Panasonic Industrial Automation Sales 的 KT Temperature Controllers 规格书
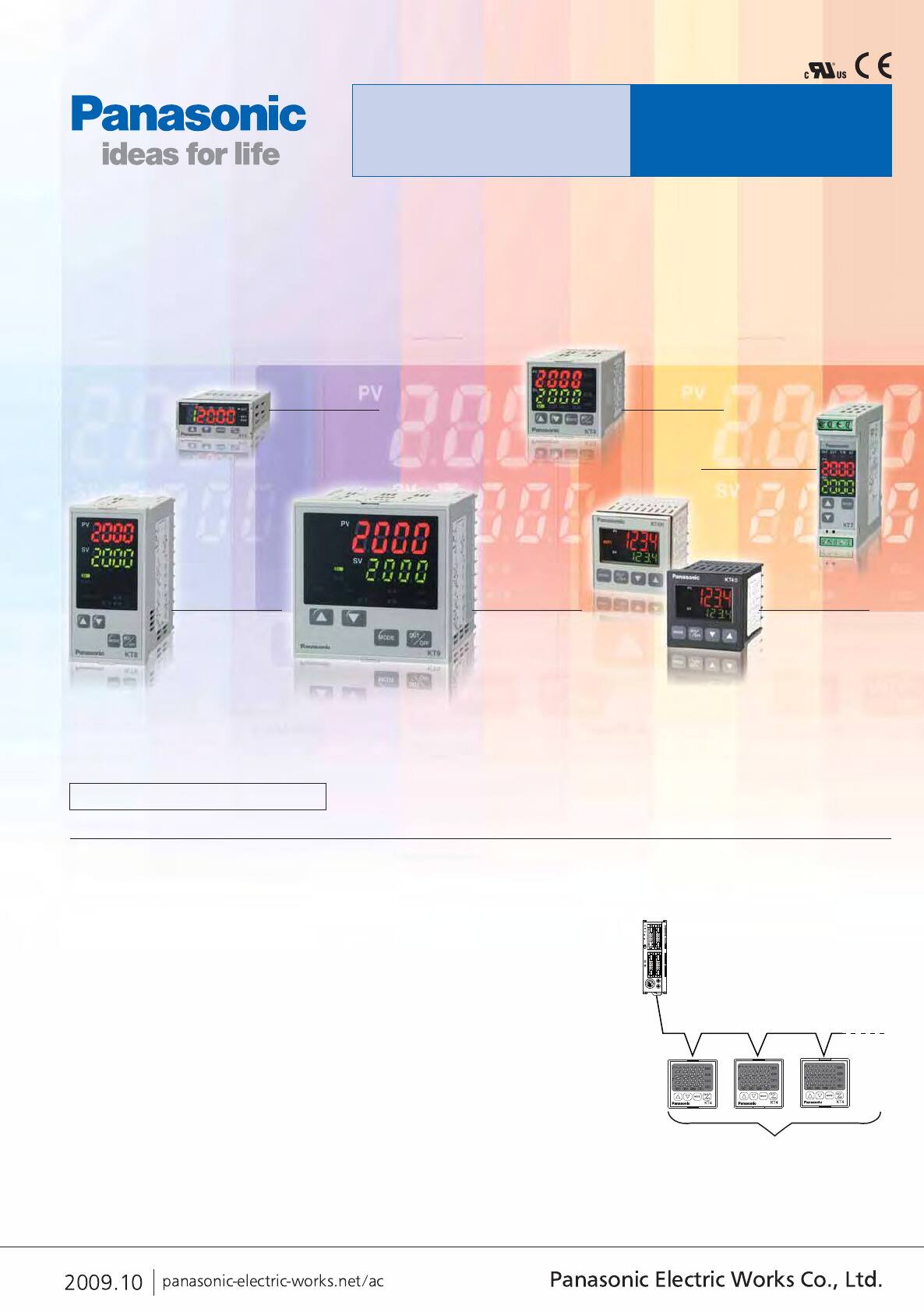
KT Temperature
Controller
KT2 Series
[48×24×98.5mm]
KT9 Series
[96×96×98.5mm]
KT8 Series
[48×96×98.5mm]
KT4H/B Series
[48×48×56mm]
KT4 Series
[48×48×95mm]
KT7 Series
[22.5×75×100mm]
KT4H
KT4B
Your Simple, Accurate and Economical
Temperature Controller
Compact temperature controller (DIN
48×24) that can support pattern control
Additions to KT2 series
Broad lineup of temperature controllers
allow you to satisfy application and space requirements.
Compliance with RoHS Directive
(Sample System Configuration)
FPΣ Programmable Controller
(Panasonic Electric Works)
Up to 31 units can be connected
RS-485
*In the configuration above, the FPΣ requires a
communication cassette (FPG-COM3).
*Modbus is a communication protocol developed for
PLCs by Modicon Inc.
FEATURES
1. Multi-input
Versatile thermocouple, RTD, DC voltage
and DC current input for temperature
detecting sensors
2. Simple operation enables highly
accurate temperature control
All required operations can be enabled
by the front keys and highly accurate PID
control mode ensures an input span of
±0.2%.
3. DIN Rail mounting types are aligned
taking global market demand into
consideration
The KT7 series is equipped with DIN rail
mounting complying to DIN standards.
Furthermore, because its control panel is
compact, the KT7 saves space.
4. Nine step pattern control possible.
For KT2 series, despite DIN 48 × 24 size,
selection is possible of control with fixed
set point and nine step pattern control.
5. Meets market demands for cost-
effectiveness
The KT series offers both economy and
high performance.
6. The KT series complies with UL,
CSA standards and CE marking.
7. Improved visibility and ease of
operation
More compact than before
The KT4H/KT4B series features the
largest PV digit size in the industry.
Visibility is improved with an 11-segment
display. Connectable to a PC, it offers a
full range of control and communication
functions.
8. Communication specification uses
RS485 (Modbus protocol)
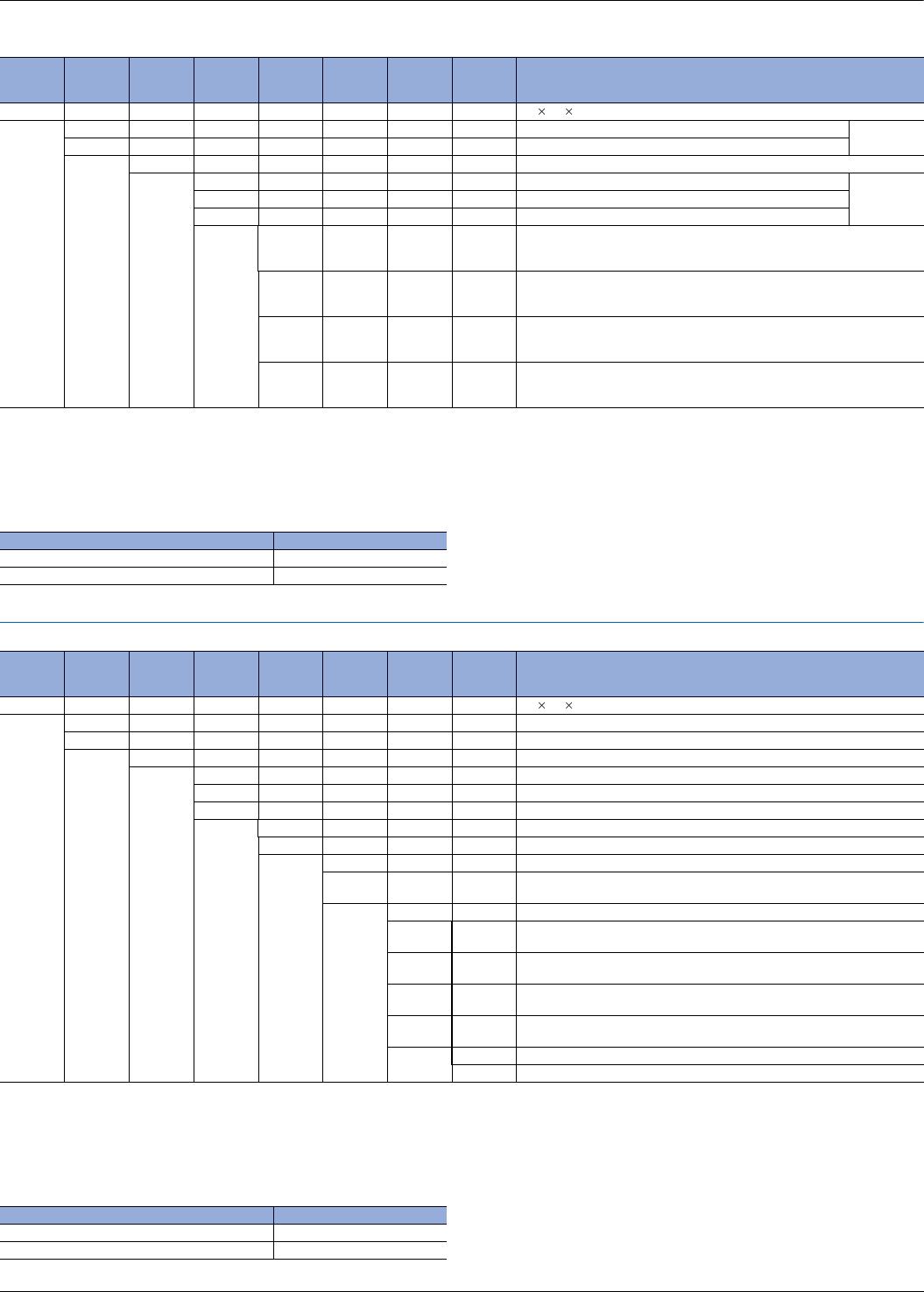
KT (AKT2,4,7,8,9,4H,4B)
2
PRODUCT TYPES
1. KT2 Series
* When heating/cooling is selected, alarm output 1 cannot be used.
When the communication function is selected, alarm output 2 cannot be used.
• Part No.
(Ex) Part No. when the optional functions (of Heating/Cooling control: relay contact output + Communications function) is added on to
the basic model are as follows; Part No.: AKT21110101
• Options
Note: When Current input is specified, a shunt resistor (sold separately) is required.
2. KT4 Series
Notes: 1. CT1 or CT2 for current detection is provided as an accessory when heater burn-out alarm function is added.
2. Event output will be shared if you choose alarm output 2 and the heater burnout alarm.
• Part No.
(Ex) Part No. when the optional functions (of Heating/Cooling control: SSR output + Communications function) is added on to the
basic model are as follows; Part No.: AKT41111401
• Options
Note: When Current input is specified, a shunt resistor (sold separately) is required.
Base
model Power
supply Sensor
input Control
output Alarm
output
Heating/
cooling
control
Heater
burnout
alarm
Commu-
nication
function Description
AKT2 48 × 24 × 98.5mm
1 100 to 240V AC Must be
specified
2 24V AC/DC
1 Multi-input (Thermocouple, RTD, DC current and DC voltage)
1 Relay contact output 1a 3A 250V AC Must be
specified
2 Non-contact voltage output (for SSR drive)
3 Current output
200Blank When both heating/cooling and communication functions are not added:
Relay contact output (alarm 1): Can be used
Open collector output (alarm 2): Can be used
110Blank When only heating/cooling function is added:
Relay contact output (alarm 1): Cannot be used
Open collector output (alarm 2): Can be used
1001
When only communication function is added:
Relay contact output (alarm 1): Can be used
Open collector output (alarm 2): Cannot be used
0101
When both heating/cooling and communication functions are added:
Relay contact output (alarm 1): Cannot be used
Open collector output (alarm 2): Cannot be used
Product name Part No.
Shunt resistor (for Current input) AKT4810
Terminal cover AKT2801
Base
model Power
supply Sensor
input Control
output Alarm
output
Heating/
cooling
control
Heater
burnout
alarm
Commu-
nications
function Description
AKT4 48 × 48 × 95mm
1 100 to 240V AC
2 24V AC/DC
1 Multi-input (Thermocouple, RTD, DC Voltage and DC Current)
1 Relay contact output 1a 3A 250V AC
2 Non-contact voltage output (for SSR drive)
3 Current output
1 Relay contact output 1a (Alarm output 1)
2 Relay contact output 1a (Alarm output 2)
0 Not available
4SSR output 0.3A 250V AC (Heating/Cooling control not supported when 2
alarm output points are selected)
0 Not available
15A (Heater burn-out alarm not supported when control output is current
output type/not supported when heating and cooling control is selected)
210A (Heater burn-out alarm not supported when control output is current
output type/not supported when heating and cooling control is selected)
320A (Heater burn-out alarm not supported when control output is current
output type/not supported when heating and cooling control is selected)
450A (Heater burn-out alarm not supported when control output is current
output type/not supported when heating and cooling control is selected)
Not available
1Available
Product name Part No.
Shunt resistor (for Current input) AKT4810
Terminal cover AKT4801

KT (AKT2,4,7,8,9,4H,4B)
3
3. KT8 Series
Notes: 1. CT1 or CT2 for current detection is provided as an accessory when heater burn-out alarm function is added.
2. If a communication function is added, second main setup is not possible
• Part No.
(Ex) Part No. when the optional functions (of Alarm output; Alarm output 2 + Heating/Cooling control: Current output) are added on to
the basic model are as follows; Part No.: AKT8111230
• Options
Note: When Current input is specified, a shunt resistor (sold separately) is required.
4. KT9 Series
Notes: 1. CT1 or CT2 for current detection is provided as an accessory when heater burn-out alarm function is added.
2. If a communication function is added, second main setup is not possible
• Part No.
(Ex) Part No. when the optional functions (of Alarm output; Alarm output 2 + Heating/Cooling control: Non-contact voltage output) are
added on to the basic model are as follows; Part No.: AKT9111220
• Options
Note: When Current input is specified, a shunt resistor (sold separately) is required.
Base
model Power
supply Sensor
input Control
output Alarm
output
Heating/cool-
ing control Heater burn-
out alarm Communica-
tions function
Description
AKT8 48 × 96 × 98.5mm
1 100 to 240V AC
2 24V AC/DC
1 Multi-input (Thermocouple, RTD, DC Voltage and DC Current)
1 Relay contact output 1a1b 3A 250V AC
2 Non-contact voltage output (for SSR drive)
3 Current output
1 Relay contact output 1a (Alarm output 1)
2 Relay contact output 1a (Alarm output 2)
0 Not available
1 Relay contact output 1a
2 Non-contact voltage output (for SSR drive)
3 Current output
0 Not available
15A (Heater burn-out alarm not supported when control output is current
output type/not supported when heating and cooling control is selected)
210A (Heater burn-out alarm not supported when control output is current
output type/not supported when heating and cooling control is selected)
320A (Heater burn-out alarm not supported when control output is current
output type/not supported when heating and cooling control is selected)
450A (Heater burn-out alarm not supported when control output is current
output type/not supported when heating and cooling control is selected)
Not available
1Available
Product name Part No.
Shunt resistor (for Current input) AKT4810
Terminal cover AKT8801
Base
model Power
supply Sensor
input Control
output Alarm
output
Heating/cool-
ing control Heater burn-
out alarm Communica-
tions function
Description
AKT9 96 × 96 × 98.5mm
1 100 to 240V AC
2 24V AC/DC
1 Multi-input (Thermocouple, RTD, DC Voltage and DC Current)
1 Relay contact output 1a1b 3A 250V AC
2 Non-contact voltage output (for SSR drive)
3 Current output
1 Relay contact output 1a (Alarm output 1)
2 Relay contact output 1a (Alarm output 2)
0 Not available
1 Relay contact output 1a
2 Non-contact voltage output (for SSR drive)
3 Current output
0 Not available
15A (Heater burn-out alarm not supported when control output is current
output type/not supported when heating and cooling control is selected)
210A (Heater burn-out alarm not supported when control output is current
output type/not supported when heating and cooling control is selected)
320A (Heater burn-out alarm not supported when control output is current
output type/not supported when heating and cooling control is selected)
450A (Heater burn-out alarm not supported when control output is current
output type/not supported when heating and cooling control is selected)
Not available
1Available
Product name Part No.
Shunt resistor (for Current input) AKT4810
Terminal cover AKT9801
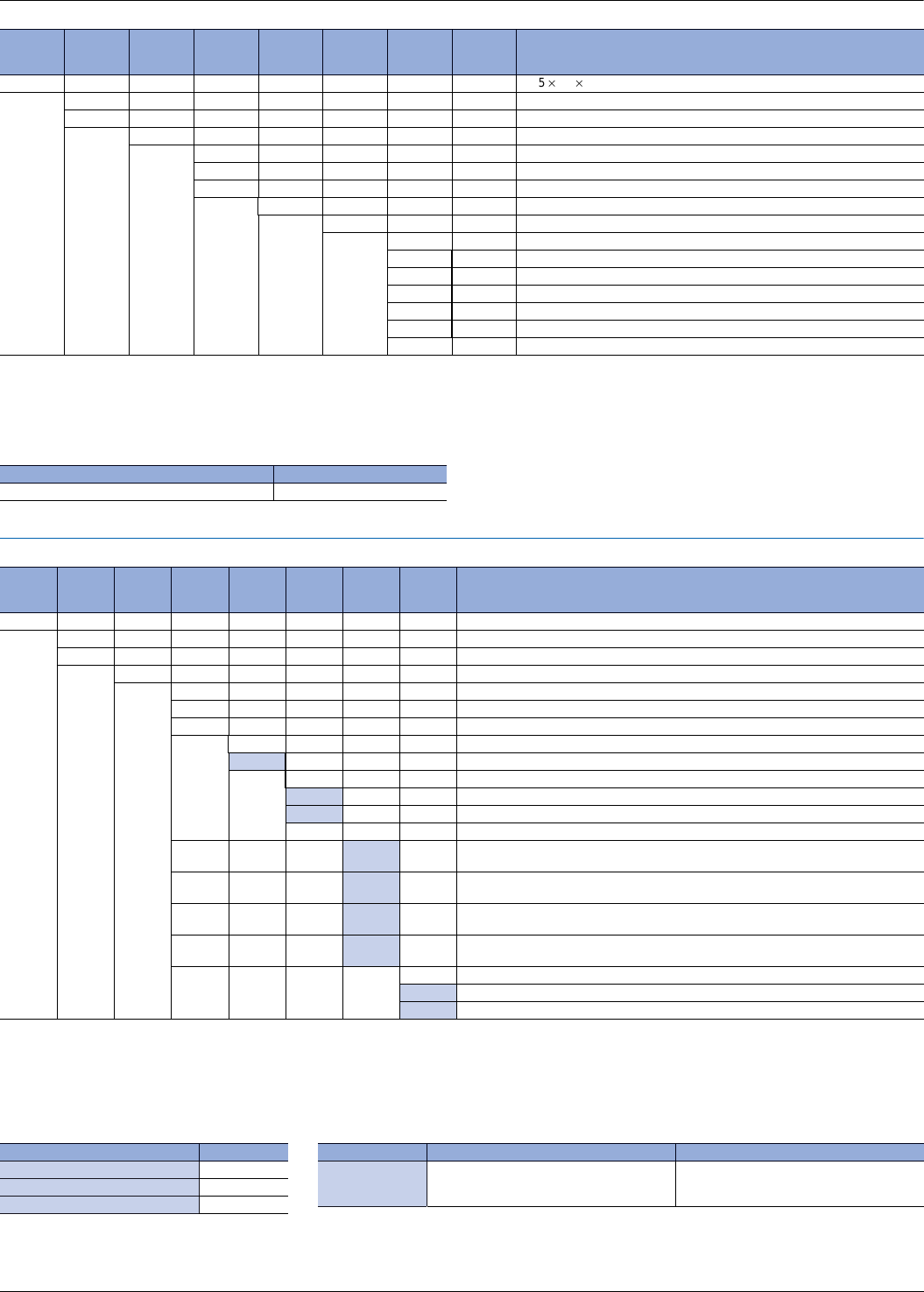
KT (AKT2,4,7,8,9,4H,4B)
4
5. KT7 Series
Note: CT1 or CT2 for current detection is provided as an accessory when heater burn-out alarm function is added.
• Part No.
(Ex) Part No. when the optional function (of Heater burnout alarm: 10A) is added on to the base model are as follows;
Part No.: AKT7111102
• Options
Note: When Current input is specified, a shunt resistor (sold separately) is required.
6. KT4H Series
Notes: 1. CT1 or CT2 for current transformer is provided as an accessory when heater burn-out alarm function is added.
2. Under some conditions, option functions (shaded items) may not be available; please check the “Descriptions” of the above table for non-functioning circumstances.
• Part No.
(Ex) Part No. when the optional functions (Heating/Cooling control + communication function) are added on to the basic model are as
follows; Part No.: AKT4H1111101
Base
model Power
supply Sensor
input Control
output Alarm
output
Heating/
cooling
control
Heater
burnout
alarm
Commu-
nications
function Description
AKT7 22.5 × 75 × 100mm
1 100 to 240V AC
2 24V AC/DC
1 Multi-input (Thermocouple, RTD, DC Voltage and DC Current)
1 Relay contact output 1a 3A 250V AC
2 Non-contact voltage output (for SSR drive)
3 Current output
1 Open collector output (Alarm output 1)
0 Not available (without Heating/Cooling function)
0 Not available
1 5A (not available for the Current output type) Open collector output
2 10A (not available for the Current output type) Open collector output
3 20A (not available for the Current output type) Open collector output
4 50A (not available for the Current output type) Open collector output
Not available
1Available
Product name Part No.
Shunt resistor (for Current input) AKT4811
Base
model Power
supply Sensor
input Control
output Alarm
output
Heating/
cooling
control
Heater
burnout
alarm
Commu-
nications
function
Description
AKT4H 1 100 to 240V AC
2 24V AC/DC
1 Multi-input (Thermocouple, RTD, DC Voltage and DC Current)
1 Relay contact
2 Non-contact voltage (for SSR drive)
30DC current
Heater burn-out alarm not possible.
11 point (1a)
20 2 points (1a + 1a)
Heating/cooling control output not possible.
0 Not available
10 Relay contact
Heater burn-out alarm not possible.
20 Non-contact voltage (for SSR drive)
Heater burn-out alarm not possible.
0 Not available
1 or 2 0 3 Single phase 20A (Heater burn-out alarm not supported when control output is DC
output type/not supported when heating and cooling control is selected)
1 or 2 0 4Single phase 50A (Heater burn-out alarm not supported when control output is DC
output type/not supported when heating and cooling control is selected)
1 or 2 0 5Three phase 20A (Heater burn-out alarm not supported when control output is DC
output type/not supported when heating and cooling control is selected)
1 or 2 0 6Three phase 50A (Heater burn-out alarm not supported when control output is DC
output type/not supported when heating and cooling control is selected)
Blank Not available
1 Serial communication RS-485
2 Contact input
• Options
Product name Part No.
Shunt resistor (for Current input) AKT4810
Terminal cover AKT4H801
Tool cable AKT4H820
• Setting software
Note: Please download user manual from the company website.
Product name Description Remark
KT Monitor Editing of all types of data, File saving
Monitoring of readings, Saving of log files
Available for download at no charge from
company website.
http://www.panasonic-electric-works.net/ac
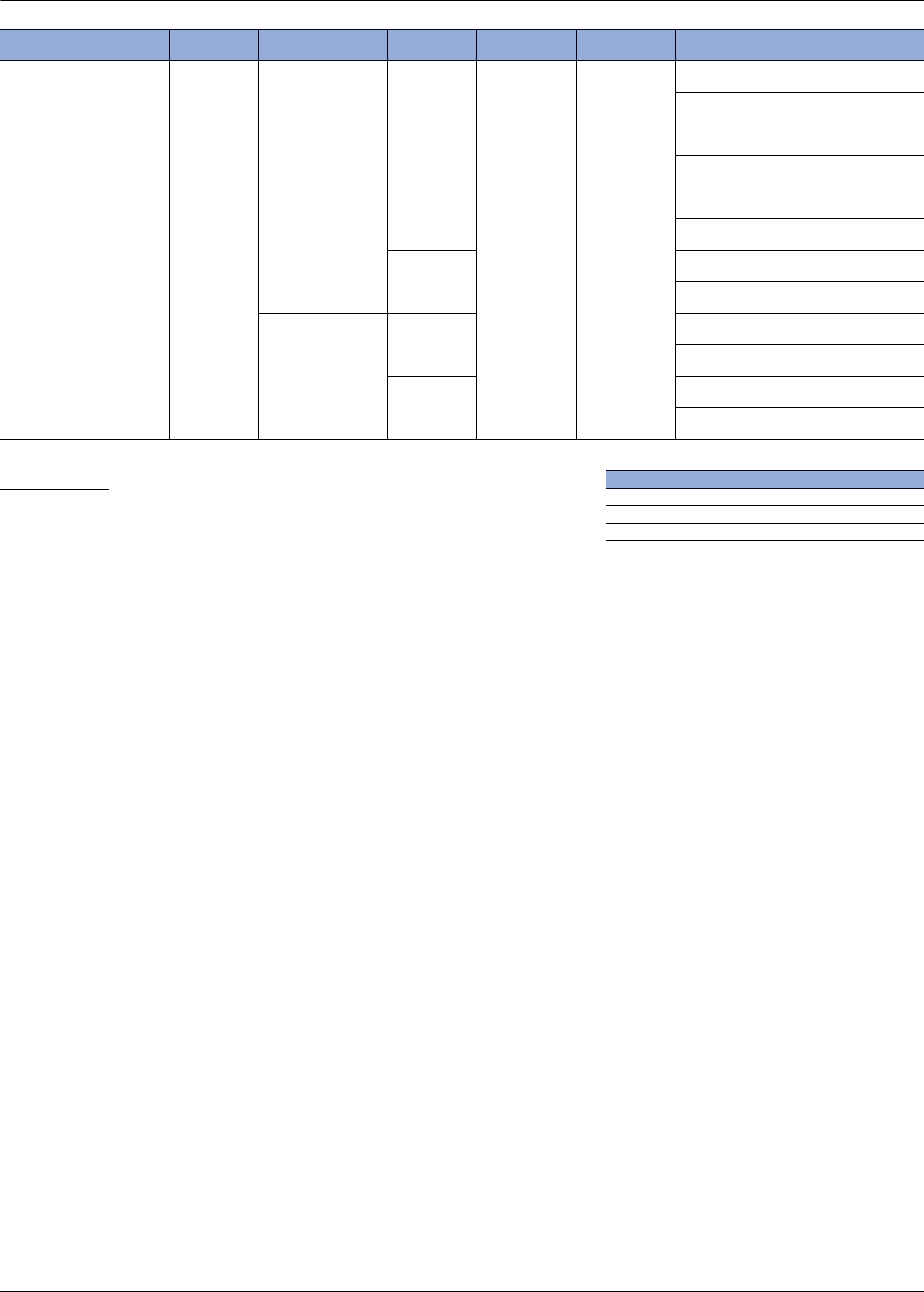
KT (AKT2,4,7,8,9,4H,4B)
5
7. KT4B Series
Base
model Power supply Sensor input Control output Alarm output Heating/cooling
control Heater burnout
alarm Communications
function Model No.
AKT4B 1
(100 to 240V AC) 1
(Multi-input)
1
(Relay contact)
1
(1 point)
0
(Not available) 0
(Not available)
Blank
(Not available) AKT4B111100
1
(Serial communication) AKT4B1111001
2
(2 points)
Blank
(Not available) AKT4B111200
1
(Serial communication) AKT4B1112001
2
(Non-contact voltage)
1
(1 point)
Blank
(Not available) AKT4B112100
1
(Serial communication) AKT4B1121001
2
(2 points)
Blank
(Not available) AKT4B112200
1
(Serial communication) AKT4B1122001
3
(DC current)
1
(1 point)
Blank
(Not available) AKT4B113100
1
(Serial communication) AKT4B1131001
2
(2 points)
Blank
(Not available) AKT4B113200
1
(Serial communication) AKT4B1132001
*Please inquire if you need specifications not included in the model numbers above.
*Use RS485 for serial communication.
Example Model No.: AKT4B111100
Specifications: Power supply 100 to 240V AC, Heating/cooling control: Not available,
Sensor input: Multi-input, Heater burnout alarm: Not available,
Control output: Relay contact, Communications function: Not available,
Alarm output: 1 point
• Options (Common for KT4H and KT4B)
Product name Model No.
Shunt resistor (for Current input) AKT4810
Terminal cover AKT4H801
Tool cable AKT4H820
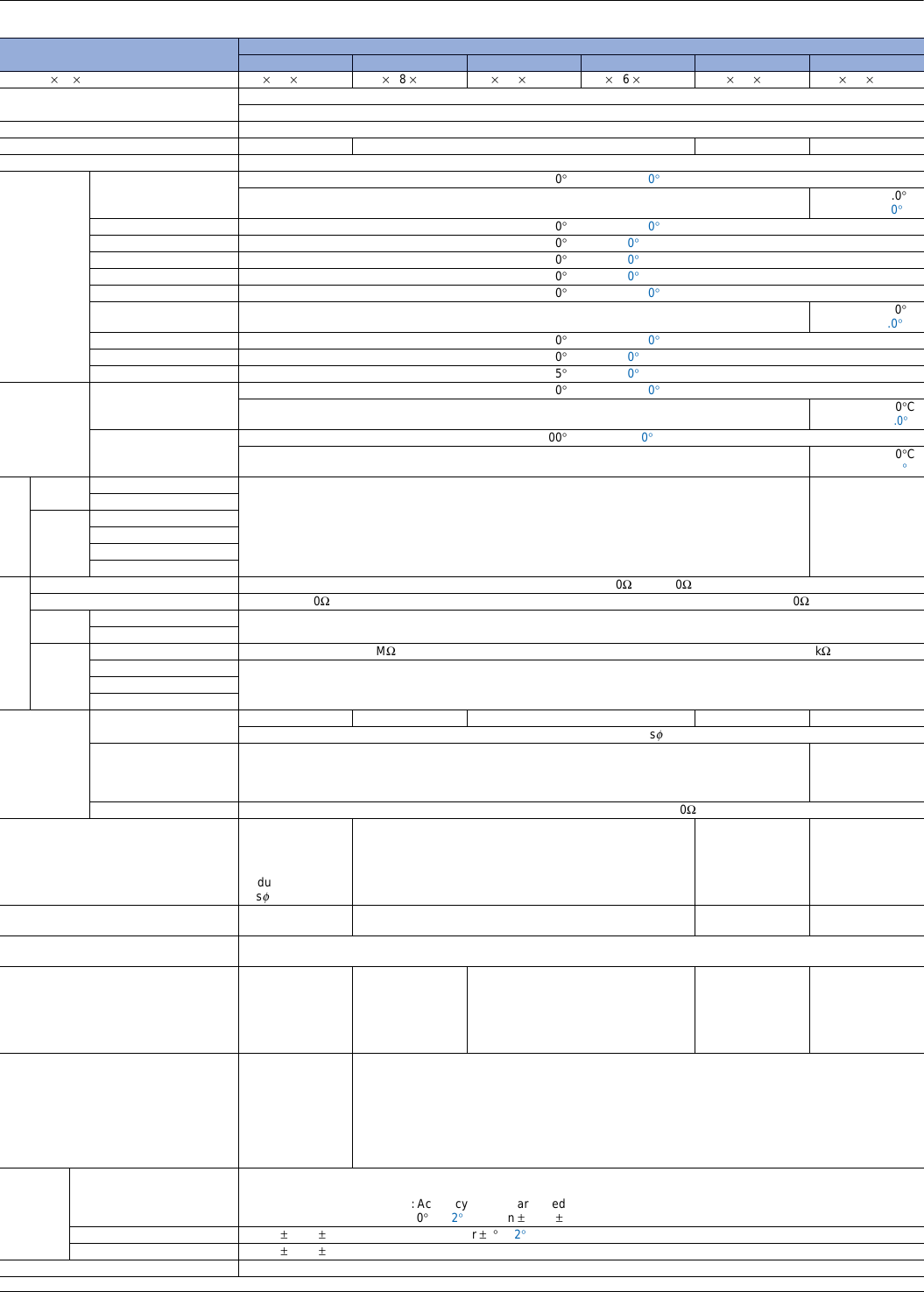
KT (AKT2,4,7,8,9,4H,4B)
6
RATING & SPECIFICATIONS
Display Specifications
KT2 KT4 KT8 KT9 KT7 KT4H/4B
Size (W × H × D) 48 × 24 × 98.5mm 48 × 48 × 95mm 48 × 96 × 98.5mm 96 × 96 × 98.5mm 22.5 × 75 × 100mm 48 × 48 × 62mm
Supply voltage (Must be specified) 100 to 240V AC
24V AC/DC
Frequency 50/60Hz
Power consumption Approx. 5VA Approx. 8VA Approx. 6VA Approx. 8VA
Input type Input range
Thermocouple
K–200 to 1370°C (–320 to 2500°F)
–199.9 to 400.0°C (–199.9 to 750.0°F)–200.0 to 400.0°C
(–320 to 750.0°F)
J –200 to 1000°C (–320 to 1800°F)
R 0 to 1760°C (0 to 3200°F)
S 0 to 1760°C (0 to 3200°F)
B 0 to 1820°C (0 to 3300°F)
E –200 to 800°C (–320 to 1500°F)
T –199.9 to 400.0°C (–199.9 to 750.0°F)–200.0 to 400.0°C
(–320 to 750.0°F)
N –200 to 1300°C (–320 to 2300°F)
PL-II 0 to 1390°C (0 to 2500°F)
C (W/Re5-26) 0 to 2315°C (0 to 4200°F)
RTD
Pt100 –200 to 850°C (–300 to 1500°F)
–199.9 to 850.0°C (–199.9 to 999.9°F)–200.0 to 850.0°C
(–320.0 to 1500.0°F)
JPt100 –200 to 500°C (–300 to 900°F)
–199.9 to 500.0°C (–199.9 to 900.0°F)–200.0 to 500.0°C
(–320.0 to 900.0°F)
DC
Current 4 to 20mA DC –1999 to 9999, –199.9 to 999.9
–19.99 to 99.99, –1.999 to 9.999
• Scaling and change to the decimal point position is possible for DC current and DC voltage input.
• DC current input is supported with an externally mounted 50Ω shunt resistor (sold separately).
–2000 to 10000
0 to 20mA DC
Voltage
0 to 1V DC
0 to 10V DC
1 to 5V DC
0 to 5V DC
Multi-input
Thermocouple K, J, R, S, B, E, T, N, PL-II, C (W/Re5-26) External resistor: Max. 100Ω (max. 40Ω external resistor for B input)
RTD Pt100, JPt100Ω 3-conductor system (Allowable input conductor resistance for each conductor: max. 10Ω)
DC
current 0 to 20mA DC Input impedance: 50Ω (Connect 50Ω shunt resistor between input terminals.)
Allowable input current: max. 50 mA (when 50Ω shunt resistor is used)
4 to 20mA DC
DC
voltage
0 to 1V DC Input impedance: min. 1 MΩ, Allowable input voltage: max 5 V, Allowable signal source resistance: max. 2 kΩ
0 to 5V DC Input impedance: min. 100 kΩ, Allowable input voltage: max 15 V, Allowable signal source resistance: max. 100Ω1 to 5V DC
0 to 10V DC
Control output
(Must be
specified)
Relay contact (contact
material: silver alloy) 1a 1a 1a1b 1a 1a
3A 250V AC (Resistive load), 1A 250V AC (Inductive load cos
φ
=0.4), Electric life: 100,000 times
Non-contact DC voltage 12 V DC, Max. load current: 40mA (Short-circuit protected)
12V DC ±15%,
Max. load current:
40mA (Short-
circuit protected)
DC current 4 to 20mADC Load resistance: Max. 550Ω
Alarm output 1 (EVT1)
Relay contact
(Contact material: Ag alloy)
Relay contact 1a
3A 250V AC
(Resistive load),
1a 1A 250V AC
(Inductive load
cos
φ
=0.4)
Relay contact 1a 3A 250VAC (Resistive load)
Electric life: 100,000 times
Open collector,
Control capacity:
24V DC 0.1A
(Max.)
Relay contact 1a:
3A 250VAC
(Resistive load)
Electric life:
100,000 times
Alarm output 2 (EVT2) Open collector
0.1A 24V DC The same as the one of Alarm output 1 None Same as
Alarm output 1
Control mode Actions mentioned below can be selected by key operation. [Default PID] PID (with auto-tuning function), PI, PD (with manual
reset function), P (with manual reset function), ON/OFF action
Target temperature setting
Primary setting/
secondary setting
(switched by
external terminal)
—Primary setting/secondary setting
(switched by external terminal) —
Primary setting/
secondary setting/
third setting/fourth
setting (switched
by external
terminal)
Program control function
1 pattern, 9 step
setting is possible
(However, make
function selection
setting of either
control with fixed
set point or
program control.)
—
Accuracy Thermocouple
Within ±0.2% ±1 digit of each input span or within ±2°C (4°F) whichever is greater
However, R and S input; Within ±6°C (12°F) in the range of 0 to 200°C (0 to 400°F)
B input 0 to 300°C (0 to 600°F): Accuracy is not guaranteed.
K, J, T, E, and N input less than 0°C (32°F): Within ±0.4% ±1 digit of input span
RTD Within ±0.1% ±1 digit of each input span or ±1°C (2°F) whichever is greater
DC current and DC voltage Within ±0.2% ±1 digit of each input span
Sampling period 250ms
+2
0

KT (AKT2,4,7,8,9,4H,4B)
7
Display Specifications
KT2 KT4 KT8 KT9 KT7 KT4H/4B
Hysteresis (ON/OFF) Thermocouple & RTD: 0.1 to 100.0°C (32.18 to 212°F)
DC current and DC voltage: 1 to 1000 (The decimal point place follows the selection)
Proportional band
For sensor input
range and DC
current,
DC voltage
0.0 to 110.0%
Thermocouple: 0 to 1000°C (0 to 2000°F)
RTD: 0.0 to 999.9°C (0.0 to 999.9°F)
DC current and DC voltage: 0.0 to 100.0%
For sensor input
range and DC
current,
DC voltage
0.0 to 110.0%
0 to 1000°C
(32 to 1832°F)
The decimal point
input: 0.0 to 1000°C
(32 to 1832°F)
DC current and DC
voltage: 0.0 to
100.0%
Integral time 0 to 1000 seconds
Derivative time 0 to 300 seconds
Proportional cycle 1 to 120 seconds
Allowable voltage fluctuation When 100 to 240V AC; 85 to 264V AC When 24V AC/DC; 20 to 28V AC/DC
Insulated resistance 500V DC 10MΩ or greater
Breakdown voltage
1.5kV AC for 1 min
between input
terminal and power
terminal, & between
output terminal and
power terminal
1.5kV AC for 1min between input terminal and ground terminal,
between input terminal and power terminal
between power terminal and ground terminal
between output terminal and ground terminal, & between output
terminal and power terminal
1.5kV AC for 1 min
between input terminal and power terminal,
& between output terminal and power
terminal
Malfunction vibration 10 to 55 Hz (0.35 mm) to each direction (120ms sweep) for 10 min.
10 to 55 Hz
(1 cycle/min.)
single amplitude
0.35 mm
(10 min. on 3 axes)
Breakdown vibration 10 to 55 Hz (0.75 mm) to each direction (120ms sweep) for 10 min.
10 to 55 Hz
(1 cycle/min.)
single amplitude
0.75 mm
(1 hour on 3 axes)
Malfunction shock X, Y & Z each direction for 5 times 98m/s2 (10G)
Breakdown shock Same as above, but 294m/s2 (30G)
Ambient temperature 0 to 50°C
Ambient humidity 35 to 85%RH (No condensation)
Mass Approx. 120g Approx. 130g Approx. 240g Approx. 370g Approx. 150g Approx. 120g
Waterproof IP66 (applicable only to the front panel subject to rubber gasket employed) None
IP66 (applicable only
to the front panel
subject to rubber
gasket employed)
Display character height PV: 8.7mm,
SV: 8.7mm (PV/SV
switching display)
PV: 10.2mm
SV: 8.8mm PV: 11.2mm
SV: 11.2mm PV: 18mm
SV: 13.2mm PV: 7.4mm
SV: 7.4mm PV: 12mm
SV: 6mm
Options
Heating/Cooling
control
(Relay contact
material: silver
alloy)
Relay contact:
1a 3A 250V DC
(Resistive load)
Non contact relay
0.3A 250V AC
(Resistive load)
• Relay contact:
1a 250V AC 3A (Resistive load),
250V AC 3A (Inductive load cosø=0.4),
Electric life: 100,000 times
• Non-contact voltage:
12 V DC Max. 40mA
(Short-circuit protected)
• DC current: 4 to 20mA DC
Load resistance: Max. 550Ω
None
Relay contact:
Control capacity 1a:
3A 250V AC
(Resistive load),
Electric life: 100,000
times
Non-contact voltage:
12V DC±15% Max.
40mA (Short-circuit
protected)
Heater burn-out
alarm output
(Relay contact
material: silver
alloy)
—
Heater rated current must be selected from 5A, 10A, 20A and 50A.
Setting accuracy: Within 5% of heater rated current
Relay contact 1a 250V AC 3A (Resistive load), Electric life:
100,000 times
Open collector,
Control capacity:
24V DC 0.1A (Max.)
Specify either single-
phase 20 A, single-
phase 50 A, 3-phase
20 A, or 3-phase
50 A for rated heater
current.
Setting accuracy:
within ±5% of rated
heater current
Relay contact 1a: 3A
250V AC (Resistive
load), Electric life:
100,000 times
Communication
function RS-485/Modbus Protocol (Modbus is a communication protocol developed for PLCs by Modicon Inc.)
Communication speed: 2400/4800/9600/19200bps
Tool port —
Communication
interface
C-MOS level
Cannot be used at
the same time as
serial communica-
tion (option).
*This port can only
be used with the tool
cable (AKT4H820).
Accessories Mounting frame Included with unit Not available Included with unit
Terminal cover Sold separately Not available Not available
Rubber gasket Not available Included with unit
+2
0

KT (AKT2,4,7,8,9,4H,4B)
8
COMMUNICATION FUNCTION OVERVIEW
Note: That main setting No. 2 will not be possible on the KT8 and KT9 when the communications functions is added.
PARTS AND FUNCTIONS
1. KT2 series
Item Specification
KT2, 4, 8, 9, 7 KT4H/4B
Communication type Half-duplex
Communication speed Select 2400, 4800, 9600, or 19200 bps using key operation.
Synchronization type Asynchronous
Protocol Modbus Modbus RTU, Modbus ASCII, MEWTOCOL (Slave)
Coding ASCII Binary/ASCII
Error correcting Command re-send
Error detection Parity check, check sum
Data structure Start bit: 1, Data bit: 7, Parity: Even parity, Stop bit: 1
Interface EIA RS485 compliant
No. of nodes 31
Maximum cable length 1,000 m (cable resistance must be within 50Ω)
PV/SV display (red): Indicates the input value and setting value. During setting mode, characters
and setting value of the setting item are indicated in turn.
MEMO/STEP display (green): Indicates memory number during fixed value control. Indicates step number
during program control.
PV indicator (red): Lights up when the input value (PV) is indicated.
SV indicator (green): Lights up when main setting value (SV) is indicated.
AT indicator (yellow): Flashes during AT (auto-tuning).
T/R indicator (yellow): Flashes during serial communication (Lit while sending data, Unlit while
receiving data)
OUT indicator (green): Lights up when control output or OUT1 (Heating side, option Heating/Cooling
control) is ON. (For DC current output type, it flashes corresponding to the
manipulated variable in a 0.25 second cycle)
EV1 indicator (red): Lights up when Event output 1 or OUT2 (Cooling side, option Heating/Cooling
control) is ON.
EV2 indicator (red): Lights up when Event output 2 is ON.
Increase key ( ): Increases the numeric value.
Decrease key ( ): Decreases the numeric value.
Mode key ( ): Selects the setting mode or registers the setting value.
(By pressing the Mode key, the setting value or selected value can be
registered)
OUT/OFF key ( ): The control output OUT/OFF or program control RUN/STOP can be switched.
1
2
3
4
5
6
7
8
9
10
11
12
13
OFF
MODE
OUT
1
2
3456
11 12 13
7
8
9
10

KT (AKT2,4,7,8,9,4H,4B)
9
6. KT4H/4B series
2. KT4 series 3. KT8 series
1
2
3
6
45
1
2
3
6
45
4. KT9 series 5. KT7 series
1
2
3
54 6
1
2
35
4
Note: Color selection is the same for each size.
1PV display
Indicates PV (process variable).
2SV display
Indicates SV (setting value).
3Increase key
Increases numerical value.
4Decrease key
Decreases numerical value.
5Mode key
Switches the setting mode.
6OUT/OFF key
Control output is turned on or off when
control output is ON.
(Bottom side)
3
9
4
7
8
1
2
5
6
1 Action indicators (backlight: orange)
°F °C ..................... Lights respectively when temperature unit °F/°C is selected.
T/R ........................ Lights during Serial communication (option) TX output.
AT ......................... Flashes during auto-tuning or auto-reset
OUT1 .................... Lights when control output is ON or Heating output (option) is
ON.
For DC current output type, it flashes corresponding to the
manipulated variable in 0.25 second cycles.
OUT2 .................... Lights when Cooling output (option) is ON.
EVT1 ..................... Lights when Alarm 1 output is ON.
EVT2 ..................... Lights when Alarm 2 output (option) is ON or Heater burnout
alarm (option) is ON.
LOCK .................... Lights when Lock 1, Lock 2 or Lock 3 is selected.
2 MEMO display ....... Indicates the set value memory number (backlight: green).
3 PV display ............. Indicates the PV (process variable) (backlight: red/orange/green).
4 SV display ............. Indicates the SV (set value) (backlight: green).
5 Mode key ............... Selects the setting mode, and registers the set value.
6 OUT/OFF key ........ The control output ON/OFF or Auto/Manual control can be
switched.
7 Increase key .......... Increases the numeric value.
8 Decrease key ........ Decreases the numeric value.
9 Tool connector ....... By connecting the tool cable, the following operations can be
conducted from the external computer using the exclusive tool
software.
- Reading and setting of SV, PID and various set values from
external computer
- Reading of PV and action status
- Function change
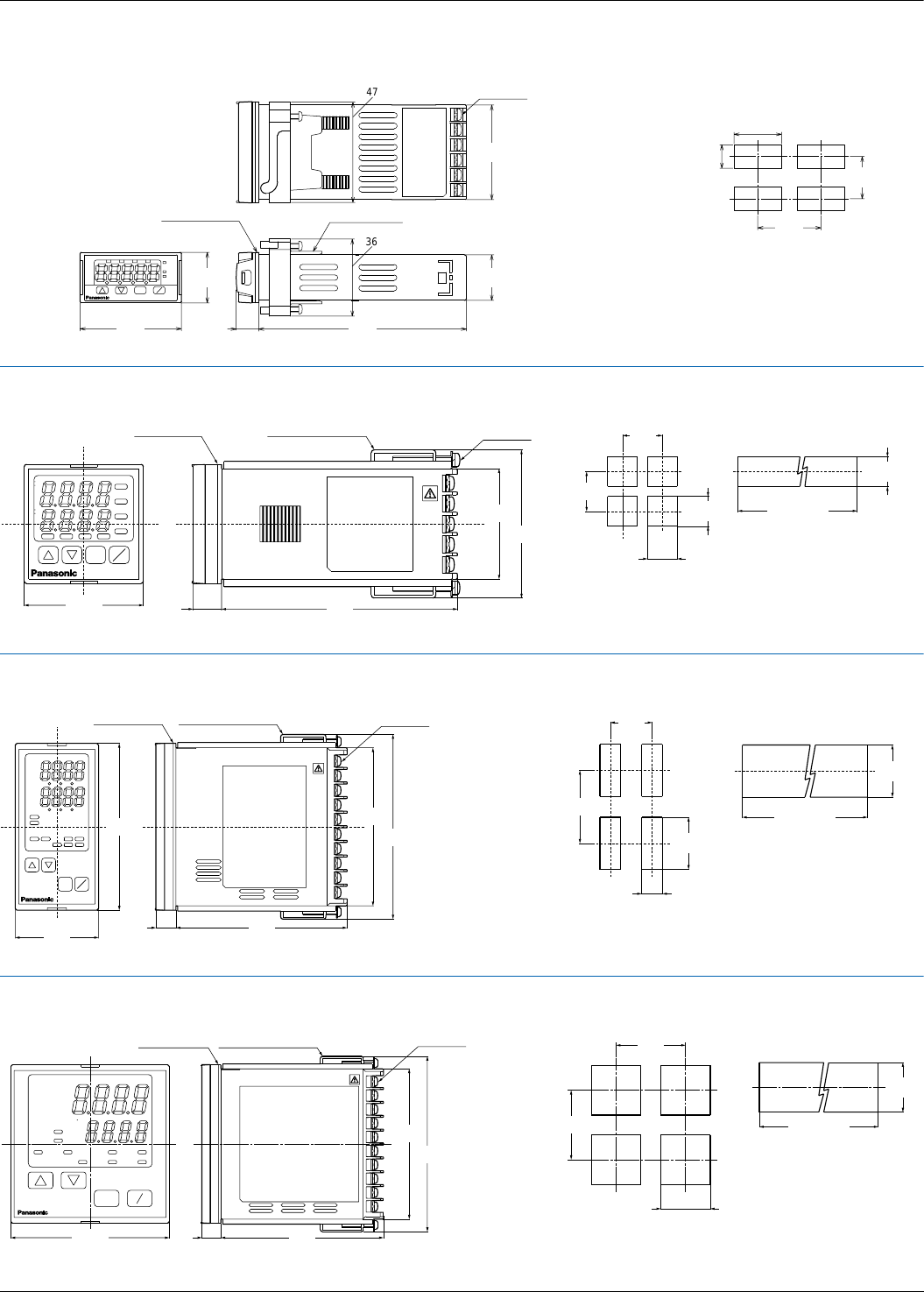
KT (AKT2,4,7,8,9,4H,4B)
10
DIMENSIONS (unit: mm inch) Tolerance: ±1 ±.039
1. KT2 series
• External dimension
KT2
OFF
OUT
MODE
PV SV AT T/R
MEMO/STEP
OUT
EV1
EV2
Mounting frame
Rubber packing
98.5
24
48
21.6
44.8
36.5
10.6
47.6
1.437
1.874 M3 M.118
3.878
.945
1.890
.850
1.764
.417
• Panel cutout
60
40
22.2+0.3
0
.874+.012
0
45+0.6
0
1.772+.024
0
2.362
1.575
Note: The communications terminal is the screw terminal on the
back of the unit.
2. KT4 series
• External dimension
KT4
OFF
MODE OUT
TX/RX
PV
SV
SV1 SV2 AT EVT
A1
OUT2
OUT1
44.5
59.7
9511.5
48
Rubber gasket Screw type mounting M3 M.118
1.752
2.350
3.740.453
1.890
• Panel cutout
Note: The communications terminal is the screw terminal on the
back of the unit.
75
Lateral close mounting
n: Number of units mounted
75
45+0.5
−0
+.020
−0
45+0.5
−0
+.020
−0
n × 48 – 3
+0.5
−0+.020
−0
45+0.5
−0+.020
−0
1.772
n × 1.890 – .118
2.953
2.953
1.772
1.772
3. KT8 series
• External dimension
KT8
OFF
OUT
MODE
SV
PV
OUT1
OUT2
AT
TX/RX
HB
A1
A2/LA
SV1
SV2
91
106.2
98.511.5
Rubber gasket Screw type mounting M3 M.118
96
48
3.583
4.181
3.878.453
3.780
1.890
• Panel cutout
Note: The communications terminal is the screw terminal on the
back of the unit.
75
130
Lateral close mounting
n: Number of units mounted
92+0.5
−0
+.020
−0
92+0.5
−0
+.020
−0
n × 48 – 3
+0.5
−0+.020
−0
45+0.5
−0+.020
−0
n × 1.890 – .118
3.622
3.622
1.772
2.953
5.118
4. KT9 series
• External dimension
OUT1
PV
SV
A2/LA
TX/RX
A1
AT
HB
SV1
SV2
OUT2
MODE OUT
OFF
KT9
91
106.2
98.511.5
96
Rubber gasket Screw type mounting M3 M.118
3.583
4.181
3.878.453
3.780
• Panel cutout
Note: The communications terminal is the screw terminal on the
back of the unit.
130
130
Lateral close mounting
n: Number of units mounted
92+0.8
−0
+.031
−0
n × 96 – 3
+0.5
−0+.020
−0
92+0.5
−0+.020
−0
5.118
5.118
3.622
3.622
n × 3.780 – .118
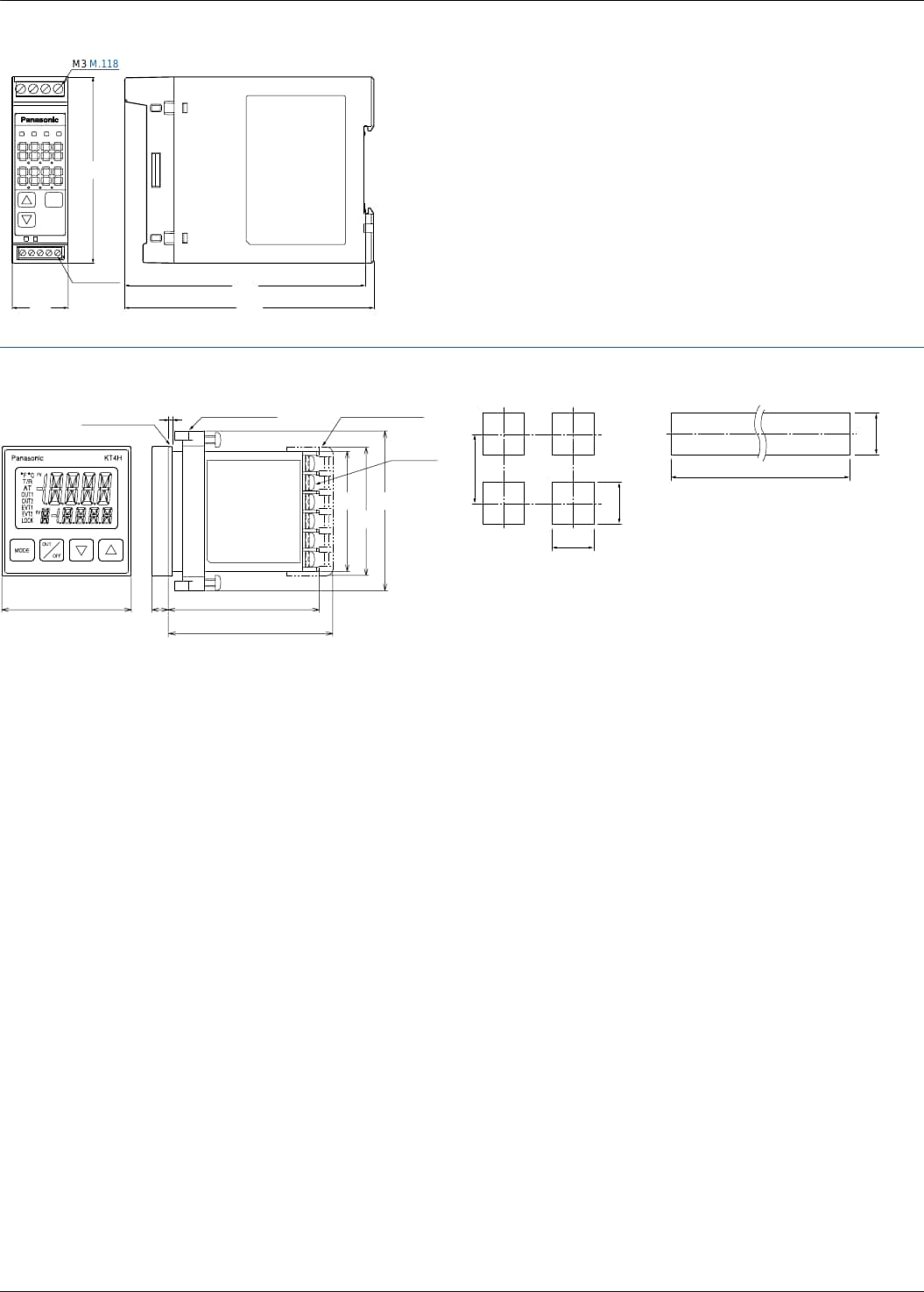
KT (AKT2,4,7,8,9,4H,4B)
11
6. KT4H/4B series
5. KT7 series
• External dimension
MODE
SV
PV
ATT/R
EVT
OUT
KT7
98765
1
243
97
100
75
22.5
M2 M.079
M3 M.118
3.819
3.937
2.953
.886 Note: The communications terminal is the modular jack on the
bottom of the unit.
• External dimensions • Panel cutout • Lateral close mounting
56.0
2.205
.059
1.5
61.0
2.402
6
.236
Rubber gasket
48
1.890
Mounting frame Terminal cover
(Sold separately)
M3 screw
n × 48 − 3
45+0.5
0
1.772+.020
0
n: Number of units mounted
Notes: If lateral close mounting is used for the controller,
IP66 specification (Dust-proof/Drip-proof) may be
compromised, and all warranties will be invalidated.
+0.5
0
n × 1.890 − .118+.020
0
45+0.5
0
1.772+.020
0
45+0.5
0
1.772+.020
0
75
2.953
44.5
1.752
47.5
1.870
59.2
2.331
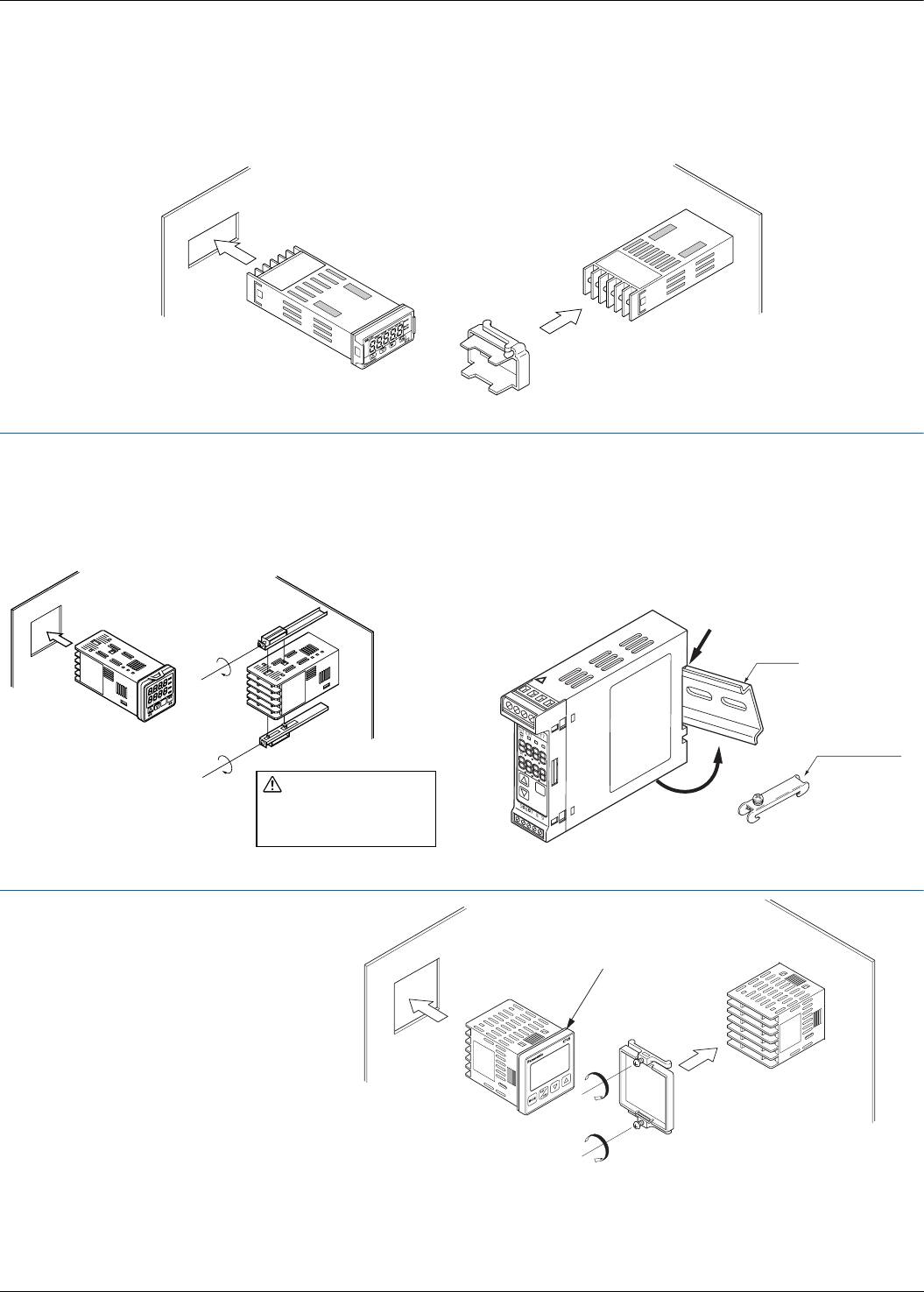
KT (AKT2,4,7,8,9,4H,4B)
12
INSTALLATION
1. KT2 series
Please install vertically in order to satisfy the IP66 specification for dust and splash proofing.
The possible control panel plate thickness for installation is between 1 to 10 mm.
(1) Insert the unit from the front of the control panel.
(2) Insert the mounting frame until that the edges (2) make contact with the panel.
(3) Tighten the clamp screw and then turn it 3/4 of a turn after the edge of the screw reaches the panel.
2. KT4, 7, 8, 9 series
• Panel Mounting
Mountable panel thickness: Within 1 to 15mm .039 to .591inch
Insert a controller from the front side of the panel.
Attach the mounting brackets by the holes at the top and bottom
of the case and secure the controller in place with the screws.
• DIN rail mounting (KT7)
1) Hook 1 of the KT7 on the upper side of the DIN rail.
2) Making the 1 part of the KT7 as a support, fit the lower part
of the KT7 to the DIN rail.
KT7 will be completely fixed to the DIN rail with a “Click” sound.
Recommended DIN rail: Part No. ATA48011
Recommended fastening plate: Part No. ATA4806
MODE
G/T
pv
av
EVT T/B AT
Notice
As the case is made of resin, do not
use excessive force while screwing
in the mounting bracket. The torque
is approximately 0.12N·m
KT7
MODE
56789
G/T
pv
av
EVT T/B AT
1
DIN rail
2
Fastening plate
3. KT4H/4B series
Please install vertically in order to satisfy
the IP66 specification for dust and splash
proofing.
The possible control panel plate
thickness for installation is between 1 to 5
mm.
1) Insert the unit from the front of the
control panel.
2) Push the installation frame fully into
contact with the panel and tighten the
screws (screw torque from 0.05 N·m to
0.06N·m).
Rubber gasket
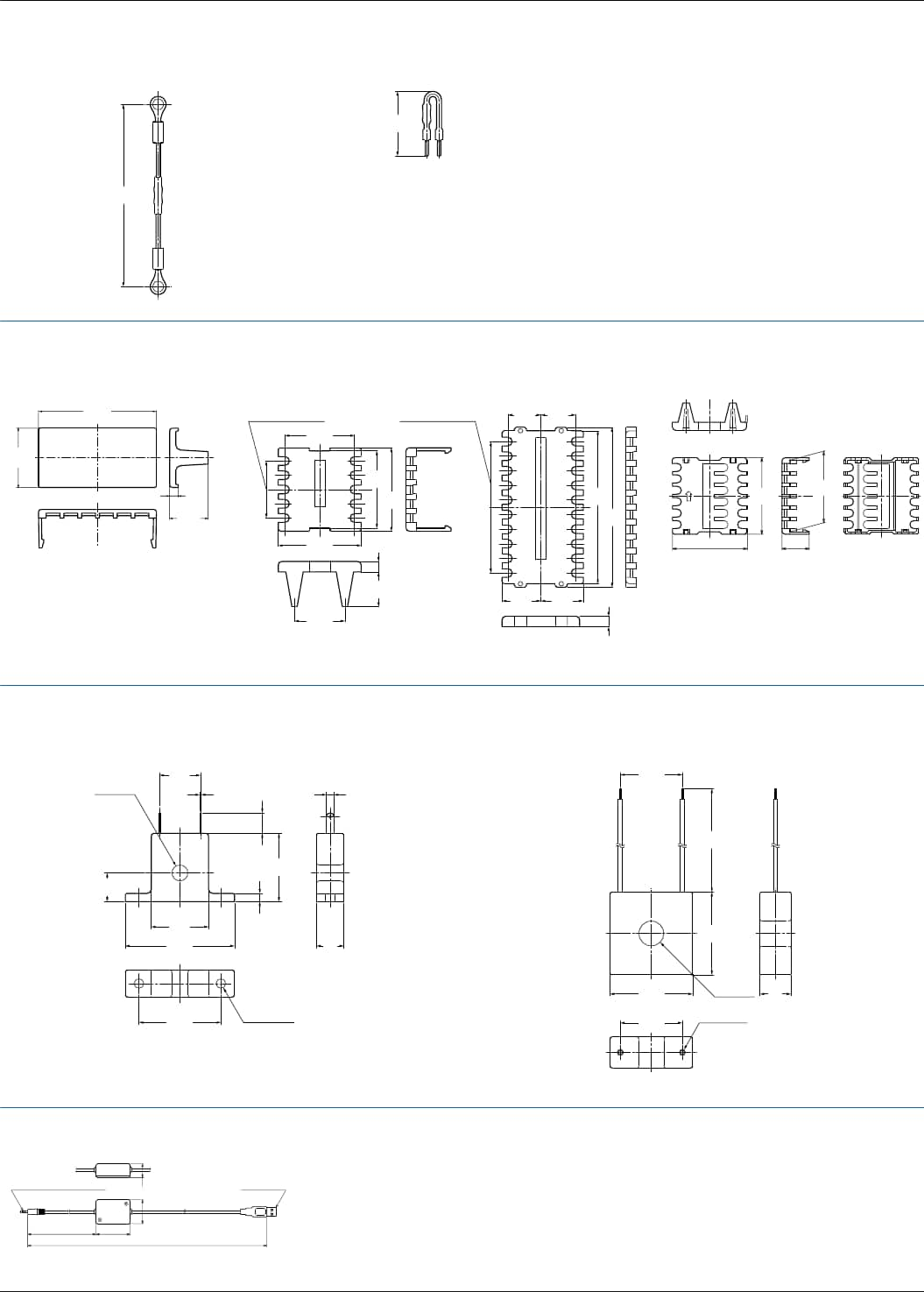
KT (AKT2,4,7,8,9,4H,4B)
13
OPTION
1. Shunt resistor
2. Terminal cover
Note: 2pcs of terminal cover of AKT8801 can be used as an AKT9801 cover.
3. Current transformer (CT)
4. Tool cable
AKT4810 (for KT2, 4, 8, 9, 4H and 4B) AKT4811 (for KT7)
AKT2801 (for KT2) AKT4801 (for KT4) AKT8801 (for KT8)
AKT9801 (for KT9) AKT4H801 (for KT4H/4B)
74±6
2.913±.236
26±1
1.024±.039
47.5
23.8
3.5
15.5
1.870
.937
.138
.610
40
48
19 20
88
92
24.5
6
22.3
9 × 8.4 = 75.69 × 8.4 = 75.6
47.7
29
20
6
44.5
1.575
1.890
.748 .787
3.465
3.622
.965
.236
.878
9 × .331 = 2.9769 × .331 = 2.976
1.878
1.142
.787
.236
1.752
46.5 17
1.831 .669
>PC<
47.5 44.5
1.870 1.752
• External dimension
1) CT1 (for 5,10 and 20A)
Note: CT1 or CT2 for current detection is provided as an accessory when heater
burn-out alarm function is added.
2) CT2 (for 50A)
lk
KL
21
40
30 2-3.5 dia.
5.8 dia.
25
10
3
10.5
15
0.5 7.5 2.8
.827
1.575
1.181 2-.138 dia.
.228 dia.
.984
.394
.118
.413
.591
.020 .295 .110
kl 30
100
40
40 15
30 2-M3 .118
12 dia.
1.181
3.937
1.575
1.575 .591
1.181
.472 dia.
AKT4H820
n2.5 Plug 3-Pole type
200±20 50
7.784±.787 1.969 2000±40
78.74±1.575
USB Plug
20
.787
35
1.378
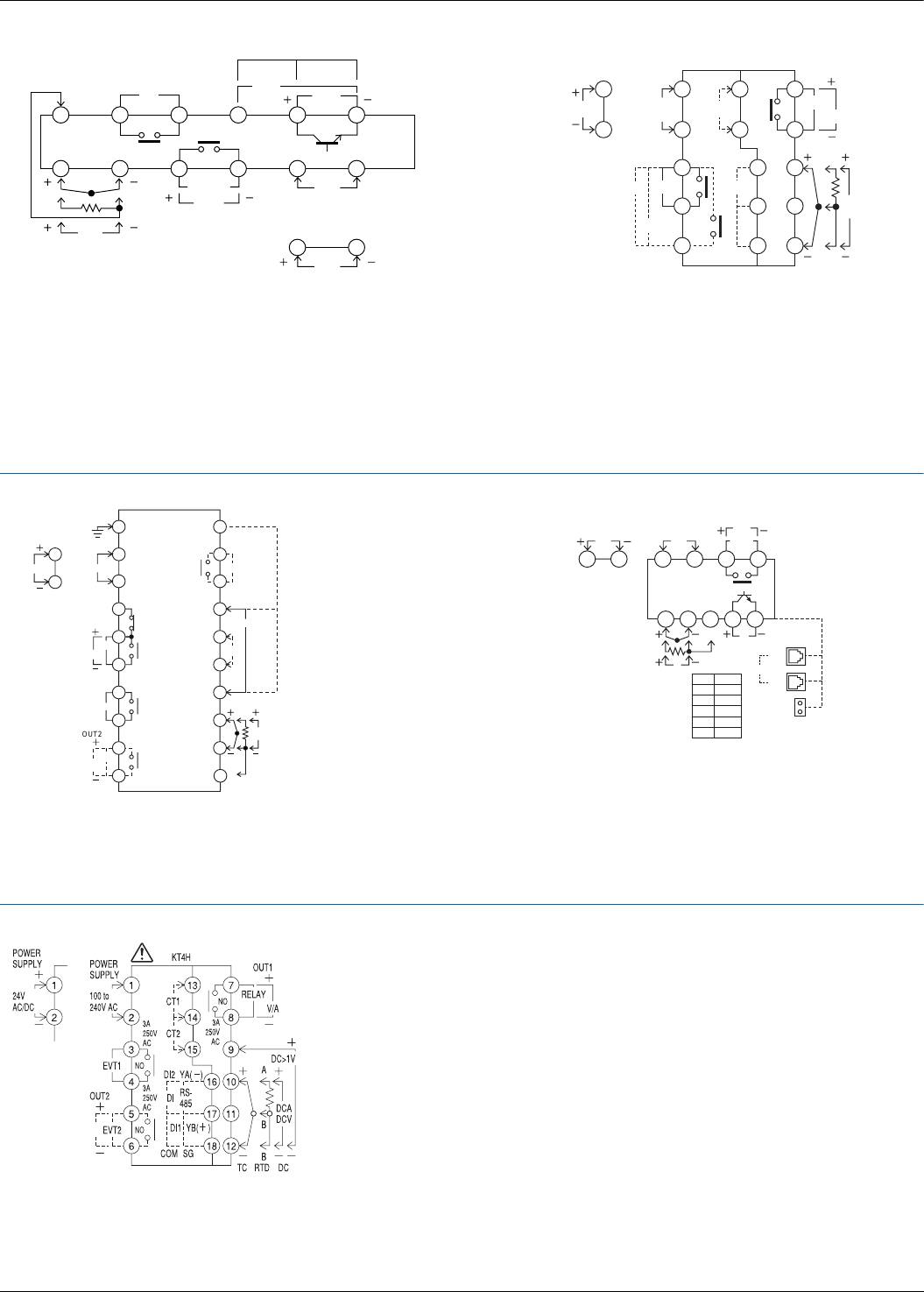
KT (AKT2,4,7,8,9,4H,4B)
14
EXTERNAL CONNECTION DIAGRAM
5. KT4H/4B series
1. KT2 series
• TC: Input terminal for thermo couple.
• RTD: Input terminal for the resistance temperature sensor.
• DC: Input terminal for DC current or DC voltage.
For DC current input, connect a separately sold receipt resistor (50Ω) between the input
terminals.
• OUT1: Output terminal for the control output or heating output [option: heating/cooling control].
• POWER SUPPLY: Power supply terminal.
• EV1/OUT2: Output terminal for event output 1 or cooling output [option: heating/cooling control].
• EV2: Output terminal for event output 2.
• DI: Input terminal for DI input. (There are three types of D1 input, the SV1/SV2 external switching
function, the OUT/OFF (RUN/STOP) output switching function, and timer function.)
• RS-485: Communication terminal for serial communication. (EV1, 2 is alarm output)
2. KT4 series
• POWER SUPPLY: Power supply
• OUT1: Control output 1 (heat output)
• OUT2: Control output 2 (cooling output)
• RELAY: Relay contact output
• V/A: DC voltage output/direct current output
• V: Contactless relay output
• A1: Alarm 1 output
• EVT: Event output (A2 output and heater cutoff alarm output)
• CT: CT input
• TC: Thermocouple
• RTD: Resistance temperature detection
• DC: Direct current or DC voltage
• RS-485: Serial communications
100 to 240V AC
POWER SUPPLY
24V AC/DC
POWER SUPPLY
NO
EV1/OUT2 EV2
NO
3A
250V
AC
3A
250V
AC
TC
DC
RTD
B
B
AV/A
OUT1
RELAY
1
7
2
8
3
9
4
10
5
11
6
5 6
12
SG
D1
YA (–)RS-485 YA (+)
KT2
0.1A
24V
DC
2
3
4
5
1
2
1
7
8
9
10
6
12
13
14
15
11
POWER
SUPPLY POWER
SUPPLY
24V AC/DC 100 to
240V AC CT NO
NO
OUT2
SA1
EVT
3A
250V
AC
3A
250V
AC
YA (–)
YB
(+)
RS-485
NO SG
0.3A
250V
AC
KT4 TC DCRTD
B
B
A
V/A
OUT1
RELAY
3. KT8 and KT9 series
Note: That main setting No. 2 will not be possible on the KT8 and KT9 when the communications
functions is added.
4. KT7 series
• POWER SUPPLY: Power supply
• OUT: Control output
• RELAY: Relay contact output
• V/A: DC voltage output/direct current output
• EVT: Event output
[Alarm, loop fault alarm or heater cutoff alarm (optional)]
• TC: Thermocouple
• RTD: Resistance temperature detection
• DC: Direct current or DC voltage
• RS-485: Serial communications
• CT: CT input
24V AC/DC
250V AC
SV2
CT
A
B
B
TC
RTD
DC
A2/(HB)
YA(–)
YB(+)
RS-485
SG
3A
250V AC
3A
250V AC
OUT2/HB
KT8/KT9
A1
100 to 240V AC
POWER
SUPPLY POWER
SUPPLY
GND
2
1
2
3
4
OUT1
RELAY
RELAY
V/A
V/A
NO
NO
NO
3A
250V AC
NO
NC
5
6
7
8
9
10 20
19
18
17
16
15
14
13
12
11
3
• POWER SUPPLY: Power
supply
• OUT1: Control output 1
• OUT2: Control output 2
(cooling output)
• RELAY: Relay contact output
• V/A: DC voltage output/direct
current output
• A1: Alarm 1 output
• A2: Alarm 2 output
• HB: Heater cutoff alarm
output
• SV2: Second main setup
• CT: CT input
• TC: Thermocouple
• RTD: Resistance
temperature detection
• DC: Direct current or DC
voltage
• RS-485: Serial
communications
1
56789
23412
POWER SUPPLY POWER SUPPLY
24V AC/DC 100to 240V AC OUT
V/A
RELAY
KT7 250V AC
3A
0.1A
24V DC
TC
RTD
DC ABBEVT
RS-485
No.1
No.1
No.2
No.3
No.4
No.5
No.6
SG
NC
YB(+)
YA(–)
NC
SG
No.6
No.1
No.6
CT
POWER SUPPLY ....... Power supply
EVT1 .......................... Alarm 1 output
EVT2 .......................... Alarm 2 output (option) or heater burn-out
Alarm output (option)
OUT1 ......................... Control output or heating output (option)
OUT2 ......................... Cooling output (option)
TC .............................. Thermocouple input
RTD ........................... Resistance temperature detection input
DC .............................. Direct current input (DCA) or DC voltage input (DCV)
(For DC voltage input, + side terminal number differs depending on the voltage.
Also, DC current input, connect s shunt resistor between No. 10 and 12 terminal.)
CT1 ............................ Current transformer input 1 (option: Single, three phase)
CT2 ............................ Current transformer input 2 (option: Three-phase)
DI ............................... Contact input (option)
RS-485 ....................... Serial communication RS-485 (option)

KT (AKT2,4,7,8,9,4H,4B)
15
Communication Function Connection Diagram (PLC Connection Diagram)
3. KT4H/4B series
NOTICE ON OPERATION
1. KT2, 4, 8 and 9 series 2. KT7 series
Notes: 1. Terminating Resistors (Terminators)
The KT series has a built-in pull-up resistor or pull-down resistor, which
serves as the terminating resistor. For this reason, do not connect the
terminating resistor on the communication line.
2. Please use a RJ-116 polarized type modular connector.
Please use a cable that is suitable for a modular connector.
Shielded cable
RS-485 KT4
YA (–)
YB (+)
COM
13
14
15
KT8 , 9
YA (–)
YB (+)
COM
11
14
17
KT4
YA (–)
YB (+)
COM
13
14
15
KT2
YA (–)
YB (+)
COM
10
11
12
KT2
YA (–)
YB (+)
COM
10
11
12
KT8 , 9
YA (–)
YB (+)
COM
11
14
17
PLC
(–)
(+)
Communicatin cable
No.0 No.1KT7 No.30
Terminal 3 to YB (+)
Terminal 4 to YA (–)
PLC
(–)
(+)
Shielded cable
RS-485 KT4H
16
YA (−)
17
YB (+)
18
COM
KT4H
16
YA (−)
17
YB (+)
18
COM
PLC
(−)
(+)
Notes:
1. To prevent current flow along shield sections, ground one end of the shield line. (If both ends of the
shield section are grounded, a closed circuit with the earth will form and electricity flowing through the
shield line will cause increased susceptibility to noise.)
2. Terminating Resistors (Terminators)
The KT4H series has a built-in pull-up resistor or pull-down resistor. For this reason, do not connect the
terminating resistor on the communication line.
1. NOTICE ON SITE SELECTION
This instrument is intended to be used in
the following environment (IEC61010-1)
Overvoltage category II, Pollution degree
2
Mount the controller in a place with:
1) A minimum of dust, and an absence of
corrosive gases
2) No flammable, explosive gases
3) Few mechanical vibrations or shocks
4) No exposure to direct sunlight, an
ambient temperature of 0 to 50°C (32 to
122°F) that does not change rapidly
(When installing inside a panel, make
particular allowance for heat dissipation.
Avoid installation in situations such as
above equipment that generates heat.)
5) Locations in which temperature rapidly
changes may cause condensation.
6) Locations or atmospheres in which
gasoline, thinners, alcohol, or other
organic solvents are present, or in which
ammonia, sodium hydroxide, or other
strong alkaline substances may adhere.
7) Locations susceptible to direct impact
or the transmission of vibrations, or
where splashing with water is possible.
8) In the proximity of equipment in which
large switching surges occur or near
high-voltage cables, high-voltage
equipment, power lines, power
equipment, ham radio transmitters, or
equipment containing these or similar
devices.
9) An ambient non-condensing humidity
of 35 to 85%RH
10) No large capacity electromagnetic
switches or cables through which large
current is flowing
11) No water, oil or chemicals or where
the vapors of these substances can come
into direct contact with the controller
2. NOTICE ON THE WIRING
1) The terminal block of KT4, 8, 9, 4H, 4B
series are designed to be wired from the
left side (KT2 series are designed to be
wired from the upper and lower direction).
The lead wire must be inserted from the
left side of the terminal, and fastened by
the terminal screw. Use a solderless
terminal with insulation sleeve that fits to
the M3 screw.
2) Terminal fastening torque is approxi-
mately 0.6N·m to 1.0N·m (KT4, 8, 9, 4H
and 4B).
For KT7 series by M3.0 screw is less
than 0.5N·m and by M2.0 screw 0.25N·m
respectively.
3) Use a thermocouple and
compensating lead wire according to the
input specification of the controller.
4) Use a 3-wire system of RTD according
to the input specification of the controller.
5) This controller has no built-in power
switch, circuit breaker or fuse. Therefore,
it is necessary to install them in the circuit
near the external controller.
(Recommended fuse: Time-lag fuse,
rated voltage 250V AC, rated current 2A)
6) In the case of 24V AC/DC power
supply, do not confuse the polarity when
it is DC.
7) With the relay contact output type, use
an auxiliary electromagnetic switch
externally according to the capacity of the
load to protect the built-in relay contact.
8) When wiring, keep input wire
(thermocouple, RTD, etc.) away from AC
source and load wire to avoid external
interference.
9) Turn the power supply to the
instrument off before wiring or checking.
Working or touching the terminal with the
power switched on may result in Electric
Shock which could cause severe injury or
death.
Wire-
pressed
terminal
Company
name Part number Fastening
torque
Fork type
NICHIFU
Co., Ltd. 1.25Y-3
0.6 N⋅m,
Max.
1.0 N⋅m.
J.S.T. Mfg.
Co., Ltd. VD1.25-B3A
Round
type
NICHIFU
Co., Ltd. 1.25-3
J.S.T. Mfg.
Co., Ltd. V1.25-3
3.2mm dia. 3.2mm
Max. 5.8mm Max. 5.8mm
.126inch dia. .126inch
.228inch .228inch
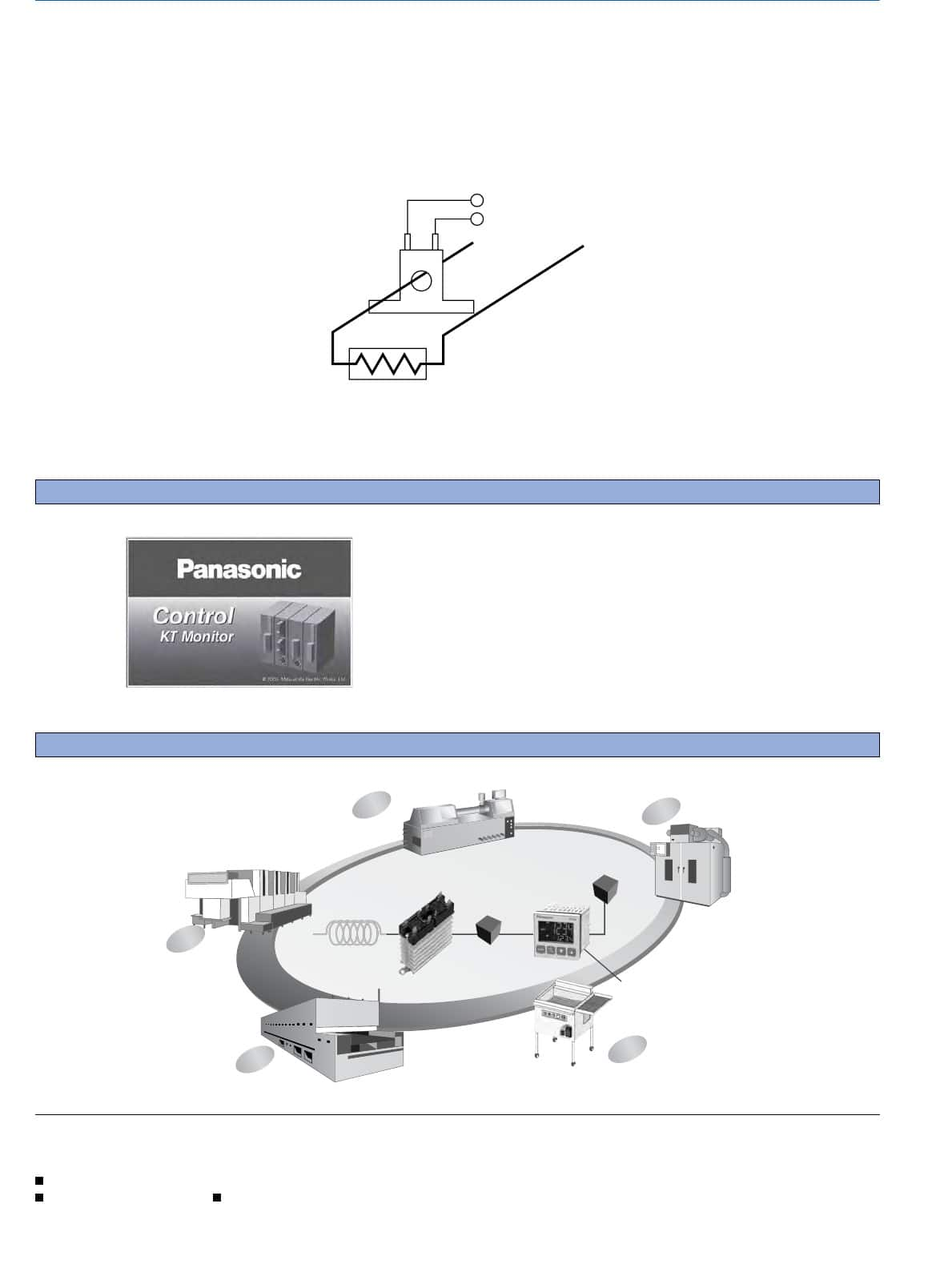
KT (AKT2,4,7,8,9,4H,4B)
16
Automation Controls Business Unit
Head Office: 1048, Kadoma, Kadoma-shi, Osaka 571-8686, Japan
Telephone: +81-6-6908-1050 Facsimile: +81-6-6908-5781 Specifications are subject to change without notice.
All Rights Reserved © 2009 COPYRIGHT Panasonic Electric Works
Panasonic Electric Works Co., Ltd.
Printed in Japan.panasonic-electric-works.net/ac ARCT1B317E 200910-0YT
Available for download free of charge. Use it to acquire data from the KT series temperature controller.
Contributing to space savings of various heater control systems
KT Monitor
Applications
10) Do not drop wire chips into the holes
of vent when wiring, because they could
cause fire, malfunction or trouble with the
device.
11) To prevent the unit from harmful
effects of unexpected high level noise, it
is recommended that a surge absorber
be installed between the electromagnetic
switch coils.
3. NOTICE ON THE MOUNTING
1) Do not use excessive force while
screwing in the mounting bracket of KT4,
8, 9, 4H and 4B series. For KT4, 8 and 9
series, recommended torque is approxi-
mately 0.12N·m. For KT4H and 4B,
recommended torque is approximately
0.05 to 0.06 N·m.
2) When mounting the KT7 series to the
DIN rail, mount it in a lateral direction.
Make sure a click is audible when fixed
into place.
4. OPTIONAL HEATER BURN-OUT
ALARM OUTPUT (KT4, 7, 8, 9, 4H and
4B series)
1) This alarm is not available for detecting
current under phase control.
2) Use the current transformer (CT)
provided, and pass one lead wire of the
heater circuit into the hole of CT.
3) When wiring, keep CT wire away from
AC source and load wire to avoid external
interference.
4) In three phase installations, ensure
that R, S, and T are each connected to a
2-line CT that connects with CT1 ((13)–
(14)) and CT2 ((14)–(15)) terminals.
5. Please use rod terminals for the
terminal portion of the KT7 series.
We recommend terminals made by
Phoenix Contact.
(1) to (4) are AI0.25–8YE, AI0.34–8TQ,
AI0.5–8WH, AI0.75–8GY, AI1.0–8RD,
and AI1.5–8BK.
(5) to (9) are AI0.25–8YE, AI0.34–8TQ,
and AI0.5–8WH.
The screw tightening torque for (1) to (4)
should be no more than 0.5 N·m and for
(5) to (9) it should be no more than 0.25
N·m. Make sure no screw is loose.
Heater
Power supply
CT
CT input terminal
Download from http://www.panasonic-electric-works.net/ac
FEATURES
1. Parameters can be set from a computer.
2. Measurement data can be monitored from a computer.
3. Measurement data can be logged to a computer.
Controller
Sensor
KT4H Temperature Controller
Heater
<Temperature Control System Configuration>
Printing machine
Kitchen appliance
Injection molding machine
LCD curing oven
Printing machine
Kitchen appliance
Injection molding machine
LCD curing oven
Temperature controlled bathTemperature controlled bath