Enhance Sensor Measurement Accuracy via Factory Calibration and Dynamic Post-Deployment Compensation
投稿人:电子产品
2014-07-03
It was not that long ago that factory sensor calibration and self-calibrating sensors were either non-existent or a rarity. Product development advances have changed all that, resulting in a boon for designers in such areas as sensor cost, accuracy, reliability and, of course, ease of use.
Many individual sensors are now calibrated either before or after deployment. An advantage of pre-deployment calibration is that the manufacturer can calibrate many sensors at one time rather than individually, resulting in a substantial cost savings. In-place calibration, on the other hand, occurs after a sensor is installed, is much more time-consuming, and the sensor is potentially exposed to environmental factors that may affect calibration accuracy.
In the past, calibration efforts were frankly a nightmare for the designer. Challenges did not stop after the first calibration, as there were many obstacles to keeping sensors accurate. Either pre- or self-calibration provides:
- Elimination of measuring uncertainty
- Reliability of data over time
- Elimination or a significant impact on frequency of maintenance
- Minimal interference with sensor function
- Cost reduction
The complexity of sensors is dramatically increasing as more and more sensors are relied upon to perform correction computations and handle application-specific algorithms, monitor themselves, and communicate via an interface. Nevertheless — and in large part because the task of maintaining sensor systems is being helped along by storing sensor-specific correction information in non-volatile memory, allowing for the replacement of individual sensors without recalibration — sensors are becoming easier to use. Using a comparison with a reference, sensors can monitor themselves and when the reference is available as input, the sensor can recalibrate itself.
A variety of sensor types can be factory calibrated. Here is a look at temperature/humidity, inertial sensors, and a CO2 sensor module that all offer factory calibration.
One pre-calibrated sensor device is the Silicon Labs’ Si702x/2x digital I²C humidity and temperature sensors (Figure 1). The complete device family delivers fully factory-calibrated humidity and temperature sensor elements with an analog-to-digital converter, signal processing, and an I²C host interface. A CMOS-based device, it offers low power consumption.
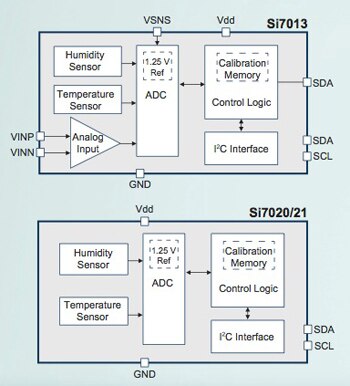
Figure 1: The Si701x/2x devices are Silicon Labs’ second-generation family of relative humidity and temperature sensors. All members of this device family combine fully factory-calibrated humidity and temperature sensor elements with an analog-to-digital converter, signal processing, and an I²C host interface.
Features of the precision relative humidity sensor include: (for Si7013/Si7021) ± 3% RH (maximum) at 0–80% RH, while Si7020 offers: ± 4% RH (maximum) at 0–80% RH. The temperature sensor has a ±0.4°C accuracy (maximum) at -10 to +85°C, auxiliary second-zone sensor input (Si7013), a 0 to 100% RH operating range and up to -40 to +125°C operating range. Power consumption is at 1.9 μW average power at 3.3 V and 1 sample per second. There is an integrated on-chip heater and the device is housed in a 3 mm x 3 mm DFN package.
Factory calibration for this sensor delivers excellent long-term stability and lifetime protection during reflow as well as in operation. An optional factory-installed filter/cover protects against contamination from dust, dirt, household chemicals, and other liquids.
Applications include AEC-Q100 automotive-qualified use, industrial HVAC/R, thermostats/humidistats, respiratory therapy white goods, micro-environments and data centers, and automotive climate control and de-fogging.
Another example is the ADIS16445 sensor device from Analog Devices, a complete inertial system including a triaxial gyroscope and a triaxial accelerometer. Each sensor in the device combines iMEMS technology with signal conditioning, optimizing the sensor’s dynamic performance. Factory calibration characterizes each sensor for sensitivity, bias, alignment, and linear acceleration (gyroscope bias) so that each sensor has its own dynamic compensation formulas to ensure accurate sensor measurements.
The ADIS16445 (Figure 2) is a simple, cost-effective way to integrate accurate, multi-axis inertial sensing into industrial systems. All required motion testing and calibration are part of the production process at the factory so that integration into the application is both easy and fast. Tight orthogonal alignment also simplifies inertial frame alignment when used in navigation systems.
Features include a triaxial digital gyroscope with digital range scaling, ±62°/s, ±125°/s, ±250°/s settings and <0.05° axis-to-axis misalignment spec. The triaxial digital accelerometer has a ±5g minimum and the sensor offers autonomous operation and data collection, does not require external configuration commands, has a 175 ms start-up time, and comes with factory-calibrated sensitivity, bias, and axial alignment, as well as a calibration temperature range of −40° to +70°C.
Applications include platform stabilization and control, navigation, and robotics.
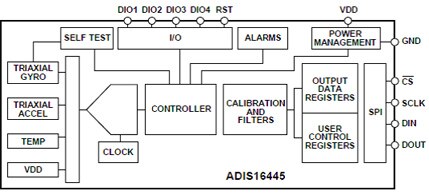
Figure 2: Working diagram of the Analog Devices ADIS16445 inertial sensor with factory calibration.
Another example of factory calibration where we see the importance of software is the Telaire 6613 CO2 Module from Amphenol Advanced Sensors (formerly GE Sensing). The module is designed to meet OEM volume, cost, and delivery requirements. All units are factory calibrated to measure CO2 concentration levels up to 2,000 and 5,000 ppm, and dual-channel sensors are available for higher concentrations.
Features include a flexible CO2 sensor platform designed to interact with other microprocessor devices, and the elimination of the need for calibration in most applications with Telaire’s patented ABC Logic software.
ABCLogic software enables C02 sensors to automatically calibrate themselves once installed in the field, eliminating maintenance concerns. All sensors with ABC Logic have a Lifetime Calibration Guarantee, whereby the supplier will provide calibration for the sensor if it is found to be out of calibration.
Gas sensors typically drift and the extent of drift depends on the quality of the components and design. Even a small amount of drift, however, will cause a need for recalibration, which means a maintenance visit for each sensor, and performing recalibration routines that take up to 20 minutes. If this happens frequently, it will wipe out any energy-saving benefit that could have come from CO2-based demand controlled ventilation.
Telaire self-calibrating sensors (Figure 3) have been on the market for years, and their first products are still accurately measuring C02. Most have never been field calibrated.
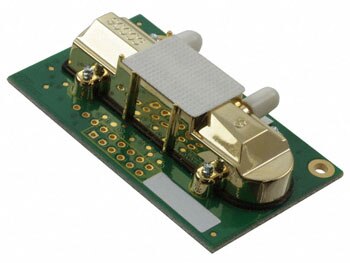
Figure 3: Telaire’s CO2 module comes complete with its ABCLogic calibration software.
In summary, calibration and self-calibration provide designers and applications much in the way of reliability and accuracy, and most of all speed of implementation. This article has presented the benefits of factory calibration and examined several excellent examples of sensors provided by major suppliers offering this advantage.
For more information about the devices discussed in the article, use the links provided to access product pages on the DigiKey website.
免责声明:各个作者和/或论坛参与者在本网站发表的观点、看法和意见不代表 DigiKey 的观点、看法和意见,也不代表 DigiKey 官方政策。