Synchronous Step-Down DC/DC Converters Handle Wide Input Voltage Ranges
投稿人:电子产品
2014-10-28
From communications infrastructure to industrial systems, wide input voltage ranges are common. Consequently, input voltages as high as 100 V must be converted to 24, 12, or 5 V and lower DC voltages that can be used to power a variety of ICs and electronic loads across these systems. Also, in some cases, transient conditions can approach voltages as high as 100 V at the input in low voltage converters and must be considered upfront when designing DC/DC power supplies. To address these requirements, power management solution providers like Texas Instruments, Linear Technology, Maxim Integrated and others have prepared integrated high-voltage regulators and controllers that simplify the design of synchronous step-down DC/DC converters with lower bill of material (BOM) cost and higher reliability.
Wide input voltage range
Speaking of transients and surges, many regulators targeted for 24 and 12 V rails are rated for 28 or 20 V, according to TI’s white paper, “Wide VIN power management ICs simplify design, reduce BOM cost, and enhance reliability,” by Vijay Choudhary[1]. To protect these devices from higher voltage surges, the norm has been to use protective clamps that can limit the input voltage spikes to a level below the rated voltage (Figure 1). However, these clamps add cost, area and design time. An alternative cost effective solution is TI’s LM5576.
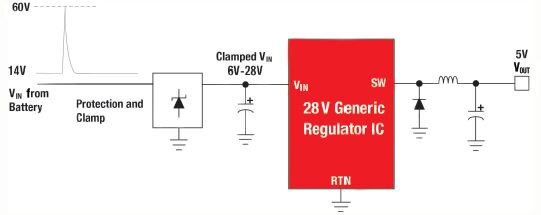
Figure 1: A generic low-voltage regulator in a battery-powered system is protected with a voltage clamp against input voltage surges.¹
A member of the supplier’s SIMPLE SWITCHER line, LM5576 is a robust buck regulator that is designed to handle an input voltage range of 6 to 75 V (Figure 2). As such, it can handle input transients without requiring a low-voltage clamp protection circuit. It delivers 3 A of continuous output current with an integrated 170 mΩ N-channel MOSFET. To overcome the limitation of low duty cycles associated with current-mode regulators, the LM5576 uses an emulated current-mode architecture, which provides inherent line regulation, tight load transient response, and ease of loop compensation. Plus, it offers an adjustable operating frequency from 50 to 500 kHz to optimize size and efficiency. The regulator comes in a power-enhanced HTSSOP-20 package with an exposed die-attach pad for thermal dissipation.
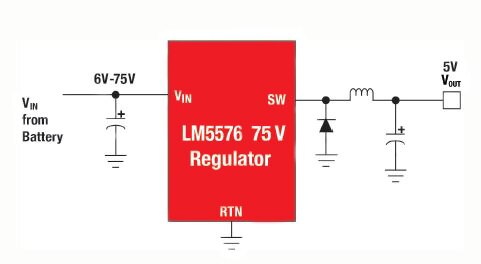
Figure 2: TI’s LM5576 with high-voltage rating eliminates an input clamp protection circuit.
There are some applications where you would like an extra margin of safety. Although a lower-voltage regulator IC may work in theory, using a higher-voltage counterpart gives some relief to the designer. According to TI, a DC/DC controller or regulator with sufficient voltage margin provides a lot of flexibility to the designer. One such part is LM5017. A 100 V 600 mA constant-on-time (COT) synchronous buck regulator with integrated high-side and low-side MOSFETs, LM5017 can be used in multiple applications requiring different input and output rails as depicted in Figure 3. Since it can efficiently regulate down higher voltages, it is well suited for 48 V telecom and 42 V automotive power bus rails. Protection features include thermal shutdown, undervoltage lockout (UVLO), minimum forced off-time, and an intelligent current limit.
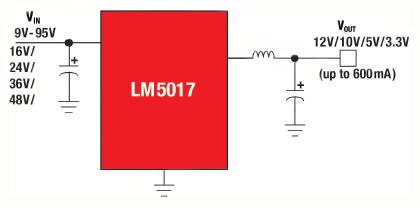
Figure 3: A high-voltage constant on-time (COT) synchronous buck regulator like LM5017 can be deployed in multiple applications requiring different input and output rails.
For higher-current applications, high-voltage integrated controllers like TI’s LM5116 and LM5117 can handle a widely varying input supply from 5.5 to 65 V. The built-in high- and low-side MOSFET drivers can supply peak currents of 3 A. Other key features include emulated peak current-mode control, user-programmable output, programmable operating frequency, thermal shutdown, cycle-by-cycle current limit, and adjustable line undervoltage lockout. The controllers come in power enhanced HTSSOP-20 packages with die-attached pads to aid thermal dissipation.
Other solutions
Similar wide input synchronous step-down DC/DC controller and regulator ICs are also available from Linear Technology and Maxim Integrated. Rated for 4 to 60 V input voltage range, Linear’s LTC3891 is designed to protect against high-voltage transients, continue operation during automotive cold crank, and cover a broad range of input sources and battery chemistries. It can therefore accommodate a wide range of intermediate bus voltages. The output voltage can be set from 0.8 to 24 V at high output currents up to 25 A with efficiencies as high as 95 percent, suiting it well for 12 or 24 V automotive, heavy equipment, industrial control, robotics, and telecom applications. As the buck controller is intended for battery-powered devices, the IC is tailored to draw very-low quiescent current in the sleep mode; LTC3891’s datasheet shows only 50 μA quiescent current in sleep mode. In addition, an overvoltage comparator guards the transient overshoots as well as other conditions that may create overvoltage at the output. Other features include selectable continuous, pulse-skipping, or low-ripple burst-mode operation at light load, selectable current limit, very-low dropout operation, adjustable output voltage soft-start or tracking, a power good output voltage monitor, and no-current foldback during start-up.
Likewise, Maxim Integrated’s synchronous step-down DC/DC converter MAX17505 (Figure 4) can handle a voltage input range of 4.5 to 60 V to deliver an output voltage that can vary from 0.9 V to 90 percent VIN.
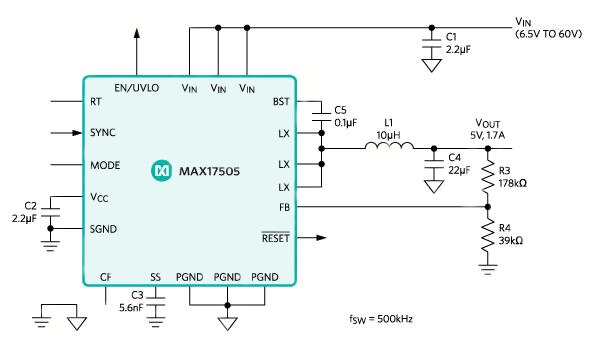
Figure 4: With integrated synchronous MOSFETs and a compensation circuit, MAX17505 needs few external components to deliver a regulated output from a wide input voltage range.
Since the synchronous MOSFETs are integrated along with the compensation circuit, MAX17505 minimizes the need for external components to complete the solution at lower cost. The low-resistance on-chip MOSFETs ensure high efficiency at full-load and simplify board layout. Additionally, a programmable soft-start feature reduces input inrush current and an output enable/undervoltage lockout pin (EN/UVLO) allows the designer to turn on the part at the desired input voltage level. Furthermore, an open-drain reset pin provides a delayed power-good signal to the system upon achieving successful regulation of the output voltage.
In short, wide input high-voltage synchronous buck controller and regulator ICs make it easy to create regulated DC/DC converters that can handle voltages as high as 100 V on input rails. By eliminating input voltage clamping circuits, these power managements ICs are also lowering the cost of building such converters while enhancing their reliability and simplifying board layout. Engineers will find that several vendors cater to such needs.
For more information on the synchronous buck controllers and regulators discussed in this article, use the links provided to access product pages on the DigiKey website.
Reference
- White paper, “Wide VIN power management ICs simplify design, reduce BOM cost, and enhance reliability,” by Vijay Choudhary, Applications Engineer, Texas Instruments.
免责声明:各个作者和/或论坛参与者在本网站发表的观点、看法和意见不代表 DigiKey 的观点、看法和意见,也不代表 DigiKey 官方政策。