如何更快地获得更好的测量结果并加速产品开发
投稿人:DigiKey 北美编辑
2025-05-13
开发先进的电子和机电产品需要与时间赛跑。功能强大的全新数据采集 (DAQ) 工具有助于简化和加快开发过程,并在竞争中获胜。
这些 DAQ 工具性能优异,如用于传感器、电池和其他设备的 20 位 ±10 V 输入(每通道采样率高达 1 MS/s)、多达 16 路的数字 I/O 线、计数器、正交编码器输入、旋转变压器、脉冲/事件计数传感器(如仪表)、高速电压信号、用于电流测量的分流电阻上的压降等。
此外,还需要自动生成多种功能,包括读/写 TTL 数字线路、通过数字线路驱动低电流继电器、生成 ±10 V 输出控制信号和 ±10 V 信号以模拟传感器、生成脉宽调制 (PWM) 信号,以及对电压、数字和计数器信号进行同步。
要在市场竞争中获胜,这些综合型工具还必须简单易用,并具备模拟和数字输入/输出的独立定时引擎、自校准、USB 连接以及快速设置和集成等功能。系统应提供软件选项,如免费日志软件、API,以及对 Python 和 C/C++ 的高级支持。
USB DAQ
NI 的新型 mioDAQ USB 系统性能优良,灵活性高,可加快各种电子和机电系统的上市时间。首先是使用 USB Type C 的连接功能。mioDAQ USB 只需一根电缆即可快速连接笔记本电脑或台式电脑,进行数据采集、分析和供电。
该系统提供多达 16 个通道的 20 位分辨率和 ±10 V 测量,可支持每秒同时 100 万次采样。此外,该系统还具有各种数字输入/输出和计数器/定时器通道,可用于高性能、高灵活性测试和产品开发系统(图 1)。
图 1:所示为 mioDAQ USB 的一侧,包括各种输入/输出。USB 连接器位于另一侧。(图片来源:NI)
智能 ID 引脚与用户提供的 EEPROM 进行通信,因此可在测试台中内置智能功能。EEPROM 可直接与弹簧端子插头连接,或设计到原型板中。可通过 EEPROM 进行以下查询:
- 确认电缆是否插入正确的端口
- 采集被测设备 (DUT) 的信息,用于通道和常数映射
- 自动记录元数据
冷结补偿 (CJC) 与热电偶一起使用。该功能可校正热电偶热端(测温位置)和冷端(热电偶导线连接测量系统的位置)之间的温差。CJC 大大提高了热电偶测量的准确性,尤其是在冷结温度波动的情况下。
性能可靠
mioDAQ 采用台式设计,经久耐用,可用于全自动测试夹具。该设备可以在长达 10 年的时间内保持精度不变而无需重新校准,因此适用于频繁的重新校准会影响生产效率的制造测试或现场应用。此外,该设备还包括两年校准一次的型号,非常适合实验室台架测试和验证应用。
自校准功能可根据工作环境的差异和任何制造组件的差异进行调整。只需点击硬件配置实用程序中的一个按钮,即可启动自准校准。mioDAQ 驱动程序会将自校准调整参数存储在板载 EEPROM 中,采用多变量多项式实现,既不会明显影响处理速度,又实现了优于较简单线性校准方程的性能。
mioDAQ 支持的测量示例包括:
- 传感器和其他设备,±10 V 信号,速度每通道高达 1 MS/s
- 分流电阻上的电压降
- 电池电压(±10 V 峰值测量值)
- USB 或电池供电型设计的电源轨
- 脉冲和事件计数
- 正交编码器
- 解析器
- 用于测量线性位移的弦线电位计
- 低压电流传感器和互感器
一些 mioDAQ 设备支持多路复用,以实现更高的通道数。多路复用模式使用单个模数转换器处理多个模拟输入通道。虽然这样做会有效地增加通道数量,但要求多路复用通道共享总采样率,从而降低了单个通道的采样率。
此外,控制信号还可自动用于各种功能,如:
- ±10 V 输出信号
- 数字输出信号
- 外部继电器(通过数字线路控制)
- 生成脉冲宽度调制 (PWM) 信号
- 模拟传感器
- 连接到 LED
- 时钟和触发器
四种 mioDAQ 型号,包括零件编号为 789887-01、789882-01、789888-01 和789884-01 的器件,使用户能够获得所需的确切性能,以便快速设计更好的产品并进行研究(表 1)。
|
表 1:mioDAQ USB 分为四种型号,用户可根据应用要求选择相应的性能。(表格来源:NI)
汽车发动机舱
要实现最大效益,就必须充分了解设备的规格和功能。例如,mioDAQ 支持三种模拟输入终端配置。
在差分模式下,可测量两个输入终端之间的电压差,用于最大限度地降低共模噪声的影响。在单端参考 (RSE) 模式下,测量与地隔离的特定参考点的信号电压。如果需要测量浮地或隔离地的信号电压,且没有外部接地基准,则可以使用非基准单端 (NRSE) 模式。
独立的定时引擎可为模拟输入 (AI) 通道、模拟输出 (AO) 和数字输入/输出 (DIO) 线路设置不同的速率。例如,用户可以选择:
- 将系统同步到相同的时钟,并以相同的速率和时间使用 AI、AO 和 DIO
- 触发模拟输入电压值
- 同时触发多个子系统,使其以不同的运行速率启动
- 重新触发数据采集,根据触发条件采集固定数量的样本,然后复位并等待下一次触发事件
NI mioDAQ USB 可编程功能接口 (PFI) 是一系列数字 I/O 线路,可将其配置为静态数字 I/O,或用于计数器/定时器、触发和定时功能。这些接口提高了控制和监测的灵活性。
例如,PFI 线路可用于模拟采集、生成波形或计数器事件等功能。软件支持包括 NI-DAQmx 驱动程序和配置实用程序,简化了 PFI 线路的使用。
项目快速启动
在 NI mioDAQ 包装盒中,用户可以找到快速启动所需的硬件,包括 NI mioDAQ、带锁定螺丝的 2 m 长 USB-C 到 USB-C 连接线(零件编号 789956-02)、弹簧端子(零件编号 785502-01)、提供应力消除的端子后壳(零件编号 785080-01)以及用于拧紧 USB 连接器上的锁定螺丝的 NI 螺丝刀。电缆、弹簧端子和后壳也可单独购买(图 2)。
图 2:NI mioDAQ 随附了开始使用并加速开发工作所需的连接器和电缆。(图片来源:NI)
通过软件加快设置速度并提高灵活性
用户通过扫描设备上的 QR 码即可开始设置 mioDAQ。用户通过此操作可进入 NI 网站页面,然后下载必要的软件和资料。可用资源包括用户手册、设置视频、引脚分布图和软件,其中包括下载 FlexLogger Lite 和 LabVIEW、Python 和 C/C# 驱动程序的链接,可确保设置过程顺利进行并尽量缩短设置过程。
NI Measurement & Automation Explorer (MAX) 免费软件提供对 NI 硬件的访问,是与 NI 硬件和软件交互的中枢。MAX 软件与所有 NI 驱动程序、系统配置一起自动安装。通过 MAX 软件,用户可以配置设备、排除故障,甚至创建用于测试目的的模拟设备,而无需物理硬件。
NI FlexLogger Lite 是一款免费的软件,适用于希望获取数据并做记录的简单项目或新用户。无需编程即可为传感器及其他测量装置实现数据的快速配置、可视化与记录。
FlexLogger Lite 可自动识别 NI DAQ 硬件,并提供传感器专属的配置选项。该软件可对获取的数据进行实时可视化,使用户能够在测量的同时监控测量结果。该软件还支持以常见格式记录数据,如 Excel 或二进制 .tdms文件。
FlexLogger Lite 是全功能 FlexLogger 软件的配套软件,用户可以选择升级到完整版,以获得更多高级的功能,如自动测试、定制测量和扩展到多个机箱。
对于更复杂的需求,用户可以使用 LabVIEW。该软件可在 Windows 和 Linux 系统中运行,为自动化、测试和测量应用提供图形化编程语言和开发环境。与传统的文本编程相比,其图形化界面更容易直观地可视化复杂的过程,使一目了然。
该软件广泛应用于航空航天、汽车和过程等行业,可实现测量、测试和数据采集的自动化。该软件支持数据可视化和分析,并具备确定性行为的实时控制能力。
为了获得更强大、更全面的软件环境,mioDAQ 兼容 NI LabVIEW+ 套装软件,这是一套捆绑式 NI 测试软件,旨在简化测试和验证流程。这也是一套用于自动化、数据采集、分析和报告的综合工具。以 LabVIEW 为基础,LabVIEW+ 套装的主要组件包括:
- 用于设计、管理和执行测试序列的 NI TestStand 测试框架
- 用于交互式仪器配置和控制的 InstrumentStudio
- 用于快速和可扩展数据记录的 FlexLogger
- 提供数据分析和报告功能的 DIAdem
安装选择:
mioDAQ USB 不仅仅是一个桌面设备。用户可以选择垂直或水平 DIN 导轨安装、平面面板安装和 19 英寸机架安装,以构建测试台和自动化系统。安装套件附带了直角连接器的 USB-C 电缆,有助于完成安装。此外,还提供备用 USB-C 连接器,零件编号为 789957-02。安装细节包括(图 3):
- 水平 DIN 专用夹套件(零件编号 789986-01)用于水平安装在标准 35 mm DIN 导轨上。包括一条具有直角接头的 USB-C 连接线。
- 使用编号 789955-01 为的零件,可以通过键孔实现 DIN 导轨和平面面板安装。包括一条具有直角接头的 USB-C 连接线。
- 19 英寸机架安装使用编号为 789953-01 的零件,最多可安装两台 mioDAQ 设备,包括两根具有直角连接器的 USB-C 电缆。
图 3:除桌面安装外,mioDAQ 安装组件还可用于水平 DIN 导轨(左上)、 垂直 DIN 导轨、平面面板安装(右上)以及 1U 高 19 英寸机架配置(下)。(图片来源:NI)
结语
NI mioDAQ USB 突破了硬件性能纵深并构建了软件工具广度,从而能加快高端电子和机电产品的研发进程并赢得市场竞争。首先是更简化的设置和配置,然后是长达 10 年的测量校准保证。提供多种通道数的型号选择,使用户能够根据项目需要优化配置。在任何情况下,都能提供用户所需的精确度和准确度。
推荐阅读:
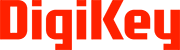
免责声明:各个作者和/或论坛参与者在本网站发表的观点、看法和意见不代表 DigiKey 的观点、看法和意见,也不代表 DigiKey 官方政策。