Learning Sensorless Brushless DC Motor Control the Easy Way
投稿人:Convergence Promotions LLC
2011-10-26
Microchip’s new low cost BLDC development tool makes learning advanced, sensorless BLDC control easy
Much like cell phones have become an indispensable part of our daily lives, electric motors accompany us wherever we go. An electric motor turns the fan and compressor in our house, washes and dries our clothes, and even blends that critical iced coffee drink for our afternoon shot of caffeine. Electric motors make up a huge percentage of the energy we use every day, so the more efficiently we can spin a motor, the more energy we can save. Also, because they are in so many products and perform so many different functions, being able to precisely control an electric motor is a very important task.
Microchip offers motor control solutions for any type of electric motor system. In particular, Microchip’s dsPIC® Digital Signal Controller (DSC) and PIC24 microcontroller (MCU) products enable motors to be controlled digitally, bringing precise control and efficiency to the motor control system. Microchip’s latest dsPIC DSC products feature innovative features and low prices to fit the needs of a sensorless brushless DC system. One of the most popular types of motor is the brushless DC motor (BLDC). The key feature of a BLDC motor is that it, well, doesn’t have brushes! Inside a BLDC is a permanent magnet attached to the shaft that rotates, or rotor. The BLDC motor has three sets of coils positioned around the rotor. Once a coil is energized it produces a magnetic field which causes the permanent magnet on the rotor to align with that magnetic field, which in turn rotates the rotor.
However, the rotating action stops when the rotor is aligned with the magnetic field created by the energized coil. To keep the rotor in motion, the coils are energized in a particular sequence, 120° out-of-phase from one another. This is what makes the BLDC motor a “three phase motor.” See Figure 1.
Figure 1: To keep the rotor in motion, the coils are energized in a particular sequence, 120° out-of-phase from one another.
The process of energizing and de-energizing the coils to keep the rotor spinning is called commutating. What makes a BLDC such an attractive motor is that commutation occurs electrically, without any mechanical interaction between the rotor and coils. This makes the BLDC motor very reliable and at the same time relatively inexpensive to build. The challenge in controlling a BLDC motor is knowing when to commutate, as commutation must occur at precise points during rotation in order for the motor to have maximum torque and smooth operation. Most BLDC motor systems use Hall Effect sensors to detect where the shaft is in its rotation and thus when to commutate. This introduces more cost, in cabling and sensors, and another point of failure. A more advanced system is to eliminate the sensors entirely by sensing the back Electromotive Force (back EMF) generated by the motor’s rotation and calculate when to commutate based on the back EMF of the motor. A digital signal controller, such as a dsPIC DSC, greatly simplifies implementing this kind of “sensorless” motor control system.
Stop right there! Don’t think another thought! “Advanced” doesn’t have to mean complicated or… expensive! Digital signal controllers provide all the functionality of an MCU with these convenient “tools” for digitally controlling virtually any motor type. One example is described in Microchip’s app note AN1160 on sensorless BLDC motor control which includes easy-to-follow example software. In addition, there are many motor control tools on the market that make learning simple but are often cost prohibitive. Breaking this cost barrier is Microchip’s $90 Motor Control Starter Kit (Figure 2). This kit features Microchip’s newest low cost, high performance dsPIC DSC. With advanced motor control systems within reach, let’s take a look at how a sensorless BLDC system works and at what a low cost sensorless BLDC development system looks like.
Take another look at Figure 1. Notice how there is always one coil (or phase) that isn’t driven? The motor’s back EMF will be visible on this phase because it isn’t being driven. By sensing the voltage on this phase, it is possible to reconstruct the back EMF waveform for this phase. With careful timing, this can be done for each phase of the motor, enabling all three back EMF signals to be reconstructed. Since the commutation times are based on the back EMF of the motor, the commutations times can be found from the reconstructed back EMF waveform, eliminating the need for sensors. Details on sampling the back EMF, reconstructing the back EMF waveform, and detecting when commutation should occur can be found in numerous app notes from many suppliers. Microchip’s app note AN1160 uses a zero crossing method to detect when to commutate and also uses a digital filter on the sampled back EMF waveform to reduce noise introduced by switching of the motor driver. Other suppliers use similar methods in their app notes to achieve sensorless BLDC control.
While app notes and example software are very useful in explaining how a sensorless BLDC system works, the real world is a much better teacher. Spinning a real motor and executing software on a real digital signal controller can quickly illustrate many concepts that might easily be misunderstood by just reading an app note. To help with this, there are numerous sensorless BLDC development boards available. The Motor Control Starter Kit (MCSK DM330015-ND) from Microchip is one of the least expensive and most full featured boards available. The MCSK includes a high performance dsPIC digital signal controller, an on-board USB programmer and debugger, a BLDC motor driver and a BLDC motor right on the board. See Figure 2.
Figure 2: Image of Motor Control Starter Kit.
Learning requires being able to see all the signals in a system, so the MCSK includes test points to easily connect a scope and see all the important signals, including easy access to the motor phases. Also featured on the MCSK is Microchip’s capacitive touch technology, which enables innovative and reliable human machine interfaces. With everything built right onto the board, including the motor, learning sensorless BLDC motor control can happen anywhere with just a single board. For more information on the MCSK please visit http://www.microchip.com/Developmenttools/ProductDetails.aspx?PartNO=DM330015
The dsPIC DSC included on the MCSK is Microchip’s new ultra low cost dsPIC33FJ16MC204. Running at 16 MIPS with 16 KB of Flash, this device has more than enough performance, memory, and peripherals for sensorless BLDC motor control. The peripheral set includes Microchip’s industry leading motor control PWM modules, which greatly simplifies generating the PWM signals for the motor driver. Also included are standard communication peripherals such as UART, I²C™ and SPI. These new devices also include Microchip’s capacitive touch peripheral which enables capacitive touch sensing and accurate current measurement. For more demanding applications, Microchip also offers an easy migration path to the 40 and 60 MIPS processors, which are code and feature set compatible and range in memory size from 32 KB to 512 KB of Flash. More information on the dsPIC family can be found at http://www.microchip.com/design-centers/16-bit.
Motor and motor control methods are bringing more efficiency and reliability to systems in the world around us. The low cost and high reliability of the BLDC motor will continue to make it a popular choice for electric motor systems. Sensorless BLDC control will also continue to grow in popularity, by reducing costs and increasing reliability. Development tools and software, such as Microchip’s MCSK and app note AN1160, will further accelerate the trend and make motor sensors a thing of the past.
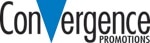
免责声明:各个作者和/或论坛参与者在本网站发表的观点、看法和意见不代表 DigiKey 的观点、看法和意见,也不代表 DigiKey 官方政策。