新型 PLC 有助于加快复杂和关键自动化流程的部署速度
投稿人:DigiKey 北美编辑
2025-05-14
新型可编程逻辑控制器 (PLC) 集先进功能和灵活性于一体,能够快速开发和部署复杂的关键基础设施和自动化流程。
对于从可再生能源和微电网控制到工业 4.0 工业物联网 (IIoT) 改造(即使是小型工厂)、石油和天然气、机器设计以及装瓶、包装、纺织和类似应用中的制程设备自动化等各种用途来说,这都是一项重要的发展。
要提供最佳的解决方案,最新的技术必不可少。这些 PLC 采用双核 64 位处理器,可满足最具挑战性的自动化要求。Linux 操作系统是一加分项,且代码可移植,并可与符合 IEC 61131-3 标准的系统互操作。同时使用基于万维网的管理系统可简化配置。
此外,还需要选择通信接口、支持多种现场总线协议、IIoT 连接、云连接、能源管理软件和全面的安全工具,以提供解决一系列关键开发和集成方案所需的灵活性。
PFC300 简介
Wago 推出了 PFC300 PLC,以帮助加快部署复杂而关键的自动化流程。本文首先深入探讨了 PFC300 的功能和优势,最后举例说明了如何将其应用于智能工厂和微电网安装。
PFC300 采用模块化设计,可快速适应复杂而关键的工业 4.0 工厂、微电网和楼宇自动化领域不断变化的需求和未来要求。市面上有各种模拟、数字和专用输入/输出 (I/O) 模块可供选择,能够满足各种特定的自动化需求。此外,还可以通过增减 I/O 模块来提高或降低系统的复杂性。
这些 PLC 具有耐环境性,因此可安装在苛刻的环境中。其工作温度范围为 -25°C 至 +60°C,相对湿度 (RH, 非冷凝) 最高可达 95% ,污染等级为 2 级,符合 IEC 61131-2 标准。
它们按照 IEC 60068-2-6 要求提供最高 4g 的抗振能力,并根据 IEC 60068-2-27 标准,提供 15g 的抗冲击能力。电磁兼容性 (EMC) 性能包括符合 EN 61000-6-2 标准的抗扰度和符合 EN 61000-6-3 标准的耐辐射性。同时它们还按照 IEC 60068-2-42 和 60068-2-43 要求,可以承受各种污染物的暴露。
图 1:PFC300 具有模块化、可扩展和可承受恶劣环境特性(图片来源:Wago)
现场总线和边缘连接
PFC300 支持多种现场总线、EtherNet 协议和远程控制协议,简化了为关键和复杂的自动化过程构建控制网络的任务。
集成的现场总线包括 Modbus TCP 主机/从机、Modbus (UDP)、Modbus (RTU)、EtherNet/IP 适配器(从机)、EtherNet/IP 扫描仪、EtherCAT 主机、PROFINET 控制器(有限)、OPC UA 服务器/客户端和 OPC UA Pub/Sub(可安装)。
此外,还可以选择远程控制协议许可,如用于关键基础设施中 SCADA 系统的 DNP3、用于变电站自动化的 IEC 60870 和 IEC 61850,或广泛用于楼宇自动化的 BACnet。
前面板的 D-sub 9 针 RS 485 连接器用于 CANopen、Modbus RTU 和其他串行通信协议。服务接口后面的 USB-C 连接器可直接用于编程、配置和固件更新。两个 RJ-45 千兆位以太网端口和一个集成式交换机支持线路拓扑布线。
除了通信接口和 USB-C 连接器之外,PFC300 的前面板还包括一个安全数据 (SD) 卡接入端口、状态指示灯和电源连接器(图 2)。
图 2:PFC300 的前面板包括通信接口、状态指示灯、电源连接和其他接入点。(图片来源:Wago)
到达云端
在设计和部署复杂的关键基础设施和自动化流程时,需要云连接。而 PFC300 则利用消息队列遥测传输 (MQTT) 协议实现安全高效的云连接。
同时这也允许使用各种云服务,如 Microsoft Azure、Amazon Web Services (AWS)、IBM 云、SAP 云和 Wago 云。Wago 云提供了一个简单直观的解决方案,用于管理机器数据以及可视化趋势和图形,无需大量编程支持。
数据传输使用传输层安全 (TLS) 加密,云连接数据可使用 Wago 的网络管理系统 (WBM) 进行配置。WBM 允许用户通过网络浏览器界面监控、配置和控制 PFC300 和远程 I/O 模块,无需安装本地软件即可轻松访问和管理。WBM 允许选择哪些数据应传输到云端,哪些应在本地处理。
为了进一步促进云连接,Wago 的库可用于基于 IEC 61131-3 的 CODESYS 2.3 和 e! COCKPIT,Wago 的集成开发环境支持所有自动化任务,从硬件配置和编程到模拟、可视化和调试,并针对 PFC300 等 Wago PLC 进行了优化。
标准化加快了开发速度
Wago 为 PFC300 提供了多种软件开发途径。它们包括用于系统集成的 C 和 C++ 等高级编程语言,以及支持标准 IEC 61131-3 控制编程语言的 CODESYS V3.5 平台,包括结构化文本 (ST)、功能块图 (FBD)、梯形图 (LD)、指令列表 (IL)、顺序功能图 (SFC) 和功能图 (CFC)。
包括新型 PFC300 在内的 PFC 系列控制器中的 Wago 操作系统 (OS) 基于实时 Linux,能够实现灵活而强大的自动化解决方案。除支持 C 和 C++ 外,还可以用任何支持 Linux 的语言创建程序,并直接在控制器上执行。
支持所有标准 IEC 61131-3 编程语言的 CODESYS 软件还可创建网络可视化,让机器操作员和维护人员能够通过平板电脑或个人电脑上的网络浏览器访问机器。
可扩展存储
PFC300 还包括一个存储卡插槽,采用双推机构并带有一个密封盖。它可以处理 SD、SDHC 和 SDXC 格式(所有保证属性仅对 Wago 存储卡有效)。这些卡是通用的,有多种用途,如:
- 一般数据存储
- 使用可引导 SD 卡进行固件更新,该卡可在 PFC300 启动时自动启动更新
- 存储大型图片,供网络可视化应用使用
- 备份 PLC 的映像以供存储,或将设备文件和参数从一个控制器传输到另一个控制器,以加快部署速度
- 使用 FTP 远程访问存储卡
分层安全工具
部署复杂的关键基础设施和自动化流程需要最高级别的安全性。PFC300 控制器可提供所需的多层安全工具。
它支持虚拟专用网络 (VPN),使用传输层安全 (TLS) 加密技术保护数据,实现安全通信。集成防火墙可防止未经授权的访问。
WBM 采用 HTML5 实现,通过 TLS 1.3 加密,PFC300 支持 SNMP v3、SFTP、FTPS、HTTPS 和 SSH 等安全协议,确保数据交换安全。USB-C 端口可确保更新的安全访问,现场总线协议可确保与连接设备进行安全通信。
工业 4.0 和智能工厂
PFC300 PLC 提供全面的现场总线连接、实时数据功能以及 IIoT 和云集成,实现了制造灵活性、流程优化和预测性维护。这些都是工业 4.0 智能工厂的标志。在复杂和关键的工业流程中,可以消除自动化孤岛,优化能源消耗。
PFC300 PLC 可与 Wago 能源数据管理 (EDM) 软件相结合,用于资源优化和能源监控,从工厂车间的单个设备,到在边缘编译整个设施的数据,并将其推送到云端进行更深入的分析(图 3)。
- EDM 提供实时监控和能耗反馈,支持效率最大化和主动维护。
- 广泛的集成和灵活的通信选择实现了跨设备和整个工厂网络的无缝数据集成。
- 可视化工具使得数据更容易获取,并加快了分析速度。
图 3:PFC300 具备从现场到云端的工业 4.0 自动化所需的所有功能。(图片来源:Wago)
EDM 是一款基于网络的应用程序,用户无需编程即可监控、分析和报告能耗详情。它可以自动连接电表和传感器,收集、编译和存储数据,以供未来分析之用。
数据可显示为时间序列或条形图等线形图,并可导出为逗号分隔值 (CSV) 文件,且与各种分析软件包兼容。EDM 软件及相关硬件组件(如仪表和传感器)具有模块化和可扩展性,可快速适应工业设施中不断变化的设备和基础设施。
EDM 软件能够让设备工程师识别出改善能耗和实施节能计划的最有效机会。系统还可以设置能耗限制,并在超过限制时发出警报。EDM 软件提供的数据是复杂的工业 4.0 设施和微电网等关键基础设施整体能源管理的重要环节。
微电网和能源管理
微电网和综合能源管理计划对于支持可持续发展越来越重要。PFC300 PLC 提供功能强大的工具,非常适合关键的绿色能源基础设施,包括楼宇自动化、微电网变电站、能源数据管理、电动汽车充电负载管理以及其他绿色能源应用(图 4)。
- 这些 PLC 可以控制建筑物内的供暖、通风和空调 (HVAC) 系统,并监控本地能源的产生、储存和使用。
- 它们可以记录和分析能源消耗模式,以优化整个微电网的可用能源资源,从连接微电网与公用电网的变电站到电动汽车充电器或建筑物等特定负载位置。
图 4:PFC300 支持的微电网可提高可持续性和能源安全。(图片来源:Wago)
动态负载管理可通过 Wago 的应用负载管理 (ALM) 软件实现,从而实现电动汽车充电、光伏等可再生能源、储能系统和电网电力管理的一体化。例如,ALM 可用于调节电网连接点(如用户变电站)的总充电功率,缓解负荷峰谷,防止电网过载。
该软件可根据车辆数量、充电优先级、时间、可用电网容量和其他因素动态分配电动汽车充电负荷。它可以进行配置,在公用事业费率高峰期优先使用本地发电和储能资源,减少高需求的充电。
PFC300 可记录和分析能耗数据,其基于网络的管理系统和对 IIoT 通信协议的支持可实现数据可视化,并对本地和远程能耗进行监控。
结语
可承受恶劣环境的 PFC300 具备所有功能,可快速开发和部署复杂的关键基础设施和自动化流程。其模块化和可扩展的设计提供了适应各种应用场景的灵活性。全面、安全的通信选项支持从地面到云端的连接。
推荐阅读:
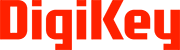
免责声明:各个作者和/或论坛参与者在本网站发表的观点、看法和意见不代表 DigiKey 的观点、看法和意见,也不代表 DigiKey 官方政策。