Keeping Track of Industrial Processes with Sensors
投稿人:DigiKey 欧洲编辑
2012-06-07
The success of industrial processes is based in large part on creating stable, repeatable conditions in which they are carried out. This helps reduce the variability in the process, improving the chances of creating a consistent output as well as making troubleshooting problems much easier.
Sensors can be used to build measurement, feedback and control systems that stabilize the operating conditions for industrial processes. But what do you measure? We will look at some basic sensor types, relevant to industrial process control, which measure factors including temperature, pressure, humidity, liquid levels, gas concentrations, and mass flow. Understanding what sensors are available, how they work, and their capabilities and limitations helps designers create monitoring systems that provide the kind of accurate information necessary to ensure stability and repeatability in industrial processes.
Temperature
Tracking temperature is one of the most basic elements of process control. Although we are used to thermistors and temperature probes, other approaches are emerging to make it easier to gather multiple temperature readings from large installations.
Take Maxim’s DS18S20, a ‘1-wire’ digital thermometer, which only needs a single data line to communicate with a host controller. The part is available in a three-leaded TO-92 package, on which two of the leads are dedicated to power and ground and the third is the data output, and in an 8-pin Small Outline package with five unconnected leads. The thermometer can even draw its power from the data line, removing the need for a separate supply and simplifying installation.
Each device has a unique 64-bit serial code stored in an onboard ROM, so that multiple sensors can be connected on the same 1-wire bus and yet still be addressed individually by a microprocessor. The output is a 9-bit code representing temperatures between −55 and +125°C. Accuracy is ±0.5°C over the range of −10 to +85°C.
The part can also be programmed with upper and lower temperature trigger points, which if reached will set an Alarm flag. The master controller can poll all devices on the 1-wire bus specifically for this Alarm condition.
Applications for distributed digital thermometer systems that can be built with the part include heating and ventilation controls, temperature monitoring systems for buildings and equipment, and process monitoring and control systems.
Pressure sensing
There are two ways of measuring pressure: as an absolute, compared to a reference such as pure vacuum, and as a relative figure, the difference between the pressures in two places. Absolute pressure measurements need to have a reference against which to compare. This is why barometers have a sealed and evacuated chamber against which the ambient pressure is measured. Honeywell does something conceptually similar in its SDX range of plastic-packaged silicon pressure sensors, which have an internal vacuum reference and a sensing port through which the ambient pressure is registered.
The parts are calibrated and temperature-compensated to give a stable output over a working temperature range of 0 to +50°C, and pressure ranges including 0 to 15 PSI, 0 to 30 PSI, and 0 to 100 PSI. The output is a voltage proportional to the absolute pressure and ratiometric to the supply voltage, which can range up to 20 V DC.
The parts are supplied in the same sort of DIP package used for ICs, which makes assembling products using them much easier. Although the package is solvent-resistant, Honeywell specifies these parts are for use with non-ionic working fluids such as air and dry gases. For more hostile environments, Honeywell also offers a series of stainless-steel pressure sensors based on a piezoresistive sensor chip held in an oil-isolated housing. They are designed to be robust enough to be built into equipment such as industrial controls, hydraulic controls, and tank pressure monitoring systems.
Parts are available to measure pressure ranges up to 5000 PSI, with or without integral temperature compensation and calibration sensors. Operating temperature range is −40 to 125°C, although the compensated temperature range is less, at 0 to 82°C.
It is worth noting that the full-scale span (i.e. the difference in output between zero pressure and maximum pressure readings) on these devices is not large – on the compensated versions it is just 4 mV (from 98 to 102 mV in most cases), while on the uncompensated versions the span is slightly greater, at a maximum of 210 mV (from 290 to 500 mV) for the 5000 PSI part. This means that the output signals will have to be carefully shielded from interference, particularly in industrial environments which are likely to suffer from conducted and radiated noise, if they are going to be consistently useful.
As the name implies, differential pressure sensors measure the difference between two pressure regimes and so need two ports. Freescale Semiconductor’s MPXV7002 series of piezoresistive transducers uses an ingenious package to achieve its differential sensing. Like Honeywell’s SDX series, the parts are built using silicon micro-machining techniques to create what is effectively a strain gauge, with, in Freescale’s case, the added advantage of integrated temperature compensation, calibration, and signal-conditioning circuitry on the same die.
Figure 1: Freescale Semiconductor’s differential pressure transducers use an innovative package to create the two chambers necessary for differential pressure sensing.
The die is mounted in the package so that there is a void above it and a void below it, both of which having ports. A gel coating isolates the die surface and the wire bonds that connect its signals to the package from the environment, but allows the sensor diaphragm to be influenced by the ambient pressure. Various packages are available to route the ports to the side or top of the sensor for convenient connection to sensing tubes.
This approach, while robust enough, means that the part is most suitable for sensing dry gases. The part senses ±0.3 PSI, producing an output voltage proportional to the differential pressure that has a typical full-scale span of 4 V DC with a 5 V DC supply. Accuracy is quoted at a typical error of 2.5 % over the temperature-compensated range of 10 to 60°C.
Humidity sensing
There are two major approaches to sensing humidity in industrial applications, using either resistive or capacitive techniques.
TDK has a range of resistive humidity sensors, the CHS series, which benefit from the simplicity of the resistive approach. The parts, which are available in variants for industrial, consumer, and office use, work from a 5 V DC supply and include support circuitry on board so you do not need to add control circuitry or to calibrate them. The measurement range is 5 % to 100 % relative humidity and the output varies linearly up to 1 V DC at 100 % relative humidity. This means that relative humidity can be read from the sensors as a voltage measurement.
TDK says the operating temperature range for the parts is +5 to +45°C, and that the temperature dependency of the measurements is just ±5 %.
Measurement Specialties produces a capacitance-based humidity sensor that offers a greater sensing range, operating temperature range and accuracy than the TDK part, at the cost of a little more complexity in its use.
The HS1101LF will sense between 0 and 100 % relative humidity, operates between −60 and +140°C and has an accuracy of ±2 %. It is based on a ‘patented polymer structure’, and is used as a humidity-controlled variable capacitor in oscillator circuits, which can be designed to output a voltage or a frequency that varies with humidity. As the response of the part is non-linear, the company provides both the polynomial equation of the way its capacitance varies with humidity, look-up tables relating humidity with capacitance, and the output frequency of a suggested 555-based sensing circuit. The part can be driven with an oscillating signal of 10 KHz at 1 V, although it will operate from 5 KHz to 30 KHz.
Figure 2: The HS1101LF capacitive sensor from Measurement Specialties can be used in this circuit to produce an output frequency that varies with humidity.
RH (%) | 0 | 5 | 10 | 15 | 20 | 25 | 30 | 35 | 40 | 45 | 50 |
Fout (Hz) | 7155 | 7080 | 7010 | 6945 | 6880 | 6820 | 6760 | 6705 | 6650 | ||
RH (%) | 55 | 60 | 65 | 70 | 75 | 80 | 85 | 90 | 95 | 100 | |
Fout (Hz) | 6600 | 6550 | 6500 | 6450 | 6400 | 6355 | 6305 | 6260 | 6210 |
Figure 3: The non-linear output of the circuit can be linearized using this look-up table.
One issue with a capacitive-based sensing strategy is that designers have to be careful to control stray capacitances between the part and the board layout. Given that the sensor has a nominal capacitance of 180 pF, a 25 pF stray capacitance would cause the sensor to under-report a 75.5 % relative humidity by 4 %. Measurement Specialties says that the board and the components need to be carefully coated to prevent unexpected deviations from true measurements in high humidity conditions.
Liquid level
Sensing liquid levels is an important part of industrial process control, which can be accomplished in a number of ways.
Honeywell’s LLE series of sensors uses an LED and a phototransistor mounted in a liquid-proof package to do the sensing. It works on the principle of total internal reflection: when no liquid is present, the light from the LED is internally reflected from the dome of the window in the package to the phototransistor. When liquid covers the dome, the effective refractive index at the boundary between the dome and the liquid changes and allows some of the light to escape. The phototransistor receives less reflected light and its output switches, indicating the presence of a liquid.
The part is available in screw- and push-in packages, and is protected against reverse polarity, over-voltage, short circuits, and transients. Honeywell suggests it could be used in home appliances, vending machines, medical applications, compressors and machine tools, among other applications.
MEDER electronic offers another approach: a float switch, which is mounted vertically over the liquid to be sensed. MEDER offers the switch with both a polypropylene float, for use with water and dilute acids, and a polyamide float, for use in oil, gasoline and brake fluid. Both floats include embedded magnets whose field drives a reed switch in the body of the part. The switch can be normally open or normally closed, and can be specified to switch up to 10 W, or up to 100 W.
Cynergy 3 also offers a float-based level switch, the RFS 10 series, which mounts the switch itself horizontally through the side of the vessel, and has a hanging float that pivots as the liquid level rises. The switch is normally closed and so can be used to automatically stop a vessel filling when it reaches the set level. The part is available with floats made in various materials to suit a range of applications, which, the manufacturer says, could include wall-mounted kettles and hot vending machines.
Gas
Many industrial processes involve the use of a variety of gases whose concentrations have to be monitored if the process is going to work safely and with repeatable results. One of these gases is oxygen. Honeywell offers the GMS-10, an oxygen monitor that was initially designed for use in boilers and has now been developed into a product range addressing applications such as exhaust gas testing, oxygen monitoring on aircraft, and in medical test equipment.
The sensor will measure oxygen pressures ranging from 2 mbar to 3 bar, with an accuracy of better than 5 mbar.
It is based on two zinc-oxide discs separated by a small hermetically-sealed chamber. One of the discs acts as a reversible oxygen pump that fills and empties the chamber in cycles. The second disc measures the ratio of the partial pressure difference and generates a corresponding sense voltage. A heating element produces the 700°C required for the zinc-oxide disc to act as an oxygen pump. The time taken for the pump to achieve particular minimum and maximum pressures in the chamber is used as a proxy for the partial oxygen pressure in the sampled environment.
The part has power inputs for the heater and the pump, and produces a voltage output that varies linearly with the amount of oxygen in the air. It does not need a reference gas to operate, or external temperature compensation.
Parallax Inc. offers a sensor for another important gas: benzene. The MQ3 is made up of an aluminum oxide tube covered in a tin-oxide sensing layer and heated internally by a nickel-chrome heater coil. The tube is mounted on electrodes protruding from a resin base so that gas can flow around it freely. The whole assembly is covered by stainless-steel gauze to prevent explosions.
The resistance of the tin-oxide layer varies depending on the concentration of volatile gases in the air: the sensor reacts to alcohol, benzene, hexane, methane, liquid petroleum gas, and carbon monoxide. Because of the way it works, heating a sensing material to prompt a reaction that changes the material’s resistance, the sensor is sensitive to the ambient temperature and humidity, as well as the presence of gases other than the one you want to sense. For this reason, the company recommends calibrating the sensor at the particular temperature, humidity, and concentration of the gas for which you are testing. Applications for this particular sensor include use in breathalyzers.
Parallax also offers sensor modules that can sense carbon monoxide, methane, propane, and alcohol. A 4-pin microcontroller interface is used to read the sensors and tell when a preset gas level has been reached or exceeded.
Flow
Industrial process control often relies on an accurate understanding of the flow rate of air, gases, or liquids.
Honeywell’s AWM40000 mass-flow sensor family produces a voltage output that varies with the flow rate of gas through the part, although the relationship is not entirely linear so the output would have to be interpreted to give a linear scale. The parts are available to suit various flow rates, ranging from ±25 SCCM (standard cubic centimeters per minute) up to +6 SLPM (standard liters per minute).
The un-amplified devices need to be connected to a heater circuit, to control the heating of the sensor element, and to a sensing-bridge supply circuit. A differential amplifier can be used to boost the output and to introduce voltage offsets. In the conditioned versions of the sensor, the differential amplifier, heater control, and sensing-bridge supply circuitry are all built in.
Omron has its own range of mass-flow sensors, the DSF-01/02/05 family, in which the sensing elements are built using micro-electromechanical machining techniques. The parts are suitable for use with air, non-corrosive gas, and natural gas flows, in applications that Omron suggests could include respiratory monitoring, analysis equipment and combustion control. The parts produce an analog output between 1 and 5 V DC, and are available in versions to measure flow rates of up to 1, 2, or 5 SLPM.
Conclusion
This article has outlined some of the basic sensor types relevant to industrial process control and how they work. Careful selection of sensors in terms of how they work, their operating ranges, sensitivity and accuracy can help designers to build control systems that improve the stability of industrial environments and the repeatability of the processes that are carried out in them.
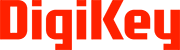
免责声明:各个作者和/或论坛参与者在本网站发表的观点、看法和意见不代表 DigiKey 的观点、看法和意见,也不代表 DigiKey 官方政策。