Low Cost Micro-Machined Sensors Open Up Opportunities for Gyroscopes
投稿人:DigiKey 欧洲编辑
2013-05-30
Low cost, mass produced gyroscopic sensors and the various micromachining technologies are opening up a range of new applications. Devices from Analog Devices, STMicroelectronics, and Bosch Sensortec demonstrate the different technologies available and the ways to use micro-machined gyroscopes in various applications.
Gyroscopes are becoming an increasingly important part of the design of electronic systems. Moving from the initial high-volume application of car airbags and navigation systems, the technology is moving into many different areas. The improvements in the manufacturing process and innovations in materials and designs are providing smaller, lower power devices that are opening up new ways of using and protecting equipment.
Other applications such as image stabilization, telematics, and e-tolling are making use of low-cost gyroscopes, but the technology is also making its way into mainstream applications such as motion control with Man-Machine Interfaces (MMI) and appliances and robotics. The additional cost of supporting three dimensions of measurement is now low enough to allow gyroscopes to be used in applications that previously only employed one- or two-dimensional accelerometers, such as switching the profiles of displays from portrait to landscape, gaming controllers and even menu scrolling. The 3D data from the gyroscope can be translated by software into more sophisticated control of the interface to enhance the user experience.
The technology is even extending to shock detection and drop protection for warranty logging, providing more detailed information on what happened to the device.
The integration of more processing around the micro-machined sensor is also allowing more control of the power consumption. Using separate signal chains for the different axes of movement provides finer control of the power consumption and so supports advanced power management for mobile devices. This enhanced power control also opens up applications in pedometers and step counting, which can be combined with other portable devices and Web applications such as mapping in more sophisticated applications.
STMicroelectronics is one of the leading suppliers of micro-machined accelerometers that combine a single mass with highly integrated processing and interface electronics. The A3G4250D is a low-power 3-axis angular rate sensor that provides high levels of stability at the zero-rate level and sensitivity over temperature and time. It includes a sensing element and an SPI digital interface to deliver the measured angular rate to the external world. An I²C-compatible interface is also available.
The interface is manufactured using a CMOS process that allows a high level of integration to design a dedicated circuit that is trimmed to better match the sensing element characteristics. This provides a higher level of accuracy for the sensor, with a full-scale range of ±245 dps, and is capable of measuring rates with a user-selectable bandwidth.
The angular rate gyroscope produces a positive digital output for counter-clockwise rotation around the sensitive axis. The sensitivity comes from the gain of the sensor and can be determined by applying a defined angular velocity to it. This value changes very little over temperature and time.
Zero-rate level
The zero-rate level describes the actual output signal of any gyroscope if there is no angular rate present. The zero-rate level of precise MEMS sensors is, to some extent, a result of stress to the sensor and, therefore, the zero-rate level can slightly change after mounting the sensor onto a printed circuit board or after exposing it to extensive mechanical stress. This value also changes very little over temperature and time, but needs to be taken into account after the manufacturing process. Vibration is also a key challenge for the zero-rate level, and this can be tackled using the differential signals from the orthogonal sensor elements, reducing the vibration of the mechanical design and with filtering of the signal if the key frequencies are known.
Stability over temperature and time
Using a single-driving mass approach and optimized design means devices such as the A3G4250D are able to guarantee a perfect match of the MEMS mechanical mass and the ASIC interface and provide high levels of stability over temperature and time. With the zero-rate level and sensitivity performances at a factor of ten over previous generations, the A3G4250D allows the user to avoid any further compensation and calibration during production for a faster time to market, easy application implementation, higher performance, and cost savings.
A key example of the integration capability to support the micro-machined element is the FIFO in the A3G4250D. There is a 32-slot, 16-bit data FIFO allocated to each of the three output channels for the yaw, pitch, and roll measurements. This allows consistent power saving for the system, as the host processor does not need to continuously poll data from the sensor. Instead, it can wake up only when needed and burst the significant data out from the FIFO. This buffer can work in five different modes. Each mode is selected by the FIFO_MODE bits in the FIFO control register.
The control of the FIFO through a programmable watermark level, FIFO_empty or FIFO_Full event signals can be handled via dedicated interrupts on the DRDY/INT2 pin, and these are easily configured through CTRL_REG3, with the event detection information made available in FIFO_SRC_REG.
Figure 1: The block diagram of the A3G4250D micro-machined sensor from STMicroelectronics.
Modes
This architecture opens up different modes of operation. In FIFO mode, data from the yaw, pitch, and roll channels are stored in the FIFO. A watermark interrupt can be enabled, which is triggered when the FIFO is filled to the level specified in the WTM 4: 0 bits of FIFO control register. The FIFO continues filling until it is full (32 slots of 16-bit data for yaw, pitch, and roll). When full, the FIFO stops collecting data from the input channels. To restart data collection, it is necessary to write FIFO_CTRL_REG back to bypass mode.
In stream mode, data from yaw, pitch, and roll measurements are stored in the FIFO. A watermark interrupt can be enabled and set as in FIFO mode. The FIFO continues filling until full, again with 32 slots of 16-bit data for yaw, pitch, and roll. When full, the FIFO discards the older data as the new data arrives. Programmable watermark level events can be enabled to generate dedicated interrupts on the DRDY/INT2 pin.
At the same time, Analog Devices has also been pioneering the use of highly integrated micro-machined structures for accelerometers such as car airbag sensors and has extended this capability to cover three-axis gyroscopes.
The ADXRS652 is a complete angular rate sensor used as a gyroscope. It is based on a patented, high volume, BiMOS surface-micromachining process that is used to make a functionally complete and low-cost angular-rate sensor integrated with all of the required electronics on one chip.
The ADXRS652 is an industrial grade gyroscope that is pin, package, temperature and function compatible to the related automotive grade ADXRS620 and ADXRS622 gyroscopes. Automotive grade gyroscopes have more guaranteed minimum/maximum specifications due to automotive testing.
The ADXRS652 operates on the principle of a resonator gyro and uses two poly-silicon sensing structures, each containing a dither frame that is electrostatically driven to resonance. This produces the necessary velocity element to produce a Coriolis force during angular change. At two of the outer extremes of each frame, orthogonal to the dither motion, are movable fingers that are placed between fixed pickoff fingers to form a capacitive pickoff structure that sense the Coriolis motion. The resulting signal is fed to a series of gain and demodulation stages that produce the electrical rate signal output. The dual-sensor design rejects external g-forces and vibration. Fabricating the sensor with the signal conditioning electronics preserves signal integrity in noisy environments.
Figure 2: The ADXRS652 gyroscope from Analog Devices.
The electrostatic resonator requires 18 V to 20 V for operation but only 5 V is typically available in most applications, so a charge pump is included on chip. If an external 18 V to 20 V supply is available, two capacitors can be omitted.
The output signal is a voltage proportional to angular rate about the axis normal to the top surface of the package. The output is ratio metric with respect to a provided reference supply. An external capacitor is used to set the bandwidth. Other external capacitors are required for operation.
New opportunities
Bosch Sensortec has added additional processing in its BMA120 triaxial, low-g acceleration sensor to open up opportunities in low-power consumer market applications. It allows measurement of accelerations in three perpendicular axes. The interface circuits convert the output of a three-channel micromechanical acceleration sensing structure that works according to the differential capacitance principle.
This provides a low-cost way to sense tilt, motion, shock and vibration in cell phones, handhelds, computer peripherals, man-machine interfaces, virtual reality features, and game controllers.
The gyroscope is highly configurable to give the designer full flexibility when integrating the sensor into a system. All features can be set by software via the digital interface and this enhances its use in areas such as motion detection applications, such as device orientation detection, gaming, HMI and menu browser control.
The g-ranges and bandwidths can be user programmed via the serial digital interface. Here the user can choose between an I²C and an SPI (3-wire/4-wire) interface mode.
One of the key elements of the BMA120 is the intelligent interrupt engine that gives the hardware and software designer full control. Various motion detection scenarios can be identified by the sensor and signaled to the system via a simple interrupt pin. By using the digital serial interface, the exact details of the motion event that triggered the interrupt can be read out from the device.
Application examples include pedometers, the detection of tap patterns comparable to fingertips on notebook touch pads, and the recognition of the position of hand held devices in three-dimensional space for game controllers or to automatically rotate the content of a display.
The interrupt controller's job is to classify the various movements into four movement categories:
- Random movement: usually used to "wake up" a mobile device from the stand-by mode
- Rotational movement: effects targeted rotation of displayed contents according to whether the mobile device is held vertically or horizontally
- Tapping: single or double taps on the mobile device trigger various functions, for example, muting a ring tone
- Fast/slow: optional control functions according to the speed of a movement, for example, automatic emergency call in response to vigorous shaking of a mobile phone
When the interrupt controller recognizes a programmed movement, it sets the interrupt output from logical "0" to "1". Details about the recognized pattern can be queried through the digital interfaces. Tools are already available for the development of necessary applications, as are drivers for the various operating systems: Windows Mobile, Linux and Android.
Another important feature of the BMA120 acceleration sensor is the power management module. This module allows for optimizing the sensor’s power consumption in-line with the specific user requirements so that it wakes up only at set intervals such as every two seconds. For some user cases, the power consumption drastically shrinks to just a fraction of what would be required in full performance mode by using the different modes (as in figure 3).
Mode | Wake-up time | Current consumption at 1.8 V VDD |
Power-off | only 1 ms | 0 μA |
Suspend | ≥ 400 μs | 1 μA (typ.) |
Low-power (sleep) | ≥ 400 μs | 2 μA (typ.) |
Full performance | - | 430 μA |
Figure 3: The power management modes of the Bosch Sensortec BMA120 micro-machined gyroscope.
Conclusion
The development of effective high-volume micro-machining processes has opened up a wide range of opportunities for three-axis gyroscopes. Different technologies can be used for the sensors from BiCMOS to quartz crystal, but the integration of the processing alongside the sensor has allowed lower power and more power management, as well as smaller size and lower cost. While the zero point errors have to be considered for low-cost devices, the additional integrated conditioning circuitry allows simpler, lower cost structures to be used without creating problems of drift or inaccuracy. This is opening up the use of gyroscopes in new ways to enhance the design and development of consumer and industrial equipment.
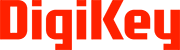
免责声明:各个作者和/或论坛参与者在本网站发表的观点、看法和意见不代表 DigiKey 的观点、看法和意见,也不代表 DigiKey 官方政策。