Motion Performance Considerations when Selecting VFD Cables for Robotics
投稿人:DigiKey 北美编辑
2025-06-25
Several key factors must be considered to ensure a minimum solution size and maximum reliability when specifying variable frequency drive (VFD) cables for industrial robotics. There’s no “one-size-fits-all” solution, and a careful analysis of specific motion requirements is needed to determine the best cable for each application.
Some types of cables are suited for gantry robots, while others excel in multi-axis articulated robots, pick-and-place applications, or other robotic solutions.
Specifications to consider include minimum bend radius, maximum torsion, wire stranding construction, continuous flex rating (based on bend radius, distance, acceleration, speed, and weight), insulation and jacket materials, and the level of shielding for electromagnetic interference (EMI).
This article details some of the subtleties when specifying cables for industrial robotics and shows how ÖLFLEX® VFD 1XL and VFD 1XL with signal cables from LAPP, rated for up to two million bend cycles, are suitable for use with a range of robot designs, including gantry robots. It then reviews the demands of multi-axis articulated robots with complex twisting and bending motions that may benefit from using ÖLFLEX ROBOT F1 cables.
The article then briefly presents ÖLFLEX SERVO FD 7DSL, a hybrid cable made with Class 6 extra fine-stranded wire and designed for up to 10 million bend cycles for use in robotics applications, such as automated assembly and pick-and-place. It closes by examining the importance of cable glands in ensuring cable and robot motion reliability.
Motion basics
The key differentiator between VFD cables for general industrial applications and industrial robotics is the ability to support rapid, repeatable, and precise motion. That can place a lot of stress on the cables.
Most VFD cables are rated for some level of flexibility. Often, that means they can be bent to facilitate routing the cable during installation. That can be useful in stationary applications, but it’s not nearly enough for robotics.
Factors that impact cable flexibility include the type of insulation, the addition of wraps or shielding, the conductor size, and stranding structure, among others. Achieving a high number of flexing cycles requires careful attention to every aspect of cable construction, including a jacket material that’s both thin and abrasion-resistant.
The cable’s bend radius is a basic specification that indicates how tightly it can bend without damage, but it doesn’t indicate the number of flexing cycles the cable can withstand. Understanding the type of motion that will be experienced is crucial for selecting the proper cable and ensuring the required life cycle.
Bend radius is one aspect of continuous flex, also called rolling flex, that’s an important specification for robotics applications. Torsional flexing is another type of flexibility that’s crucial in certain types of robots; in some cases, the cable can rotate around its axis ±360° (Figure 1).
Figure 1: Bending flex can be beneficial in most industrial cable installations. Continuous flex and torsional flex capabilities are required for industrial robotics. (Image Source: LAPP)
Continuous flex refers to the repeated, linear, back-and-forth movement of a cable, commonly found in applications like automated equipment, gantry robots, or cable track systems. This type of flexing subjects the cable to constant abrasion and stress, requiring it to withstand continuous movement without failure.
Cables designed for torsional flexing can withstand constant twisting. In a robot, the cable may also be pulled back and forth, combining linear continuous flexing with rotational torsional flexing. Cables in applications such as multi-axis articulated robots, industrial painting robots (especially in their end-effectors), and pick-and-place systems can experience torsional flexing.
Unlike many other areas in industrial process control, there’s no standardized terminology to describe or quantify the different types of cable flexibility. Each manufacturer must develop its own classification system, usually based on a series of IEC standards, such as IEC 60228, “Conductors of insulated cables.”
IEC 60228:2023 specifies the nominal cross-sectional areas for conductors in electric power cables and cords of various types and applications. Requirements for the numbers and sizes of wires, as well as resistance values, are also included.
It categorizes conductors into classes based on their flexibility and construction, including solid (Class 1), stranded (Class 2), flexible (Class 5), and highly flexible (Class 6) conductors. More flexible conductors have a larger number of finer wires within the strands.
In addition to referring to various IEC standards, LAPP’s continuous flex test methodology has earned UL Verification based on a detailed audit. The audit included requirements for calibrated specialty equipment, well-trained staff, and controlled documentation, all in compliance with ISO/IEC 17025, an international standard that sets the requirements for the competence of testing and calibration laboratories.
LAPP defines a series of five continuous flex performance levels and two levels of performance for torsional flex cables (Table 1). LAPP has also defined three levels of bending flexibility for basic industrial cables and three levels of torsional flexibility for specialty cables used in wind turbines.
Table 1: Continuous flex and torsional flex performance levels as defined by LAPP. (Table Source: Lapp)
Light weight is also an important consideration when selecting robotics cables. Industrial robots experience rapid acceleration and braking, and lightweight cables minimize the amount of mass, facilitating rapid motions and improving the cable’s ability to reliably withstand the rigors of millions of bending and twisting cycles.
Basic robot motion
The LAPP ÖLFLEX VFD 1XL cable features a CF-01 continuous flex rating, making it suitable for applications such as gantry robots. These cables are oil- and UV-resistant, as well as shielded. The enhanced cross-linked polyethylene (XLPE) insulation, also known as XLPE plus, possesses the mechanical properties required for robotics and features a reduced outer diameter, which supports installation in tight spaces while maintaining CF-01 flexibility.
The ÖLFLEX VFD 1XL is a good example of the importance of cable construction on flexibility. Basic models like 701703 with fine tinned copper wires, shielding consisting of barrier tape and triple layer foil tape (100% coverage), plus a tinned copper braid (85% coverage) are rated for CF-01 flexibility with a rated cycle life range of 1 to 2 million cycles and chain lengths up to 15 feet.
Adding a pair of individually foil-shielded wires for a signal connection with an uninsulated tray cable (TC) drain wire can simplify installations by enabling one cable to handle both power and signal but at the expense of a lower flexibility rating. ÖLFLEX VFD 1XL with signal cables have a flexibility rating of FL-02, making them suited for general industrial applications.
For example, the model 701715 ÖLFLEX VFD 1XL with signal has an FL-02 rating and is highly flexible due to its “continuous flexing design attributes.” However, it lacks a rated cycle life, making it unsuitable for most robotics applications (Figure 2).
Figure 2: With the added signal wires, this ÖLFLEX VFD 1XL cable has a flex rating of FL-02, suitable for general industrial applications. Without the signal wires, the flex rating increases to CF-01, making the cable ideal for basic robotic applications. (Image Source: DigiKey)
Maximum robot motion
For the most demanding robotics applications, designers can rely on the ÖLFLEX ROBOT F1 cable, which features a high torsional flex rating of TCF-01. That level of torsional flexibility is achieved by both basic models, such as 0029591, and shielded models, like 0029689. Both have extra-fine copper wires, as specified in IEC 60228 and thermoplastic elastomer (TPE) insulation.
Smaller cables from 0.14 mm² up to 0.5 mm² have tinned copper wires, while those ≥0.75 mm² have bare copper wires. The main performance difference is the maximum torsion rating, which is ±360° per meter for unshielded cables and ±180° per meter for shielded cables.
The maximum torsion rating indicates the amount of twisting the cable can withstand over a 1-meter length without being damaged. Cables like these with a TCF-01 flexibility rating can withstand continuous motion and high dynamic stress over 10 million torsion cycles.
ÖLFLEX ROBOT F1 cables are specifically designed for use in applications such as multi-axis articulated robots, welding robots, and industrial paint-spraying robots. For example, painting robots are often six-axis designs that can implement intricate movements requiring significant levels of twisting (Figure 3).
Figure 3: Industrial painting robots. (Image Source: LAPP)
Not all axes in a multi-axis robot necessarily experience the same type or level of flexing. Depending on the design, some axes can experience twisting of ±360°, sometimes in opposite directions, while other axes experience more linear continuous flexing and little or no twisting. The ÖLFLEX ROBOT F1 cables can be used in all motion scenarios but are especially suited for applications where combined twisting and bending stresses occur, such as connections to end-effector tools.
Intermediate robot motion
ÖLFLEX SERVO FD low capacitance hybrid servo cables, such as model 1023278, feature extra-fine wire strands of bare copper, as defined in IEC 60228, a polyurethane (PUR) outer sheath, and are designed for highly dynamic power chain applications. They are suited for applications that require high cycle lives and an intermediate level of flexibility, such as some gantry robot designs and assembly or pick-and-place machines.
These cables are rated CF-04 for continuous flexing and are designed for high-cycle, continuous flexing applications with long cable tracks supporting chain lengths of up to 300 feet. They have a cycle life rating of 8 to 20 million cycles. The signal pair is suitable for Hiperface DSL and single-cable solution (SCS) open-link interfaces. They can withstand the stress of high acceleration.
Importance of strain relief
The protection provided by strain relief is essential in robotics applications where cables experience significant mechanical stress. It also ensures the longevity of cable connections by preventing the transfer of external forces to internal connections, such as solder joints or connector pins.
LAPP’s SKINTOP SL/SLR series are durable, liquid-tight, easy-to-assemble strain relief cable glands designed for robotics applications. For example, the S2221 has a clamping range of 9 to 16 mm and is suited for medium-diameter VFD cables (Figure 4).
Figure 4: Cable glands like this provide strain relief for cables in applications like industrial robotics. (Image Source: LAPP)
The neoprene bushing in SKINTOP SL/SLR cable glands provides a liquid-tight and dust-proof hermetic seal rated for IP68. They also have an integrated locking mechanism with an internal ratchet for vibration-proof protection.
Conclusion
It’s important to understand the motion requirements when selecting cables for robotics. Will the cable experience continuous flexing, similar to a gantry robot, torsional flexing, similar to an industrial painting robot, or both? And how much flexing? For example, some multi-axis articulated robots can flex ±360°, while others require only ±180° of flexing.
The addition of features like signal wires can reduce the flexibility rating of a cable, as seen with ÖLFLEX VFD 1XL versus VFD 1XL with signal wires. Other cables, such as ÖLFLEX SERVO FD, can maintain very good levels of continuous flex even with integrated signal cables and serve the needs of pick-and-place and assembly robots. Finally, the use of cable glands can deliver strain relief needed to protect both the cables and any attached electronics, as well as provide enhanced environmental protection.
Recommended reading:
- Autonomous Mobile Robot Types and Applications
- How SMEs Can Use an Industrial Metaverse to Explore and Deploy Robotic Solutions Rapidly
- What are the Key Factors Used to Classify Industrial Robots?
- How to Optimize Intra Logistics to Streamline and Speed Industry 4.0 Supply Chains – Part One of Two
- What are the Important Considerations when Assessing Cobot Safety?
- Safely and Efficiently Integrating AMRs into Industry 4.0 Operations for Maximum Benefit
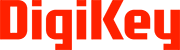
免责声明:各个作者和/或论坛参与者在本网站发表的观点、看法和意见不代表 DigiKey 的观点、看法和意见,也不代表 DigiKey 官方政策。