input and output of the inverter, keeps it operating as a linear amplifier. A resonating element, such as a piezoelectric crystal and its related circuitry, are connected to the internal inverter to complete the oscillator (Figure 1, left).
Figure 1: A clock oscillator is created when an external crystal resonator and its associated circuitry are connected to the MCU's internal inverter and feedback resistor (left); crystals have both series and parallel resonances (right). (Image source: ECS Inc.)
The resistor, inductor, and capacitor (RLC) equivalent circuit model of the crystal consists of an inductor (L1) in series with a capacitor (C1) and a resistor (R1). In parallel with the series components is a shunt capacitor (C0), representing the input and output capacitance of the inverter, the crystal package, and the associated wiring. The series branch determines the crystal's serial resonant frequency (Fs). The parallel capacitor resonates with the serial branch, yielding the crystal’s parallel or anti-resonant frequency (Fa). The reactance plot shows both resonances (Figure 1, right); the serial resonance always occurs at a lower frequency than the parallel resonance.
Generally, the oscillator is set to a frequency between the serial and parallel resonances, where capacitive loading is used to adjust the oscillator frequency. The crystal’s specified frequency is associated with a precise load capacitance. A load capacitance greater than the crystal’s specified load will decrease the oscillator frequency, while a lower load capacitance will raise it.
The oscillator in Figure 1 is a Pierce oscillator configuration. It is composed of two branches: the active branch, which is the MCU’s internal inverter, and the passive branch that consists of the crystal and its associated components. The crystal and the capacitors C1 and C2 form a frequency-selective pi network in the feedback loop of the oscillator. The pi filter provides a 180° phase shift at the desired oscillator frequency.
Conditions for oscillator start-up
The oscillator is a feedback circuit that initiates and sustains stable oscillation. The theoretical feedback conditions for oscillator start-up are that the loop has unity gain and a phase shift of zero degrees. The crystal in the feedback loop is a passive element with associated losses. The active branch must supply negative resistance greater than the crystal's equivalent series resistance (ESR) for the oscillator to function. Crystal losses are a function of the crystal's ESR, the oscillator frequency, and the circuit's shunt and load capacitances. The ESR of a crystal can be found in its datasheet. The negative resistance of the oscillator should be at least five times the ESR.
Another approach to the oscillator startup conditions is considering its transconductance (gm), measured in milliamperes per volt (mA/V). In this case, the gain of the inverter must exceed the losses of the feedback loop. The theoretical minimum is a loop critical gain of one, but this is not a practical limit. In practice, the amplifier's gain should result in a gain margin of five times the worst-case critical gain (gmcrit). The gmcrit is the minimal transconductance of an oscillator required to maintain a stable oscillation. The critical gain is a function of the ESR, frequency, and capacitance, per the equation: gmcrit = 4 × ESR × (2pF)2 × (C0 + CL)2.
The oscillator’s transconductance can be found in the MCU’s datasheet.
As a worst-case critical gain function, Gmcrit-Max uses the same equation but enters the maximum values of each crystal parameter from the datasheet. Having the gain of the oscillator greater than five times Gmcrit-Max assures proper operation under all conditions.
Start-up performance is evaluated based on the oscillator's ability to initiate operation consistently under all environmental conditions the circuit is expected to encounter, as well as its latency, which is the time it takes to start (Figure 2).
Figure 2: The oscillator starts when unity gain is reached as VDD increases. Start-up time is measured from when VDD leaves zero volts until the oscillator stabilizes at the crystal frequency. (Image source: ECS Inc.)
Crystal drive level
Crystals dissipate power due to the current flowing through them. The drive power level is the product of the RMS current through the crystal squared, times the ESR. Crystals have a specified maximum drive level, typically stated in milliwatts (mW) or microwatts (μW). Exceeding the maximum drive level can result in unstable operation, mode jumping, reduced product lifetime, or even crystal failure. Also, if the drive level is too low, the oscillator may not start.
The drive level can be controlled by placing a resistor in series with the crystal. The resistor RS in Figure 1 is an example; it controls the current through the crystal and keeps the drive level within specification.
Crystal operating modes
The dimensions of the crystal element determine its fundamental frequency. As the thickness of the crystal element is decreased, its frequency increases. At some point, the crystal is too thin and fragile to operate reliably. This limiting frequency is about 50 megahertz (MHz).
Crystal oscillators operating at higher frequencies use crystals designed to emphasize the odd harmonics of the crystal’s fundamental frequency. These harmonic mode frequencies are referred to as overtones. Overtone crystals are designated by the harmonic number, such as third, fifth, or seventh overtone mode. These crystals have a structure that differs from that of fundamental mode crystals. Overtone oscillator designs may incorporate circuit elements, such as L-C tank circuits, to suppress the fundamental frequency and ensure operation at the desired overtone frequency.
Frequency tolerance and stability
Frequency tolerance refers to the oscillator's measured deviation from its design frequency. Tolerance is typically measured in parts per million (ppm), usually at a temperature of +25°C.
Frequency stability measures how much an oscillator's frequency changes over time or within a given temperature range. It is also measured in ppm. Numerous factors can affect crystal stability, including temperature, operating voltage, and aging, which is a slow variation in the crystal's frequency over time. Aging is measured in ppm per year. Overdriving the crystal can also degrade its stability.
To clarify, one ppm means that the frequency of a 1 MHz crystal may vary by 1 hertz (Hz), which is equivalent to 0.0001%. For example, an 8 MHz crystal with a tolerance of 30 ppm can vary in frequency by 240 Hz from its nominal frequency.
AEC-Q200 qualification
Crystals, like other passive devices intended for installation in electric vehicles, must be qualified to meet the exacting requirements imposed by that environment, including the AEC-Q200 global standard for stress resistance. Parts are deemed to be AEC-Q200 qualified if they have passed a stringent suite of stress tests, including temperature, thermal shock, moisture resistance, dimensional tolerance, resistance to solvents, mechanical shock, vibration, electrostatic discharge, solderability, and board flex, among others.
Crystal selection tool
The ECS Inc. Automotive Crystal Selector Tool provides a straightforward method for matching automotive-grade crystals with STMicroelectronics' SPC5 and STM8 automotive-qualified MCUs.
Opening the selection tool provides the designer with a list of SPC5 and STM8 MCUs, as well as ECS automotive-qualified crystals, along with a display of crystal oscillator parameters (Figure 3).
Figure 3: The home page of the Automotive Crystal Selector Tool shows lists of MCUs and crystals. (Image source: ECS Inc.)
The STMicro MCUs are listed in the blue area. The crystals appear in the white area. The process begins with the selection of an MCU, such as the SPC56AP at the top of the MCU list (Figure 4).
Figure 4: Upon selection of the SPC56AP MCU, the compatible crystals and their associated design parameters are presented. (Image source: ECS Inc.)
When the SPC56AP MCU is selected, the tool updates the crystal list to show only the crystals compatible with that MCU, along with their associated design parameters. At this point, the designer selects the desired parameters. For example, suppose a clock frequency of 8 MHz and the highest gain margin of 23.42 are desired. Making those selections reduces the crystal selection to a single part, the ECS-80-8-30Q-VY-TR crystal (Figure 5).
Figure 5: Selecting the desired crystal parameters pinpoints the ECS-80-8-30Q-VY-TR crystal. (Image source: ECS Inc.)
This 8 MHz crystal is designed to operate with an 8 picofarad (pF) capacitive load and has a tolerance of 30 ppm. Used in conjunction with the SPC56AP, it has a gmcrit of 0.17 mA/V and a gm of 4 mA/V, resulting in an actual gain margin of 23.42. The worst-case gain margin, based on Gmcrit-Max, is five.
Another example uses an STM8AF processor operating at a clock frequency of 24 MHz. This choice of inputs yields the ECS-240-8-33B2Q-CVY-TR3 (Figure 6), a 24 MHz crystal intended to operate with an 8 pF capacitive load and a frequency tolerance of 10 ppm.
Figure 6: Selecting a crystal for an STM8AF processor operating at 24 MHz results in the ECS-240-8-33B2Q-CVY-TR3. (Image source: ECS Inc.)
All of the crystals in the selection guide are AEC-200 qualified with an operating temperature range of -40 to 150°C.
Conclusion
Automotive MCUs operate in challenging environments and must be supported by appropriate clock crystals. The selection of clock crystals requires an understanding of key parameters, including frequency, temperature range, tolerance, stability, ESR, and transconductance, to ensure precision timing and stability. ECS Inc. offers a tool to help select from the wide range of AEC-Q200-qualified crystals matched to the STM8x and SPC5x series MCUs.
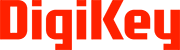
免责声明:各个作者和/或论坛参与者在本网站发表的观点、看法和意见不代表 DigiKey 的观点、看法和意见,也不代表 DigiKey 官方政策。