如何将协作机器人安全整合至工业应用
投稿人:DigiKey 北美编辑
2020-02-06
目前,市面上有些紧凑型工业机器人能以高性价比的方式整合至小型生产线中。部分吸引力在于,这类机器人可与操作人员协作,为其分担重复性任务,从而减少因操作人员疲劳而引起的错误。然而问题在于,与移动的机器共享工作空间可能会对人员构成安全隐患。
确保协作机器人 (cobot) 安全的关键是慎重考虑所涉及的风险,并配置机器人及其控制系统以减轻潜在危害。所幸,如今已出台相关技术规范以引导开发人员规避风险,确保安全。
本文阐示了在工作环境中添加协作机器人的优势,指出了相关安全问题,介绍了最新的法规指南并提出了风险评估和缓解策略。此外,本文还介绍了内置安全机制的协作机器人,凭借该机制即可安心将其加入任何生产或工作流程中。
为何要添加协作机器人?
长期实践证明,大型制造厂的工业机器人在提高生产吞吐率同时降低成本方面可谓物超所值。而如今,通用紧凑型工业机器人可使中小型生产同样受益。但不同于大型机器人,紧凑型机器人专为与操作人员协作而设计,无法独立作业(图 1)。人机共享工作空间有助于最大限度地减少机器人的空间占用,从而节省宝贵的生产场地,提高成本效益。
图 1:小型工业机器人专为人机协作设计,无法独立作业。(图片来源:KraussMaffel/KUKA Robotics)
与所有动力机械一样,如果使用不当,这些协作机器人也可能会造成伤害。因此,将协作机器人整合至生产线时,必须慎重考虑操作人员的安全问题。请谨记,考虑要素包括机器人的运动范围和速度、所需搬运的物料以及人机交互的方式和频率。一旦清楚了这些内容,就可以将适当的安全增强功能整合至系统设计中。
美国职业安全与健康管理局 (OSHA)、加拿大职业健康与安全中心 (CCOHS) 和欧盟委员会等组织制定的法规要求,针对协作机器人操作安全的某些要素作出了详细规定。例如,《美国联邦法规》(CFR) 第 29 条第 1910 部分,又称为 OSHA 标准,要求系统在维修操作期间必须锁定危险能量源(第 147 节),防止操作期间发生电击(第 333 节)。但是,这类法规旨在适用于各类工业机械,并且不一定与技术发展保持同步。针对一般工业机器人(特别是协作机器人)制定的法规相对较少。
然而,为了填补这方面的空缺,业界专门针对工业机器人制定了若干技术标准。其中包括 IEC 61508 功能安全标准、ISO 12100 机械安全性设计标准以及 ISO 10218-1 和 ISO 10218-2 工业机器人安全标准。最近,业界又颁布了 ISO/TS 15066 协作机器人安全技术标准。这些标准中,只有部分是针对机器人系统设计提出的要求,其他均是为开发人员和操作人员提供的建议,并给出详细指导以确保人机交互的安全。
协作机器人风险评估
为了确保协作机器人的安全,首先要对预期的机器人操作和使用方式进行谨慎的风险评估——不仅针对机器人本身,还需涵盖整个应用和工作环境。例如,搬运锐利金属板的机器人系统所带来的风险与搬运纸板箱的系统截然不同。同样,配备抓具的机器人风险评估与配备钻头或烙铁的机器人大相径庭。
因此,开发人员必须充分了解系统的操作范围、机器人的运动特性、工作空间和工作流程以及其他类似要素,以便确定机器人操作过程中的潜在风险来源。这些来源包括可能造成某种形式的伤害——无论是有意、无意造成,还是由设备故障引起——任何可能的人机交互。
一旦确定了风险,就必须针对各项风险进行评估。依照以下三项关键标准,可将评估的各项风险分为可忽略、低、中、高和极高五类:
- 潜在伤害的严重程度
- 接触危害的频率和/或持续时间
- 避免危害的可能性
利用风险树进行评估的典型方法如图 2 所示。伤害的严重程度由轻微(例如数天即可完全愈合的割伤或挫伤)到严重(导致永久性损伤或死亡)。接触频率从低(偶尔)到高(频繁或连续),避免可能性从可能到不可能。评估人员可按照自己的方式量化这些标准,以反映具体情况。
图 2:风险等级评估要求检查潜在伤害的严重程度和可能性。(图片来源:Richard A. Quinnell)
不过,ISO/TS 15066 为业界带来的见解之一是,对人机互动的无害物理接触进行了量化定义。由于协作机器人应用中很可能发生甚至预期出现人机物理接触,因此该定义就显得尤其重要。该标准定义了两种接触类型:瞬时接触和准静态接触(图 3)。
瞬时接触是指人员可快速脱离与机器人的接触,例如机器人部件冲撞到操作人员的手臂;准静态接触是指人的身体部位夹在机器人和固定物体之间,例如机器人的抓具将操作人员的手压在桌面上。
图 3:人机接触(意外接触或预期接触)可分为两类:瞬时接触和准静态接触。(图片来源:Richard A. Quinnell)
在协作机器人应用中,对接触力的限制基于人类的疼痛阈值。无论有意接触还是无意接触,都必须通过配置将协作机器人的力量控制在疼痛阈值以下。接触力限值有所不同,具体取决于所涉及的身体部位。例如,接触头部的疼痛阈值就远低于手臂。此外,准静态触点的阈值也低于瞬时接触。
确定风险并进行评估后,关键在于确认每项风险的“等级可否接受”。在多数情况下,可忽略或极低的风险尚可容忍,但其他情况都必须采取一种或多种缓解措施。因此,为了确保机器人的安全,第二步则是选择适当的风险缓解措施,然后重新评估风险,并且不断重复这一过程,直至所有风险都降到可接受水平为止。
风险缓解途径
为了缓解风险,可采取的一些最常用方法包括:重新设计机器人工作流程或其工作空间布局以消除危害,或限制人机交互以最大限度地减少接触。传统工业机器人应用中,常常设置防护栅以隔离人员与机器人工作空间,并在人员进入该区域时通过互锁装置停止机器人作业,藉此限制人机交互。但在协作机器人应用中,机器人必须与人员共享协作工作空间,因此需要采取其他方法。
目前,业界已确定了四种关键方法可用于协作式人机交互:
- 安全级监控停止
- 手动引导
- 速度和间距监控
- 功率和力大小限制
开发人员需要确定最适合其应用的方法或方法组合。
适合采用安全级监控停止法的应用要求人机交互仅在特定条件下发生,例如机器人末端执行器的装载或卸载,或对进行中的工作进行检查。在这类人机交互中,机器人在保护空间内自主运行,并且持续监控以检测是否有人进入该区域。操作人员进入该工作空间前需启动安全级停止状态,而操作人员处于该区域内时,机器人保持通电但停止动作。待操作人员离开工作空间后,机器人才会自动恢复自主运行。如果有人进入监控空间而未启动安全级停止状态,则系统将启动保护性停机,关闭系统电源。
在手动引导方案中,操作人员进入机器人工作空间前需启动安全级停止状态,并在借助手动引导机制重新定位机械臂后,触发机器人的下一个动作。手动引导机制可能只是简单抓住并操纵机械臂,也可能是使用手持控制设备来操控机器人动作。机器人升降辅助等应用可以采用手动引导式协作。
如果操作人员和机器人经常需要共享同一工作空间,并且操作人员能在该区域内自由活动,则速度和间距监控法相当管用。在这一方案中,系统会监测人机间距,并尽量始终保持最小保护间距(图 4)。两者保持安全间距时(不可能发生接触),机器人可以全速自由移动;若间距缩短,机器人会继续工作,但速度减慢,以便能更快速地完全停止动作;间距过短时,机器人进入安全级停止状态,确保不会造成伤害。
图 4:速度和间距监控可识别机器人周围区域,并以此界定机器人的安全操作。(图片来源:Richard A. Quinnell)
在这种方法中,对各段距离的定义需要了解机器人系统的运动能力。设计系统时应确保:一旦监控器检测到有人朝保护空间移动,并在人员进入该区域前,机器人运动机构就已完全停止动作。为了计算合适的间距,开发人员必须清楚:
- 机器人和人员的移动速度
- 系统检测潜在闯入的反应时间
- 机器人收到命令后停止移动所需的时间
对于速度和间距监控法,工作空间布局有助于简化安全区的定义和监控。以下图为例,布局构建了本质安全区(图 5)。工作台将人员与机器人的工作空间隔离,在此区域内机器人可以全速自由移动。但是机器人进入工作台侧的协作区域时,就会自动减速,以便减少准静态接触的机会。减速会减小潜在瞬时接触力,使人员可趁机避开危害,从而最大限度地减轻该区域的风险。
机械限位器可防止机机器人运动机构进入人员工作区域以规避风险。采用这类布置只需最低限度地监控机器人工作空间以防人员闯入,即可确保较高的系统安全性。
图 5:通过工作空间设计可构建本质安全区。(图片来源:Richard A. Quinnell)
在极可能发生人机接触的应用中,功率和力大小限制法特别管用。如需使用该方法,机器人必须能够检测运动机构何时承受了异常力,以便检测接触并作出反应。此外,机器人还必须能够最大限度地减小潜在接触力,例如避开锋利的边缘和挤压点、使用表面衬垫以及限制移动速度。
应用设计时,应尽量避免经常发生接触,并仔细评估可能发生的接触类型(瞬时或准静态)以及所涉及的身体部位。同时,还应最大限度地减少准静态接触的机会,并彻底防止与头部、颈部或喉部发生接触。
机器人系统的安全功能
选择机器人用于协作型应用时,开发人员需记住该如何实施一种或多种上述缓解措施。机器人的物理设计及其控制系统都是决定安全措施是否能轻松实施的评估要素。但是通常情况下,机器人供应商往往会设法确保系统安全。
例如,KUKA 的 Agilus 机器人套件系列包括用于手动引导控制的 smartPAD 触摸操作面板,以及具有集成安全功能的 KR C4 系统控制器。此外,还可选用 KUKA.SafeOperation 软件以完善套件功能。该套件的机械臂具有多种可达距离,包括 540 mm (KR 3 R540)、900 mm (KR 6 R900-2) 和 1100 mm (KR 10 R1100-2)(图 6)。
图 6:KUKA 的 Agilus KR 3 等紧凑型工业机器人在设计时,就将安全作为主要考虑因素。只要安装设置遵循行业标准,操作人员即可放心与之共享工作空间和协作。(图片来源:Kuka Robotics)
上述三款机器人均采用曲面设计,表面覆盖能量吸收衬垫,以最大限度地减少接触压力。关节均采用全包覆式设计以消除任何挤压危害。此外,机器人的关键运动轴均具有可调机械限位器,以便开发人员对机器人工作空间设置物理限制。
套件中包含 smartPAD,适用于需要手动引导操作的应用(图 7)。
图 7:KUKA 机器人套件中包括 smartPad 触摸操作面板,适用于手动引导控制。(图片来源:KUKA Robotics)
KR C4 控制器的集成安全软件包含安全级和紧急停止的实施例程,并且能够监控符合行业标准的外部传感器以构建安全栅。此外,就系统内部而言,该软件还能监控机器人的位置及其绕所有运动轴的动作。
KUKA.SafeOperation 软件允许开发人员定义单元区域:具有三至十个顶点的凸多边形,规定在此区域外机器人无法移动,从而增强内部监控功能(图 7)。此外,开发人员还可使用笛卡尔坐标或指定轴坐标,在此单元区域内定义多达 16 个监控空间。
图 8:开发人员可使用 KUKA.SafeOperation 软件优化与位置相关的安全监控,定义操作区并为末端执行器工具建模。(图片来源:KUKA Robotics)
如需进一步优化与位置相关的安全监控,SafeOperation 软件允许用户为机器人安装法兰连接的末端执行器工具建模,最多可使用六个用户定义的球体。机械臂动作时,这些球体随之一起移动。如果操作过程中机械臂或工具球体移入或移出监控空间,软件将有所响应。可能的响应包括发出警报信号、减慢机器人运动速度和实施安全停止。因此,开发人员可轻松控制机器人在其运动范围内任意位置的动作。
这些功能简化了风险缓解方案的实施,但其本身并不能确保人机交互的安全。如需将机器人系统集成到生产工作流程中,尤其是协作型应用中,开发人员仍必须进行风险评估并采取缓解措施,具体方法取决于应用。应对措施包括遵循所有制造商的指南和限制、适当培训用户以及酌情实施监控系统和设置护栏。
总结
在制造及其他工作流程中,机器人和协作机器人渐受青睐,但是工业自动化开发人员仍须考虑其潜在危害。若要将机器人集成到工作流程中,新出台的机器人安全标准虽然确有帮助,但借助设计时就以安全作为主要考虑因素的机器人系统,相对更简单安全。
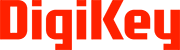
免责声明:各个作者和/或论坛参与者在本网站发表的观点、看法和意见不代表 DigiKey 的观点、看法和意见,也不代表 DigiKey 官方政策。