Behind the Robot: Sensing, Safety, and Control in Industry 4.0
投稿人:DigiKey 北美编辑
2025-06-19
Modern industrial robotics systems rely on increasingly sophisticated infrastructure to support evolving artificial intelligence (AI) and machine learning (ML) capabilities, seamless interconnectivity, and scalable deployment across factory floors. These systems require sensors, safety hardware, circuit protection, and control components that meet the demands of high bandwidth, real-time responsiveness, and stringent functional safety standards.
This article explores the foundational technologies behind Industry 4.0 robotics, focusing on how sensor and safety solutions from SICK and industrial control components from Eaton contribute to safe motion control, adaptive system behavior, and deterministic decision-making. Topics include key enablers for resilient, intelligent automation, such as sensing architectures, machine safety compliance, fault-tolerant control strategies, and the integration of distributed edge automation networks.
Advanced sensing systems for dynamic factory environments
As shown in Figure 1, Industry 4.0 robots leverage advanced sensors to operate safely and efficiently on factory floors. Despite harsh conditions, such as variable lighting, airborne particulates, and mechanical vibration, these sensors must rapidly process real-time data to accurately track human personnel, mobile robots, and fast-moving assembly lines.
Figure 1: Multi-axis Industry 4.0 robotic arms use integrated sensors and real-time feedback to operate precisely and quickly. (Image source: Igus)
Robotic platforms integrate multiple sensor modalities to support spatial awareness and millisecond-level responsiveness. Sensor fusion algorithms combine these inputs to generate a coherent, real-time model of the robot’s operating environment. Vision systems manage object detection and localization, while safety-rated laser scanners monitor restricted zones for proximity violations. Low-latency time-of-flight (ToF) sensors capture three-dimensional spatial data, enabling reactive path adjustments and context-aware behavior.
Robots also rely on internal and contact-based sensors to refine motion control and interaction. Tactile sensors — including force/torque sensors and limit switches — provide feedback for grasping, assembly, and compliant tasks. Inductive, capacitive, and ultrasonic proximity sensors detect nearby objects without contact, typically at shorter ranges than ToF systems. Encoders and potentiometers track joint position and velocity for precise motion planning, while inertial measurement units (IMUs) measure acceleration and angular velocity to maintain orientation and balance. Lastly, electrical sensors monitor current and voltage to assess motor load and detect faults.
Standards-based safety for industrial robotics
Industry 4.0 robots must comply with strict international safety standards to protect human personnel and equipment. Three key standards — ISO 13849, IEC 62061, and ISO 10218 — define the functional and control system safety requirements governing robotic systems on the factory floor.
ISO 13849 outlines design and validation criteria for safety-related control components. It follows a risk-based methodology and uses Performance Levels (PL) to classify system integrity based on hazard severity, exposure frequency, and possible avoidance. IEC 62061 addresses the functional safety of electrical, electronic, and programmable control systems, applying Safety Integrity Levels (SIL) to quantify the required risk reduction. Together, these standards define how sensing and control functions must be designed, implemented, and verified in safety-critical applications.
ISO 10218 applies these principles specifically to industrial robots. It covers safety requirements for robot design, workcell layout, system integration, and operation. This includes using safety-rated sensors for emergency stops, safeguarding, and motion monitoring. These components must meet defined performance and reliability thresholds, typically demonstrated through structured testing and validation.
ISO 13849, IEC 62061, and ISO 10218 form the core of robotic safety standards. Additional standards, including IEC 60204-1 for electrical safety and ISO/TS 15066 for human-robot collaboration, extend the basic framework for safe deployment and integration.
Integrated safety systems for human-robot collaboration
Factory operators deploy safety solutions from suppliers such as SICK and Eaton to comply with functional and machine safety standards. For example, SICK’s Safe EFI-Pro system supports real-time control of safety functions across both stationary and mobile robots using integrated sensors, controllers, and actuators. As shown in Figure 2, the microScan safety laser scanner — a key component of the system — enables adaptive, situation-dependent motion detection in dynamic environments.
Figure 2: SICK’s microScan3 safety laser scanner monitors protective fields and dynamically detects motion to support adaptive safeguarding in industrial environments. (Image source: SICK)
Operators also implement SICK’s End-of-Arm Safeguard (EOAS) to maintain a dynamic protective field around robotic tool heads. EOAS leverages ToF technology to enable safe, contactless human-robot collaboration with response times under 110 milliseconds.
To complement these automated systems, SICK provides manual and perimeter safety components. The ES21 emergency stop switch allows operators to quickly halt machinery during an emergency, while the STR1 non-contact safety switch uses RFID technology for tamper-resistant guard monitoring, supporting high coding levels and compliance with EN ISO 14119.
Protective strategies for surge and voltage control
A coordinated robotic safety strategy requires both motion-level safeguards and reliable power control. Eaton’s transient voltage suppressors limit temporary surges and voltage spikes to protect sensitive components. As shown in Figure 3, FAZ-NA miniature circuit breakers, like the FAZ-C10/2-NA, protect control wiring and auxiliary components from overcurrent events.
Figure 3: Eaton’s FAZ-C10/2-NA miniature circuit breaker protects control wiring and auxiliary components from overcurrent events in industrial automation systems. (Image source: Eaton)
To support electrical safety and system integrity, Eaton also offers a broad range of circuit protection devices and manual switches, such as the BP-SRR rocker, M22S-WKV-K11 selector, and BP-STE toggle, that control equipment functions and operating modes.
Eaton’s Power-NTC inrush current limiters (ICLs) and resettable PTC fuses help safeguard circuits from high inrush currents during power-up and fault conditions. Thermal protection devices — such as the TJD thermal fuse — add a critical layer of safety by interrupting current flow to prevent excessive and dangerous heat buildup in tightly integrated robotic systems.
Fault-tolerant and distributed control systems
Factory robotics systems must maintain safe operational continuity in the event of sensor failures, actuator malfunctions, or network disruptions. Manufacturers rely on distributed fault detection, isolation, and recovery (FDIR) architectures to minimize downtime and improve system resilience. By decentralizing control logic across multiple nodes and enabling localized fault response, FDIR reduces the impact of individual component failures and helps prevent broader disruptions.
These fault-tolerant strategies are implemented through distributed control systems incorporating real-time diagnostics and built-in redundancy. Distributed control systems use integrated diagnostics to monitor critical components' health and performance continuously. Redundant sensors and communication paths maintain control integrity during primary system failures, while error-handling routines enable controlled shutdowns or transitions to defined safe states.
FDIR and the Flexi Soft safety controller
These strategies are highlighted by SICK’s Flexi Soft safety controller. As shown in Figure 4, Flexi Soft supports FDIR-based Industry 4.0 robotics by enabling decentralized safety logic through modular expansion and configurable functions designed to address specific system requirements.
Figure 4: SICK’s Flexi Soft safety controller enables decentralized safety logic and modular expansion for fault-tolerant, distributed control in Industry 4.0 robotic systems. (Image source: SICK)
SICK’s industrial-grade sensors — including encoders, pressure transducers, photoelectric sensors, and machine vision cameras such as the Ranger3 — deliver critical feedback across distributed robotic systems. These sensors, integrated at key control points, support real-time monitoring, dynamic positioning, object detection, and system-level diagnostics. This enables early fault detection, localized response, and continued operation in distributed environments.
Edge-based sensing and monitoring for smarter automation
Industry 4.0 robotics increasingly leverage edge-level sensing and monitoring to improve system insight, responsiveness, and autonomy. Instead of sending all data to centralized platforms for processing, advanced robotic systems now perform key analytics closer to the edge at the sensor or device level. This enables faster fault detection, more efficient decision-making, and improved resilience during network interruptions.
Edge-enabled devices such as industrial cameras and circuit monitors extend localized intelligence beyond control logic. They capture real-time environmental and operational data, providing machine-level visibility into conditions that affect safety, quality, and uptime. These platforms reduce latency, ease bandwidth demands, and improve coordination across distributed robotic systems.
Edge computing and embedded intelligence
These edge-based strategies are reflected in products such as SICK’s SensingCAM SEC100, which provides edge-level image capture and analysis for Industry 4.0 robotics. As shown in Figure 5, it delivers high-resolution streaming and event-triggered video recording for object recognition, process monitoring, and quality inspection.
Figure 5: SICK’s SensingCAM SEC100 delivers edge-level image capture and analysis, enabling real-time monitoring and visual diagnostics in robotic inspection applications. (Image source: SICK)
The industrial camera enables real-time visibility into blind spots and dynamic inspection areas, supporting root cause analysis by capturing image data before and after trigger events.
The SEC100 easily integrates with existing machine vision systems and supports continuous monitoring without overloading centralized resources. It also generates visual records for quality documentation, such as packaging verification and component assembly tracking. Embedded at the machine level, the SEC100 brings visual intelligence closer to the point of operation.
The shift toward localized processing and real-time insight extends to facility-level energy monitoring. As shown in Figure 6, Eaton’s PXBCM-DISP-6-XV touchscreen display interfaces with the Power Xpert Branch Circuit Monitor to provide real-time visualization of voltage, current, and power data at the panel level.
Figure 6: Eaton’s PXBCM-DISP-6-XV touchscreen display provides real-time panel-level visualization of voltage, current, and power data to support predictive maintenance and energy optimization. (Image source: Eaton)
Used across industrial systems — including robotic work cells — it helps operators identify irregularities, detect faults, and optimize energy use. The display supports predictive maintenance and improves operational visibility by enabling on-site access to circuit-level diagnostics.
System-level strategies for Industry 4.0 robotics
To operate safely and efficiently, Industry 4.0 robotic systems require a deployment strategy that unifies sensing, safety, control, and networking. Sensors and safety components must meet stringent standards while enabling adaptive safeguarding and real-time responsiveness across distributed environments. Consistent performance across diverse factory systems depends on open standards and multi-protocol communication to ensure interoperability and scalability.
Control components must process high data volumes at the edge with secure, low-latency connections to supervisory systems. Coordinating processing and feedback across distributed nodes requires precise synchronization and timing. Deterministic protocols, low-jitter signal paths, and time-aware control loops help maintain predictable behavior under dynamic conditions. Fault-tolerant architectures support safe fallback states and continuous operation, while systems that combine localized control with centralized oversight enable flexible, reconfigurable manufacturing processes.
Summary
From sensor fusion and functional safety to edge computing and fault-tolerant control, Industry 4.0 robotics depend on tightly integrated systems that ensure safe, reliable, and responsive operation in complex environments. Solutions from DigiKey suppliers such as SICK and Eaton help unify sensing, power protection, and control infrastructure — facilitating scalable deployment, standards compliance, and adaptive performance.
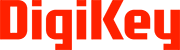
免责声明:各个作者和/或论坛参与者在本网站发表的观点、看法和意见不代表 DigiKey 的观点、看法和意见,也不代表 DigiKey 官方政策。