The Precision Challenge in Industrial Measurement
投稿人:DigiKey
2012-06-14
The dirty, noisy, messy Industrial Factory environment would seem to be the last place one would expect to find high technology. Mundane functions such as pressure, temperature, or flow of the limitless variety of materials encountered in the modern factory environment including water, petroleum, paint, fruit juice, bread dough, or steel all demand a surprising level of measurement accuracy in an exceptionally challenging environment – with ever-increasing demands for greater accuracy in order to improve costs and efficiency, and to reduce environmental impacts.
First, consider that many of the sensor technologies actually provide overall measurement accuracy less than 0.1 percent due to their own physical properties and errors due to the influence of their surrounding environment. Thermocouple and photosensor nonlinearity, load cell creep, strain gage offset drift, and other error sources all add up to degrade the measurement right at the offset.
Also, observe that the majority of popular transducer technologies provide outputs of only fractions of a volt at the output (tens of mV in a thermocouple or strain gage with excitation voltages of 10 V or less), and that their small size (for quick response time, small size, and minimum impact on the medium being measured) results in very high impedance (near-zero currents), or a high sensitivity to offset errors due to bias currents through the sensor.
Finally, observe that in most cases the physical arrangement of the process itself imposes numerous challenges, including long cable lengths which incur electrical interference, difficult packaging due to the environment involved, and of course the aforementioned dirty, noisy mess of a factory floor filled with motors, solenoids, contactors, AC heaters, and so on.
If we desire to preserve the accuracy of our sensor in this environment, we must take into account the influence of a wide variety of error-producing factors. They include the operating temperature range, which is in the range of 100°C and, therefore, requires careful temperature compensation. Offset errors, due to bias currents causing voltage drops across connectors and long lead lengths (including thermoelectric effects at bimetal interfaces) and induced noise is addressed by utilizing techniques such as two-wire, differential sensing, and ratiometric circuit configurations which take advantage of the CMRR (Common-Mode error Rejection Ratio) of a carefully-designed measurement circuit. Supply variations must also be considered, demanding a circuit designed to provide a high PSRR (Power Supply error Rejection Ratio).
Figure 1: Typical industrial pressure sensor circuit.
The numerical analysis and critical Error Budget which a designer must work through in order to reliably achieve the desired overall measurement accuracy against the factors we have reviewed here is considerable. But there are numerous techniques at his disposal to address these errors, including the circuit design techniques mentioned above, and correction and calibration techniques, which take advantage of high-resolution A/D conversion to perform software calibration, and storage of the correction coefficients in non-volatile memory. Careful selection of the sensor buffer amplifier, voltage reference, and A/D converter are crucial to achieving the measurement accuracy that we have been discussing, and new solutions that advance the state of the art in measurement accuracy continue to emerge on a regular basis. Such devices stretch the capabilities of the best leading edge technology, including design, layout and test skills, and the advanced mixed-signal semiconductor processes needed to achieve this level of performance.
Beginning at the sensor, we can see that the performance of this first interface is the most crucial portion of the design as it is called upon to get the best from the sensitive, low-level signal. This signal is then delivered to the input of an Analog-to-Digital Converter (ADC), which is called upon to digitize the output of the amplifier to the desired resolution and, hopefully, accuracy. While the accuracy specifications of the Precision ADC – obtained from bench and ATE testing under perfect conditions – are a best-case goal, in reality there are numerous error sources to be dealt with, and this most-challenging device demonstrates the pinnacle of the art of mixed-signal design and process. Also, we must remember any ADC measurement is only as accurate as the Reference Voltage connected to it, thus requiring sources at least as stable and noise-free as the sensor itself. It is easy to see why designers of such systems tend to be unusually uncompromising in their designs, cutting corners only when they are certain that their first effort has been proven to exceed the needs of their system.
In low-noise, high-precision amplifiers, the term “zero drift” has emerged over the last few years as a way to describe a level of overall accuracy in which the individual error specifications of the device – initial values and drift with time and temperature included – each introduce roughly the same magnitude of error to the total measurement in typical applications. The Vos, or Input Offset Voltage, and related Drift are the first considerations in precision amplifiers, and the leading edge, chopper-stabilized ISL28134 is quick to demonstrate exceptional capabilities, with a guaranteed offset of 2.5 µV leading the way in this product segment. With a TCVos (drift) of just 15 nV per degree Celsius and LTD (long-term drift) below the noise floor, this is definitely a device to be taken seriously. With an input bias current of 120 pA and only 250 nV noise between 0.1 Hz and 10 Hz – excellent for many types of high-accuracy, high-impedance sensors – we can see that we have a truly powerful solution worth considering for top-end designs.
Figure 2: ISL28134 input voltage noise density.
Figure 3: ISL2813x family long term drift.
Again, the first truth in data conversion is that an ADC is only as good as the Voltage Reference used to make the measurement (unless we’re running a ratiometric arrangement as discussed above) since the conversion is literally a comparison between the two voltages. Leading the precision market is the new ISL21090, a new reference that brings to the market for the first time a level of Total Error (the sum of initial value, offset drift, line and load regulation, noise, and long-term drift), which satisfies the needs of the highest-resolution applications. The industry-leading performance of this particular device has attracted a great deal of attention, including recognition as an EN-Genius Product of the Year for 2011, confirming Intersil’s increasing focus on Precision Analog solutions - and resulting success. This device is a showcase for Intersil’s state-of-the-art PR40 Advanced Bipolar Process. The PR40 process is fabricated on bonded silicon-on-insulator (BSOI) substrates and uses deep trench isolation (DTI) to build devices with complete dielectric isolation. The process features a core-bipolar foundation and optional device modules that are added as needed to facilitate product-specific, low-cost manufacturing.
Figure 4: ISL21090 voltage noise.
Turning our attention to the A/D converter, for the highest measurement accuracy, Oversampling, often called Delta-Sigma ADCs, is used. Return to our 0.1 percent sensor accuracy guideline, which corresponds to a 10-bit accurate measurement. A rough calculation of the error budget can be seen in the product of a 100-degree temperature range, offset errors twice – to 10 times the sensor signal, and common mode noise and drift of a volt or more on top of a 10 mVFS signal which we hope the 100 dB CMRR of our front-end amplifier will remove. It is easy to see why a designer would look to the A/D converter to provide additional measurement resolution in order to remove the repeatable, systemic error sources in software. High flow rate control loops, a typical industrial circuit, utilize a 12-to-16-bit ADC running at 125 kSPS to 1 MSPS to do the job. The highest-accuracy, low-frequency applications measuring slow-changing variables such as weight and temperature, including Certified Trade Scales or high-capacity industrial equipment, look for 20 bits of noise-free resolution to reach their measurement goals by software calibration methods.
The firstborn of Intersil’s renewed focus on converters for low-noise industrial applications provides an excellent demonstration of design skills; the ISL26132 and ISL26134, low-noise 24-bit Delta-Sigma ADCs feature 2 or 4-channel inputs, with a very low noise PGA (10.2 nV/rt-Hz at 10 SPS) resulting in up to 21.6 bit noise-free resolution, accessible through a very easy-to-use serial digital interface. This device offers an immediate upgrade to existing designs in weigh scale and temperature measurement systems without modification. As you can see in Figure 5, it has never been easier to achieve such a high level of measurement accuracy reliably with such a low parts count.
Figure 5: Weigh scale application example.
Reviewing the needs of the difficult Industrial environment, the value of Intersil’s renewed focus on Precision Analog and the resulting exceptional performance of their latest products is apparent. Future products will no doubt continue to demonstrate this focus, with a growing repertoire of leading-edge solutions.
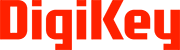
免责声明:各个作者和/或论坛参与者在本网站发表的观点、看法和意见不代表 DigiKey 的观点、看法和意见,也不代表 DigiKey 官方政策。