RTDs, PTCs, and NTCs: How to Effectively Decipher This Alphabet Soup of Temperature Sensors
投稿人:Convergence Promotions LLC
2011-09-14
Need a temperature sensor for your next application? You’ll first need to sort through the three letter acronyms before arriving at any BOMs.
This article describes two types of commonly used passive temperature sensors – resistance temperature detectors (RTDs) and thermistors. It aims to help the designer make a proper choice when to use one or the other and shows how to effectively interface these devices to analog signal conditioning circuitry.
Temperature control is fundamental – and may be critical – in many of the various systems that designers are improving or innovating using electronic feedback methods. Let’s start with the amazing detectors first and then move on to the amplifiers.
RTDs
RTDs operate on the principle of changes in electrical resistance of pure metals, and are characterized by a linear positive change in resistance with changing temperature. Platinum (Pt) is by far the most common element used for RTDs because of its wide temperature range, accuracy, and stability. RTDs also exhibit the most linear signal with respect to temperature of any electronic temperature sensor. Figure 1 shows the excellent linearity of these RTD beasts over temperature.
Equation 1 below shows the widely used third order mathematical approximation of the RTD’s relationship between resistance and temperature – the Callendar-Van Dusen equation. The RTD is more linear than the thermocouple, but still requires curve-fitting over a fairly wide temperature range.
For temperatures

a fourth order polynomial is used.
For temperatures

a quadratically approximated formula is used.
Equation 1: The Callendar-Van Dusen equation has been reliably used for years to approximate the RTD resistance/temperature curve over a wide temperature span.
Where:
RT= Resistance at temperature T in ºC
R0= Nominal resistance at T=0º C
The coefficients according to IEC 60751 for the Vishay PTS, for example, are:
A= 3.9083X10-3 ºC-1
B= -5.775X10-7 ºC-2
C= -4.183X10-12 ºC-4
The Callendar-Van Dusen equation has been around for 100 years, and even though it is not the best fit for platinum RTDs, it is widely used today. Callendar and Van Dusen performed their work well before the advent of modern digital computers. They could not use much more than a third order equation since they had to solve the equation by hand. They used an equation that was reasonably accurate and could be solved in a human lifetime.
In 1968, the International Electrotechnical Commission recognized the shortcomings of the Callendar-Van Dusen equation and defined a 20-term polynomial equation for the resistance versus temperature curve for 100 Ω platinum RTDs (for 1,000 Ω RTDs just multiply by 10). In Callendar and Van Dusen’s day, a 20-term polynomial would have taken several days to solve per temperature point. The arrival of the digital computer made solving such an equation trivial.
The temperature coefficient “a” value depends upon the grade of platinum used and defines the sensitivity of the metallic element, but is normally used to distinguish between resistance/temperature curves of various RTDs. For example, in the PTS series data sheet, this “a” value is 3850 ppm/K. This means that the resistance of the sensor will increase 0.385 Ω for every degree Celsius increase in temperature. This “average” relationship can be used over a limited temperature range (over a delta of about 100 degrees Celsius in a linear equation. This temperature coefficient of resistance is defined as the resistance of the RTD at 100 degrees Celsius minus the resistance at zero degrees Celsius divided by 100. The result is then divided by the resistance at zero degrees Celsius. The temperature coefficient of resistance is the average resistance change from zero degrees to 100 degrees Celsius. The actual change for each and every degree from zero degrees to 100 degrees Celsius is very close, but not identical to it (see Equation 2).

Equation 2: The linear equation which approximates the RTD resistance/temperature curve over a narrow temperature span.
Be very cautious to use the proper coefficients corresponding to the standard referenced in the manufacturer’s data sheet to calculate temperature. As seen previously, Vishay’s PTS series uses the IEC 60751 standard with one set of coefficients, but some RTDs might use other standards of calibration, such as ITS-90 or DIN 43760 standards (see Table 1).
Standard | Temperature Coefficient (a) | A | B | C |
DIN 43760 | 0.003850 | 3.9080 X 10-3 | -5.8019 X 10-7 | -4.2735 X 10-12 |
American | 0.003911 | 3.9692 X 10-3 | -5.8495 X 10-7 | -4.2325 X 10-12 |
ITS-90 | 0.003926 | 3.9848 X 10-3 | -5.870 X 10-7 | -4.0000 X 10-12 |
Table 1: Callendar-Van Dusen coefficients corresponding to common RTDs and different standards with different coefficients.
*For temperatures below zero degrees Celsius only; C=0.0 for temperatures above zero degrees Celsius.
Other sources of errors of which the designer needs to be aware are stability, or drift over time, rise time of the sensor to reach some percentage of final resistance with a step change in temperature, and self-heating, which will occur with a current through the RTD device. Heat generated in this way causes the temperature of the RTD to rise and create a false temperature that adds to the actual temperature being measured, thus causing errors. Finally, if the RTD has lead wires connected to it, the resistance of even 5 Ω for the lead wires can add to RTD resistance creating another error source. In this case, if the error is not tolerable, you can help nullify the error in a front-end bridge configuration (see Figure 2).
Now let’s look at some active front-end amplifier solutions.
An excellent choice as a front-end amplifier would be the Texas Instruments (TI) XTR105 (see Figure 3). This amplifier helps solve the many error problems mentioned before, has current source drive to power the RTD, and even has internal linearization circuitry to improve linearity by a 40:1 margin. An added benefit is the 4 to 20 mA twisted-pair output configuration, which is excellent in a noisy industrial environment.
The schematic symbol for the RTD is a resistor with an arrow through it indicating a variable resistance and is shown in Figure 4.
Vishay has the PTS series in 100 Ω and PTS series in 500 Ω in surface mount package and U.S. Sensor has the PPG series in 100 Ω and PPG series in 500 Ω with two-wire radial leads. Both of these series use a thin-film manufacturing process, which provides cost advantages when compared to wire-wound structures because of lower material cost factor.
Thermistors
Thermistors are thermally-sensitive resistors and are similar to RTDs in that they are electrical resistors in which resistance changes with temperature.
Thermistors have a very high sensitivity, and therefore are very responsive to changes in temperature with faster response times than RTDs, but have a smaller temperature range than RTDs.
Thermistors have either a negative temperature coefficient (NTC) or a positive temperature coefficient (PTC). The NTCs have resistance that decreases with increasing temperature. The PTCs exhibit increased resistance with increasing temperature. Figure 5 shows a typical thermistor temperature curve compared to a typical 100 Ω RTD temperature curve.
Let’s look at some pros and cons of the RTD versus the thermistor in Table 2.
RTC | Thermistor |
Range: -200°C to +850°C | Range: 0°C to +100°C |
Fair Linearity | Poor Linearity |
Requires Excitation | Requires Excitation |
Low Cost | High Sensitivity |
Table 2: Pros and cons of RTDs versus thermistors.
Thermistors, like RTDs, being resistive devices, need an excitation current. The designer must be aware of self-heating just like in the RTD, which is a cause of errors. Lead wire resistance can have the same effect of causing errors in a thermistor as it does in an RTD. Again, a bridge configuration can help solve this problem.
By the 1960s, thermistors were mainstream sensors. Steinhart and Hart, two researchers at the Woods Hole Oceanographic Institute, published a paper defining a temperature versus resistance formula for thermistors. The Steinhart-Hart equation has become the industry standard equation for thermistors.
The classic Steinhart-Hart equation is seen in Equation 3.

Equation 3: The classic Steinhart-Hart equation for thermistors.
Where:
T = Temperature in Kelvin (Kelvin = Celsius + 273.15)
A0, A1, A3 = Constants derived from thermistor measurements
R = Thermistor’s resistance in ohms
ln = Natural Log (Log to the Napierian base 2.718281828)
In practice, three thermistor resistance measurements at three defined temperatures are made. These temperatures are usually the two endpoints and the center point of the temperature range of interest. The equation hits these three points directly and has a small error over the range.[1]
Since the thermistors’ temperature coefficient creates significant non-linearity contributing to error, this will limit useful applications to very narrow temperature ranges unless linearization techniques are used.
The thermistor can be used over a wider range of temperatures if the designer can tolerate the trade-off of lower sensitivity to achieve improved linearity. One such approach is to simply shunt the thermistor with a fixed resistor. As shown in Figure 6, the parallel combination exhibits a more linear variation with temperature as compared to the thermistor by itself.
The value of the fixed resistor can be calculated from Equation 4.

Equation 4: Equation to calculate a linearizing shunt resistor for a thermistor.
Where:
RT1 is the thermistor resistance at T1, the lowest temperature in the measurement range.
RT3 is the thermistor resistance at T3, the highest temperature in the range.
RT2 is the thermistor resistance at T2, the midpoint,
To further improve the linearity, one can apply the output of this linearity network to the input of an analog-to-digital converter (ADC), which can perform further digital linearization. A 12-bit ADC should suffice for most thermistors.[2]
The schematic symbol for the thermistor is shown in Figure 7.
Conclusion
All things being equal, the choice of a temperature sensor depends on the application.
- Resistance temperature detectors (RTDs) display excellent linearity, accuracy, and stability. The RTD is a more linear device than the thermocouple, but it still requires curve-fitting over a fairly wide temperature range.
- Be very cautious to use the proper coefficients corresponding to the standard referenced in the manufacturer’s data sheet to calculate temperature.
- Thermistors have a very high sensitivity and therefore are very responsive to changes in temperature with faster response times than RTDs, but have a smaller temperature range than RTDs.
- The thermistor can be used over a wider range of temperatures if the designer can tolerate the trade-off of lower sensitivity to achieve improved linearity.
References
- Building Automation Products, Inc., Gays Mills, WI 54631, USA – application note 3/13/2008.
- Analog Devices, Section 7, Temperature Sensors, Walt Kester, James Bryant, Walt Jung.
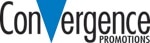
免责声明:各个作者和/或论坛参与者在本网站发表的观点、看法和意见不代表 DigiKey 的观点、看法和意见,也不代表 DigiKey 官方政策。