Understanding Flexible Multi-Conductor Cables for Industrial Applications
投稿人:DigiKey 北美编辑
2025-07-01
The multi-conductor cables used for power and control in applications such as industrial automation, heavy machinery, robots, and power generation are subject to continuous flexing and torsion, wide temperature variations, and exposure to oil, water, and industrial chemicals. These conditions can lead to shortened cable life, unreliable operation, and compromised safety. Signal integrity is also an issue, so cables may require shielding to minimize electromagnetic interference (EMI).
Designers of systems for these applications must be well-versed in materials that can withstand the rigors of industrial environments and understand the nuances of conductor layout and placement. They must also ensure compliance with international standards related to environmental capability and safety.
This article provides a brief overview of the cabling requirements of industrial applications. It then introduces examples of super-flexible, continuous-flex cables from LAPP and shows how their material and specialized construction enables designers to meet these specifications.
Industrial motion
Automated factories are constantly in motion. Robotic arms extend, rotate, and withdraw; and processing stations turn and position products for machining and pick-and-place operations, while machine tools rotate and translate tool heads (Figure 1).
Figure 1: Automated machines require reliable cables that can bend and twist through millions of cycles. (Image source: LAPP)
These applications, as well as those for cranes, wind turbines, and heavy vehicles, all require flexible cables that can withstand millions of bending and twisting cycles. Typical cable motions include continuous flexing, torsional flexing, and bending flex (Figure 2).
Figure 2: The typical flexing motions that cables are exposed to include continuous, torsional, and bending. (Image source: LAPP)
A cable rolling back and forth in a linear motion, commonly in a cable track, results in continuous flexing. Torsional flex, common in robotic machines, results from twisting a cable longitudinally, clockwise or counterclockwise, in a 90° to 360° range. Bending flex, also called tick-tock flexure due to its similarity to the motion of a pendulum, results from a cable being bent back and forth about a stationary point. In all these cases, the highest stress occurs at the stationary bend point and the driven point.
Understanding how cables are designed to handle a specific type of bending is critical to ensuring reliability and a long functional life.
Flexible cable
A cable's flexibility is a function of its internal structure. It begins with a wire conductor surrounded by insulation. The most common conductor used is copper, followed by aluminum and silver options. Insulation is selected from a range of thermoplastics or elastomers and is applied by extrusion.
In general, greater cable flexibility is achieved by using multiple smaller wires. Since a cable’s resistance is a function of the cross-sectional area of the wire, multiple smaller wires must be used to maintain the cable's series resistance. DIN VDE 0295/IEC 602258 specifies several flexibility classes for industrial cables (Figure 3).
Figure 3: The DIN VDE 0295/IEC 602258 classes for flexible cable structures range from solid for fixed applications to extra-fine stranded wire for extra-flexible installations. (Image source: LAPP)
Class 1 conductors use solid wire, typically made of copper. They are intended for installation in buildings where a fixed, strong, and rigid cable is needed.
Class 2 conductors contain multiple stranded wires with a smaller individual diameter. This cable class offers more flexibility but is still intended for fixed installations in applications that may require bending, coiling, or occasional movement, such as when initially locating and routing them.
Class 5 flexible conductors use finer wires to produce cables with greater flexibility. These cables are used in line cords for portable power tools, extension cords, and other applications where flexibility is useful but not required repeatedly.
Class 6 extra-flexible conductors use even finer wires. This conductor type is used for cables installed in movable electrical equipment such as robotics and industrial machines, as well as in areas where cables are subject to frequent movement or twisting.
The wires in multiwire cables are twisted or laid to achieve a circular cross-section, minimize the diameter, and enhance flexibility (Figure 4).
Figure 4: Shown are common cable lays to reduce diameter, ensure a circular cross section, and increase flexibility. (Image source: LAPP)
Bunch-lay cables contain any number of wires in a random pattern twisted together in the same direction. Bunch construction will not have a well-defined geometric configuration and may have a variable cross-section. The related unilay constructions will have a well-defined geometry and cross-section.
Concentric-lay cables use a core wire surrounded by well-defined layers of helically laid conductors. Each concentric layer has a reversed lay direction. Due to the twisting, the lay length in each succeeding course increases. Concentric-laid cables are used in continuous flex applications.
Conductors in a concentric unilay surround a single wire core with one or more layers of helically-laid conductors. Successive layers are wrapped in the same direction of lay and increase lay length in each succeeding course. This cable lay is typically used in designs that require torsional and continuous flexing.
Cable construction
A cable consists of several wires surrounded by layers of lubricating and insulating materials. The most commonly used insulation is polyvinyl chloride (PVC). Multiple wires are laid and enclosed with protective layers, forming the cable. For example, the LAPP ÖLFLEX FD 890 and FD 890 CY continuous flex control cables (Figure 5) use multiple copper conductors with specially formulated PVC insulation.
Figure 5: The structure of both shielded and unshielded flexible cables includes copper conductors with PVC insulation. (Image source: LAPP)
Cables from the FD 890 family (Figure 5, top) have 3 to 50 wires and wire sizes of 20 AWG to 2 AWG, while cables from the FD 890 CY family (Figure 5, bottom) have 3 to 34 wires, with wire sizes of 20 AWG to 6 AWG. Their structures are similar, except for the addition of the shield braid.
The FD 890 CY series cables include a tinned copper braid for applications that require EMI shielding. Shielded cables are necessary in areas such as the factory floor, where there is typically a higher concentration of active power and control cables in a confined space. The shielded cables have a similar core structure to the unshielded cables, with an added internal PVC jacket under the braid to isolate it from the wires in the core. Due to the extra layers, the cable diameter is greater than that of a comparable unshielded cable. The outer jacket has the same characteristics as the unshielded cable.
An example of the ÖLFLEX FD 890 series is the 8920044 four-conductor unshielded cable with 20 AWG wires; the equivalent metric specification is a 0.5 mm2 conductive cross-sectional area. The assembled cable has a diameter of 7.4 mm. An example of the shielded ÖLFLEX FD 890 CY family is the 8914044S four-conductor cable with 14 AWG wires. This cable has a conductive cross-sectional area of 2.5 mm2, with a cable diameter of 14 mm. The shielding braid provides 85% coverage of the core wire’s surface.
Both cable families exceed the Class 6 flexibility standard. They are rated to handle operating voltages up to 600 volts and are breakdown tested to 2000 V. The temperature specification for both cable series depends on the application. For example, it is -5°C to +90°C for applications that require continuous flexing and -25°C to +90°C for stationary use.
The minimum bend radius is a figure of merit for cable flexibility. It gives the smallest bend radius that the cable can sustain without damage and is usually expressed in multiples of the cable diameter (D) (Figure 6).
Figure 6: The minimum bend radius is defined in terms of multiples of the cable diameter (D). (Image source: LAPP)
The cable shown in Figure 6 has a minimum bend radius of three times the cable diameter. The FD 890 cables have a bend radius of 7.5 cable diameters. Due to the added inner jacket and shield layers, the FD 890 CY shielded cables have a greater minimum bend radius of 10 diameters. For example, the minimum bend radius for the 14 mm FD 890 CY cable is 140 mm.
The FD 890 and FD 890 CY cables are certified to UL, CSA, CE, and RoHS standards for motion, flame retardancy, oil resistance, and sunlight resistance.
Conclusion
The LAPP ÖLFLEX FD 890 and FD 890 CY multi-conductor cables are designed for continuous flex in applications that include industrial automation, heavy machinery, robots, and power generation. These cables use fine wire stranding and specifically formulated compounds to optimize flexing life and provide high resistance to oil, water, and industrial coolants and solvents. A shielded version is available for applications where EMI is a concern.
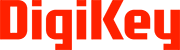
免责声明:各个作者和/或论坛参与者在本网站发表的观点、看法和意见不代表 DigiKey 的观点、看法和意见,也不代表 DigiKey 官方政策。