Analog Devices Inc./Maxim Integrated 的 PD86-1180 Short Spec 规格书
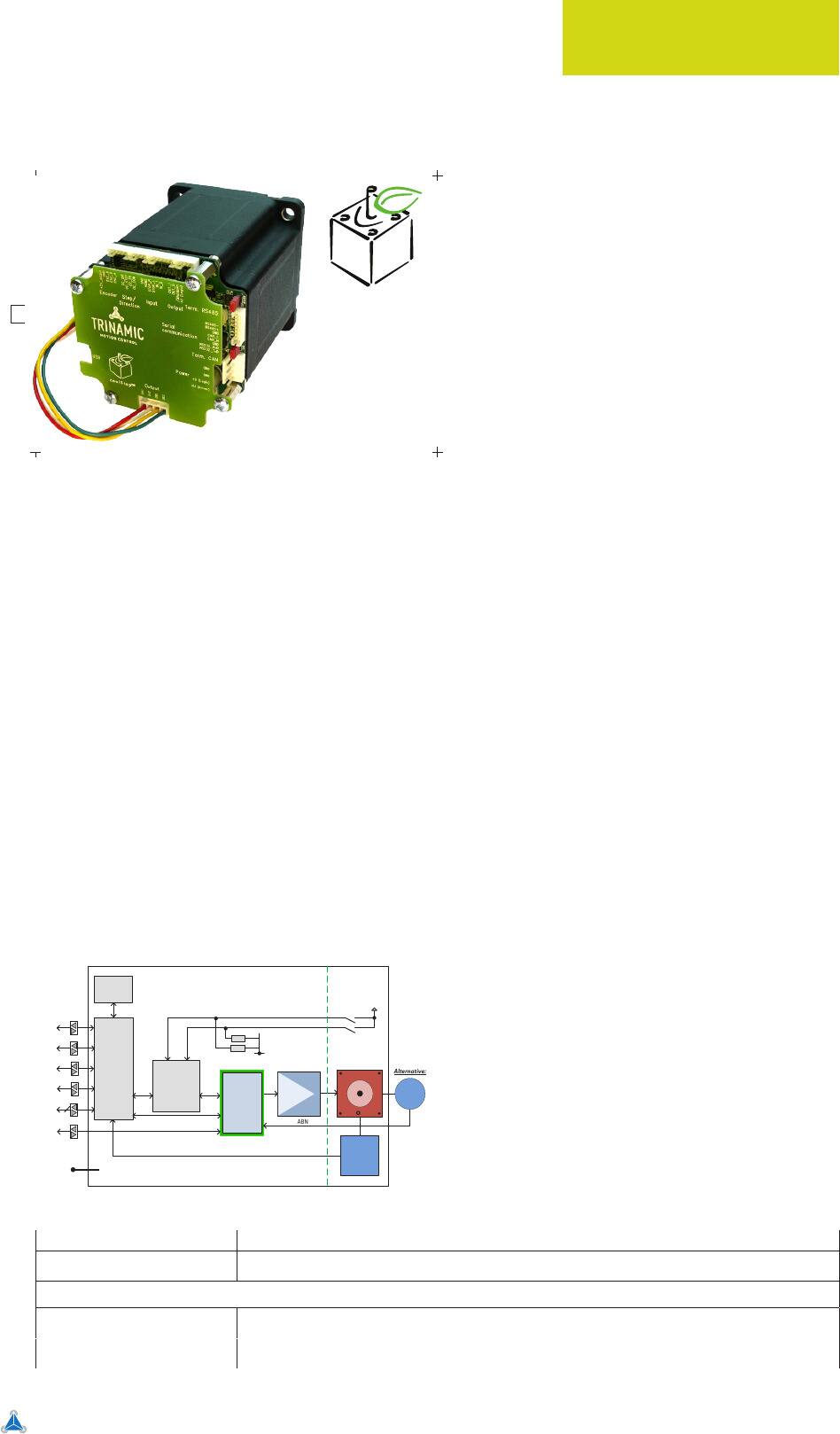
PANdrivesMECHATRONIC DRIVES WITH STEPPER MOTOR
INFO
M A IN CH A R AC T ER IS T ICS
www.trinamic.com – for detailed information and datasheets
The PANdrive PD86-1180 is a mechatronic solution including a
86mm flange motor, a controller board and a sensOstep™
encoder. It can be controlled via serial interface or operated in
stand-alone mode. Power supply, external encoder, interface and
multi purpose I/Os can be connected with JST connectors.
With the advanced stallGuard2™ feature the load of the motor
can be detected with high resolution. The new outstanding
coolStep™ technology for sensorless load dependent current
control allows energy efficient motor operation.
The PD86-1180 comes with the PC based software develop-
ment environment TMCL-IDE for the Trinamic Motion Control
Language (TMCL™). Predefined high level TMCL™ commands
guarantee a rapid development of motion control applications.
Communication traffic is kept very low since all time critical
operations, e.g. ramp calculation are performed onboard.
CANopen firmware will be available optionally.
PD86-1180
86mm / NEMA34
Stepper Motor with
Controller / Driver,
Encoder and
Serial Interface
Optional CANopen
ORDER CODE DESCRIPTION
PD86-3-1180 (-option) PANdrive 7.00 Nm, 118.5mm length with motor QSH8618-96-55-700
INTERFACE OPTIONS
TMCL with TMCL™ firmware
CANopen with CANopen firmware (under development)
TMCM-1180 and PD86-1180 Hardware Manual (V1.00 / 2010-JUN-28) 21
Copyright © 2010, TRINAMIC Motion Control GmbH & Co. KG
7 Functional description
In figure 7.1 the main parts of the PD86-1180 are shown. The PANdrive™ mainly consists of the µC
(connected to the EEPROM TMCL™ memory), the TMC428 motion controller, the TMC262A-PC power driver
with its energy efficient coolStep™ feature, the external MOSFET driver stage, the QSH8618 stepper motor,
and the integrated sensOstep™ encoder. Alternatively it is possible to connect an external encoder. Nominal
supply voltages are 24VDC or 48VDC.
18… 55V DC
µC
TMCL™
Memory
Motion
Controller
TMC428
CAN
RS232
4
add.
I/Os
Step
Motor
USB
Step/
Dir
RS485
MOSFET
Driver
Stage
Energy
Efficient
Driver
TMC262
Power
Driver
TMC262A-PC*
with
coolStep™
external
Encoder
sensOstep™
Encoder
ABN
Alternative:
Stop
Switches
+5V
ABN
PD86-1180
TMCM-1180
* TMC262A-PC is a special driver version of TMC262 for PD86-3-1180 with slightly different characteristics
Figure 7.1: Main parts of the PD86-1180
7.1 System architecture
The TMCM-1180 integrates a microcontroller with the TMCL™ (Trinamic Motion Control Language) operating
system. The motion control real-time tasks are realized by the TMC428.
7.1.1 Microcontroller
On this module, the Atmel AT91SAM7X256 is used to run the TMCL™ operating system and to control the
TMC428. The CPU has 256KB flash memory and a 64KB RAM. The microcontroller runs the TMCL™ (Trinamic
Motion Control Language) operating system which makes it possible to execute TMCL™ commands that are
sent to the module from the host via the RS232, RS485, USB, or CAN interface. The microcontroller interprets
the TMCL™ commands and controls the TMC428 which executes the motion commands. In addition it is
connected with the encoder interface and processes the inputs.
The flash ROM of the microcontroller holds the TMCL™ operating system. The TMCL™ operating system can
be updated via the RS232 interface or via the CAN interface. Use the TMCL-IDE to do this.
c o o l S t e p™
sensorless closed loop current control
load detection
ELECTRICAL
DATA • 24 to 48V DC (nom.) supply voltage
MOTOR DATA • flange size 86mm/NEMA34
• holding torque 7.0 Nm
INTERFACE • CAN, USB, RS232, RS485
• step&direction interface
• inputs for ref. & stop switches
• general purpose I/Os
• encoder interface (ABN)
FEATURES • stallGuard2™ sensorless high resolution
load detection
• coolStep™ sensorless load dependent
current control
• up to 256 times microstepping
• microPlyer™ 16 to 256 times microstepping
interpolation
• memory for 2048 TMCL commands
• motion profile calculation in hardware (RT)
• on the fly alteration of motion parameters
(e.g. position, velocity, acceleration)
SOFTWARE • stand-alone operation using TMCL™
or remote controlled operation
• PC-based application development
software TMCL-IDE included
• optional CANopen firmware (CiA 302, 402)
OTHER • pluggable JST connectors
• RoHS compliant
10 mm